Introduction: The Critical Role of a Manufacturing Plant Audit in Digital Transformation
In the world of manufacturing, where complexity and precision are paramount, the path to improvement often begins with an honest, thorough assessment of current practices. “Prescription without diagnosis is malpractice,” a phrase often attributed to the medical field, holds equally true in manufacturing. Just as a doctor wouldn’t prescribe treatment without understanding a patient’s specific needs and conditions, manufacturing leaders shouldn’t rush into digital transformation without a clear, data-driven view of their facility’s unique challenges and opportunities.
A manufacturing plant audit serves as this essential diagnostic step. It’s a comprehensive evaluation that goes beyond surface-level observations, examining the intricate details of technology, processes, equipment efficiency, workforce skills, safety practices, and compliance. Through this audit, plant managers and executives gain an accurate picture of their facility’s current state, allowing them to make informed, targeted decisions on where and how to implement digital solutions that deliver real, measurable value.
In this guide, we’ll walk through the stages of a manufacturing plant audit—from pre-audit preparation to on-site assessment and post-audit reporting. With the right methodology and focus, an audit can reveal hidden opportunities for digital transformation, helping companies avoid costly mistakes and drive sustained improvements across their operations.
Pre-Visit Preparation: Setting the Foundation for a Successful Audit
We begin a well-prepared audit long before setting foot on the manufacturing floor. Our pre-visit phase is designed to gather essential context, align expectations with your team, and build a foundational understanding of your facility’s processes and technologies. This groundwork ensures that our on-site visit will be focused, efficient, and impactful. Here’s what we’ll be doing during this pre-visit preparation phase:
1. Gathering Preliminary Materials and Documentation
- Requesting Relevant Documentation: We start by gathering available materials from your team, which provide us with a snapshot of current operations and any key areas needing attention. We’ll request documents such as:
- Process Flowcharts and Standard Operating Procedures (SOPs): These documents help us understand how core processes operate and highlight critical steps or equipment used.
- Equipment Inventory and Maintenance Logs: Reviewing your equipment and maintenance history is essential for assessing asset conditions and identifying potential obsolescence risks.
- Current Technology Architecture: We’ll ask for details on any existing digital systems, data collection methods, and integration points between technologies. This information allows us to assess the level of digital maturity and spot any data flow gaps.
- Performance Metrics: Historical data on KPIs, production efficiency, downtime, and quality measures will give us an initial sense of well-performing areas and those that could benefit from improvement.
2. Conducting a Kick-Off Conversation
- Clarifying Objectives: We will hold a kick-off conversation with your key stakeholders, such as plant managers, process engineers, and IT/OT leaders. This session is crucial for clarifying the audit’s objectives, defining success criteria, and setting clear expectations for everyone involved.
- Discussing Challenges and Priorities: We invite your team members to share their main pain points, priorities, and specific goals for the audit. This helps us tailor our focus during the on-site visit to ensure our findings align with your concerns.
- Setting a Schedule and Agenda: To facilitate a smooth process, we’ll outline the audit’s timeline, planned interactions with staff, and specific areas we’ll need access to during the visit. This coordination helps minimize disruptions to your regular operations and ensures that everyone is prepared for our arrival.
3. Understanding Processes and Technologies in Use
- Reviewing Process Maps and System Overviews: We’ll study your facility’s process flow maps and technology architecture to gain familiarity with the production environment and key technologies in use. Identifying how processes and systems interact is essential to spotting areas for potential improvement.
- Noting Data Collection Methods and Integration Points: We’ll assess how data is gathered and identify any existing integration challenges, helping us uncover digital transformation opportunities. Observing gaps in data flow or connectivity limitations is vital to enhancing operational visibility.
- Identifying Stakeholders for On-Site Conversations: Lastly, we’ll establish a list of individuals to speak with during the on-site audit, such as operators, supervisors, and maintenance staff. Their insights are invaluable in understanding on-the-ground processes and identifying potential improvement areas.
By thoroughly gathering information, building rapport with your team, and developing a detailed understanding of your facility’s technology and processes, we ensure that we are well-prepared for an efficient and effective on-site audit. This pre-visit preparation is foundational to ensuring that our recommendations will be closely aligned with your facility’s needs and ready to drive meaningful, impactful change.
On-Site Visit: In-Depth Assessment and Engagement with Key Stakeholders
During our on-site visit, we conduct an in-depth assessment of how your plant operates, uncovering challenges and identifying where digital transformation can have the most significant impact. Our time on-site includes discussions with key stakeholders and a comprehensive audit of technologies and integrations. This hands-on evaluation is the core of our audit and provides the foundation for an actionable, tailored report. Here’s what we will be doing during the on-site visit:
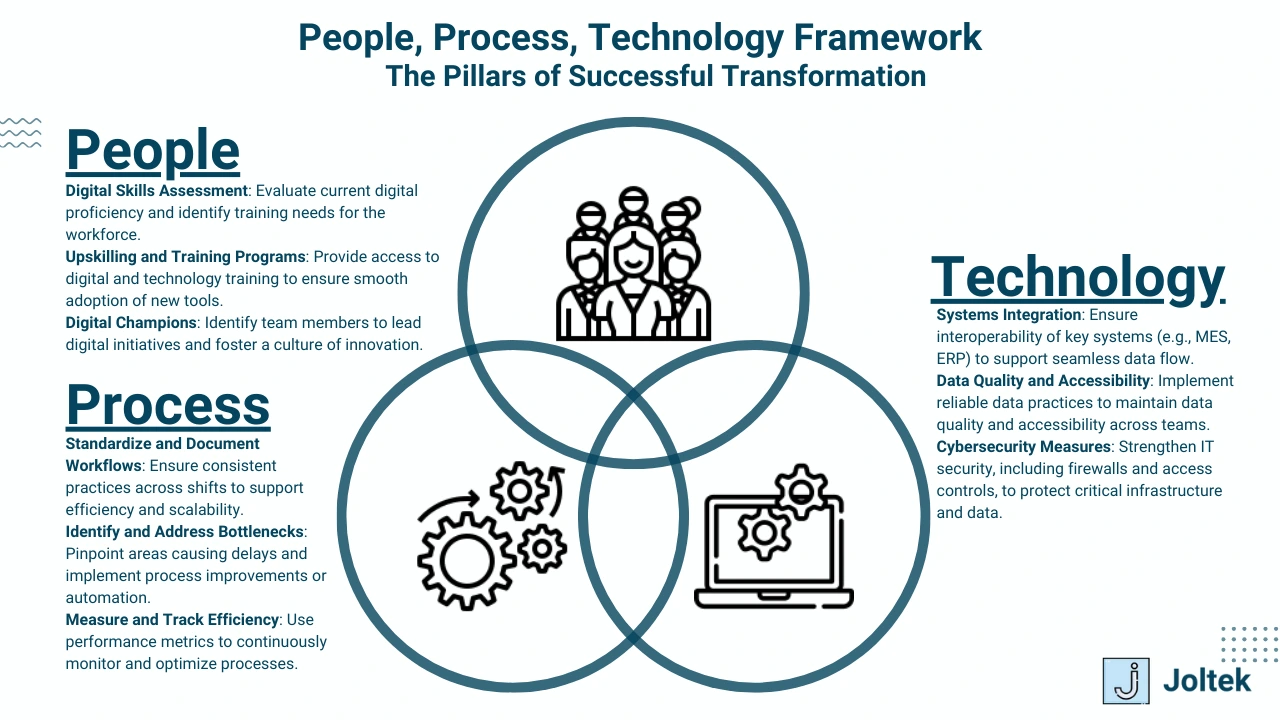
1. Engaging in Stakeholder Conversations to Understand Priorities, Deficiencies, and Operations
- Plant Manager: We start with an overview conversation with the plant manager, who provides a high-level perspective on strategic goals, current challenges, and operational priorities. Understanding the plant manager’s vision helps us align our audit with the facility’s long-term objectives.
- Engineering Manager: We will discuss ongoing and planned projects with the engineering manager, including any modifications, upgrades, or equipment needs. This conversation gives us insights into process improvements, resource allocation, and skill gaps that could impact future digital initiatives.
- Maintenance Manager: Maintenance teams are a critical source of information on equipment reliability, lifecycle stages, and common issues. We’ll discuss their preventive and predictive maintenance practices and identify any gaps in technology or skills that could lead to downtime or inefficiencies.
- Production Manager: We will talk with the production manager to review process flow, capacity, bottlenecks, and performance metrics. This discussion helps us uncover limitations in current workflows and identify opportunities where automation, data integration, or process adjustments could yield efficiency gains.
- Quality Manager: The quality manager’s insights are essential for understanding product consistency, standards compliance, and quality control effectiveness. We’ll examine how quality metrics are tracked and any traceability issues that could benefit from digital solutions.
- Health, Safety, and Environmental (HS&E) Manager: We will engage with the HS&E manager to understand safety practices, incident history, and compliance requirements. This helps us identify potential risks that could be addressed through technology or process adjustments.
- IT Manager (or IT/OT Lead): A collaborative conversation with the IT or IT/OT lead is crucial for understanding existing IT architecture, cybersecurity practices, data management, and connectivity challenges. We will assess any limitations in network infrastructure or system integrations that could impact technological upgrades.
Additional Stakeholders: Depending on the facility, we may also speak with operators, supervisors, and other staff who work directly with equipment and systems. These individuals often provide practical insights into daily operations, highlighting issues or opportunities that may not be visible to upper management.
2. Conducting a Technology and Systems Audit to Evaluate Infrastructure and Integration
- Assessing Control Systems (PLC, HMIs, SCADA): We start by auditing core control systems, documenting the types of PLCs, HMIs, and SCADA systems in use. We assess their age, compatibility, and any integration challenges, identifying potential obsolescence, data silos, or bottlenecks impacting real-time decision-making.
- Manufacturing Execution System (MES): We evaluate the MES to understand how it supports scheduling, production tracking, and resource management. We also assess whether it’s integrated with other systems, such as ERP, and its adaptability for future enhancements or automation.
- Enterprise Resource Planning (ERP): We examine the ERP system’s connectivity with shop-floor systems to determine if data flows seamlessly between ERP and MES. Any gaps in ERP integration can restrict visibility and create manual workarounds that affect operational efficiency.
- Other Systems (e.g., Quality, Asset Management): We will take stock of additional systems used for quality management, asset tracking, and predictive maintenance, evaluating their integration with primary control systems and accessibility across platforms.
3. Assessing Data Architecture and Integration
- Data Collection and Flow: We map out the facility’s data architecture, documenting data origins, collection methods, and storage locations. We assess connectivity across various systems to identify any limitations in data access, visibility, or consistency.
- Identifying Data Silos: We look for data silos—systems that operate independently and don’t share information with other platforms. Data silos hinder effective decision-making and obscure a complete view of facility performance.
- Cybersecurity Practices: With increased connectivity, cybersecurity is paramount. We assess cybersecurity protocols, including firewalls, access controls, and redundancies, and identify any vulnerabilities that could pose risks during or after digital upgrades.
4. Making Physical and Operational Observations
- Process Flow and Layout: We observe the physical layout and flow of production processes, looking for inefficiencies like redundant steps, long transport times, or space constraints that affect productivity. These observations often reveal areas where digital solutions or physical reconfigurations can improve efficiency.
- Safety and Compliance Inspections: We review safety protocols, incident records, and industry standard compliance. We document potential risks and assess how technology could support safer operations and regulatory adherence.
- Workforce Interactions with Technology: We observe how employees interact with equipment and systems, noting any skill gaps, training needs, or user experience issues that could impact technology adoption. Understanding the workforce’s digital proficiency is essential for planning effective training programs to ensure successful transformation.
By engaging stakeholders, auditing technology, assessing data flows, and observing operational dynamics, we develop a comprehensive view of your facility’s strengths, weaknesses, and readiness for transformation. This on-site assessment enables us to deliver precise, relevant recommendations that align with both day-to-day operations and strategic goals, setting the stage for impactful digital transformation.
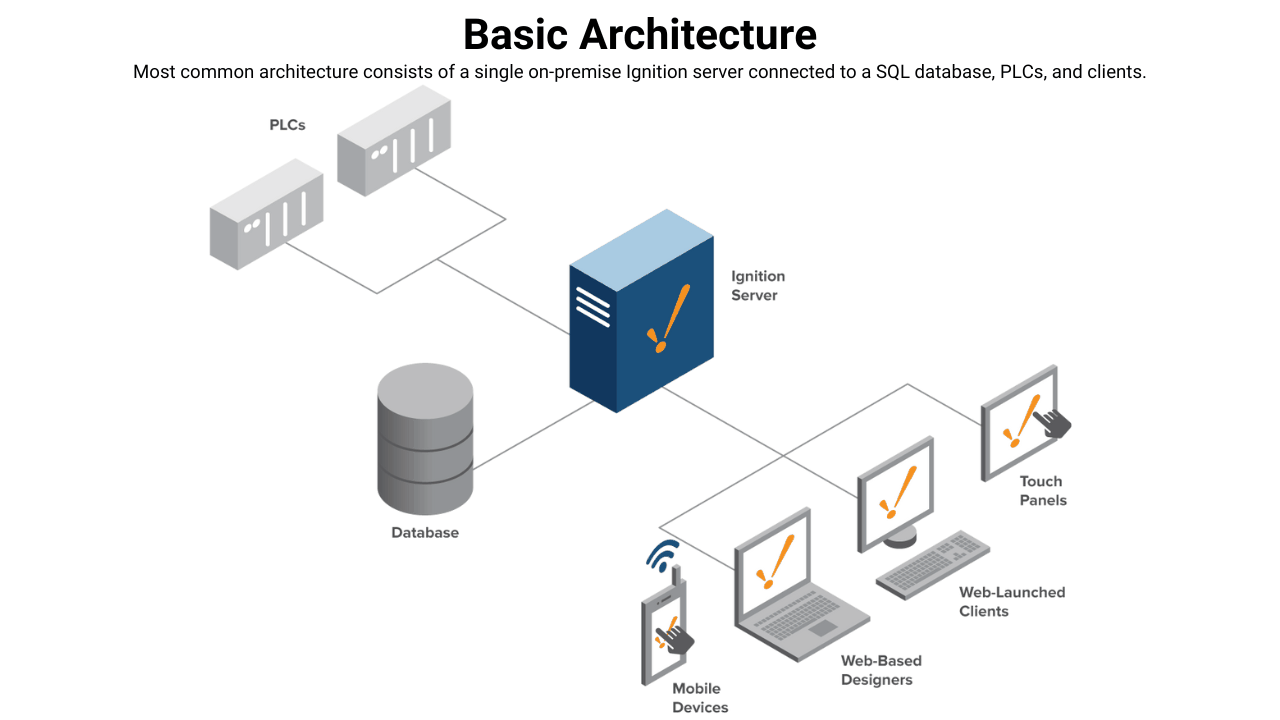
Post-Visit: Delivering a Strategic and Actionable Roadmap
After completing the on-site audit, our post-visit phase focuses on consolidating findings, sharing insights, and collaboratively defining the path forward. Here, we bring together observations, data analysis, and stakeholder insights to develop a clear, actionable plan tailored to your facility’s specific needs. Our post-visit process includes the following steps:
1. Developing the Assessment Document
- Current State Summary: We begin by providing a concise overview of your facility’s current state, covering each major area reviewed—technology, processes, data architecture, safety, compliance, and workforce readiness. This summary offers stakeholders a grounded view of the plant’s operational health.
- Detailed Findings and Observations: We break down the assessment into specific findings from each area:
- Technology Assessment: We describe the condition of control systems (e.g., PLCs, HMIs, SCADA), integrations, data flow, and any observed obsolescence. We highlight any gaps or risks in connectivity and data accessibility.
- Operational Efficiency and Process Flow: We summarize observations on process efficiencies, bottlenecks, or redundant steps, identifying areas where improvements can streamline workflows, reduce costs, or enhance production capacity.
- Safety and Compliance Observations: We provide an overview of safety practices and compliance status, noting potential risks or regulatory gaps.
- People and Skill Development Needs: We identify any skill gaps in the workforce’s interaction with technology and outline areas for training or upskilling to support future digital initiatives.
- Visuals and Data Points: To make complex data more accessible, we include visuals—such as charts, diagrams, and process maps—where possible. We also incorporate relevant KPIs, downtime statistics, and other quantitative metrics to support our qualitative observations.
2. Reviewing Findings with Key Stakeholders
- Scheduling a Review Meeting: We bring together the stakeholders involved in the audit—including the plant manager, engineering, production, maintenance, quality, HS&E, and IT leads—to review the assessment document. Our goal is to validate findings, address any questions, and ensure alignment on priorities.
- Discussing Specific Concerns and Feedback: We encourage stakeholders to share additional insights or clarifications. This open discussion may reveal further context or priorities that we can integrate into our recommendations, helping to create buy-in for the proposed path forward.
3. Defining the Path Forward
- Identifying Short-Term and Long-Term Goals: We outline a roadmap with both quick wins (short-term opportunities for immediate improvement) and long-term initiatives (strategic projects aligned with digital transformation goals). Prioritizing these actions helps your team see where to start while keeping the larger vision in focus.
- Defining Clear Next Steps: To ensure momentum post-audit, we provide specific actions and timelines, such as:
- Short-Term Actions: Examples include targeted maintenance improvements, system upgrades, or initial training sessions.
- Long-Term Initiatives: These may involve upgrading control systems, integrating MES and ERP, implementing new data collection methods, or developing a cybersecurity plan.
- Outlining Resource Requirements: For each recommendation, we highlight required resources, such as budget, personnel, or external expertise, allowing stakeholders to plan accordingly.
4. Presenting Tangible Opportunities for Improvement
- Technology Recommendations: We suggest specific technologies or upgrades that align with your facility’s needs, such as advanced analytics, predictive maintenance tools, or improved control system integration. Where possible, we include estimated ROI to demonstrate value.
- Process Optimization Opportunities: We recommend process adjustments or automation possibilities to reduce inefficiencies or eliminate bottlenecks, detailing potential benefits such as time savings, cost reduction, or increased capacity.
- Workforce Development Plan: We provide a roadmap for workforce upskilling, identifying essential training areas for successful digital adoption. This may include training on data management, equipment operation, or digital tools. (EX: 5 Whys Root Cause Analysis)
- Risk Mitigation and Compliance Enhancements: We address any safety or compliance gaps noted during the audit, offering targeted recommendations to improve risk management and ensure regulatory adherence.
By delivering a comprehensive and actionable assessment, this post-visit phase not only clarifies the current state but also empowers your team to take tangible steps toward a digitally transformed and more efficient facility. Our tailored recommendations equip your stakeholders with a roadmap for improvement that aligns with operational goals and prepares the facility for future growth.
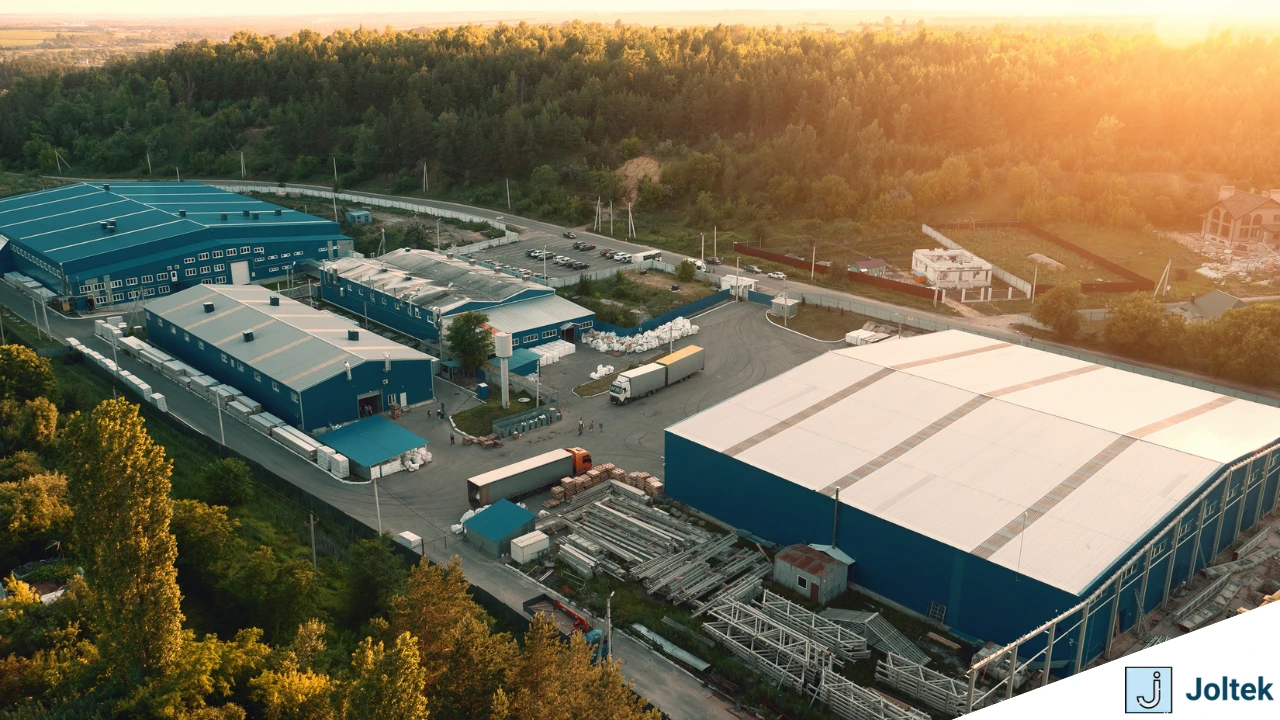
Conclusion: Empowering Transformation Through a Strategic Audit
Completing a manufacturing plant audit is not just the end of an assessment; it’s the beginning of a purposeful journey toward enhanced efficiency, resilience, and digital transformation. By thoroughly evaluating your facility’s current state, engaging with key stakeholders, and providing targeted recommendations, our audit delivers clear, data-driven insights and a practical roadmap for improvement.
Our detailed assessment document, coupled with a collaborative review, offers an honest reflection of your plant’s operational strengths and areas for growth. This empowers decision-makers to address immediate priorities while planning for sustainable, long-term advancements. Each recommendation—from technology upgrades and process optimizations to workforce development and safety improvements—is crafted in alignment with your facility’s unique context and strategic goals.
With this audit as a foundation, your team is empowered to make informed, impactful decisions that drive measurable improvements. By embracing these findings and implementing the recommended path forward, your facility not only maximizes its current capabilities but also builds the resilience and adaptability needed to excel in an increasingly digital manufacturing landscape.