Introduction
Definition and Scope of Manufacturing Consulting
Manufacturing consulting refers to the professional services offered to manufacturing organizations to optimize their operations, improve productivity, reduce costs, and achieve strategic objectives. These services encompass a broad spectrum, ranging from operational efficiency and process optimization to implementing cutting-edge technologies and fostering innovation. Manufacturing consultants bring specialized expertise, tools, and methodologies to address challenges and identify opportunities for growth and improvement.
Key aspects of manufacturing consulting include:
- Process Improvement: Streamlining workflows and eliminating inefficiencies.
- Technology Integration: Assisting with the adoption of new technologies, such as automation, additive manufacturing, and Industry 4.0 solutions.
- Cost Reduction: Identifying cost-saving opportunities while maintaining quality and performance.
- Strategic Planning: Aligning manufacturing capabilities with business objectives to achieve long-term goals.
- Workforce Development: Providing training and fostering a culture of continuous improvement.
By leveraging data-driven approaches and deep industry expertise, manufacturing consulting firms cater to a diverse range of industries, including automotive, aerospace, food and beverage, medical devices, and consumer goods.
Importance in the Modern Industrial Landscape
The role of manufacturing consulting has grown significantly in today’s rapidly evolving industrial environment. Several factors contribute to this heightened importance:
- Technological Disruption:
- With the advent of Industry 4.0, manufacturers face the challenge of integrating advanced technologies like IoT, AI, robotics, and data analytics into their operations. Manufacturing consultants guide companies through this digital transformation, ensuring smooth implementation and maximum ROI.
- Global Competition:
- Manufacturing companies operate in a fiercely competitive global market. Consulting services help organizations achieve operational excellence and differentiate themselves through quality, efficiency, and innovation.
- Economic Pressures:
- Rising costs of raw materials, energy, and labor demand a strategic approach to cost management. Consultants play a crucial role in identifying inefficiencies and implementing cost-saving measures without compromising on performance or quality.
- Sustainability Goals:
- Environmental regulations and consumer demand for sustainable practices have driven manufacturers to adopt greener processes. Consulting firms provide strategies to reduce waste, improve energy efficiency, and achieve sustainability certifications.
- Complex Supply Chains:
- Modern supply chains are intricate and often span multiple geographies. Manufacturing consultants assist in optimizing supply chain operations to reduce lead times, enhance reliability, and mitigate risks.
- Need for Resilience:
- The COVID-19 pandemic highlighted vulnerabilities in manufacturing systems. Consulting firms help companies build more resilient operations by adopting flexible manufacturing practices, diversifying suppliers, and leveraging digital tools for risk management.
In summary, manufacturing consulting is a cornerstone for organizations looking to thrive in a dynamic industrial landscape. By addressing current challenges and positioning companies for future growth, consultants act as enablers of innovation, efficiency, and strategic advantage.
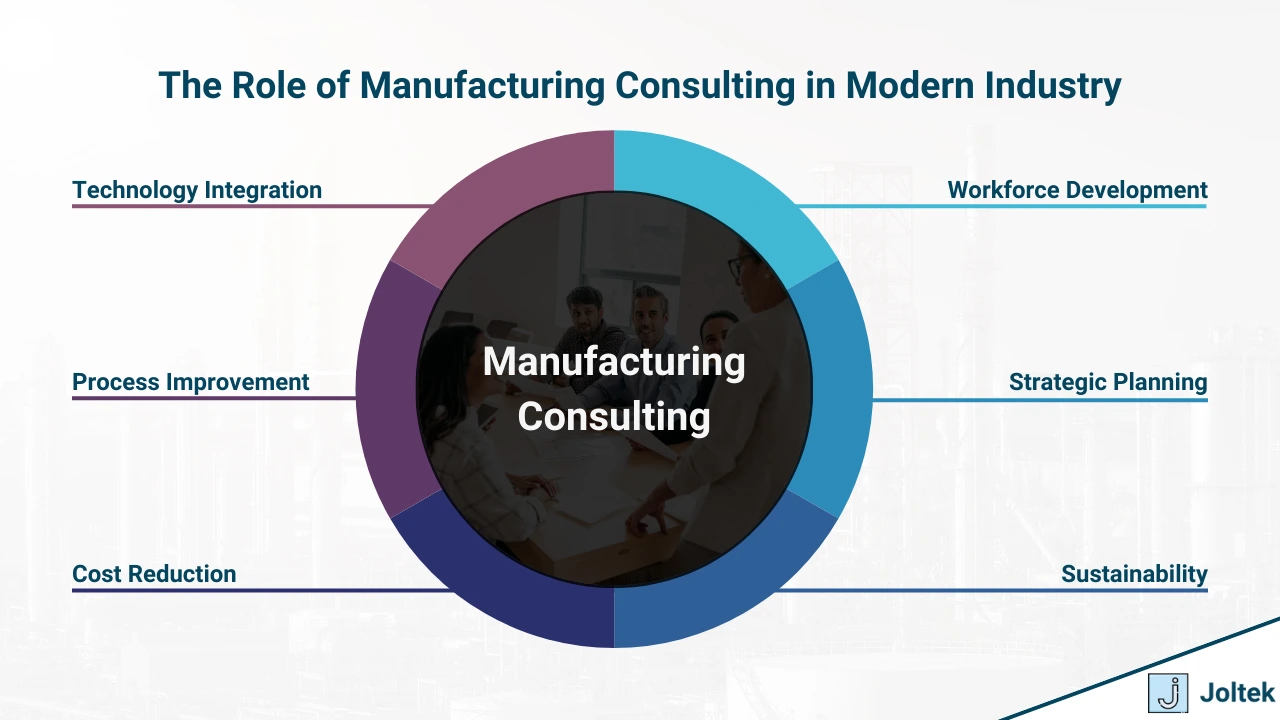
Types of Manufacturing Consulting Services
Overview of Various Consulting Services Available to Manufacturing Firms
Manufacturing consulting encompasses a wide array of specialized services designed to address the unique challenges faced by manufacturers and help them seize opportunities for growth and improvement. One of the most prominent areas is lean manufacturing consulting, which focuses on streamlining operations by eliminating waste and fostering a culture of continuous improvement. Lean consultants apply techniques such as Value Stream Mapping and 5S methodologies to enhance efficiency and productivity across the organization.
Another significant area is manufacturing operations consulting, which is centered around optimizing daily workflows, production scheduling, equipment utilization, and resource management. This type of consulting involves identifying bottlenecks in operations and implementing strategies such as predictive maintenance to minimize downtime and improve throughput.
The field of additive manufacturing consulting has grown in importance with the rise of 3D printing and advanced fabrication technologies. Consultants in this area guide companies through the adoption and scaling of additive technologies, focusing on material selection, equipment integration, and workforce training. Similarly, smart manufacturing consulting addresses the challenges of Industry 4.0 by helping manufacturers integrate advanced technologies like IoT, artificial intelligence, robotics, and cloud computing into their operations to create data-driven, connected systems.
Consulting services also extend to industrial product design and development, where experts assist manufacturers in designing and developing new products with manufacturability and cost-effectiveness in mind. These services often involve applying principles such as Design for Manufacturing (DFM) to ensure that products are not only innovative but also practical to produce. Additionally, manufacturing engineering consulting focuses on optimizing engineering processes, equipment layout, and compliance with industry standards, ensuring that manufacturing systems are both efficient and resilient.
Strategic guidance is another crucial aspect, provided through manufacturing strategy consulting. Consultants help organizations align their manufacturing operations with broader business objectives, whether through capacity planning, market analysis, or investment decision-making. Supply chain optimization is often part of this, with consultants working to improve procurement, inventory management, and logistics to enhance overall efficiency.
Lastly, sustainability and workforce development consulting play essential roles. Sustainability consultants guide manufacturers in adopting environmentally friendly practices, improving energy efficiency, and ensuring compliance with regulations. Workforce development consultants, on the other hand, design and implement training programs that enhance employee skills and foster a culture of continuous improvement.
Benefits of Engaging with Manufacturing Consulting Firms
The advantages of engaging manufacturing consulting firms are both strategic and operational. One of the most significant benefits is access to industry-specific expertise and best practices. Consultants bring a wealth of experience, enabling manufacturers to solve complex problems more effectively and implement proven strategies tailored to their needs. This external perspective also ensures objectivity, allowing consultants to identify challenges and opportunities that internal teams might overlook.
Manufacturing consultants often provide tailored solutions that address the unique goals and constraints of the organization. This customization ensures that recommendations are practical and aligned with the company’s overall vision. Additionally, consultants help enhance operational efficiency by optimizing processes, improving equipment utilization, and managing resources more effectively. This often results in increased productivity, shorter lead times, and significant cost savings.
Another key advantage is guidance in adopting and integrating new technologies. As manufacturers face the challenges of digital transformation, consultants play a vital role in ensuring smooth implementation of advanced tools and systems, such as IoT, AI, and robotics. This not only reduces risks but also maximizes the return on investment from these technologies.
Beyond operational improvements, consultants provide strategic value by helping manufacturers scale and grow. Whether it involves designing scalable systems, planning for market expansion, or developing long-term strategies, consulting services ensure that manufacturers are prepared for future opportunities. Furthermore, consulting firms help companies maintain compliance with industry standards and environmental regulations, reducing risks associated with non-compliance and potential operational disruptions.
Lastly, consulting firms contribute to workforce empowerment by delivering training programs that upskill employees and foster a culture of innovation and safety. Empowered employees are more engaged, productive, and equipped to drive continuous improvement initiatives.
In summary, manufacturing consulting firms offer a comprehensive suite of services that address both immediate operational challenges and long-term strategic goals. Their expertise, objectivity, and tailored solutions enable manufacturers to thrive in a competitive and ever-changing industrial landscape.
Lean Manufacturing Consulting
Principles and Methodologies of Lean Manufacturing
Lean manufacturing is a philosophy that focuses on creating maximum value for customers while minimizing waste and inefficiencies. Rooted in the Toyota Production System, lean manufacturing emphasizes continuous improvement and operational excellence. The key principles of lean include value identification, value stream mapping, creating flow, establishing pull, and striving for perfection. These principles ensure that every activity within the manufacturing process adds value to the customer, while non-value-adding activities—classified as waste—are eliminated.
Several methodologies are used to implement lean principles. Value Stream Mapping (VSM) is a common tool for visualizing and analyzing the flow of materials and information through a production process. The 5S system—Sort, Set in Order, Shine, Standardize, Sustain—provides a framework for workplace organization and efficiency. Kaizen, another fundamental lean practice, encourages continuous incremental improvements through team collaboration and employee engagement. Other methodologies, such as Just-In-Time (JIT), focus on reducing inventory levels and aligning production with customer demand.
Role of Consultants in Implementing Lean Strategies
Lean manufacturing consultants play a critical role in helping organizations adopt and sustain lean practices. Their expertise allows them to assess current operations, identify inefficiencies, and design customized solutions to meet the company’s specific goals. One of their first steps is often conducting a comprehensive audit of the manufacturing process, using tools like value stream mapping to pinpoint areas of waste and opportunities for improvement.
Consultants also guide the cultural transformation necessary for lean implementation. Lean practices require a shift in mindset across all levels of the organization, from frontline workers to senior management. Consultants help foster this cultural shift by providing training, facilitating workshops, and embedding a commitment to continuous improvement throughout the company.
Moreover, consultants assist in deploying lean tools and methodologies tailored to the company’s needs. Whether implementing 5S practices, organizing Kaizen events, or setting up Just-In-Time systems, their role is to ensure these tools are applied effectively and integrated seamlessly into daily operations. They also establish metrics and key performance indicators (KPIs) to track progress and measure the impact of lean initiatives over time.
Two Characteristics of Lean Manufacturing
1. Continuous Improvement (Kaizen): At the heart of lean manufacturing is the principle of continuous improvement, known as Kaizen. This approach involves making small, incremental changes to processes to enhance efficiency, quality, and value over time. Kaizen relies heavily on employee participation, encouraging workers at all levels to identify inefficiencies and propose solutions. This collaborative effort not only drives improvements but also fosters a culture of ownership and accountability within the organization.
Kaizen events, or focused improvement workshops, are often facilitated by lean consultants to address specific challenges or opportunities. These events bring cross-functional teams together to analyze a process, brainstorm solutions, and implement changes quickly. Over time, the cumulative impact of these small improvements can lead to significant advancements in productivity and customer satisfaction.
2. Elimination of Waste (Muda): Lean manufacturing categorizes waste, or Muda, into seven types: overproduction, waiting, transportation, overprocessing, excess inventory, unnecessary motion, and defects. Each type of waste represents activities that do not add value from the customer’s perspective and therefore should be minimized or eliminated.
The elimination of waste is achieved through meticulous analysis of processes and the application of lean tools. For instance, Just-In-Time production reduces overproduction and excess inventory, while VSM identifies bottlenecks and inefficiencies in the flow of materials and information. By systematically addressing waste, lean manufacturing ensures that resources are utilized efficiently and costs are minimized without compromising quality.
Lean manufacturing consulting is essential for organizations aiming to adopt these principles effectively. Consultants not only provide the expertise and tools needed to implement lean strategies but also help instill the cultural and operational changes necessary for long-term success. With a focus on continuous improvement and waste elimination, lean manufacturing remains a powerful approach for achieving operational excellence and delivering value to customers.
Manufacturing Operations Consulting
Enhancing Operational Efficiency and Productivity
Manufacturing operations consulting focuses on improving the efficiency and productivity of day-to-day operations within a manufacturing facility. These consultants analyze processes, identify bottlenecks, and recommend tailored solutions to optimize resource utilization and output. The goal is to create a seamless flow of operations, where materials, labor, and equipment work in harmony to produce high-quality products with minimal waste.
Operational efficiency begins with understanding the current state of the facility’s operations. Consultants conduct comprehensive assessments, often using tools like workflow analysis, production line simulations, and key performance indicator (KPI) tracking. By measuring metrics such as cycle time, downtime, overall equipment effectiveness (OEE), and throughput, they pinpoint areas that require intervention.
Another key aspect of operational efficiency is workforce engagement. Productivity improvements often depend on the skills, motivation, and alignment of employees with organizational goals. Consultants help design training programs, establish clear communication channels, and implement best practices to ensure that employees are empowered to contribute to operational improvements.
The implementation of automation and digital technologies also plays a significant role. Consultants often assist in integrating systems such as Manufacturing Execution Systems (MES), predictive maintenance platforms, and IoT-enabled devices to enhance decision-making, monitor performance in real time, and reduce unplanned downtime.
Strategies for Process Optimization and Cost Reduction
Process optimization is at the core of manufacturing operations consulting. Consultants use data-driven approaches to streamline production workflows and eliminate inefficiencies. One commonly applied strategy is process mapping, which visualizes every step in a manufacturing operation to identify redundancies, delays, or misalignments. Consultants then recommend process redesigns, implement lean principles, or introduce advanced tools to address these inefficiencies.
Cost reduction strategies are another critical focus. Consultants analyze operational expenses, including labor, materials, energy, and maintenance, to identify opportunities for savings. For instance, they may recommend switching to more cost-effective raw materials, renegotiating supplier contracts, or optimizing energy consumption through smart energy management systems. The adoption of lean methodologies, such as Just-In-Time (JIT) inventory systems, also helps reduce carrying costs and minimize excess inventory.
Technology integration is a powerful lever for both optimization and cost reduction. For example, implementing predictive maintenance tools can reduce equipment downtime and extend the lifespan of machinery, cutting repair and replacement costs. Similarly, the use of robotics and automation in repetitive tasks reduces labor expenses and improves production speed and consistency.
Finally, consultants often focus on improving supply chain efficiency as a key driver of operational excellence. Strategies such as consolidating suppliers, implementing digital supply chain management tools, and optimizing logistics can significantly reduce costs while ensuring timely delivery of materials and finished products.
Manufacturing operations consulting delivers measurable improvements in efficiency, productivity, and cost management. By employing advanced methodologies, leveraging technology, and fostering employee engagement, consultants help organizations optimize their processes and remain competitive in a fast-paced industrial landscape. The result is not just immediate cost savings but also a robust and agile manufacturing system ready to adapt to future challenges and opportunities.
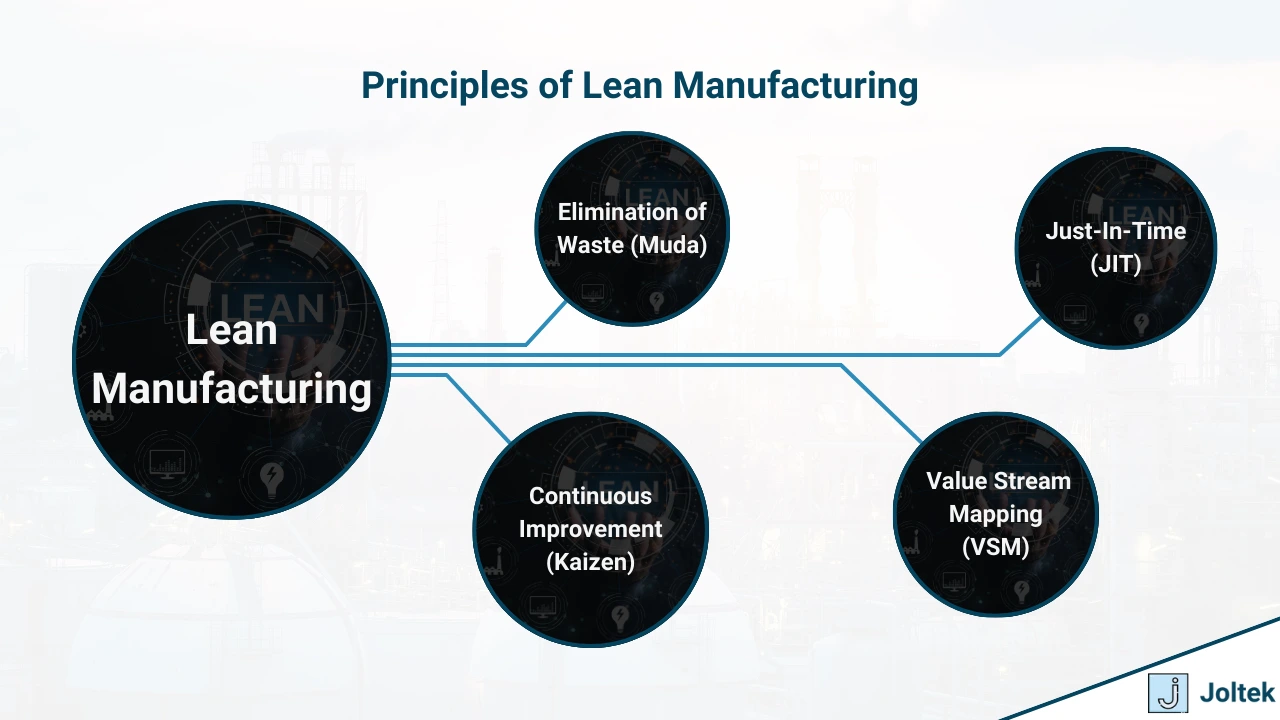
Additive Manufacturing Consulting
Introduction to Additive Manufacturing (3D Printing)
Additive manufacturing, commonly known as 3D printing, is a transformative technology that builds objects layer by layer from digital models. Unlike traditional subtractive manufacturing methods, which involve cutting or machining material away, additive manufacturing fabricates components directly from raw materials such as polymers, metals, or composites. This approach offers unparalleled flexibility in design and has applications across industries including aerospace, automotive, healthcare, consumer goods, and industrial equipment.
One of the primary advantages of additive manufacturing is its ability to create complex geometries that would be difficult or impossible to achieve using traditional methods. It allows for rapid prototyping, where engineers can quickly iterate on designs, test functionality, and bring products to market faster. Moreover, it enables on-demand manufacturing, reducing the need for large inventories and enabling customization at scale.
The technology’s benefits extend beyond design and production flexibility. Additive manufacturing can reduce material waste, improve energy efficiency, and shorten supply chains by producing components closer to their point of use. These capabilities make it a cornerstone of advanced manufacturing strategies, particularly in the context of Industry 4.0.
Consulting Services for Adopting and Integrating Additive Technologies
The adoption of additive manufacturing involves significant changes to traditional workflows, supply chains, and production methods. Additive manufacturing consultants play a vital role in guiding organizations through this transformation, ensuring the technology is implemented effectively and delivers maximum value.
Consultants begin by assessing the organization’s readiness for additive manufacturing. This includes evaluating existing manufacturing processes, identifying parts or products suitable for additive production, and analyzing cost-benefit scenarios. They help organizations understand where additive technologies can provide the greatest impact, such as reducing lead times, enhancing product performance, or enabling design innovations.
Integration of additive manufacturing into existing operations requires careful planning and expertise. Consultants assist in selecting the right technology based on the organization’s specific needs, whether it’s stereolithography (SLA), selective laser sintering (SLS), or direct metal laser sintering (DMLS). They also advise on material selection, ensuring compatibility with production requirements and quality standards.
Beyond technology selection, consultants focus on process reengineering to integrate additive manufacturing seamlessly into the production workflow. This might involve redesigning parts to take full advantage of additive capabilities, such as lightweight structures or internal channels for cooling. Consultants also provide expertise in digital design tools, such as computer-aided design (CAD) software and simulation platforms, which are critical for leveraging the potential of 3D printing.
Training and workforce development are another key aspect of consulting services. Additive manufacturing often requires new skills, including proficiency in design for additive manufacturing (DfAM), machine operation, and quality assurance. Consultants provide training programs to upskill employees and build internal expertise.
Lastly, consultants address supply chain and production strategy adjustments needed to support additive manufacturing. They help organizations transition to more agile manufacturing models, such as distributed production, where components are printed on-demand at different locations. They also guide companies in managing intellectual property concerns, given the ease with which digital files can be shared.
Additive manufacturing consulting is essential for companies seeking to unlock the full potential of 3D printing. By providing strategic guidance, technical expertise, and process optimization, consultants enable organizations to overcome adoption challenges and harness the transformative power of additive technologies. Whether for rapid prototyping, small-batch production, or full-scale manufacturing, additive manufacturing represents a game-changing approach to innovation and efficiency in the modern industrial landscape.
Smart Manufacturing Consulting
Incorporating Industry 4.0 Technologies
Smart manufacturing, a cornerstone of Industry 4.0, leverages advanced technologies to create highly automated, interconnected, and data-driven production environments. This approach transforms traditional manufacturing operations by integrating technologies such as the Internet of Things (IoT), artificial intelligence (AI), machine learning, robotics, cloud computing, and big data analytics. These tools work together to enhance visibility, improve decision-making, and enable predictive and adaptive capabilities across the manufacturing value chain.
IoT devices play a crucial role by collecting real-time data from equipment, processes, and products. This data is then analyzed using AI and machine learning to detect patterns, predict failures, and optimize performance. Robotics and automation further enhance efficiency by performing repetitive tasks with speed, precision, and consistency, freeing human workers to focus on higher-value activities. Cloud computing and edge computing ensure that this data is accessible and actionable, whether processed on-site for real-time responses or in the cloud for large-scale analytics.
Smart manufacturing also facilitates a shift from reactive to proactive maintenance strategies. For example, predictive maintenance uses sensors and AI to monitor equipment health and predict when maintenance is required, reducing unplanned downtime and extending the lifespan of machinery. Additionally, technologies like digital twins—virtual replicas of physical systems—enable manufacturers to simulate and optimize processes before implementing them in the real world.
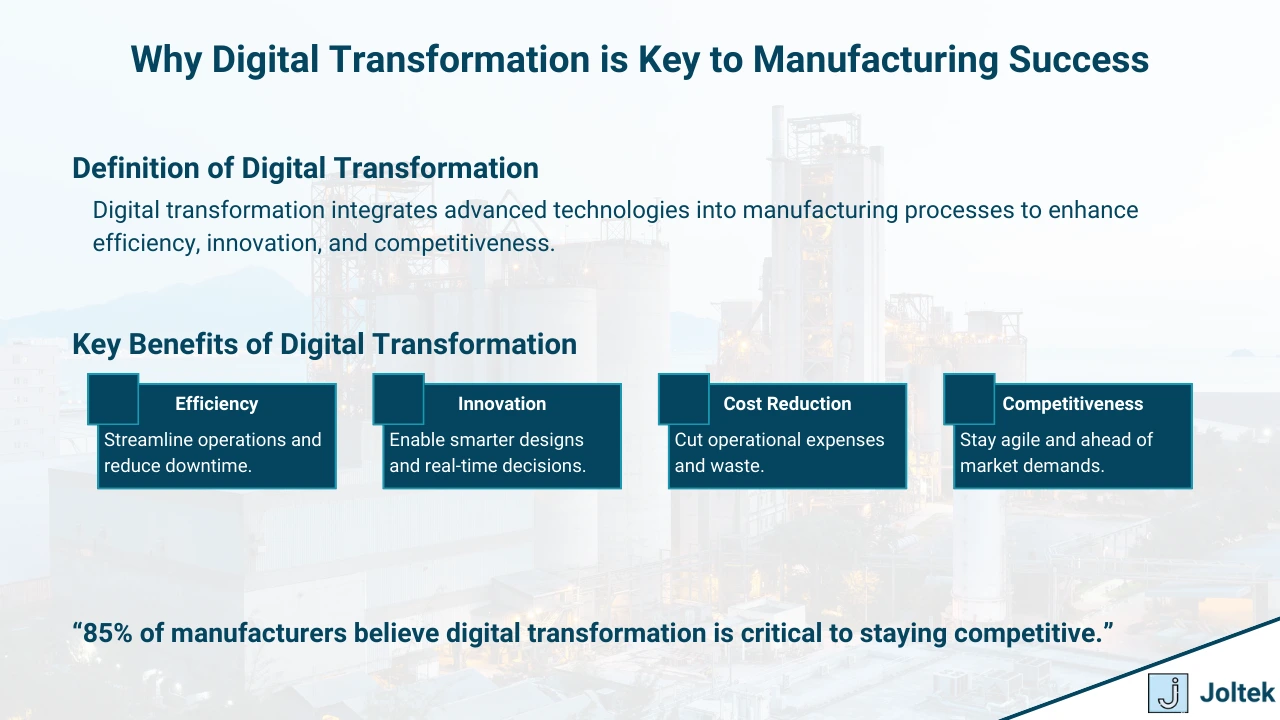
Consultants' Role in Digital Transformation and Automation
Consultants play a pivotal role in guiding manufacturing organizations through the complexities of digital transformation and automation. Their expertise helps companies navigate the challenges of adopting Industry 4.0 technologies while ensuring alignment with business objectives.
The first step in a consultant's approach is to assess the current state of the manufacturing operation. This involves conducting a digital maturity audit to evaluate existing processes, technology infrastructure, and workforce capabilities. By identifying gaps and opportunities, consultants create a roadmap for the digital transformation journey.
A key aspect of a consultant’s role is technology selection and integration. With the myriad of Industry 4.0 solutions available, choosing the right technologies can be daunting. Consultants help organizations prioritize investments based on their specific needs, such as IoT sensors for real-time monitoring, AI algorithms for quality control, or robotic systems for assembly lines. They ensure these technologies are integrated seamlessly into existing systems, enabling interoperability and scalability.
Process optimization is another area where consultants provide value. By analyzing production workflows, they identify opportunities to streamline operations through automation and data-driven decision-making. For instance, consultants might recommend deploying autonomous robots for material handling or implementing AI-powered scheduling systems to optimize production plans.
Workforce transformation is also a critical focus. Digital transformation often requires new skills and a cultural shift toward embracing innovation. Consultants design training programs to upskill employees, fostering a workforce that can effectively use advanced technologies and adapt to new ways of working. This includes training in areas such as data analysis, IoT device management, and programming for automated systems.
Finally, consultants help manufacturers measure and track the success of their digital transformation efforts. By defining key performance indicators (KPIs) such as overall equipment effectiveness (OEE), energy efficiency, and downtime reduction, they enable organizations to quantify the impact of smart manufacturing initiatives. They also establish continuous improvement practices to ensure that the benefits of digital transformation are sustained over time.
Smart manufacturing consulting is essential for companies aiming to stay competitive in an increasingly digital world. By leveraging Industry 4.0 technologies and guiding organizations through the complexities of transformation, consultants enable manufacturers to achieve greater efficiency, agility, and innovation. The result is not just a modernized production system but a strategic advantage in the fast-evolving industrial landscape.
Industrial Manufacturing Product Design and Development Consulting
Assistance in Product Design and Development Processes
Industrial manufacturing product design and development consulting provides expertise to streamline and enhance the creation of new products, from concept to production. These consultants guide companies through the complex stages of product development, offering technical knowledge, tools, and strategies to bring innovative ideas to market efficiently.
The process begins with ideation and concept development, where consultants work closely with design teams to transform ideas into viable prototypes. This involves defining product requirements, conducting feasibility studies, and leveraging advanced tools such as computer-aided design (CAD) software. Consultants often utilize techniques like design thinking to ensure the end product aligns with customer needs and market demands.
During the prototyping phase, consultants assist in selecting appropriate materials and production methods to ensure functional, durable, and cost-effective designs. They also support iterative testing, refining designs based on feedback and performance analysis. This iterative process reduces the risk of costly errors during full-scale production.
Consultants also bring value in navigating regulatory compliance and certification requirements. For industries like medical devices, aerospace, or automotive, strict standards govern product design and safety. By ensuring adherence to these requirements early in the process, consultants help avoid delays and ensure a smoother path to market entry.
Ensuring Manufacturability and Cost-Effectiveness
One of the critical aspects of product design consulting is ensuring manufacturability—designing products that can be efficiently and economically produced at scale without compromising quality or functionality. This principle, known as Design for Manufacturability (DFM), emphasizes simplicity, standardization, and compatibility with available manufacturing technologies.
Consultants analyze designs to identify potential production challenges, such as complex geometries, material constraints, or assembly difficulties. They then recommend adjustments to make the manufacturing process smoother and more cost-effective. For example, they might suggest using fewer components, incorporating modular designs, or selecting materials that are easier to source and process.
Cost-effectiveness is another focus area, where consultants help optimize the balance between performance and expenses. They conduct cost analysis to identify opportunities for savings in material selection, production methods, and supply chain management. For instance, consultants may recommend alternative materials that meet performance requirements at a lower cost or suggest processes like additive manufacturing for prototyping and small-batch production to save on tooling expenses.
Additionally, consultants assist in selecting the most suitable production technologies for a given product. For example, they might recommend injection molding for high-volume plastic parts or precision machining for metal components with tight tolerances. By matching production methods to the design’s requirements, consultants help minimize waste, reduce lead times, and improve overall efficiency.
Another area of emphasis is sustainability. Increasingly, manufacturers are looking to design products that minimize environmental impact. Consultants provide strategies for using recyclable materials, reducing energy consumption during production, and designing for product life cycle sustainability, which appeals to both regulators and environmentally conscious customers.
By offering technical expertise and strategic guidance, industrial manufacturing product design and development consultants enable organizations to create innovative, high-quality products that are both manufacturable and cost-effective. Their role is crucial in ensuring a seamless transition from design to production, reducing risks, optimizing costs, and accelerating time to market—all while maintaining the flexibility to adapt to changing market conditions and customer needs.
Manufacturing Engineering Consulting
Support in Engineering Processes and Systems
Manufacturing engineering consulting focuses on optimizing engineering processes and systems to enhance efficiency, productivity, and quality across manufacturing operations. Consultants work closely with engineering teams to assess the existing infrastructure, identify inefficiencies, and recommend improvements tailored to the organization's goals.
Consultants begin by evaluating the design, development, and production processes to ensure alignment with operational objectives. This often involves a comprehensive analysis of workflows, equipment performance, and resource allocation. They use tools such as process simulations, time-motion studies, and overall equipment effectiveness (OEE) evaluations to uncover areas where engineering systems can be streamlined.
A critical aspect of their support is addressing system-level challenges. For instance, consultants might assess how well different engineering systems—such as CAD tools, Manufacturing Execution Systems (MES), and Enterprise Resource Planning (ERP) systems—integrate and communicate. Ensuring seamless interoperability between these systems reduces delays, improves data accuracy, and supports more informed decision-making.
In addition to technical optimization, consultants also focus on workforce empowerment. By providing training and mentorship, they help engineers adopt new methodologies, tools, and technologies, ensuring the organization is equipped to sustain improvements over time.
Implementation of Best Practices and Innovative Solutions
A key role of manufacturing engineering consultants is to introduce and implement best practices tailored to the unique needs of the organization. These practices often stem from established frameworks such as Lean, Six Sigma, or Total Productive Maintenance (TPM), which are adapted to suit the specific challenges of the facility.
Consultants ensure that engineering designs and processes incorporate principles of Design for Manufacturability (DFM) and Design for Assembly (DFA). These approaches aim to simplify production, reduce costs, and improve product quality by considering manufacturing constraints during the design phase. For example, DFM might involve selecting materials that are easier to machine or designing components that require minimal assembly steps.
Innovation is another cornerstone of engineering consulting. With the rapid advancement of manufacturing technologies, consultants help organizations stay competitive by adopting cutting-edge solutions. This may include implementing advanced automation, robotics, or IoT-enabled sensors to monitor and control production systems. Consultants also guide the integration of predictive maintenance technologies, which use AI and machine learning to forecast equipment failures and reduce unplanned downtime.
Furthermore, sustainability is increasingly a priority in manufacturing engineering. Consultants develop strategies to reduce energy consumption, minimize waste, and incorporate eco-friendly materials and processes. For instance, they may recommend energy-efficient equipment, closed-loop systems, or alternative materials with a lower environmental impact.
Digital transformation is another area where consultants provide critical guidance. This involves integrating Industry 4.0 technologies, such as digital twins, cloud-based platforms, and big data analytics, to create a more responsive and data-driven manufacturing environment. By harnessing these technologies, manufacturers can improve precision, reduce lead times, and enhance scalability.
In essence, manufacturing engineering consultants serve as catalysts for improvement and innovation. By providing expertise in process optimization, best practices, and advanced technologies, they enable organizations to overcome challenges, achieve operational excellence, and maintain a competitive edge in an ever-evolving industrial landscape. Their work not only improves current operations but also sets the foundation for sustainable growth and innovation.
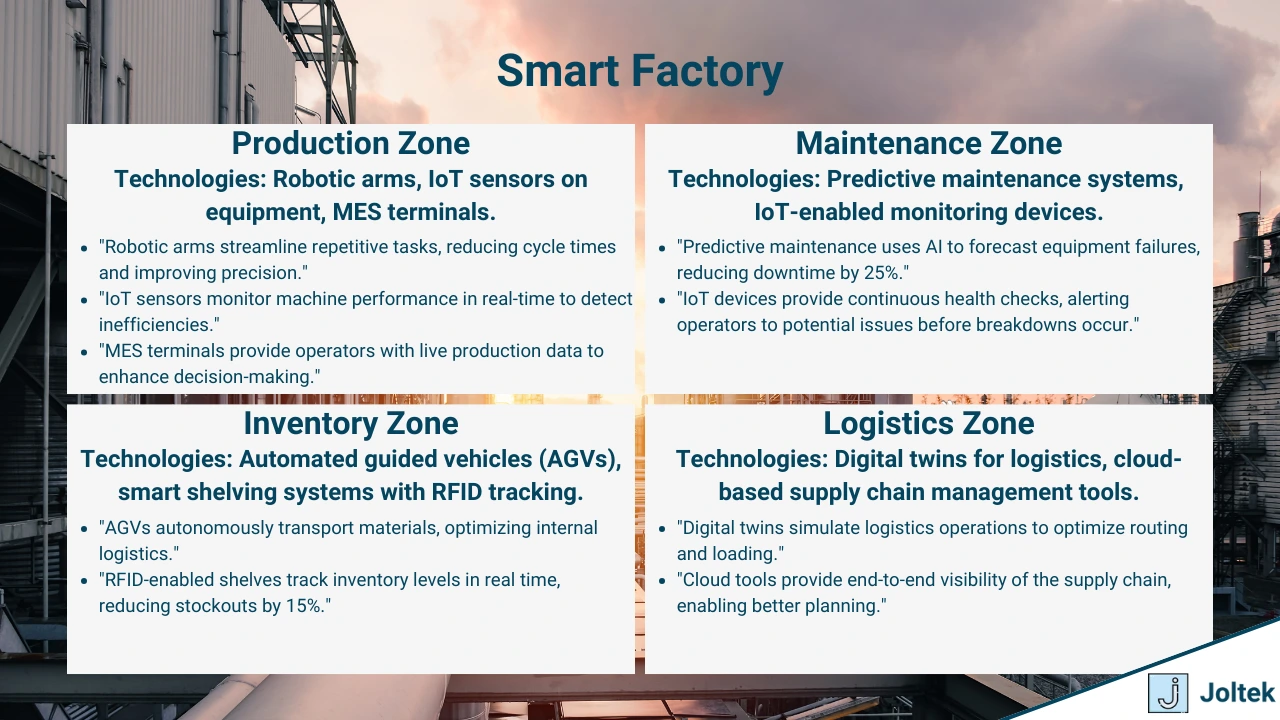
Manufacturing Strategy Consulting
Developing Long-Term Strategies for Competitive Advantage
Manufacturing strategy consulting is centered around helping organizations develop robust, long-term plans to achieve a sustainable competitive edge in the marketplace. These strategies are designed to enhance operational efficiency, adapt to changing market conditions, and position the company as a leader in its industry.
Consultants begin by conducting a comprehensive assessment of the organization's current state, evaluating factors such as production capacity, operational efficiency, market positioning, and supply chain performance. This assessment provides a clear picture of the company’s strengths, weaknesses, opportunities, and threats (SWOT analysis), forming the foundation for strategic planning.
A significant focus of manufacturing strategy consulting is identifying core competencies—areas where the organization excels or can develop a unique advantage. For example, this might involve leveraging advanced manufacturing technologies, achieving exceptional product quality, or offering unparalleled customization options. By building on these competencies, consultants help organizations differentiate themselves in the market.
In addition, consultants help manufacturers anticipate and prepare for future trends. This includes embracing innovations like Industry 4.0 technologies, adopting sustainable practices, and exploring new business models such as servitization (offering products as a service). Long-term strategies often incorporate flexibility to adapt to evolving customer demands, regulatory changes, and global economic shifts.
Aligning Manufacturing Capabilities with Business Goals
A key aspect of manufacturing strategy consulting is ensuring that manufacturing capabilities are fully aligned with broader business objectives. This alignment ensures that production operations actively support the company’s financial, operational, and customer-focused goals.
To achieve this, consultants work closely with leadership teams to understand the organization’s vision and priorities. For example, if a business aims to expand into new markets, consultants might focus on developing strategies for scaling production, increasing output, or enhancing supply chain resilience. Similarly, if cost reduction is a primary goal, consultants might prioritize lean manufacturing initiatives, process automation, and resource optimization.
Another critical area of alignment is capacity planning. Consultants assess whether the organization’s current infrastructure, workforce, and equipment are adequate to meet future demands. If gaps exist, they propose strategies for capacity expansion, such as investing in new facilities, upgrading existing equipment, or enhancing workforce skills through training programs.
Market responsiveness is another priority. Consultants help manufacturers build agile systems that can quickly adapt to changing market conditions, such as shifts in customer preferences, raw material availability, or competitor actions. This might involve adopting modular production lines, implementing digital supply chain tools, or utilizing data analytics to predict market trends.
Sustainability and regulatory compliance also play a vital role in aligning manufacturing capabilities with business goals. Consultants develop strategies to reduce environmental impact, ensure compliance with regulations, and meet stakeholder expectations for ethical and sustainable practices. This alignment not only mitigates risks but also enhances the company’s reputation and competitiveness.
Manufacturing strategy consulting bridges the gap between operational capabilities and strategic ambitions. By developing long-term plans that address both current challenges and future opportunities, consultants help manufacturers achieve lasting success. Their guidance ensures that manufacturing operations are not only efficient and resilient but also aligned with the organization’s vision, enabling sustainable growth in an increasingly complex industrial landscape.
Cost Reduction in Manufacturing
Consulting Approaches to Identify and Implement Cost-Saving Measures
Cost reduction in manufacturing is a critical goal for organizations aiming to improve profitability, competitiveness, and long-term sustainability. Manufacturing consultants employ a structured, data-driven approach to uncover inefficiencies, optimize processes, and implement practical solutions to lower costs while maintaining product quality and operational standards.
The first step in cost reduction consulting involves conducting a comprehensive cost analysis. Consultants examine key expense areas such as labor, materials, energy, maintenance, and logistics. By breaking down costs across the value chain, they identify inefficiencies and opportunities for savings. This analysis often includes benchmarking the organization’s performance against industry standards to highlight areas for improvement.
One common area of focus is process optimization. Consultants analyze production workflows to identify bottlenecks, redundancies, or underutilized resources. They may recommend redesigning processes, upgrading equipment, or adopting automation to enhance efficiency. For example, introducing predictive maintenance technologies can reduce unplanned downtime and extend equipment life, significantly lowering maintenance costs.
Another approach involves material cost management. Consultants work to reduce waste in material usage, negotiate better supplier contracts, and explore alternative materials that provide the same functionality at a lower cost. In some cases, they might recommend adopting technologies such as additive manufacturing for prototyping and small-batch production to reduce tooling expenses.
Supply chain optimization is another key strategy. Consultants assess procurement practices, inventory management, and logistics to streamline operations. By consolidating suppliers, optimizing transportation routes, and implementing digital supply chain tools, manufacturers can reduce costs while ensuring reliable material flow.
Workforce-related cost reduction strategies are also critical. Consultants often identify inefficiencies in workforce allocation or training gaps that impact productivity. By providing targeted training programs, optimizing shift patterns, or introducing incentive programs, they help maximize labor efficiency without compromising employee satisfaction.
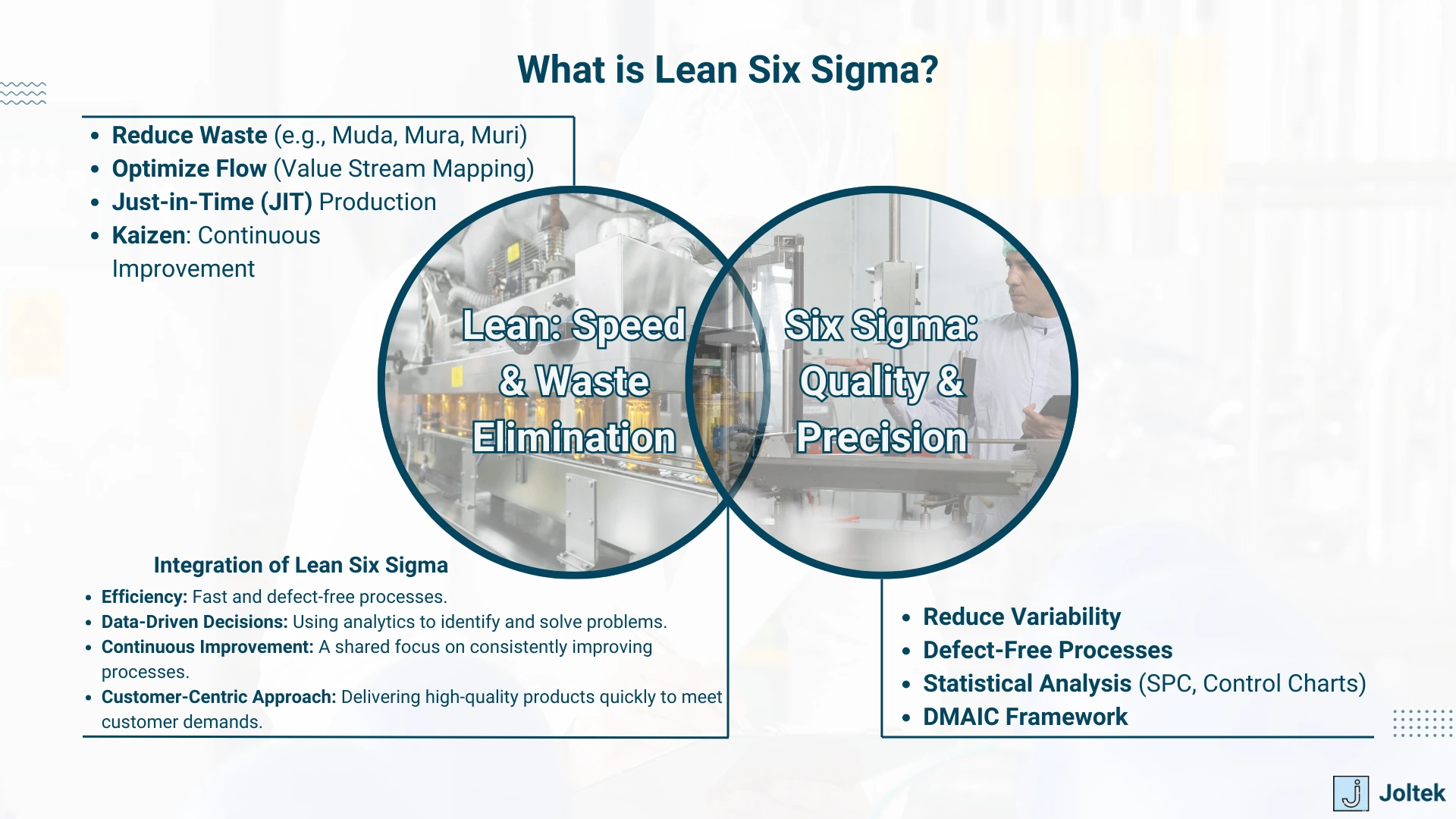
Lean Manufacturing as a Method to Reduce Costs by Eliminating Waste
Lean manufacturing is one of the most effective methodologies for cost reduction, as it emphasizes the elimination of waste (Muda) in all forms. Waste, in the lean context, includes any activity that does not add value to the customer. By systematically identifying and eliminating these non-value-adding activities, lean manufacturing helps reduce costs while improving quality and efficiency.
The seven types of waste targeted by lean manufacturing are:
- Overproduction – Producing more than is needed, leading to excess inventory and storage costs.
- Waiting – Idle time caused by delays in production or material flow.
- Transportation – Unnecessary movement of materials or products.
- Overprocessing – Performing more work or using higher quality materials than necessary.
- Inventory – Excess raw materials or finished goods that tie up capital and storage space.
- Motion – Unnecessary movements by workers that do not add value.
- Defects – Errors that result in rework or scrap, increasing material and labor costs.
Lean consultants employ tools such as Value Stream Mapping (VSM) to visualize the flow of materials and information through the production process, identifying where waste occurs. Based on this analysis, they propose targeted improvements, such as reorganizing workflows, reducing batch sizes, or implementing Just-In-Time (JIT) inventory practices.
Another cornerstone of lean manufacturing is continuous improvement (Kaizen), which fosters a culture of ongoing incremental improvements. By empowering employees to identify inefficiencies and propose solutions, organizations can achieve sustained cost reductions over time.
In addition to waste elimination, lean manufacturing enhances resource utilization. For instance, optimizing machine setup times using techniques like Single-Minute Exchange of Dies (SMED) reduces downtime and increases overall productivity. Similarly, adopting 5S practices (Sort, Set in Order, Shine, Standardize, Sustain) improves workplace organization, reducing wasted time and effort.
Cost reduction consulting and lean manufacturing are complementary approaches to achieving financial efficiency in manufacturing. Consultants not only identify cost-saving opportunities across operations but also guide organizations in adopting lean methodologies to eliminate waste and foster a culture of continuous improvement. The result is a leaner, more efficient, and financially sustainable manufacturing operation that remains competitive in a challenging market environment.
Case Studies and Success Stories
Examples of Successful Manufacturing Consulting Engagements
Case Study 1: Implementing Lean Manufacturing to Reduce Costs A mid-sized automotive parts manufacturer faced high production costs and inefficiencies in its assembly line. A consulting firm specializing in lean manufacturing conducted a detailed value stream mapping exercise to identify waste in the production process. The analysis revealed excessive waiting times between workstations and significant overproduction due to batch-oriented scheduling.
The consultants introduced a pull-based production system using Just-In-Time (JIT) principles, reducing overproduction and inventory costs. They also facilitated Kaizen workshops to streamline workflows and trained employees to use 5S for better workplace organization. As a result, the company reduced production cycle times by 20% and cut operating costs by 15%, while increasing on-time delivery rates to over 95%.
Case Study 2: Digital Transformation for a Food Processing Company A large food processing company wanted to enhance operational visibility and reduce downtime across its facilities. A smart manufacturing consulting firm implemented an IoT-enabled system that collected real-time data from production equipment. This data was analyzed using machine learning algorithms to predict potential equipment failures and recommend proactive maintenance actions.
The consultants also integrated a Manufacturing Execution System (MES) to provide a unified view of production metrics. Operators and managers could now monitor performance indicators such as overall equipment effectiveness (OEE) and downtime in real-time. The company achieved a 25% reduction in downtime and a 10% increase in overall productivity, leading to significant cost savings and improved product quality.
Case Study 3: Sustainable Manufacturing for a Consumer Electronics Firm A consumer electronics company sought to reduce its environmental impact while maintaining competitive pricing. A consulting firm specializing in sustainability conducted an energy audit and found that outdated equipment and inefficient processes were driving high energy consumption. They recommended replacing old machinery with energy-efficient models and reengineering processes to minimize material waste.
The consultants also implemented a closed-loop recycling system for by-products and educated the workforce on sustainable practices. Within a year, the company reduced energy costs by 30%, cut waste by 40%, and obtained a sustainability certification that enhanced its market reputation.
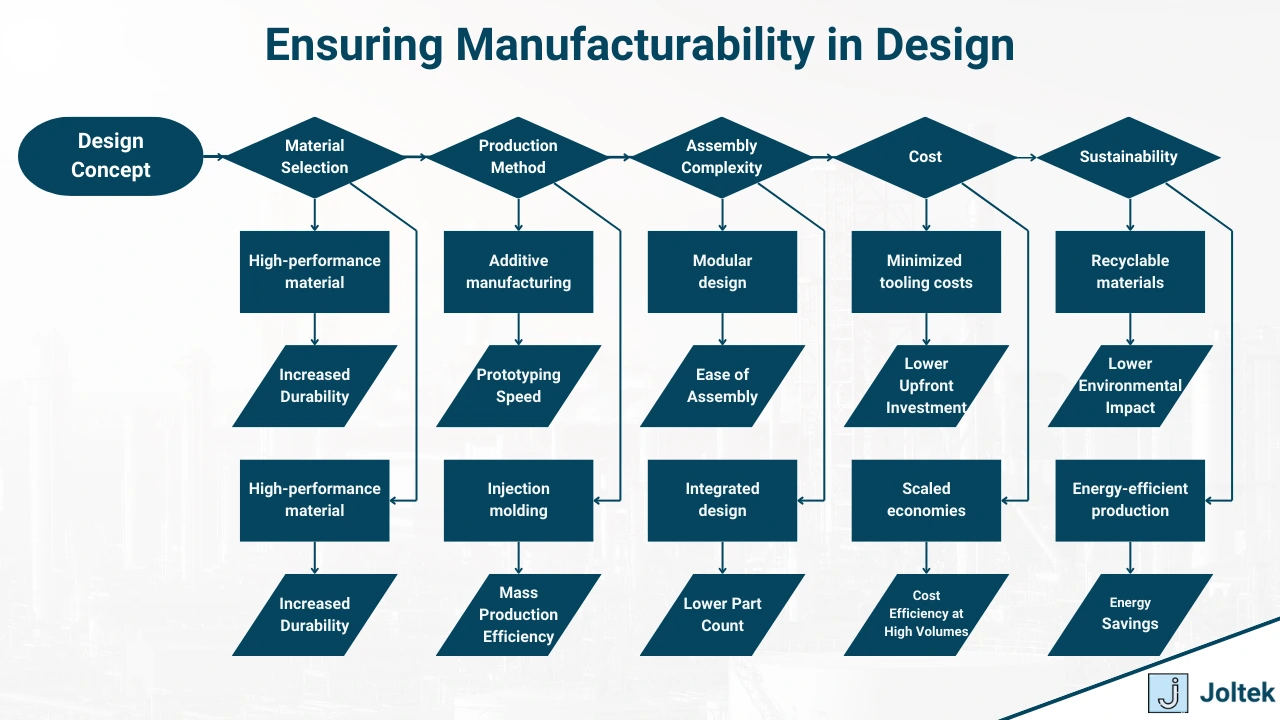
Lessons Learned and Best Practices
- Tailored Solutions Are Key: Each manufacturing facility has unique challenges and opportunities. Success depends on crafting solutions that align with the organization’s specific goals, operational constraints, and industry requirements. Consultants must avoid a one-size-fits-all approach and focus on delivering customized strategies.
- Data-Driven Decision-Making Drives Results: The use of advanced analytics, IoT, and machine learning can provide actionable insights that lead to substantial operational improvements. Companies that embrace data-driven tools are better positioned to achieve long-term success in efficiency and cost management.
- Employee Engagement Is Crucial: A common thread in successful consulting engagements is the involvement of employees at all levels. Engaging the workforce through training, workshops, and empowerment programs fosters buy-in, ensuring that changes are implemented effectively and sustained over time.
- Continuous Improvement Is a Must: Manufacturing success is not a one-time achievement but a continuous journey. Organizations that adopt frameworks like Kaizen and embed a culture of ongoing improvement are more likely to maintain their competitive edge in dynamic markets.
- Technology Integration Requires Strategic Planning: While adopting advanced technologies is essential, rushing into digital transformation without a clear roadmap can lead to inefficiencies and wasted investments. Consulting engagements that include detailed planning, piloting, and phased implementation yield better outcomes.
- Sustainability Offers Dual Benefits: Incorporating sustainable practices not only reduces environmental impact but also drives cost savings and enhances brand reputation. Companies that integrate sustainability into their operations position themselves as leaders in both ethics and efficiency.
These case studies and lessons demonstrate the transformative impact of manufacturing consulting. Whether addressing inefficiencies, adopting new technologies, or embracing sustainability, consulting engagements provide the expertise, guidance, and tools necessary to achieve measurable improvements and long-term success.
Conclusion
The Evolving Role of Manufacturing Consulting in the Industry
Manufacturing consulting has become a cornerstone for organizations striving to navigate the complexities of a rapidly evolving industrial landscape. Historically focused on operational efficiency and cost reduction, consulting today encompasses a much broader spectrum of services, including digital transformation, sustainability, workforce development, and strategic planning. Consultants act as trusted advisors, bringing specialized knowledge, tools, and methodologies to help manufacturers solve problems, seize opportunities, and future-proof their operations.
The role of consultants is not only to identify inefficiencies but also to foster innovation and resilience. By guiding companies through the adoption of advanced technologies, such as smart manufacturing and additive manufacturing, consultants enable businesses to remain competitive in a fast-paced market. They also provide critical insights into optimizing supply chains, navigating regulatory complexities, and aligning manufacturing capabilities with business objectives.
Additionally, manufacturing consultants play a pivotal role in shaping organizational culture. By embedding principles like continuous improvement (Kaizen) and lean methodologies, they help create environments where innovation and adaptability thrive. This cultural transformation is essential for sustaining gains achieved through consulting engagements.
Future Trends and Considerations
The manufacturing sector is undergoing unprecedented change, driven by technological advancements, shifting market demands, and global challenges. Manufacturing consulting will continue to evolve to address these dynamics. Several key trends and considerations will shape the future of the industry:
- Digital Transformation and Industry 4.0: As Industry 4.0 technologies mature, manufacturers will increasingly rely on consultants to integrate IoT, AI, robotics, and advanced analytics into their operations. Consultants will play a critical role in bridging the gap between technology providers and manufacturers, ensuring seamless implementation and maximizing return on investment.
- Sustainability and Green Manufacturing: The push for sustainability will intensify, with manufacturers seeking ways to reduce energy consumption, minimize waste, and adopt circular economy practices. Consultants will help companies achieve environmental goals while maintaining profitability and compliance with regulations.
- Global Supply Chain Resilience: Recent disruptions have underscored the importance of resilient supply chains. Future consulting engagements will focus on enhancing supply chain visibility, diversifying sourcing strategies, and leveraging digital tools to manage risks and improve efficiency.
- Workforce Transformation: As automation and digital tools reshape the workforce, consultants will help organizations upskill employees, design effective training programs, and foster collaboration between human and machine. The emphasis will be on creating a workforce that is both adaptable and capable of driving innovation.
- Personalization and Mass Customization: Consumer demand for personalized products will push manufacturers to adopt more flexible production systems. Consultants will guide companies in implementing strategies like modular manufacturing and advanced automation to meet these demands without sacrificing efficiency.
- Focus on Small and Medium Enterprises (SMEs): While large corporations have led the adoption of advanced manufacturing practices, SMEs will increasingly seek consulting support to remain competitive. Consultants will tailor their approaches to address the unique challenges faced by smaller manufacturers, such as limited resources and workforce constraints.
- Integration of Emerging Technologies: Technologies such as quantum computing, blockchain, and augmented reality are poised to disrupt manufacturing further. Consultants will help manufacturers explore the potential of these innovations and integrate them into their operations where relevant.
In conclusion, manufacturing consulting is more vital than ever, offering the expertise and strategic guidance needed to thrive in an era of rapid change. As the industry continues to evolve, consultants will remain at the forefront, helping organizations adapt, innovate, and succeed in an increasingly complex global economy. The future of manufacturing consulting lies not only in solving today's challenges but in anticipating tomorrow's opportunities, ensuring that manufacturers are equipped to lead in a competitive and sustainable future.
References
- Consulting Service Market Size | Industry Growth & Analysis Report
This report provides insights into the consulting service market, including growth projections and key industry players.
Mordor Intelligence - What is Lean Manufacturing and the 5 Principles Used? - TWI
An overview of lean manufacturing principles, detailing the five core concepts: value, value stream, flow, pull, and perfection.
Twi Global - 2025 Manufacturing Industry Outlook - Deloitte Insights
This outlook discusses trends and projections in the manufacturing industry, highlighting investment patterns and technological advancements.
Deloitte - Guide: Fundamentals Of Lean Six Sigma - Learn Lean Sigma
A comprehensive guide on Lean Six Sigma, explaining how lean principles integrate with Six Sigma methodologies to enhance operational efficiency.
Learn Lean Sigma - Reports - The Manufacturing Institute
A collection of reports focusing on the manufacturing sector, addressing topics such as workforce development and industry trends.
The Manufacturing Institute - The Five Principles of Lean - The Lean Way
An article elaborating on the five lean principles and their application in improving workplace efficiency.
The Lean Way - Engineering Services Market - Size, Trends & Industry Overview
This report analyzes the engineering services market, covering market size, trends, and key industry players.
Mordor Intelligence - The 5 Core Lean Manufacturing Principles - A Comprehensive Guide - Lio Blog
A detailed guide on lean manufacturing principles, discussing their implementation and benefits in various industries.
Lio Blog - Consulting Market Size, Share, and Industry Report [2032] - Dataintelo
An industry report providing insights into the consulting market's size, share, and projected growth up to 2032.
DataIntelo - Understanding Lean Manufacturing | KAIZEN Article
An article that delves into the core principles of lean manufacturing and the process of identifying and eliminating waste.
Kaizen - Manufacturing Consulting - Bain & Company
An overview of manufacturing consulting services offered by Bain & Company, focusing on digital operations and Industry 4.0 leadership.
Bain & Company - The Principles Of Lean Manufacturing
An article discussing the principles of lean manufacturing and their application in improving production efficiency.
Manufacturing.net - IBISWorld - Industry Market Research, Reports, & Statistics
A resource offering industry market research reports, statistics, analysis, data, trends, and forecasts across various sectors.
IBISWorld - Lean Manufacturing: Meaning, Principles and Tools
An article explaining lean manufacturing, its core principles, and the tools used to implement lean practices.
GeeksforGeeks - Industry Insights - Bain & Company
A collection of industry insights and data-driven perspectives on various sectors, helping businesses stay ahead of market trends.
Bain & Company - How to Implement Lean Manufacturing: Principles, Techniques, and ...
A guide on implementing lean manufacturing, discussing principles, techniques, and the differences between lean and traditional manufacturing methods.
Industrial Trainer - Industrial manufacturing industry insights and services: PwC
Insights into the industrial manufacturing industry, discussing disruptions, technological advancements, and strategies for digital transformation.
PwC - Lean Manufacturing: Principles, Tools and Methods - Valin
A guidebook on lean manufacturing, detailing principles, tools, and methods for optimizing production processes.
Valin - 2024 Contract Manufacturing Outlook - Full Report - Society of Chemical ...
A report providing insights into the contract manufacturing sector, including trends, capacities, and market segments.
SOCMA - Lean Methodology: The 5 Principles of Lean Methodology
An article discussing the history and five key principles of lean methodology, with applications in business process improvement.
MasterClass - Consulting industry in the United States - statistics & facts
Statistics and facts about the consulting services industry in the U.S., including market size and employment data.
Statista - 5 Lean Principles Every Engineer Should Know - ASME
An article outlining five key lean principles essential for engineers, focusing on value, value stream, flow, pull, and perfection.
ASME - Lean manufacturing - Wikipedia
A comprehensive overview of lean manufacturing, its history, principles, and applications across various industries.
Wikipedia
These references provide a comprehensive foundation for understanding the multifaceted aspects of manufacturing consulting, lean manufacturing principles, and industry trends.