In a previous post on Manufacturing Execution Systems, we explored the implementation from a high-level standpoint, discussed some of the areas where an MES can help, and covered a general business strategy for implementing and leveraging an MES.
In this post, we aim to dive deeper into tangible MES components, describe their integration into an architecture / control system, and provide a complete overview of what they can help you solve in a manufacturing environment.
Introduction to MES
As a fairly brief reminder, an MES lives at the data layer of the automation stack. It does not control the process but rather provides visibility and data that is synthesized from raw data and provides opportunities for improving the manufacturing process.
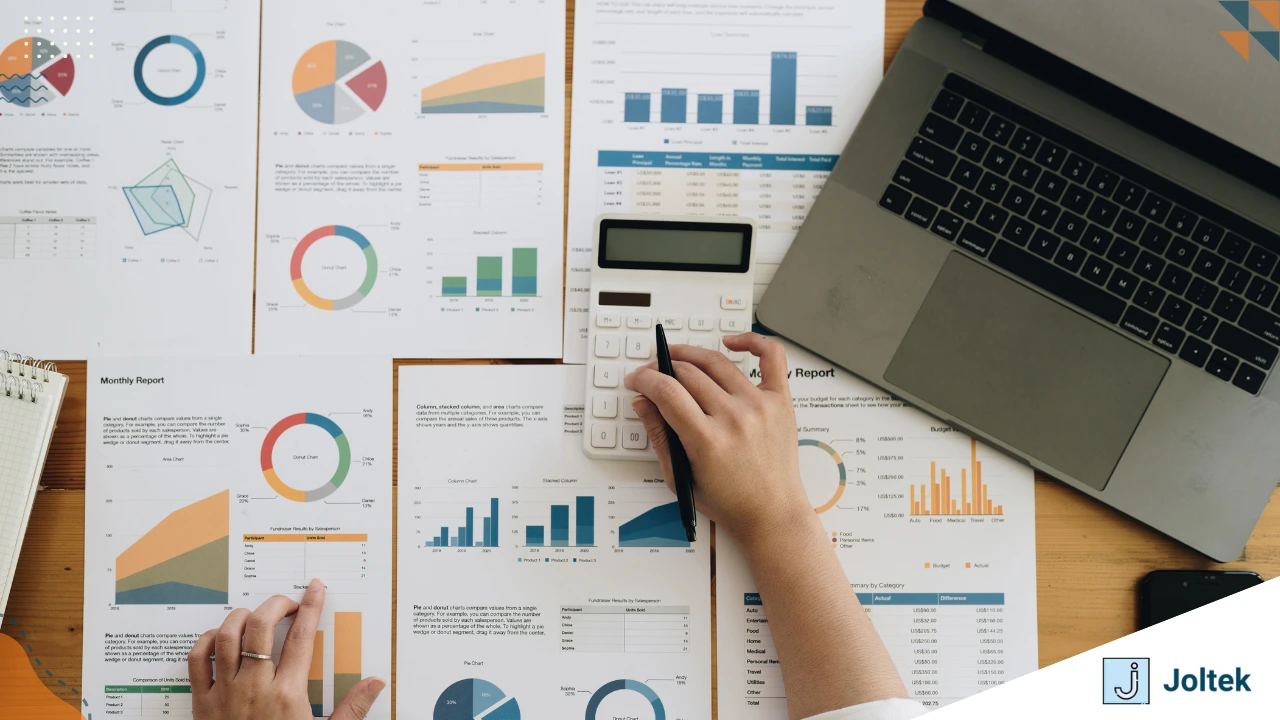
The key distinction from SCADA
The MES layer does not control the process, nor is it focused on presenting raw data. The focus of an MES is to provide synthesized information that provides a long-term picture of a process.
The key distinction from ERP
ERP, or Enterprise Resource Planning, is a set of tools for business oversight. An MES is focused on manufacturing. The main difference is that an ERP is going to have a lot of components that aren’t related to manufacturing - accounting, finance, shipping / receiving, supplier information, scheduling personnel, etc. Some of that data can be pulled into the MES, but the ERP is focused on a business as a whole while the MES is specific to manufacturing.
Key Components of a Manufacturing Execution System
The biggest question manufacturers face is - which components should we care about? The answer is always - it depends…
“Prescription without diagnosis is malpractice” - Vladimir Romanov
If you were to call your doctor and complain to him about acute pain - would he prescribe you medicine? If he’s a good doctor, he wouldn’t until examination.
The same applies in manufacturing. Without knowing the current state of a facility, it’s nearly impossible to tell which MES components would lead to the most impact. However, we can discuss the different components, their general benefits, and provide some general advice as to when they should be used, how they can be used, and ultimately give you the information to make the decision.
Unlike the governing bodies in medicine, it’s up to a private business to decide what they want to do with their money when it comes to these tools… Which is why we see a lot of projects that don’t yield the projected ROI!
Downtime / OEE Tracking
Downtime and OEE tracking are some of the most discussed components of an MES. Before we get into what they are, let’s understand why you might need to understand such metrics.
A story from Procter & Gamble - DDS [Daily Direction Setting]
Having spent multiple years at a state of the art facility from Procter & Gamble, I’ve gained an appreciation for the IWS [Integrated Work Systems], which is basically a derivative of Learn Six Sigma.
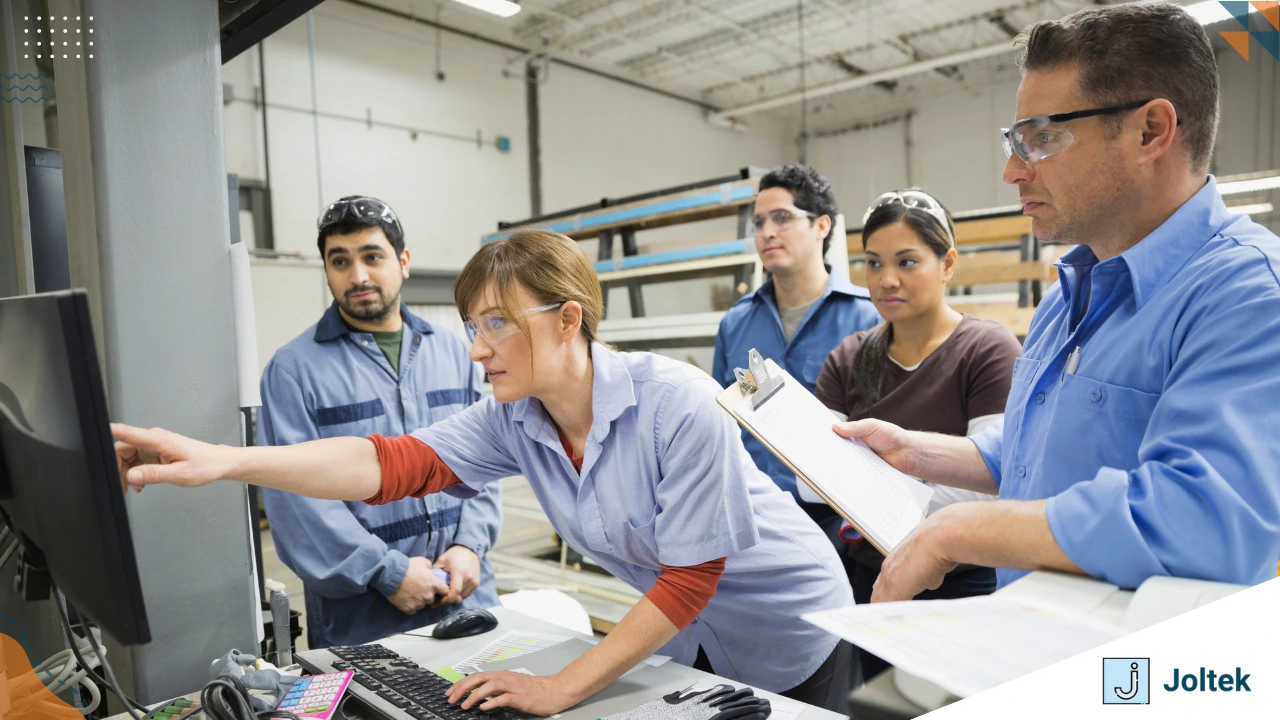
Every morning, on every line, the team would huddle up for the DDS [Daily Direction Setting]. The DDS is basically a very brief (10 min) team meeting to align priorities for the shift to come. The facility had 2 shifts - 6AM - 6PM, and 6PM - 6AM. The DDS was a critical component of achieving the results P&G has seen over the years.
What was the secret sauce here?
Well, the team had full access to data from the previous shift - notes, downtime, OEE, and asset data. They could review what the previous dealt with, understand which areas needed work (maintenance) and what they’d be prioritizing going into their shift.
—
I’ll let you in on a secret - most facilities I visit don’t have any of this data. They’re doing their best to keep production running without understanding where they need to focus for the highest returns.
The Downtime / OEE tracking is a fundamental component of giving people some visibility into their machinery.
Practical OEE Tracking Deployment
What does it take to track OEE from a practical standpoint?
In short, there are several ways of getting OEE data / metrics from a machine.
The simplest approach is to utilize existing sensors which are typically tied into a PLC. By getting production counts, reject counts, and machine state, an integrator can paint a picture as to what the asset / machine is doing.
Here’s an example:
Imagine that you have a casepacker that is putting bottles into boxes.
- At the entrance to the case packer, you have a sensor that detects bottles.
- At the exit of the case packer, you have a sensor that detects cases.
- At the reject chute of the case packer, you have a sensor that rejects “bad” cases (however it is defined at your facility).
- The machine has state logic based on what it’s doing - running, stopped, faulted, starved.
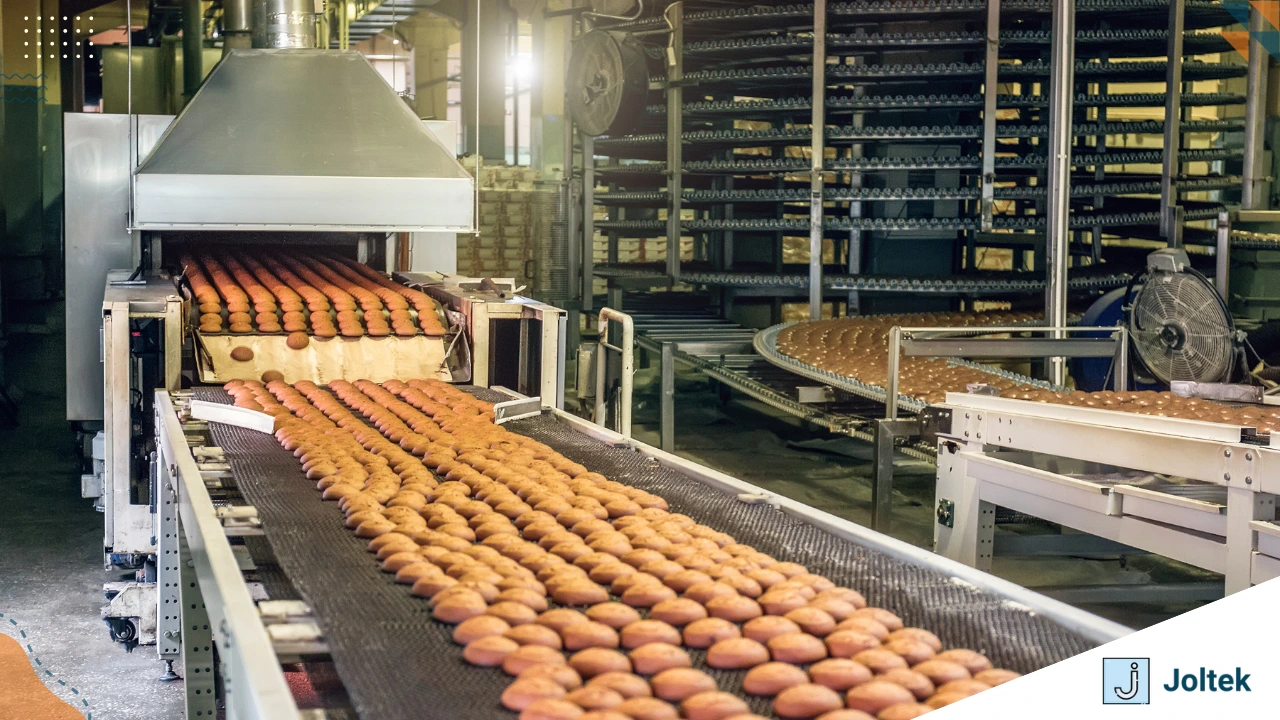
These signals are tied to the MES along with other machines on that line. The MES can synthesize the information and paint a picture as to the downtime, OEE, and, ultimately, the bottlenecks on the line.
The challenges in this deployment lie in understanding the process, understanding the equipment, and being able to send those signals from the machine to wherever the MES is running (edge, on-prem servers, or cloud).
The second option is to deploy sensors dedicated to tracking downtime / OEE. In this case, you’d be tracking the same parameters, but you’ll need to deploy hardware that is completely separated from the current control system. From my experience, this is an alternative for smaller facilities that don’t have dedicated resources or the budget for technical resources that can perform the integration described above. With the right architecture and team, it shouldn’t be difficult to pull this data from an existing system.
What can be expected from Downtime and OEE Tracking?
Downtime and OEE tracking allows manufacturers to understand the state of their floor, lines, and machines. OEE metrics should answer the question as to how productive the process is, which machines are causing the most / least downtime, and point you in the general direction of where you should be looking to improve the process. It’s important to keep in mind that OEE tracking alone isn’t going to solve the problem, nor is it going to provide you with all the data you need, but it’s rather a starting point.
Understanding the state of your assets is important; here’s an example:
The team assumes that the palletizer is constantly down because it’s not producing pallets at the end of the line. The downtime / OEE data paints a different picture - The labaler which seems to always be working, is not keeping up with the speed of the line and is causing the case packer and palletizer to be “starved.” In other words, the palletizer is constantly starting and stopping as it’s not receiving enough materials at the infeed. Rather than focusing on the palletizer, the team should be looking at the labeler and address the issue - figure out how to speed up the labeling process, or adding a second labeler to the line.
Product Track and Trace
Do you understand the journey of your project from raw materials to finished goods? Most manufacturers don’t. The track and trace capability of an MES gives manufacturers the ability to understand and be able to retrieve information about their goods after they’ve left the floor.
Why would you need that?
There are multiple reasons - 1. Regulations, 2. Compliance with the distributor / reseller of your product; 3. Troubleshooting issues in case of a recall or defect, 4. Identification of problematic assets.
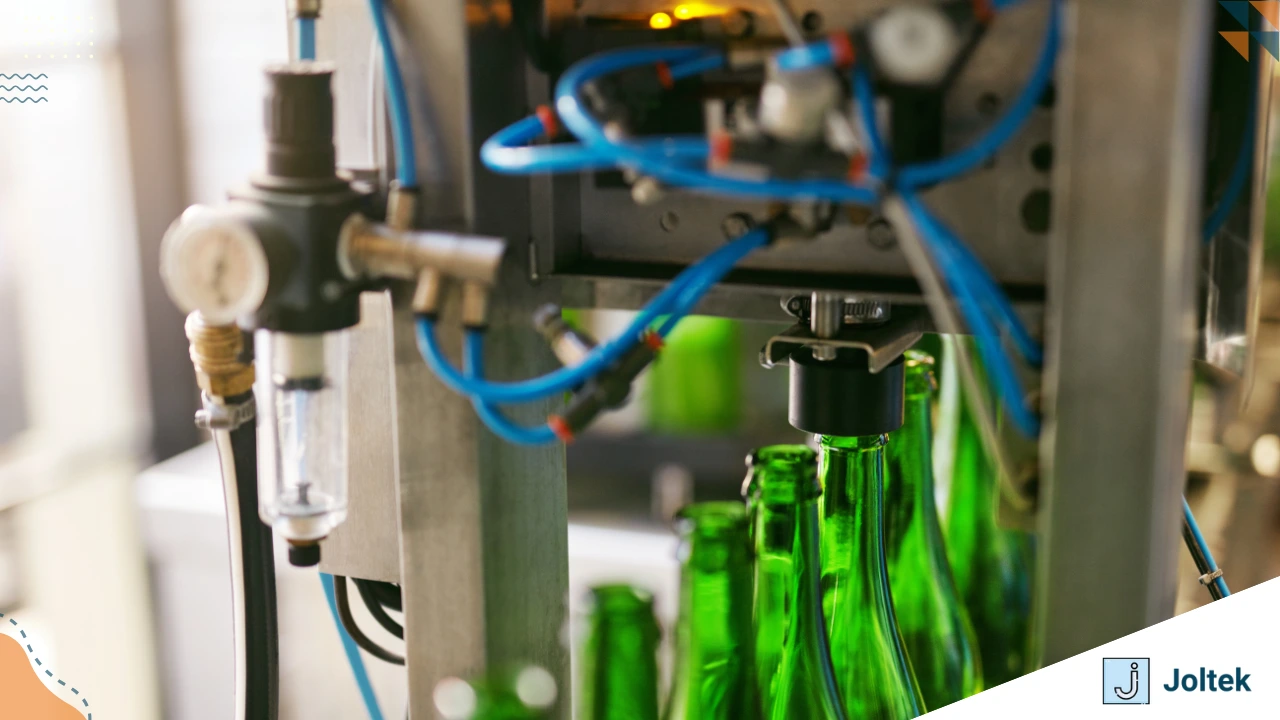
Practical Product Track & Trace Deployment
In most facilities, it’s common to have barcode applicators and scanners in various points of a process. However, these devices are rarely tied to a database that provides traceability. The integration of product tracing is thus a challenge in many environments as automated and manual tools have to be deployed.
Raw materials
Raw materials will generally arrive at your facility with a barcode. This barcode is created by the supplier. You’ll need to have a system capable of handling either this barcode or assigning the raw materials a new one. Keep in mind that depending on the process, the raw materials may go into a larger batch, at which point your system will have to handle aggregation, separation, or a direct feed. This is going to be industry and process-specific.
Production Floor
There are generally two types of processes in manufacturing - batching and discrete. In many cases, a batching process is followed by discrete packaging. For example, a brewery will have both - the brewing process is batching / continuous, while the packaging portion at the filler becomes discrete.
The key decision to be made here is the level of granularity you need for your specific process. Do you need to know how the raw materials are transformed at every stage? Do you need to know which asset has touched every single product? If that’s the case, you’ll need to add a lot of instrumentation and track all of it in a database. As you can imagine, the more you track, the higher the cost.
The most basic tracking involves an operator barcode scanner at the start of the line, and a barcode application at the end of the line by the palletizer. A much more complex system would tag the product as it comes through the line in various stages - a unique ID and tag at the filler, capper, labeler, case packer, palletizer, etc.
Note that if you have a predominantly “batching” based process, you’ll need the batching functionality of the MES to track the process of the batch which will have different implications and benefits for your facility.
Suppliers and Distributors
In many cases, it’s important and good practice to integrate with your suppliers and distributors. This integration isn’t as straightforward as the ones on-site simply because you need to deal with systems you have little control over. At this stage, you’ll need to understand the process of different companies you’re getting materials from, their “digitization” strategy and how you can interface with their systems.
Statistical Process Control
Lean Six Sigma is a methodology pioneered by Toyota that brought the company global recognition for its manufacturing process. Across north American facilities, you’d expect to see various tools that stem from the Lean Six Sigma approach. However, there’s a bigger emphasis on “operational” tools rather than the “Six Sigma” which is what statistical process control provides.
What is statistical process control?
If you’ve taken a statistics class in high-school, or college, you’ve probably learned that there’s a mathematical approach to figuring out when something is an outlier. A very basic example would be class grades - the professor would share the average, and sometimes the mean which would be indicators of how well or poorly you’ve done as related to the class. The further you are from the mean, the more of an outlier your grade is.
In manufacturing, you can apply the same logic. For example, if you’re filling bottles (or cans) with a liquid and weighing them, you’d expect to have a certain level as a mean, and a standard deviation.
Why is this important?
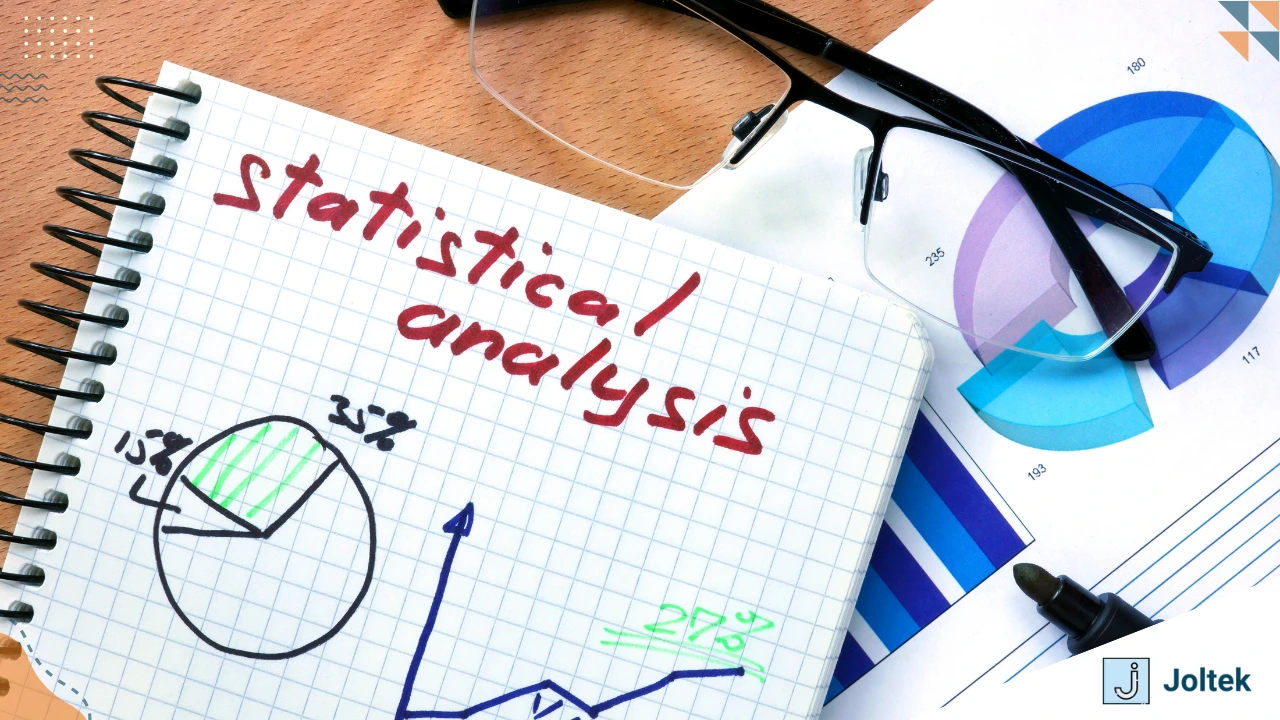
Continuing with the same example, imagine that your filler is filling a 300ml can. The filler is going to overfill and underfill as nothing is exact. Here’s a sample - 301ml, 298ml, 305ml, 299ml, 309ml, etc. The problem is two-fold - as you overfill, you’re giving away “free” product; as you underfill, you risk getting a customer complaint. Both need to be balanced.
This data can help you fine tune the filler and understand how much of an improvement your team has made. In other words, as improvements are made, the standard deviation should decrease; the filler should be more consistent.
To tie this back to the “larger picture,” you’re saving money on overfilling and on customer complaints which both cost your business money.
Practical Statistical Process Control Deployment
You need to identify key areas where statistical process control makes sense for your production team. Chances are, some of the components of your process simply can’t be adjusted, which means that the data you collect will be useless.
From a data standpoint, you need to track a set of key measurements over a long enough period of time to get a baseline. As outlined previously, most of this data is likely already within your control system; in certain cases, you’d need extra instrumentation.
You’ll need to speak with a professional to understand if you need individual measurements or an aggregate - In other words, are you sending the reading for the MES to complete these computations, or is your MES asking you for the mean, standard deviation, etc to be computed by the control system?
My experience has shown that in these applications, your facility requires a robust network architecture, which means that the control systems should be able to communicate, be able to transfer significant amounts of data, and have a repository into which they’ll be sending this data. Depending on where the MES is hosted, the final destination for this data could be local, or remote (off-prem servers, cloud, etc.).
Benefits of Statistical Process Control
We’ve briefly outlined an example of what can be done using statistical process control, but that’s just the basics. Understanding data to this granularity allows a skilled team to fine-tune different areas of the process, collect data to influence supplier negotiations, correct quality defects, and reduce stops related to process variations. Here are some further examples of the above as they relate to process control:
1. Process Fine Tuning
A machine is used to label cans as they exit the filler. The specifications of the OEM are such that the label will be applied with 4mm accuracy. Without proper maintenance, this deviation has increased. The team made the necessary adjustments and saw the labeler perform at the OEM specs.
2. Supplier Negotiations
A case packer is expecting packaging materials of two feet wide with a deviation of 1 inch. The machine experienced excessive stops due to improper materials - the team began to collect data. It was quickly apparent that the materials sent by the supplier weren’t meeting the specifications agreed upon. The team used the data to negotiate a significant discount based on the “subpar” materials received.
3. Quality Defects
Every process has a set of specifications beyond which the product is deemed to be a “reject.” This can relate to a measurement, ingredient presence, process quality, usability, etc. A basic example would be size - Imagine that your process is machining pens from a block of metal. In general, CNCs are known to have high tolerances, but as they age and receive less maintenance, they will deviate. This will result in some of your product (pens) to be “out of spec.” Does this matter to you? In the case of a pen it might not, but what if it was a medical device? By knowing the measurement and the statistical deviation, your team can make adjustments to the process and correct the issue before it gets worse.
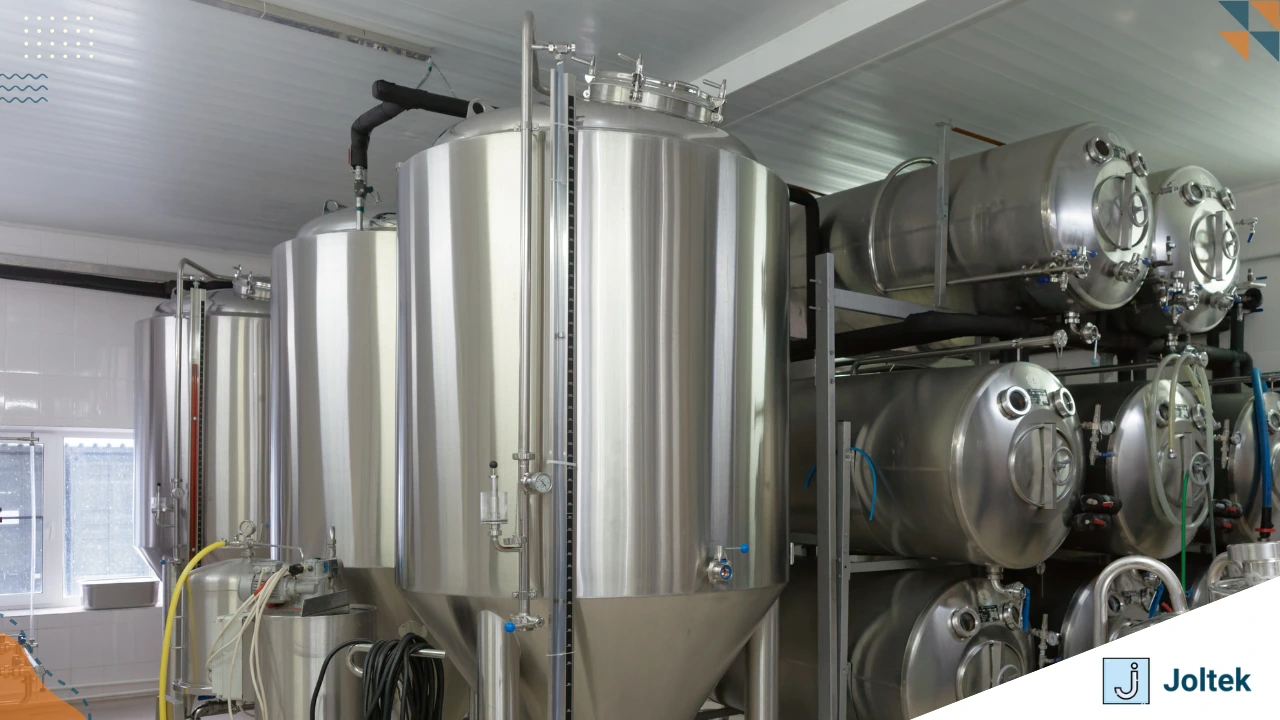
4. Stops Due to Statistical Process Control
As you can imagine, every machine expects to have raw materials of certain parameters fed into it. Let’s take a case packer for example - if the jars are 10cm in diameter, everything is fine. If the jars are 11cm in diameter the machine will almost always jam. There’s thus a point at which the machine will no longer tolerate the deviation in the size of the jars. By having the data, the team can address the issue with the jars before they get into the case packer.
Automation of Statistical Process Control
In certain facilities, it’s possible to automate the adjustment in process based on the data model supplied into the MES. The challenge is that your team must be confident in the adjustments made and most likely set certain guardrails depending on the process. In most facilities, this would be reviewed by the team of process engineers and manually adjusted as needed and monitored.
Conclusion on MES
We’ve covered three interesting applications / tools of an MES. There are certainly other applications that would fall under this category. As you shop for a solution, and team to help you implement, consider that this is a journey rather than a project. Understand their experience, their network, their approach, and evaluate if that’s what you’re looking to do. There’s rarely a one-size-fits-all solution when it comes to MES as many processes are unique, business strategies are different, and equipment differs in maturity.