Digital Transformation Solutions in Manufacturing
The Role of Digital Transformation in Modern Manufacturing
Manufacturing is undergoing a fundamental shift as companies embrace digital transformation solutions to enhance efficiency, agility, and competitiveness. For executive leaders—directors, VPs, and C-suite—understanding these solutions is essential for maintaining operational resilience and future-proofing their business.
Digital transformation in manufacturing is not just about technology; it is about aligning people, processes, and technology to achieve tangible business outcomes such as increased productivity, reduced costs, and enhanced quality.
Key Digital Transformation Solutions
1. Industrial IoT (IIoT) & Real-Time Data Analytics
The integration of IoT sensors and connected devices enables manufacturers to collect and analyze real-time data from machines, production lines, and supply chains. This data-driven approach enhances predictive maintenance, OEE (Overall Equipment Effectiveness) tracking, and real-time decision-making to minimize downtime and maximize efficiency.
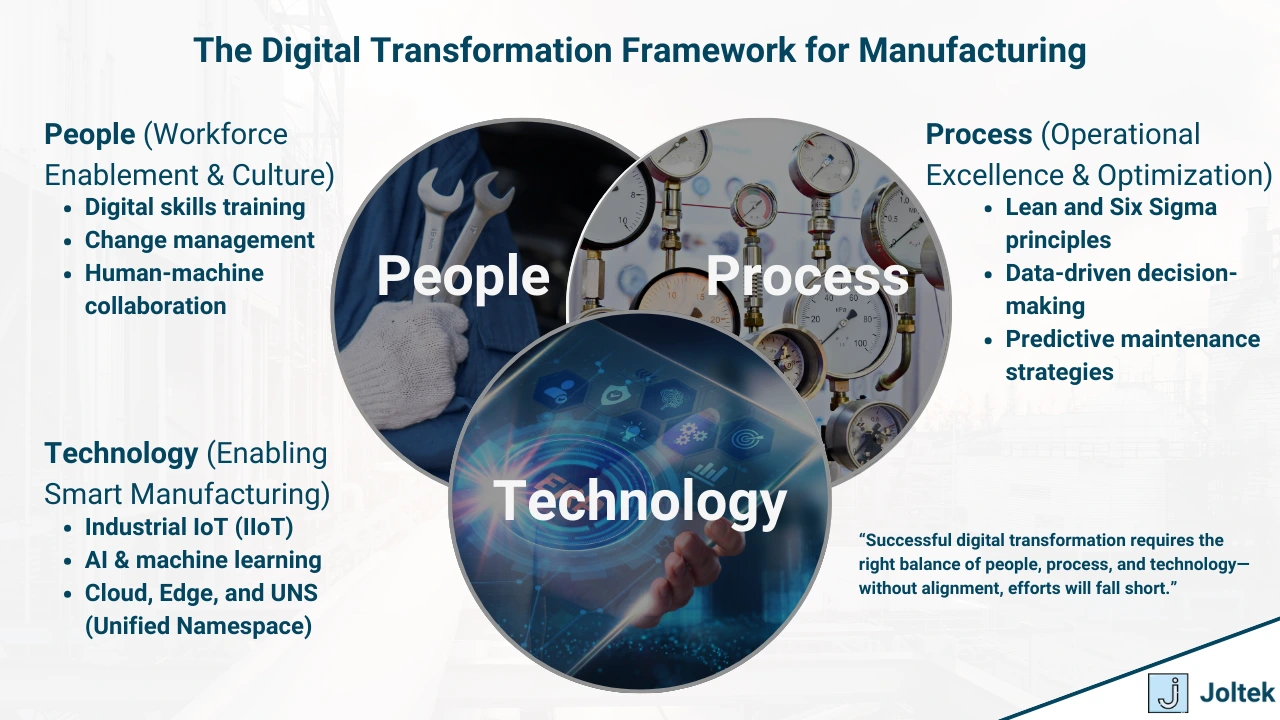
2. Manufacturing Execution Systems (MES) & Smart Factory Automation
A modern MES bridges the gap between enterprise systems (ERP) and shop-floor automation (SCADA, PLCs). It enables:
- Seamless production tracking
- Quality assurance through digital workflows
- Improved traceability and compliance
Automation solutions such as robotic process automation (RPA) and cobots further enhance productivity by streamlining repetitive tasks.
3. Unified Namespace (UNS) & IT/OT Convergence
Data silos between IT and OT systems remain a major bottleneck in digital transformation. The Unified Namespace (UNS) architecture provides a single, structured source of truth, facilitating:
- Interoperability between legacy and modern systems
- Simplified data access for AI/ML applications
- Faster deployment of digital solutions across the enterprise
4. AI, Machine Learning & Edge Computing
Artificial intelligence and machine learning (AI/ML) are transforming manufacturing by enabling:
- Advanced predictive analytics for quality control and equipment failures
- Automated process optimization based on real-time conditions
- Edge computing to process data at the source, reducing cloud latency
5. Cloud & Hybrid Manufacturing Solutions
Cloud-based platforms enable manufacturers to scale digital initiatives without major infrastructure overhauls. A hybrid model (on-prem + cloud) ensures:
- Secure, scalable storage for industrial data
- Seamless integration with ERP and supply chain systems
- Faster deployment of AI-driven analytics and digital twins
The Business Case for Digital Transformation
Investing in digital transformation solutions is not just a technology upgrade—it is a strategic decision that impacts competitiveness, resilience, and profitability. Leading manufacturers report:
- 30-50% reduction in unplanned downtime with predictive maintenance
- 15-20% increase in productivity with smart automation and AI-driven optimization
- Improved agility and supply chain resilience through real-time visibility
Overcoming Implementation Challenges
Despite the benefits, digital transformation is not without challenges. Common hurdles include:
- Legacy system integration – Many factories operate with outdated, incompatible systems. A gradual modernization plan is key.
- Change management – Successful transformation requires workforce buy-in and upskilling initiatives.
- Cybersecurity risks – Increased connectivity requires a robust industrial cybersecurity strategy.
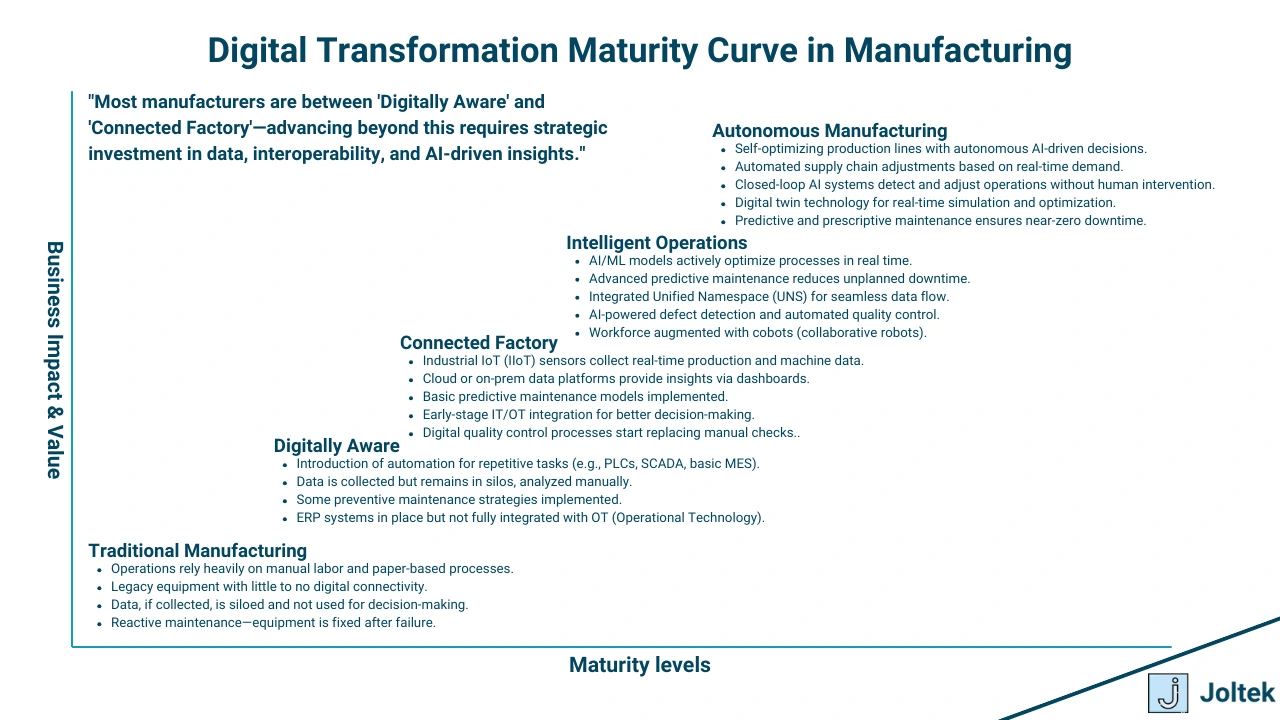
Conclusion: The Path Forward
For manufacturers looking to stay ahead, digital transformation is no longer optional—it is imperative. The key to success lies in a clear strategy, the right technology partnerships, and a phased implementation approach to ensure sustainable, long-term benefits.
If you're ready to assess your facility’s readiness for digital transformation and explore tailored solutions, let’s start a conversation.