In today’s manufacturing environment, data has become a central resource for decision-making and process improvement. However, translating raw industrial data into actionable insights is far from straightforward. Despite the frequent use of terms like IoT, digital transformation, and Industry 4.0, many manufacturers find that realizing the potential of data is far more complex than anticipated. The nuances of data generation, integration, real-time requirements, and contextualization can pose significant hurdles, especially when facilities are dealing with unique system architectures and legacy equipment. For decision-makers in manufacturing, the journey to fully unlocking data’s potential is not merely about technology; it requires a comprehensive strategy, a nuanced understanding of data’s role across systems, and often, specialized consulting support.
Understanding the Manufacturing Data Ecosystem
Manufacturing facilities function as complex systems where data flows across multiple layers—from individual field devices to higher-level systems like SCADA (supervisory control and data acquisition), MES (manufacturing execution systems), and ERP (enterprise resource planning). In a simplified view, each facility can be seen as a “black box,” with inputs like raw materials, labor, and energy contributing to outputs in the form of finished products, waste, and data. Capturing and analyzing data from these inputs and outputs is essential for decision-making, but the process involves numerous challenges. For example, individual sensors on production lines can generate vast amounts of raw data in the form of signals—highs, lows, counts, and time stamps—but this data is typically uncontextualized and requires aggregation and interpretation to be meaningful at higher decision-making layers.
For manufacturers, the first step in unlocking data’s potential lies in understanding what data is generated, where it is captured, and who needs access to it. In practical terms, data might originate from simple sensors, PLCs (programmable logic controllers), or HMI (human-machine interface) systems, all of which contribute to a vast and interconnected web of information. Each device plays a role in capturing real-time data, such as machinery status, process variables, or product quality metrics, which must then be processed and routed through appropriate channels to provide value. Yet, the needs of a plant floor operator differ greatly from those of a production manager or an executive reviewing operational data at a high level, making data contextualization a critical, yet challenging, endeavor.
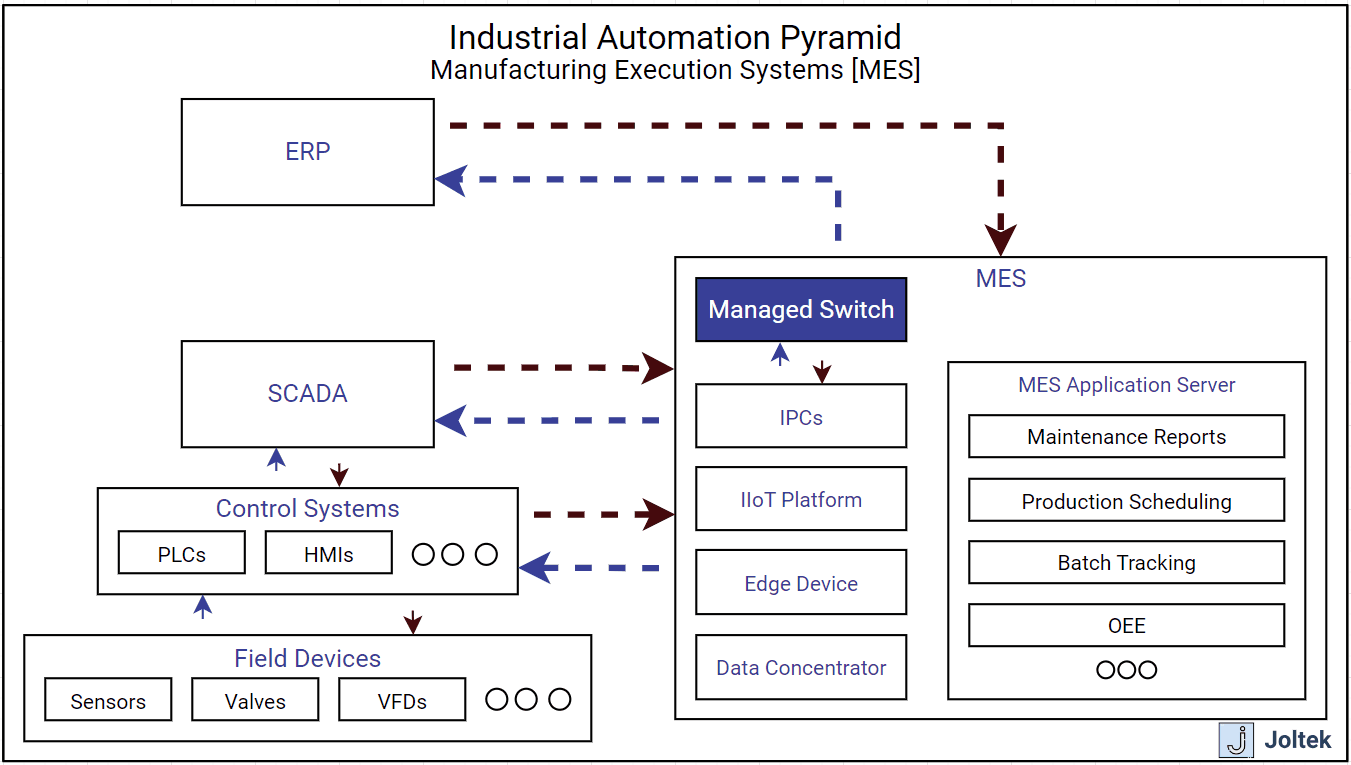
The Complexity of Real-Time vs. Historical Data in Manufacturing
One of the most pressing challenges in industrial data management is determining when real-time data is essential versus when historical data will suffice. Real-time data is necessary for certain process control functions, such as detecting levels in a tank that indicate the need for immediate transfer or activating quality control alarms based on sensor readings. For example, if a batching system’s tank reaches a full state, an operator needs this information in real-time to avoid production delays or quality issues. The cost of such delays can accumulate rapidly, particularly in high-demand environments where downtime translates directly to lost revenue and throughput. In this context, real-time data access empowers operators to respond promptly and keep processes on track.
However, real-time data is not always required, and collecting it indiscriminately can lead to network congestion, increased storage costs, and inefficient resource allocation. Data about process cycle times, equipment efficiency, or yield rates, for example, can be analyzed in aggregate or at set intervals rather than in real-time. This data informs long-term operational decisions, such as whether to add new production lines, adjust staffing, or reconfigure equipment layouts to improve efficiency. Overemphasis on real-time data can burden networks with excessive data packets that offer little immediate value but increase processing requirements and add complexity to data storage and retrieval. This nuanced approach to prioritizing data collection is essential to achieving both efficiency and cost-effectiveness.
The Role of System Integration in Data Contextualization
Integrating disparate data systems in a manufacturing facility is a challenging but vital step in transforming data into actionable insights. Manufacturing environments often involve a diverse array of systems: PLCs manage machinery control functions, SCADA systems oversee larger process operations, MES platforms track production workflows, and ERP systems handle resource planning and financial data. Each layer has its unique function, yet these systems must be interconnected to provide decision-makers with a comprehensive view of operations. However, due to variations in system architectures, equipment vendors, and data protocols, seamless integration is often challenging, particularly in facilities with legacy equipment or custom-built systems. In many cases, the data produced by each layer lacks the necessary context when viewed in isolation, leading to gaps in understanding that hinder effective decision-making.
Contextualization is a crucial part of this integration, as data must be framed according to its relevance to specific roles or departments. Raw sensor data from a conveyor belt, for example, may indicate that a part has passed through a station, but without the context of production schedules, quality thresholds, or historical cycle times, it holds little actionable value. To address these challenges, manufacturers often rely on consultants with expertise in IT-OT convergence (Information Technology and Operational Technology), who can bridge the technical and strategic gaps by designing systems that allow for both vertical and horizontal data integration. A successful integration strategy not only provides seamless data flow but also enables data interpretation at multiple levels, from operational insights for plant floor operators to strategic analytics for executives.

Custom Manufacturing Systems: A Barrier to Standardized Solutions
The inherent complexity of manufacturing environments means that custom systems are often necessary, even when facilities produce similar products. While standard solutions may be suitable for some operations, customizations become essential when unique product requirements, facility layouts, or legacy systems are involved. For instance, a food processing facility and a beverage production plant may both involve liquid handling systems, but the specific parameters for heating, cooling, mixing, and bottling can vary widely, requiring specialized equipment and tailored data solutions. Additionally, differences in vendor equipment, programming styles, and local regulatory requirements further complicate efforts to implement standardized data solutions across multiple sites.
These customizations can create significant hurdles when attempting to replicate successful data strategies across facilities. For example, a data solution designed for one facility may not transfer seamlessly to another due to differences in data protocols or system architectures. Such barriers often necessitate a careful assessment of each facility’s unique requirements, followed by tailored integration efforts. Consulting experts can play a crucial role in this process by conducting system audits, mapping data flows, and designing architectures that accommodate each facility’s specific needs. With custom solutions, manufacturers can ensure that data remains relevant and accessible to all stakeholders, maximizing its utility while minimizing unnecessary complexity.
Managing Data Volume and Resolution: Avoiding Data Overload
The vast amounts of data generated in manufacturing can easily lead to data overload, where excessive data storage and processing requirements outweigh the insights provided. For instance, analog sensors measuring tank levels might report fluctuations every millisecond, producing large volumes of near-identical readings that add little value. In such cases, storing every minor change is unnecessary, and strategic data filtering can reduce network strain and storage costs. One approach is to set data resolution thresholds, storing only significant changes rather than minute fluctuations. For example, recording tank levels at one-percent increments rather than every minor fluctuation reduces data volume while still providing valuable insight into production trends.
Another common issue in data management is the need to reconcile data accuracy with cost-efficiency. Storing high-resolution data can quickly become cost-prohibitive, particularly in facilities with limited IT infrastructure or cloud storage resources. Consulting services specializing in industrial data can help manufacturers establish data collection policies that balance the need for actionable insights with the limitations of data storage and processing. By optimizing data management practices, manufacturers can prevent data overload, reduce costs, and improve the accessibility of meaningful information for decision-making.
The Strategic Role of Consulting in Industrial Data Transformation
Effectively leveraging industrial data often requires specialized expertise, particularly in complex manufacturing environments. Consultants offer a range of services that address both the technical and strategic challenges of data integration, helping manufacturers to develop and implement robust data strategies that align with organizational goals. Consulting support often begins with an initial assessment of the facility’s data needs, followed by the creation of a data management roadmap. This roadmap typically includes recommendations for technology upgrades, system integrations, and training initiatives that equip staff with the skills needed to interpret and use data effectively.
One critical area where consulting adds value is in bridging the IT-OT gap. Many manufacturing facilities struggle with aligning the goals of IT and OT departments, as each has distinct priorities and skillsets. Consultants with experience in IT-OT convergence can facilitate collaboration, ensuring that data solutions meet both the operational needs of the plant floor and the security, compliance, and strategic requirements of the IT team. Additionally, consultants can provide continuous improvement services, helping manufacturers to refine their data strategies as technology evolves and operational demands change. This level of ongoing support is essential for maintaining competitive advantage in a rapidly changing industry landscape.
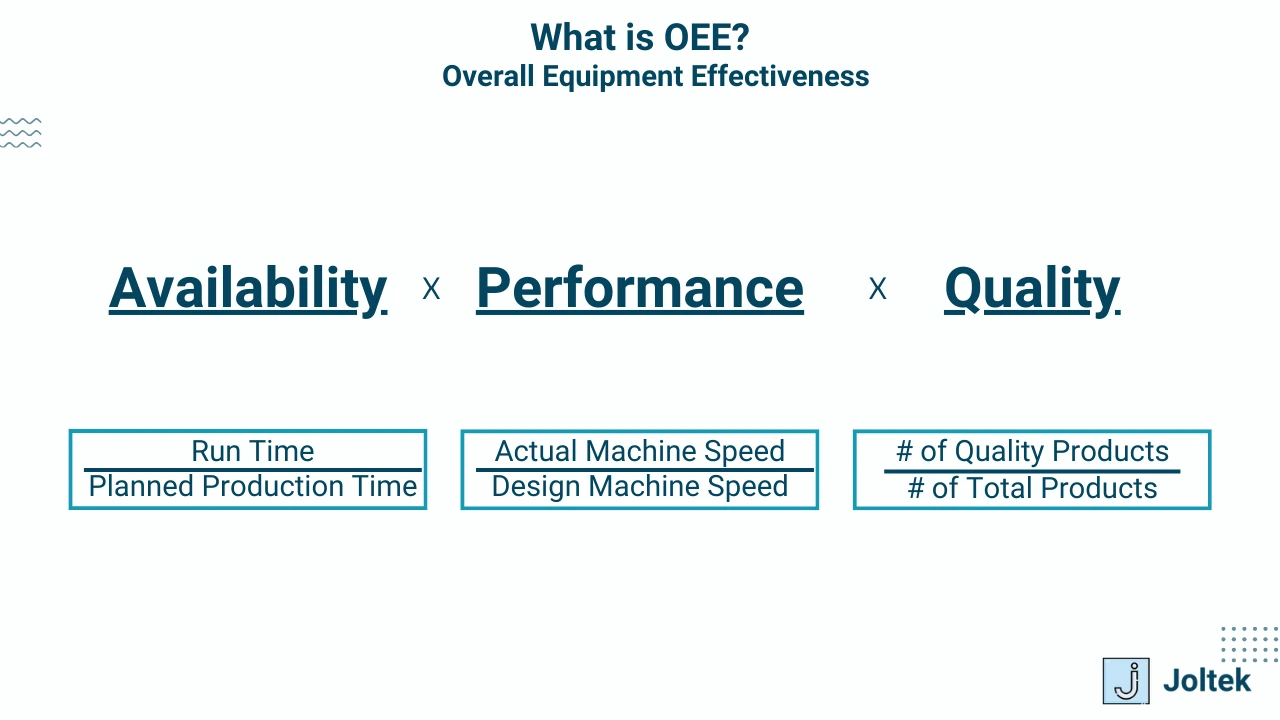
Realizing the Potential of Data in Manufacturing
For manufacturers, the value of data lies not only in its availability but in the ability to contextualize, integrate, and act upon it effectively. As the manufacturing sector continues to evolve, those who succeed will be those who recognize the strategic importance of data and invest in the resources and expertise needed to transform it into a core part of their operations. A well-defined data strategy, combined with expert consulting support, enables manufacturers to overcome technical challenges, streamline processes, and make more informed decisions, ultimately driving greater efficiency and profitability.
For manufacturing leaders looking to unlock the full potential of their data, now is the time to prioritize strategic data management. By partnering with consulting experts, manufacturers can gain the insights, tools, and systems necessary to thrive in an increasingly data-driven world.
Case Study: Enhancing Manufacturing Efficiency Through Advanced Data Analytics
Source: McKinsey & Company
In the competitive landscape of modern manufacturing, leveraging data analytics has become essential for optimizing operations and maintaining a competitive edge. This case study examines how a leading automotive parts manufacturer utilized advanced data analytics to significantly improve production efficiency, reduce downtime, and enhance product quality.
Background
The manufacturer operates multiple production lines, each equipped with a variety of machinery and sensors generating vast amounts of data. Despite having access to this data, the company faced challenges in effectively analyzing it to identify inefficiencies and areas for improvement. Common issues included unplanned machine downtime, inconsistent product quality, and suboptimal resource utilization.
Implementation of Data Analytics
To address these challenges, the company partnered with a data analytics consulting firm specializing in manufacturing solutions. The project was structured into several key phases:
- Data Collection and Integration: The first step involved aggregating data from various sources, including machine sensors, production logs, and quality control records. This data was then integrated into a centralized analytics platform capable of handling large datasets and providing real-time insights. One option for collecting this type of data is the MQTT protocol.
- Data Cleaning and Preprocessing: Ensuring data accuracy and consistency was crucial. The team employed advanced algorithms to clean and preprocess the data, addressing issues such as missing values, duplicates, and anomalies.
- Advanced Analytics and Modeling: With clean data in place, the team applied machine learning models to identify patterns and correlations. Predictive analytics were used to forecast potential machine failures, while prescriptive analytics provided recommendations for process optimization.
- Visualization and Reporting: The insights gained were presented through intuitive dashboards and reports, enabling decision-makers to monitor key performance indicators (KPIs) and track improvements over time.
Outcomes
The implementation of advanced data analytics yielded significant benefits:
- Reduced Downtime: Predictive maintenance models accurately forecasted machine failures, allowing for proactive maintenance scheduling. This approach led to a 30% reduction in unplanned downtime, aligning with industry findings that predictive maintenance can decrease machine downtime by 30 to 50%
- Improved Product Quality: By analyzing production data, the company identified factors contributing to product defects. Adjustments to the manufacturing process resulted in a 25% decrease in defect rates, enhancing overall product quality.
- Enhanced Resource Utilization: Data-driven insights enabled the company to optimize resource allocation, leading to a 15% increase in production efficiency without additional capital investment.
Conclusion
This case study demonstrates the transformative impact of advanced data analytics in manufacturing. By effectively harnessing data, manufacturers can proactively address operational challenges, improve product quality, and achieve significant efficiency gains. For decision-makers seeking to enhance their manufacturing processes, investing in data analytics solutions offers a strategic pathway to sustained competitive advantage.
Conclusion
In conclusion, the transformative power of data analytics in manufacturing is undeniable. As illustrated, manufacturers who leverage data effectively can unlock unprecedented levels of efficiency, improve product quality, and reduce operational costs, all while minimizing downtime. However, achieving these outcomes requires more than just implementing new technology; it calls for a strategic approach that aligns with the unique requirements of each facility. Through careful data collection, targeted integration, and robust analytical models, manufacturers can turn raw data into actionable insights that drive sustainable growth and competitiveness.
For leaders in manufacturing, investing in data analytics and consulting support is no longer a mere option but a strategic imperative. By partnering with experienced consultants who understand the nuances of industrial data and IT-OT convergence, manufacturers can overcome technical challenges, tailor solutions to their specific needs, and ensure that their data strategy delivers real business value. Embracing a data-driven approach to manufacturing will not only position companies for success in today’s data-centric world but will also future-proof them for the challenges and opportunities ahead.