Introduction to Unified Namespace (UNS)
In today’s increasingly interconnected manufacturing environments, the demand for real-time data exchange across diverse systems has grown exponentially. With the rise of Industry 4.0 and digital transformation, manufacturers are continually searching for ways to streamline data flow across equipment, departments, and entire facilities. But while the benefits of a fully integrated system are clear, the path to achieving seamless data flow is complex, often hindered by data silos, compatibility issues, and inefficient, point-to-point connections.
The Unified Namespace (UNS) is a revolutionary approach designed to address these challenges. In essence, a UNS serves as a centralized, real-time hub that brings together the entire structure, state, and events of a manufacturing enterprise in a single, unified data repository. By following established standards like the ISA-95 hierarchical model, UNS enables every system in an organization to communicate through a common, organized framework, providing a single source of truth that can be accessed by all relevant stakeholders.
Why UNS Matters
The traditional methods of connecting industrial systems—often relying on point-to-point integrations, proprietary interfaces, and complex, multi-layered architectures—are becoming increasingly unsustainable. These systems may have worked well when automation was simpler and data requirements were limited, but in modern manufacturing, they create several problems:
- Data Silos: Systems across manufacturing (like ERP, MES, SCADA, and PLCs) often operate independently, making it difficult for data to flow freely.
- Complex Integrations: Each point-to-point connection requires unique engineering and maintenance, consuming time, resources, and adding potential points of failure.
- Slow Data Access: Traditional architectures lack the real-time responsiveness that modern manufacturing demands, where delayed access to critical data can hinder decision-making and slow response times.
UNS addresses these challenges head-on by creating a single, unified data structure. Unlike traditional systems, UNS allows all data to be accessible within a single framework, where every device, application, or system publishes to and consumes from a central source. This significantly reduces integration complexity, allows real-time data access across the enterprise, and improves the ability to act on insights immediately.
Purpose of this Guide
This guide provides an in-depth exploration of the Unified Namespace concept, covering its architecture, its role in data-driven manufacturing, and the practical benefits it delivers. You’ll learn how UNS can transform your operations by fostering real-time data exchange, reducing integration costs, and enhancing scalability. This guide will also outline how to implement UNS using protocols like MQTT and Sparkplug, key tools, and examples from real-world manufacturing to illustrate its impact.
By the end, you’ll have a comprehensive understanding of how UNS can serve as a foundational element for achieving a truly data-driven manufacturing operation. Whether you’re an IoT architect, an industrial engineer, or a decision-maker in manufacturing, this guide will equip you with the knowledge to leverage UNS as a strategic asset in your digital transformation journey.
Understanding the Foundation of UNS
The Concept of a Unified Namespace
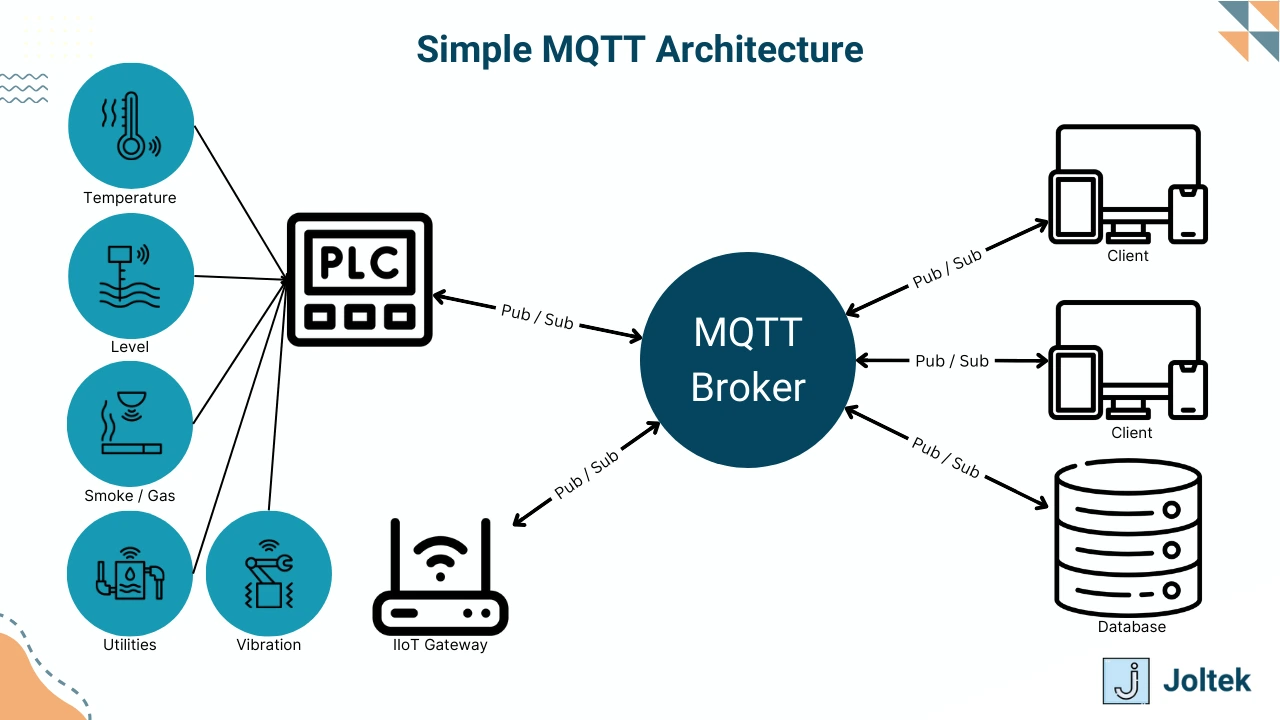
Definition and Core Principles
The Unified Namespace (UNS) serves as a central data repository and structure for an organization’s entire manufacturing ecosystem, establishing a single source of truth for all data related to production, events, and operational state. The primary principles that define UNS include:
- Single Source of Truth: By centralizing data from across the enterprise, the UNS provides a consistent and unified reference point, enabling seamless data access and consistency.
- Event-Based Updates: Unlike systems that rely on continuous polling, the UNS adopts an event-driven approach. Data is updated only when changes occur, conserving bandwidth and enabling faster response times for critical systems.
- ISA-95-Inspired Hierarchy: Following the ISA-95 standard, UNS organizes data into hierarchical levels that mirror a manufacturing business structure. This enables straightforward data organization and aligns closely with manufacturing operations, from the enterprise level to individual shop-floor devices.
Key Components
A comprehensive UNS comprises the following core elements:
- Structure: Reflecting the operational hierarchy (enterprise, site, area, line, and cell), this organizational framework allows for straightforward data access and integration across various systems and layers.
- Events: Representing real-time occurrences, these events might include production shifts, maintenance alerts, sensor readings, and more. This real-time information empowers applications and users to act immediately as new data becomes available.
- State: Reflecting the current condition of each system, machine, or process, the state data in UNS enables users to assess and react to manufacturing situations in real time.
Why Traditional Data Architectures Fall Short
Common Limitations in Traditional, Layered, or Point-to-Point Systems
Many traditional data architectures in manufacturing employ layered, point-to-point, or siloed structures. These architectures may have served well in simpler production environments, but they encounter significant challenges in modern manufacturing due to:
- Complexity: Layered architectures create complex, point-to-point connections that often require specialized integration and frequent maintenance.
- Limited Scalability: As companies add more devices, applications, and analytics tools, legacy architectures struggle to scale without extensive engineering and costly upgrades.
- Inflexibility: Integrating new data sources into layered or point-to-point systems requires unique engineering, which limits the agility needed for real-time operations.
- Data Silos: With data stored within separate systems, organizations often face barriers to sharing and analyzing data holistically, hindering effective decision-making.
Examples of Friction in Traditional Systems
In a conventional setup, for instance, a programmable logic controller (PLC) on the shop floor may need to send data to a cloud application. However, data often has to pass through multiple layers, such as SCADA, MES, and ERP, with each layer requiring proprietary configurations and integration points. This often results in:
- Data Delays: Data may take several minutes or even hours to be available to the end-user application.
- Data Compatibility Issues: Each system layer may use different data formats or communication protocols, requiring manual intervention or complex integrations.
- Increased Costs and Maintenance: Multiple, customized integrations require ongoing maintenance, especially as production requirements change or expand.
How UNS Overcomes These Limitations
Unified Structure for Real-Time Data and State Across Systems
The UNS framework consolidates all data and event information into a single, accessible structure. By adopting a unified namespace, organizations can access the real-time status, events, and hierarchical structure of operations without needing to navigate across multiple systems or deal with various integration challenges.
Reduced Reliance on Specialized Point-to-Point Integrations
With a central broker in place (typically an MQTT broker), UNS minimizes the need for direct connections between individual systems. This reduces the complexity of integrations and allows for more plug-and-play connectivity, enabling applications and devices to seamlessly publish and consume data within the UNS structure.
Enabling Data Democratization Across the Enterprise
By standardizing and centralizing data through UNS, data democratization becomes a practical reality. Information, whether it originates from the shop floor or from cloud applications, is now accessible enterprise-wide, allowing departments to draw insights and collaborate without needing complex interdepartmental data-sharing mechanisms. This enables:
- Real-time access to crucial data for decision-making across departments.
- Accelerated innovation as new applications and tools can be added to the UNS without requiring custom integrations.
- Enhanced collaboration between teams, fostering a more holistic approach to addressing manufacturing challenges and achieving operational goals.
The UNS Architecture and Design Principles
%2520A%2520Guide%2520to%2520Data-Driven%2520Manufacturing%2520Transformation.webp)
Core UNS Components
Data Producers and Consumers
In a Unified Namespace, data producers and consumers are the building blocks of the data ecosystem:
- Data Producers: Devices, sensors, applications, or any source that generates and sends data to the UNS. Producers publish data to specific topics in the namespace, including PLCs, SCADA systems, and MES platforms.
- Data Consumers: Applications, machines, or systems that subscribe to the topics within UNS to retrieve data. Consumers leverage this data for real-time decision-making, analytics, or process control.
By using a publish/subscribe model, UNS minimizes the need for direct, point-to-point connections, allowing data producers and consumers to interact through a centralized structure.
Data Hierarchy and Topic Structure
UNS topic structures organize data to reflect the hierarchy of the manufacturing environment:
- ISA-95-Based Organization: By following the ISA-95 model, data is structured in a manner that mimics the operational hierarchy, from enterprise level down to individual devices. This enables consistency and clarity in accessing data across levels.
- Structured vs. Unstructured Organization: Structured organization adheres to the hierarchy and naming conventions aligned with ISA-95, which makes data easily navigable. Unstructured organization, often found in traditional architectures, lacks this hierarchy, making it more challenging to locate and contextualize data.
For example, in a structured UNS, a sensor on a bottling line would be identified by a path such as enterprise/site/area/line/sensor, clearly indicating its place within the production hierarchy.
Semantic Contextualization
UNS enhances data’s value by adding semantic context to otherwise raw or disparate data streams. Each piece of data is associated with its purpose, location, and relationships within the organization. This semantic hierarchy enables manufacturers to extract actionable insights from data by understanding its broader operational context.
For example, temperature data labeled with /enterprise/site/line1/sensor1/temperature carries meaningful context about the location, type, and role of that data within the operation.
Designing a UNS Hierarchy
Overview of ISA-95 Model and Its Influence on UNS
The ISA-95 model offers a well-defined framework for organizing data within manufacturing environments. It defines hierarchical levels within the manufacturing ecosystem:
- Enterprise: The highest level, covering business-wide data and information, including enterprise resource planning (ERP).
- Site: Represents specific manufacturing locations or plants.
- Area: Defines sections within the plant, such as production areas.
- Line: Represents individual production lines or units.
- Cell: The most granular level, where individual machines and sensors operate.
Levels of UNS: Enterprise, Site, Area, Line, Cell
By adhering to the ISA-95 levels, manufacturers can design a UNS hierarchy that aligns with their operational needs:
- Enterprise Level: Aggregates data across multiple sites for high-level insights.
- Site Level: Provides a centralized view of each manufacturing location’s data.
- Area Level: Organizes data from different departments or production sections.
- Line Level: Enables tracking and monitoring of production lines individually.
- Cell Level: Focuses on data from individual machines or devices, supporting granular monitoring and control.
Best Practices for Structuring Data Based on Organizational Needs
When designing a UNS, consider these best practices:
- Define Standard Naming Conventions: Use consistent naming conventions for topics to maintain a structured, searchable, and understandable hierarchy.
- Organize by Function and Geography: Align the structure with the physical and operational layout of the plant for greater accessibility.
- Consider Future Scalability: Design the hierarchy with flexibility to accommodate future additions, such as new machines, lines, or even entire sites.
- Limit Depth of Topic Levels: Avoid creating overly complex topic paths, as they can hinder performance and usability.
Data Contextualization and Processing
Defining and Implementing Topic Hierarchies and Schemas
Implementing topic hierarchies and schemas within the UNS ensures data is accessible in a contextualized and meaningful way. This involves:
- Topic Hierarchies: Organize data by levels (enterprise, site, line, etc.) and create a logical path for accessing each data point.
- Schemas: Define consistent formats for message payloads, providing standardization across different types of data, such as temperatures, statuses, and events.
For instance, data from a temperature sensor could be organized as follows:
- Topic: /enterprise/site/line1/cell1/sensor1/temperature
- Schema: { "timestamp": 1672531200, "temperature": 75, "unit": "C" }
Examples of Contextualizing Raw Data for Industrial Applications
In industrial applications, raw data is typically transformed to include context, enhancing its utility. Examples include:
- Asset Health Monitoring: Raw vibration data from equipment can be processed to generate insights into the health of the equipment and preemptively indicate maintenance needs.
- Quality Assurance: Data from sensors on production lines can be contextualized to flag deviations from quality standards, enabling immediate interventions.
- OEE Calculation: Data on machine speed, downtime, and output from various systems can be integrated to monitor overall equipment effectiveness (OEE) in real time.
Leveraging Tools for Data Processing and Transformation
Several tools support UNS data processing, contextualization, and transformation:
- Node-RED: A flow-based development tool that enables data routing, transformation, and integration.
- HiByte: A data operations platform for industrial applications that supports data contextualization, modeling, and transformation.
- Ignition: A comprehensive industrial automation tool that allows for real-time data handling, visualization, and control, with native support for MQTT and UNS configurations.
Protocol Conversion in UNS
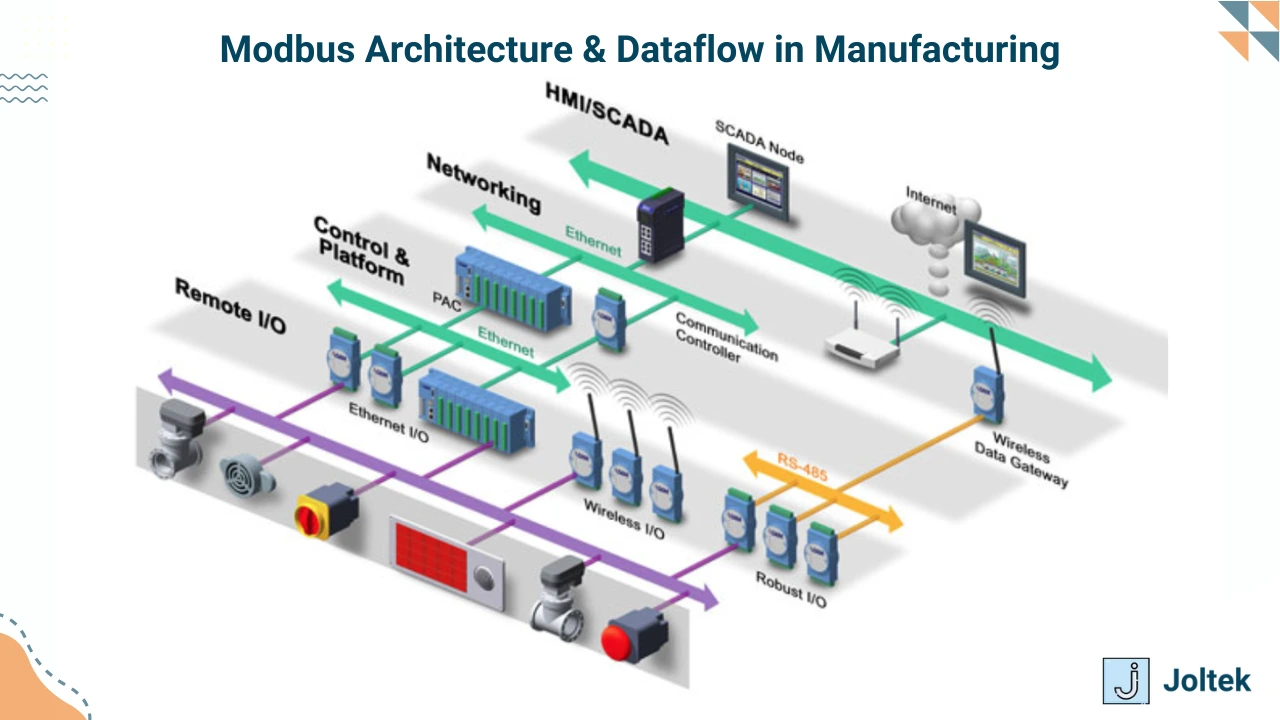
Role of Protocol Converters
To integrate legacy and non-MQTT systems, protocol converters play a vital role. They convert data from various protocols (e.g., OPC UA, SQL, Modbus) into MQTT format, enabling it to be incorporated into the UNS.
Practical Examples and Tools for Protocol Conversion
For many manufacturers, data sources vary in type and protocol, from SQL databases to PLCs. Protocol converters like BENTOS can transform these sources to MQTT, ensuring compatibility with the UNS. Practical use cases include:
- OPC UA to MQTT: Converting event data from OPC UA-compliant devices to MQTT allows for seamless integration within the UNS.
- SQL to MQTT: Many manufacturing systems store data in SQL databases. Protocol converters transform SQL data into MQTT topics, enabling historical or batch data to be included within the real-time UNS.
- Modbus to MQTT: Modbus devices are common on factory floors. Converting Modbus data to MQTT standardizes communication and integrates older devices into the UNS seamlessly.
These protocol conversion practices enable manufacturers to leverage existing equipment and systems while moving toward a unified, scalable data architecture.
Implementing UNS with MQTT and Sparkplug
MQTT as the Backbone of UNS
Benefits of MQTT for UNS Implementation
MQTT (Message Queuing Telemetry Transport) serves as the ideal protocol for UNS due to several key advantages that align with the needs of industrial environments:
- Low Bandwidth: MQTT’s lightweight messaging minimizes network traffic, reducing costs and enabling reliable data transfer in environments with limited bandwidth.
- Event-Driven: Unlike traditional polling systems, MQTT supports an event-driven architecture, where data is sent only when there’s an update, optimizing network efficiency.
- Lightweight Protocol: MQTT’s simple design is suitable for low-power devices, making it practical for connecting various edge devices across the UNS.
Key Features of MQTT Relevant to UNS
To effectively implement a UNS, it’s essential to leverage MQTT’s core features that enhance data management and distribution:
- Publish-Subscribe Model: This model allows multiple data producers to publish to a single topic, while consumers subscribe to the topics they need. It enables seamless, scalable data sharing without complex, point-to-point connections.
- Quality of Service (QoS) Levels: MQTT’s three QoS levels (0, 1, and 2) provide control over message delivery. For critical industrial data, QoS 1 (at least once) or QoS 2 (exactly once) ensures reliable message delivery, essential for accurate real-time monitoring.
- Retained Messages: MQTT can retain the last message sent on a topic, ensuring that newly connected subscribers receive the most recent state of the data. This feature supports rapid onboarding of new devices without data gaps.
Enhancing MQTT with Sparkplug
Overview of the Sparkplug Specification
Sparkplug is a specification built on top of MQTT that defines a standardized format for messages, including topic structure, payload encoding, and state management. It is specifically designed for industrial IoT and UNS implementations:
- Structured Data: Sparkplug enables a standardized structure for MQTT messages, ensuring consistency across different data producers and consumers.
- State Management: Sparkplug provides state management features, allowing the system to detect when devices are offline or online, a critical feature in maintaining data integrity and reliability in UNS.
State Management with Sparkplug B
Sparkplug B enhances MQTT’s capability with state management, which ensures devices’ statuses are known throughout the system. This is crucial for maintaining a reliable UNS:
- Device Online/Offline Status: With Sparkplug B, devices periodically publish birth and death messages. A birth message indicates a device is online and ready to communicate, while a death message signals the device has disconnected.
- Ensuring Data Integrity: Sparkplug’s state management prevents consumers from making decisions based on outdated or stale data, as the system is immediately notified of a device’s status change.
How Sparkplug’s Data Model Integrates with UNS
Sparkplug’s data model aligns well with the UNS structure by:
- Standardizing Data Representation: Data from various sources is formatted in a consistent, hierarchical manner, allowing seamless integration and interoperability.
- Scalability: Sparkplug organizes data in a structure that can easily scale across multiple sites, making it suitable for enterprise-wide deployment.
- Contextual Relevance: The Sparkplug format inherently includes metadata that adds context to the data, simplifying integration with different levels within the UNS (e.g., site, line, or cell level).
Setting Up the MQTT Broker
In-House vs. Cloud-Based Brokers
The MQTT broker is the central component of the UNS, acting as the intermediary between producers and consumers. Choosing between an in-house and cloud-based broker is critical:
- In-House Brokers: Offers full control over the data, infrastructure, and security but may require more maintenance and IT resources. Suitable for companies with high data sensitivity or strict regulatory compliance.
- Cloud-Based Brokers: Provides scalability, reduced infrastructure costs, and easier access to advanced features (e.g., clustering, redundancy). Ideal for organizations with remote sites or limited in-house IT support.
Key Broker Features
When setting up an MQTT broker for a UNS, it’s essential to consider certain features to ensure robustness and scalability:
- Broker Federation: Federation allows for multiple brokers to be connected, creating a distributed MQTT network. This setup is especially valuable in large-scale deployments where different brokers manage data at various levels (e.g., site-level brokers connected to an enterprise broker).
- Clustering: Clustering enables multiple brokers to work as a single unit, enhancing the reliability and scalability of the system. This setup ensures data continuity, as messages are replicated across the cluster in case one broker fails.
- Redundancy: By using multiple brokers or clustering, redundancy provides failover capabilities, ensuring the UNS remains functional even if one part of the system goes down.
Practical Examples of Data Flow from Producers to Consumers
To illustrate the data flow in a UNS architecture:
- Data Publication by Producers: Devices on the factory floor, such as PLCs, sensors, and SCADA systems, publish data to MQTT topics. For instance, a sensor on production line 1 might publish to /enterprise/site/line1/sensor1/temperature.
- Data Routing through the Broker: The MQTT broker routes these messages to all consumers who have subscribed to relevant topics, such as /enterprise/site/line1/#, enabling access to all data under line 1.
- Data Consumption by Subscribers: Applications like MES, ERP, and analytics platforms subscribe to the topics they need, ensuring they receive real-time data without creating multiple point-to-point connections. For instance, an ERP system might subscribe to /enterprise/site/line1/production_status for live updates.
This publish-subscribe model simplifies the data distribution process, enhances scalability, and improves data availability across the entire organization. By implementing MQTT and Sparkplug within the UNS, manufacturers gain a flexible, scalable, and efficient data ecosystem.
Practical Applications of UNS in Manufacturing
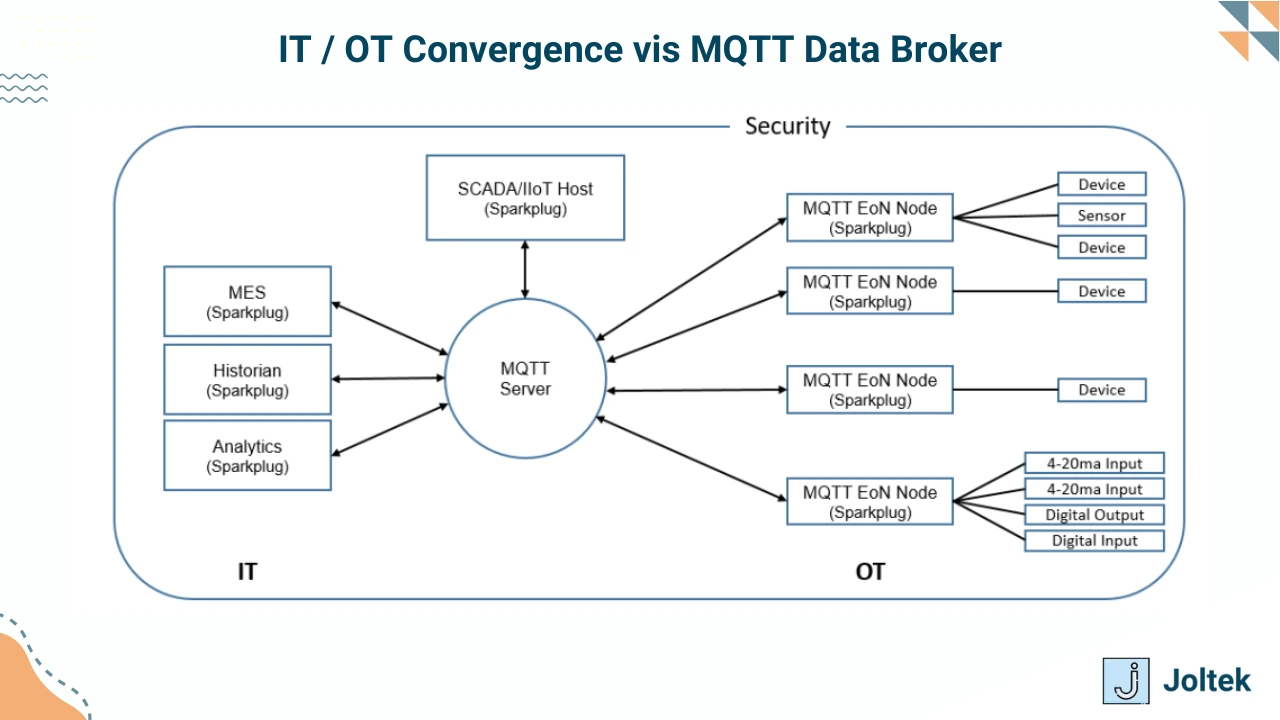
Integrating Common Industrial Components into a UNS
Examples of Data Integration for MES, SCADA, ERP, and IIoT Systems
The UNS’s capability to integrate with various industrial systems provides a unified data ecosystem that facilitates seamless data exchange:
- Manufacturing Execution Systems (MES): MES platforms can subscribe to UNS topics to access real-time production data and quality metrics, enabling automated production scheduling and quality control.
- Supervisory Control and Data Acquisition (SCADA): SCADA systems can both publish and subscribe to UNS topics, making it possible to track real-time data from sensors and equipment on the factory floor and relay critical insights for operational efficiency.
- Enterprise Resource Planning (ERP): ERP systems can retrieve production and inventory data from the UNS to enable streamlined procurement, order tracking, and resource planning across manufacturing sites.
- Industrial IoT (IIoT) Systems: With IIoT devices integrated into the UNS, data from a wide array of devices can be aggregated, enabling advanced analytics, condition monitoring, and other smart manufacturing initiatives.
Use Cases: Real-Time Monitoring, Predictive Maintenance, OEE Tracking
UNS enables critical applications in manufacturing by making data accessible across different levels of the enterprise:
- Real-Time Monitoring: With live access to data from all levels of production, operators and management can monitor key performance indicators (KPIs), detect anomalies, and take swift action.
- Predictive Maintenance: By aggregating data from equipment and running predictive algorithms, the UNS enables maintenance teams to anticipate equipment failures and schedule interventions before breakdowns, reducing downtime and extending equipment life.
- Overall Equipment Effectiveness (OEE) Tracking: Data on machine performance, availability, and quality can be automatically collected and analyzed through the UNS, allowing for accurate, real-time OEE calculation and reporting to support continuous improvement.
Role of UNS in Enabling Data-Driven Decision Making
Examples of How Organizations Use UNS for Actionable Insights
The centralized, structured data that the UNS provides is essential for data-driven manufacturing, where real-time insights enable better decision-making:
- Production Optimization: With data from various machines and systems unified in real-time, manufacturers can identify bottlenecks and adjust processes for improved efficiency.
- Supply Chain Management: ERP and MES systems that access data from the UNS can better forecast demand, manage inventory levels, and optimize the supply chain in response to production data.
- Energy Management: UNS data on energy consumption across production lines can help facilities identify high-consumption processes and implement energy-saving measures, contributing to sustainability goals.
Broker Federation and Scaling the UNS
Broker Federation: Explanation and Benefits of Federating MQTT Brokers for an Enterprise-Wide UNS
Broker federation involves connecting multiple MQTT brokers to enable data distribution across large, multi-site deployments. This approach supports scalability by:
- Load Distribution: Dividing data across brokers reduces the load on any single broker, improving system reliability and preventing data bottlenecks.
- Fault Tolerance: With federation, each broker can continue functioning independently, and disruptions in one part of the network do not impact the entire system.
- Efficient Data Flow: Federation allows each facility to manage its local data while sharing relevant data with the broader enterprise, reducing latency and optimizing bandwidth.
Structuring UNS Across Multiple Plants or Production Lines
A federated UNS can be structured to represent the organization’s physical and operational hierarchy, such as:
- Machine-Level Brokers: Each machine can connect to a local broker to send data to the line or site broker.
- Line-Level Brokers: Each production line aggregates data from its machines and transmits it to the site broker.
- Site-Level Brokers: Each facility’s site broker aggregates data from all production lines and forwards it to an enterprise-level broker for centralized monitoring and analysis.
- Enterprise-Level Broker: The central broker consolidates data from all sites, providing enterprise-wide visibility and enabling cross-site comparisons and reporting.
Examples of Broker Federation at the Machine, Line, Site, and Enterprise Level
For instance, a global manufacturing company with multiple production sites might federate brokers at different levels:
- Machine Level: Sensors on each machine connect to a local machine broker, which transmits data to the line broker.
- Line Level: The line broker consolidates data from all machines on the production line, forwarding only necessary metrics to the site broker.
- Site Level: The site broker aggregates data across production lines, sharing insights with other site brokers and the enterprise broker.
- Enterprise Level: The enterprise broker aggregates high-level metrics and analytics from all sites, providing corporate leadership with a comprehensive overview of operations across the company.
Cybersecurity and Data Governance in UNS
Key Cybersecurity Practices to Secure UNS Data Flows
Implementing a secure UNS requires robust cybersecurity measures to safeguard data and protect against unauthorized access:
- Encryption: Encrypt data flows between devices, brokers, and applications to protect sensitive information and prevent eavesdropping.
- Access Control: Use role-based access control (RBAC) to restrict data access based on user roles and responsibilities, ensuring that only authorized personnel can access certain data within the UNS.
- Device Authentication: Require each device to authenticate with the broker before it can publish or subscribe, preventing unauthorized devices from accessing the UNS.
Managing Access Control and Permissions within the UNS
Proper access control is essential to maintaining data integrity and preventing unauthorized data access within the UNS:
- Role-Based Access: Set permissions based on roles, such as operators, supervisors, and engineers, to control who can publish or consume data within the UNS.
- Data Segmentation: Structure data to restrict access to specific levels (e.g., site-level data is only accessible to site personnel), ensuring that employees only access data relevant to their roles.
- Audit Trails: Implement logging to track access and modifications within the UNS, enabling compliance audits and investigations when needed.
Data Governance Best Practices for Ensuring Compliance and Data Integrity
Data governance ensures that the data flowing through the UNS meets quality, compliance, and integrity standards:
- Data Quality Standards: Define standards for data formats, naming conventions, and update frequency to maintain consistency across all UNS topics.
- Compliance with Regulations: Ensure that data governance practices align with regulatory requirements, such as GDPR, CCPA, or industry-specific standards, to protect data privacy and avoid legal issues.
- Data Ownership and Responsibility: Assign data stewardship roles within the organization to manage data ownership, resolve quality issues, and oversee the governance of UNS data flows.
By incorporating these applications, federation structures, and security practices, manufacturers can fully harness the UNS to create a secure, scalable, and data-driven environment that supports innovation and operational excellence.
UNS Benefits and Long-Term Strategy
Benefits of UNS for Digital Transformation
Data Democratization: Making Data Available Across the Enterprise
A Unified Namespace democratizes access to data, making it readily available across departments and functions. By centralizing real-time data from production lines, inventory, quality, and maintenance systems, UNS enables different teams to collaborate seamlessly. The shared access promotes informed decision-making and boosts cross-functional alignment toward strategic goals.
Cost and Time Efficiency: Reduced Complexity in Integrations and Easier Scalability
With a UNS in place, the traditional complexities and high costs associated with point-to-point integrations are minimized. A single data model reduces the need for multiple custom integrations, enabling faster system expansions and decreasing overall IT workload. Additionally, UNS’s scalable architecture allows manufacturers to add new equipment, sites, or digital tools without significant reconfiguration, enhancing the long-term cost efficiency of the system.
Flexibility and Future-Proofing: Adaptability to Add New Systems, Protocols, or Components as Needed
A UNS provides a future-proofed architecture that easily accommodates new protocols, smart devices, and other industrial advancements. Manufacturers can integrate new data sources or technologies without extensive redesign, ensuring the architecture evolves as technology and business needs change. This flexibility also helps reduce the risk of obsolescence, which is crucial for long-term sustainability in digital transformation.
Real-World Examples of UNS in Action
Case Studies or Hypothetical Examples of UNS Driving Improvements in Manufacturing
- Example 1: Real-Time Production Monitoring – A manufacturer implements a UNS to integrate SCADA, MES, and ERP data into a unified view. With real-time visibility across systems, plant managers can detect production issues immediately and allocate resources to resolve them. This system reduced downtime by 15% and improved production speed by 10%.
- Example 2: Predictive Maintenance – By connecting sensor data from various machines to a UNS, a company enables predictive maintenance models that identify potential equipment failures. With early warnings and preventive actions, the company reduced unexpected breakdowns by 25%, minimizing both maintenance costs and lost production hours.
- Example 3: Streamlined Compliance and Quality Control – Using a UNS, a pharmaceutical manufacturer consolidates quality control, batch production, and regulatory compliance data. This consolidated approach reduces audit preparation time by 50% and ensures compliance across facilities, supporting real-time quality tracking and reporting.
How Manufacturers Have Reduced Integration Costs, Improved Response Times, or Achieved Real-Time Visibility
Manufacturers that adopt UNS report reduced integration costs by up to 30% due to fewer customizations and shorter deployment times. Real-time data accessibility across the organization also enables quicker response times to operational changes, with plant managers and decision-makers able to act on live information rather than delayed reports. Moreover, the ability to see real-time performance metrics, such as OEE, allows organizations to make proactive adjustments, fostering a more agile manufacturing environment.
Best Practices for Sustaining UNS Success
Continuous Monitoring and Management of Data Flows
To maintain a robust UNS, regular monitoring of data flows is essential. Data from various systems should be continuously checked for quality, relevance, and accuracy to ensure it meets operational needs. Automated tools and protocols for identifying and addressing inconsistencies can prevent data bottlenecks and maintain the integrity of the unified data source.
Preparing UNS for the Future: Adding Smart Devices, Optimizing Edge Processing
As new devices and industrial technologies emerge, updating the UNS to incorporate these changes will sustain its value. Integrating edge devices with local processing capabilities can streamline data handling and enhance real-time responsiveness, especially in cases where instant feedback loops are critical. Preparing for additional smart devices and enhanced edge computing capacities helps keep the UNS architecture at the forefront of operational technology.
Evolving the UNS to Keep Up with Technological Advances and Changing Business Needs
Regularly revisiting and revising UNS structures and data hierarchies in response to technological changes and evolving business needs will ensure its long-term relevance. Emerging technologies such as artificial intelligence, machine learning, and advanced analytics can further extend the UNS’s role in digital transformation. Aligning UNS capabilities with strategic goals, and making periodic updates to its components, will empower manufacturers to continuously achieve higher levels of productivity, efficiency, and insight.
Through strategic planning and adaptive practices, manufacturers can leverage the UNS not just as a tool but as a lasting framework that evolves in tandem with industry innovations and organizational growth.
Conclusion
Key Takeaways
The Unified Namespace (UNS) represents a fundamental shift in manufacturing data management, providing a single source of truth and a robust, scalable solution for digital transformation. With its event-driven structure, adherence to industry standards like ISA-95, and MQTT/Sparkplug protocol foundation, UNS simplifies data integration and ensures that all organizational data is readily available and contextualized. By breaking down data silos and supporting real-time decision-making, UNS enables manufacturers to unlock new efficiencies, improve collaboration, and create a truly data-driven enterprise.
Final Thoughts on UNS as a Strategic Asset
For manufacturers striving toward operational excellence, scalability, and resilience, UNS offers an invaluable framework. As both a current and future-ready architecture, UNS supports the addition of new devices, systems, and protocols, allowing manufacturers to continuously evolve their operations without costly rework. By standardizing and democratizing data access, UNS acts as a strategic asset that powers continuous improvement and aligns the entire organization toward digital transformation goals. With careful planning and a commitment to best practices, UNS can help manufacturing organizations stay competitive and agile in an ever-evolving landscape.
Call to Action
Considering a Unified Namespace can be transformative for some manufacturing operations, but it’s not a one-size-fits-all solution. The value of UNS depends on the unique demands of your facility and its readiness for seamless data integration. For decision-makers looking to improve efficiency, data accessibility, and scalability, engaging a skilled professional for an assessment is the next step. With over a decade of experience in manufacturing data architecture and digital transformation, I can help you evaluate whether a UNS is the right approach for your operations and guide you through implementing a tailored solution. Reach out to discuss how UNS—or an alternative approach—might best support your digital transformation goals.