Introduction
What is Lean Six Sigma?
Lean Six Sigma is a process improvement methodology that integrates the principles of Lean and Six Sigma to enhance efficiency, reduce waste, and improve quality in organizational operations.
- Lean focuses on identifying and eliminating waste—activities that do not add value to the customer—while streamlining workflows for maximum efficiency.
- Six Sigma emphasizes reducing process variation and defects through data-driven decision-making and rigorous statistical analysis.
Together, Lean and Six Sigma create a powerful framework for achieving operational excellence. This integrated approach is applied through structured projects managed by certified practitioners (White, Green, or Black Belts). Lean Six Sigma’s primary goal is to deliver consistent, high-quality results with optimized resource use.
Why is Lean Six Sigma Important in Manufacturing Today?
Manufacturing faces constant pressure to meet rising customer expectations, minimize costs, and adapt to technological advances. Lean Six Sigma is particularly valuable because it addresses these challenges holistically:
- Cost Reduction: By targeting inefficiencies and waste, manufacturers can significantly lower operating expenses without compromising quality.
- Improved Quality: The statistical rigor of Six Sigma ensures processes are fine-tuned to deliver consistent, defect-free products.
- Enhanced Speed: Lean principles help remove bottlenecks and optimize workflows, improving throughput and delivery times.
- Employee Empowerment: A Lean Six Sigma culture fosters problem-solving and continuous improvement, encouraging employees to actively contribute to operational success.
- Sustainability and Innovation: By addressing waste and inefficiencies, Lean Six Sigma not only improves profitability but also aligns with sustainability goals and spurs creative solutions.
As manufacturing evolves with digital transformation and Industry 4.0 technologies, Lean Six Sigma serves as a foundational methodology that complements and enhances modern advancements like automation, IoT, and data analytics.
Scope of the Guide
This guide explores Lean Six Sigma with a specific focus on its application in manufacturing. Key areas covered include:
- The origins and evolution of Lean Six Sigma and its integration into modern manufacturing practices.
- Core principles and tools used to drive efficiency and quality improvements.
- Case studies showcasing real-world success stories and data-backed outcomes.
- A balanced view of the methodology’s benefits and limitations.
- Alternatives and complementary approaches to Lean Six Sigma for different operational scenarios.
- Insights into its future role, particularly in the context of digital transformation and Industry 4.0.
Whether you're exploring Lean Six Sigma for the first time or looking to deepen your expertise, this guide offers a comprehensive resource to help you harness its potential for operational excellence in manufacturing.
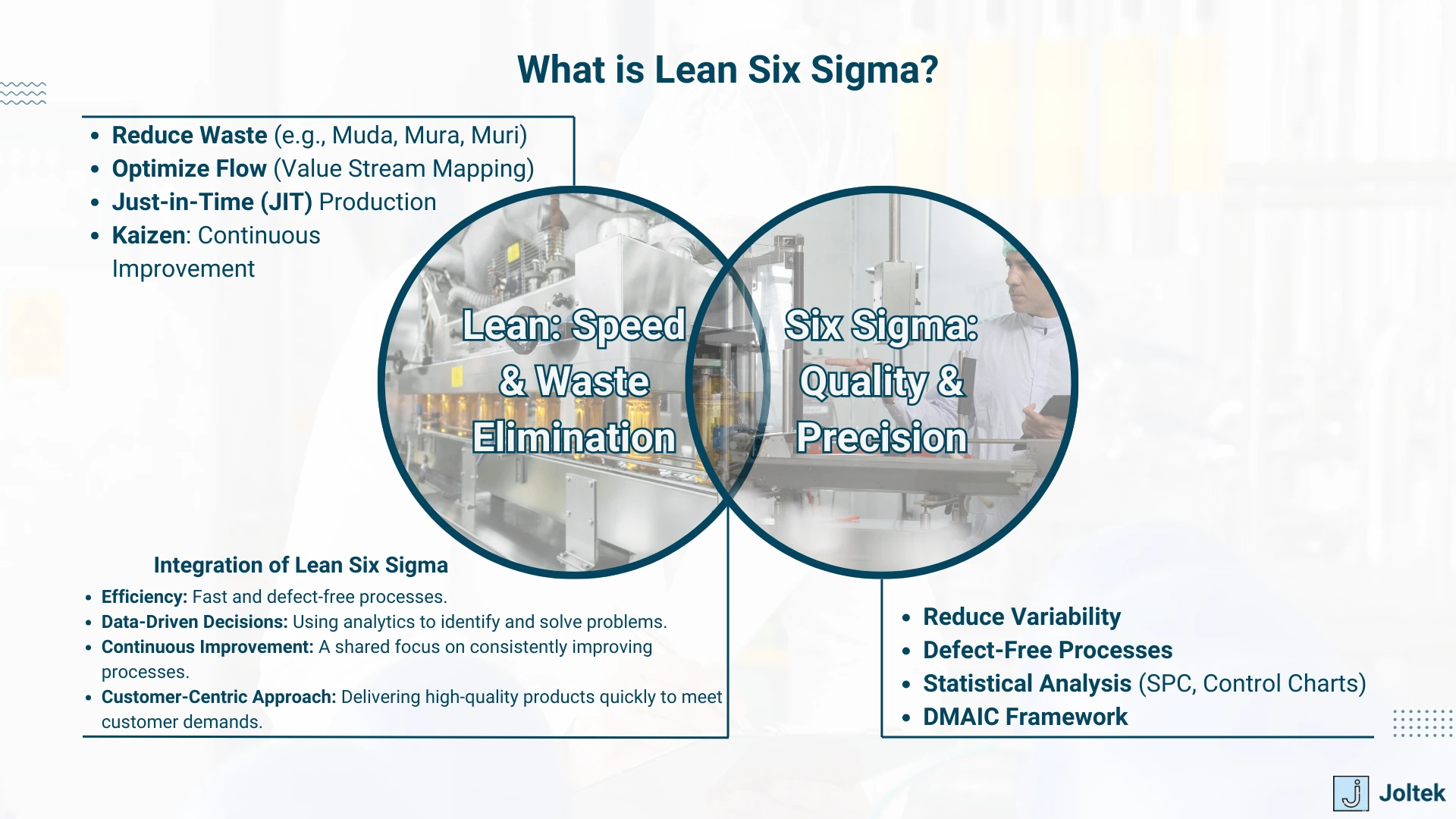
The Origins of Lean Six Sigma
Historical Context
Origins of Lean (Toyota Production System)
Lean traces its roots to the Toyota Production System (TPS), developed in post-World War II Japan under the leadership of engineers like Taiichi Ohno and Shigeo Shingo. Facing limited resources, Toyota sought to optimize production by eliminating waste and maximizing value. The key principles of TPS include:
- Muda (Waste): Eliminating activities that do not add value, such as overproduction, waiting, and defects.
- Mura (Unevenness): Addressing inconsistencies in production processes.
- Muri (Overburden): Avoiding unnecessary strain on workers and equipment.
Other concepts like Just-in-Time (JIT) production and continuous improvement (Kaizen) became foundational to Lean thinking. Over time, these principles extended beyond Toyota and Japan, shaping manufacturing practices worldwide.
Origins of Six Sigma (Motorola and GE’s Influence)
Six Sigma emerged in the 1980s at Motorola as a response to increasing defects in electronic products. Engineer Bill Smith pioneered the methodology, emphasizing the reduction of process variation to improve quality.
- Six Sigma uses statistical tools to measure and improve processes, aiming for a defect rate of fewer than 3.4 defects per million opportunities (DPMO).
- Motorola’s success with Six Sigma led to its formal adoption, earning the company a Malcolm Baldrige National Quality Award in 1988.
General Electric (GE), under CEO Jack Welch, popularized Six Sigma in the 1990s. Welch integrated Six Sigma into GE’s culture, applying it across all operations to improve efficiency, reduce costs, and drive innovation. This widespread adoption by a global conglomerate established Six Sigma as a cornerstone of modern quality management.
The Fusion of Lean and Six Sigma
How the Two Methodologies Combined
Lean and Six Sigma were initially separate methodologies addressing different aspects of process improvement:
- Lean focuses on speed and waste elimination.
- Six Sigma targets quality and precision.
The fusion of these methodologies began in the late 1990s, driven by the realization that combining Lean’s efficiency with Six Sigma’s rigor created a more powerful approach. Together, they address both process flow and process quality, offering a holistic framework for continuous improvement.
Key Contributors and Milestones
- Michael George: His 2002 book Lean Six Sigma formally introduced the combined methodology, outlining its benefits for organizations.
- Six Sigma Academy: Prominent in integrating Lean principles into Six Sigma training.
- Adoption by Industry Leaders: Companies like Honeywell and 3M became early adopters, showcasing the combined methodology’s potential to revolutionize operations.
Evolution Over Time
Adoption Trends in Manufacturing
Lean Six Sigma gained rapid traction in manufacturing due to its ability to deliver measurable improvements in efficiency, quality, and cost. Its adaptability made it suitable for diverse applications, from assembly lines to supply chain management.
- 1990s: Early adopters focused on integrating Lean and Six Sigma principles in operational areas.
- 2000s: Broader adoption across industries, with manufacturing at the forefront.
- 2010s to Present: Integration with digital tools and Industry 4.0 technologies, allowing real-time monitoring and data-driven improvements.
Global Impact Across Industries
While manufacturing remains a stronghold for Lean Six Sigma, its principles have expanded into other sectors:
- Healthcare: Streamlining patient care and reducing medical errors.
- Financial Services: Optimizing transaction processing and customer service.
- Retail: Improving inventory management and supply chain efficiency.
Today, Lean Six Sigma is a recognized standard for operational excellence, with certifications offered globally and methodologies integrated into enterprise strategies. It continues to evolve, adapting to the demands of a rapidly changing industrial landscape.
Principles of Lean Six Sigma
Lean Principles
Lean principles focus on creating value for the customer by optimizing processes, eliminating waste, and fostering continuous improvement. These principles are the foundation of operational efficiency.
Value Stream Mapping
Value Stream Mapping (VSM) is a tool used to visualize the flow of materials and information across the production process.
- It identifies value-added and non-value-added activities.
- Helps pinpoint bottlenecks and inefficiencies.
- Provides a blueprint for optimizing workflows and reducing lead times.
Eliminating Waste (Muda, Mura, Muri)
Lean aims to address three types of inefficiencies:
- Muda (Waste): Non-value-added activities such as overproduction, defects, excess inventory, unnecessary motion, over-processing, waiting, and unused talent.
- Mura (Unevenness): Variability in workloads or outputs that disrupt process flow.
- Muri (Overburden): Excessive stress on workers or equipment, leading to breakdowns and errors.
Just-in-Time (JIT) Production
JIT ensures that materials and components are delivered only as needed, minimizing inventory costs and reducing waste.
- Key practices include small-batch production, pull systems, and responsive supply chains.
- Requires precise scheduling and close supplier collaboration.
Continuous Flow
Continuous flow emphasizes smooth and uninterrupted movement of products through the production process.
- Reduces idle time and waiting.
- Aligns production rates with customer demand to avoid overproduction or shortages.
Kaizen and Continuous Improvement
Kaizen is a philosophy of incremental, continuous improvement involving all employees.
- Encourages regular evaluation of processes and workflows.
- Uses tools like Plan-Do-Check-Act (PDCA) cycles for systematic problem-solving.
- Promotes a culture of collaboration and innovation.
Six Sigma Principles
Six Sigma principles focus on reducing variation and defects to improve process reliability and quality. The methodology relies heavily on data-driven decision-making.
DMAIC Methodology (Define, Measure, Analyze, Improve, Control)
DMAIC is the core problem-solving framework in Six Sigma:
- Define: Identify the problem, customer requirements, and project goals.
- Measure: Collect and quantify relevant data to establish baselines.
- Analyze: Identify root causes of defects or inefficiencies using statistical tools.
- Improve: Develop and implement solutions to address root causes.
- Control: Establish controls to sustain improvements and prevent regression.
Process Capability (Cp and Cpk)
Process capability indices measure how well a process performs relative to specifications:
- Cp: Measures process spread compared to specification limits.
- Cpk: Adjusts for process centering, providing a more realistic capability assessment.
Statistical Tools and Data Analysis
Six Sigma relies on statistical methods to understand and improve processes:
- Tools include Pareto charts, control charts, hypothesis testing, regression analysis, and design of experiments (DOE).
- Statistical Process Control (SPC) is used to monitor and maintain process stability.
Defining Critical to Quality (CTQ) Metrics
CTQ metrics identify customer-driven performance standards:
- Define what is critical to the customer, such as delivery time, defect rate, or product durability.
- Align operational goals with customer expectations to ensure satisfaction.
Synergies Between Lean and Six Sigma
The integration of Lean and Six Sigma combines the strengths of both methodologies for maximum impact:
- Lean for Speed, Six Sigma for Precision: Lean accelerates processes by eliminating waste, while Six Sigma ensures quality and consistency through data-driven improvements.
- Complementary Tools: Value Stream Mapping (Lean) identifies inefficiencies, while DMAIC (Six Sigma) addresses root causes with precision.
- Shared Focus on Continuous Improvement: Both methodologies prioritize ongoing efforts to enhance processes, reduce costs, and improve customer satisfaction.
- Broader Application: Lean Six Sigma can address both the flow and quality of processes, making it versatile for a wide range of industries and challenges.
By leveraging these principles, organizations can achieve a balanced approach to operational excellence, ensuring both efficiency and high-quality outputs.
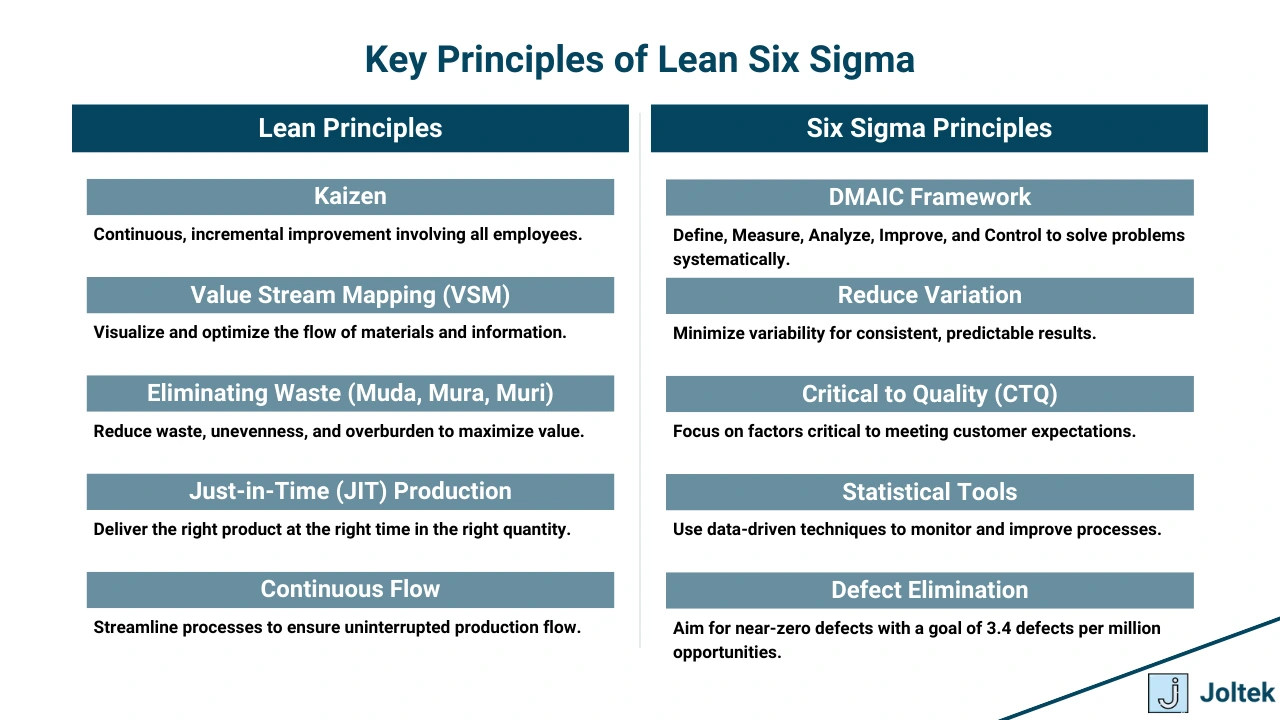
Implementing Lean Six Sigma in Manufacturing
Key Steps for Implementation
Preparing the Organization
Successful Lean Six Sigma implementation begins with preparing the organization for change. This involves securing strong leadership commitment, as executives play a crucial role in aligning Lean Six Sigma initiatives with strategic business objectives. Equally important is fostering a culture of collaboration and continuous improvement, where employees at all levels feel empowered to contribute. Organizations must also allocate adequate resources, including skilled personnel, technology, and funding, to sustain improvement projects. Without these foundational steps, Lean Six Sigma efforts are likely to encounter resistance or fail to achieve meaningful results.
Building a Cross-Functional Team
The success of a Lean Six Sigma project depends on assembling a cross-functional team with diverse expertise. This team should include individuals who understand the processes under review, technical experts skilled in Lean Six Sigma tools, and management representatives who can make critical decisions. A structured hierarchy is often followed, with roles like Green Belts and Black Belts leading projects and executive sponsors providing oversight. The diversity of perspectives ensures that solutions are both technically sound and practical to implement across departments.
Training and Certification
Equipping team members with the right skills is essential. Training programs focus on Lean Six Sigma methodologies, such as the DMAIC framework and statistical analysis. Certifications are structured into levels—White Belt, Green Belt, Black Belt, and Master Black Belt—with each level signifying deeper expertise. Certified practitioners are better equipped to lead projects, analyze data, and implement sustainable changes that drive measurable improvements.
Identifying Target Processes
Not all processes are equally suited for Lean Six Sigma projects. Identifying the right targets involves selecting processes that are critical to customer satisfaction or highly impactful to the bottom line. These are often areas with visible inefficiencies, high defect rates, or costly delays. A clear understanding of customer needs, operational goals, and baseline metrics guides this selection process.
Tools and Techniques
5S Methodology
The 5S methodology—Sort, Set in Order, Shine, Standardize, and Sustain—is a foundational Lean tool that organizes workplaces for efficiency and safety. By maintaining a clean and structured environment, manufacturers can reduce waste, improve productivity, and enhance employee morale.
Value Stream Mapping (VSM)
Value Stream Mapping is a powerful visualization tool that maps out the flow of materials and information across a process. It identifies bottlenecks and non-value-added activities, enabling teams to design an optimized future-state process.
Fishbone Diagrams (Ishikawa)
Fishbone diagrams are used for root cause analysis. By categorizing potential causes of a problem, teams can systematically investigate and address the underlying issues. This tool is especially useful during the Analyze phase of DMAIC.
Control Charts
Control charts are statistical tools that monitor process stability over time. They help detect variations that are outside acceptable limits, allowing teams to take corrective actions before defects occur.
Kanban Systems
Kanban is a scheduling system that supports Just-in-Time production. By visualizing workflow and managing task assignments, it reduces bottlenecks and ensures smooth production flow.
Statistical Process Control (SPC)
SPC uses statistical methods to monitor and control processes. By analyzing variations in real-time, SPC ensures processes remain within specified limits, minimizing defects and maintaining consistency.
Measuring Success
Metrics for Success
The success of Lean Six Sigma projects is measured using key performance indicators (KPIs) such as Defects Per Million Opportunities (DPMO), cycle time, lead time, and cost savings. These metrics provide quantifiable evidence of improvement and help evaluate the impact on overall performance.
Continuous Feedback and Iteration
Sustaining improvements requires a system of ongoing feedback and iteration. Teams must establish control mechanisms to ensure changes are maintained and continuously refined. Regular reviews and adjustments ensure that processes remain aligned with organizational goals and adapt to evolving needs.
By following these structured steps, leveraging robust tools, and focusing on measurable outcomes, manufacturers can unlock the full potential of Lean Six Sigma to drive operational excellence.
Real-World Applications
Case Studies in Manufacturing
Examples of Operational Efficiency Improvements
A global automotive parts manufacturer implemented Lean Six Sigma to optimize its assembly line. By applying Value Stream Mapping (VSM) and eliminating non-value-added steps, the company reduced idle time by 30%, increasing throughput without additional capital investments. The improvements stemmed from a systematic reorganization of workstations and better alignment of processes with customer demand.
Cost Reduction and Waste Elimination Stories
In the electronics sector, a major producer of consumer devices used Lean Six Sigma to address excessive material waste during production. By conducting a root cause analysis with Fishbone diagrams and deploying a Kanban system for inventory management, the company reduced material waste by 20%. This translated to annual cost savings of $2.5 million while maintaining high-quality standards.
Lead Time and Quality Improvement Projects
A food and beverage manufacturer focused on reducing lead times for a popular product line. Using the DMAIC framework, they analyzed bottlenecks in the production process and streamlined workflows. The result was a 15% reduction in lead times and a 25% decrease in customer complaints related to product quality, achieved by improving process stability with Statistical Process Control (SPC) tools.
Data-Driven Success Metrics
Before-and-After Analysis
Lean Six Sigma projects are grounded in measurable outcomes. For instance, a medical device manufacturer aiming to improve defect rates in precision assembly lines conducted a before-and-after analysis. Initial defect rates were 4.2%, but after implementing Six Sigma techniques, including process capability studies (Cp and Cpk), the defect rate dropped to 0.7%. This improvement not only increased customer satisfaction but also reduced warranty claims significantly.
ROI and Long-Term Impact on KPIs
The long-term financial benefits of Lean Six Sigma are often reflected in metrics such as Return on Investment (ROI) and operational KPIs. A case study in the aerospace industry showed a $10 million ROI within two years after adopting Lean Six Sigma, achieved through a combination of waste reduction and enhanced production efficiency. KPIs such as on-time delivery rates improved from 85% to 96%, demonstrating the methodology’s far-reaching impact.
Applications Across Industries
Automotive
Lean Six Sigma has been extensively applied in automotive manufacturing to improve assembly processes, reduce defects, and optimize supply chains. Companies like Toyota and Ford have used these principles to remain competitive in an industry where efficiency and quality are paramount.
Electronics
In the fast-paced world of electronics, Lean Six Sigma helps manufacturers respond to short product lifecycles and high consumer expectations. For instance, semiconductor producers use statistical tools to reduce variability in production, achieving higher yields and lower production costs.
Food and Beverage
The food and beverage sector benefits from Lean Six Sigma by improving hygiene standards, reducing spoilage, and enhancing production efficiency. A global beverage company implemented a Lean Six Sigma initiative to optimize bottling operations, cutting changeover times by 40% and reducing energy consumption.
Medical Device Manufacturing
In medical device production, precision and compliance with stringent regulations are critical. Lean Six Sigma enables manufacturers to reduce defects, improve documentation processes, and meet regulatory requirements efficiently. For example, a company producing surgical instruments reduced non-conformities by 50% through the DMAIC process, ensuring both quality and compliance.
Lean Six Sigma’s adaptability allows it to address diverse challenges across industries, making it an essential tool for driving operational excellence and achieving sustained success in manufacturing.
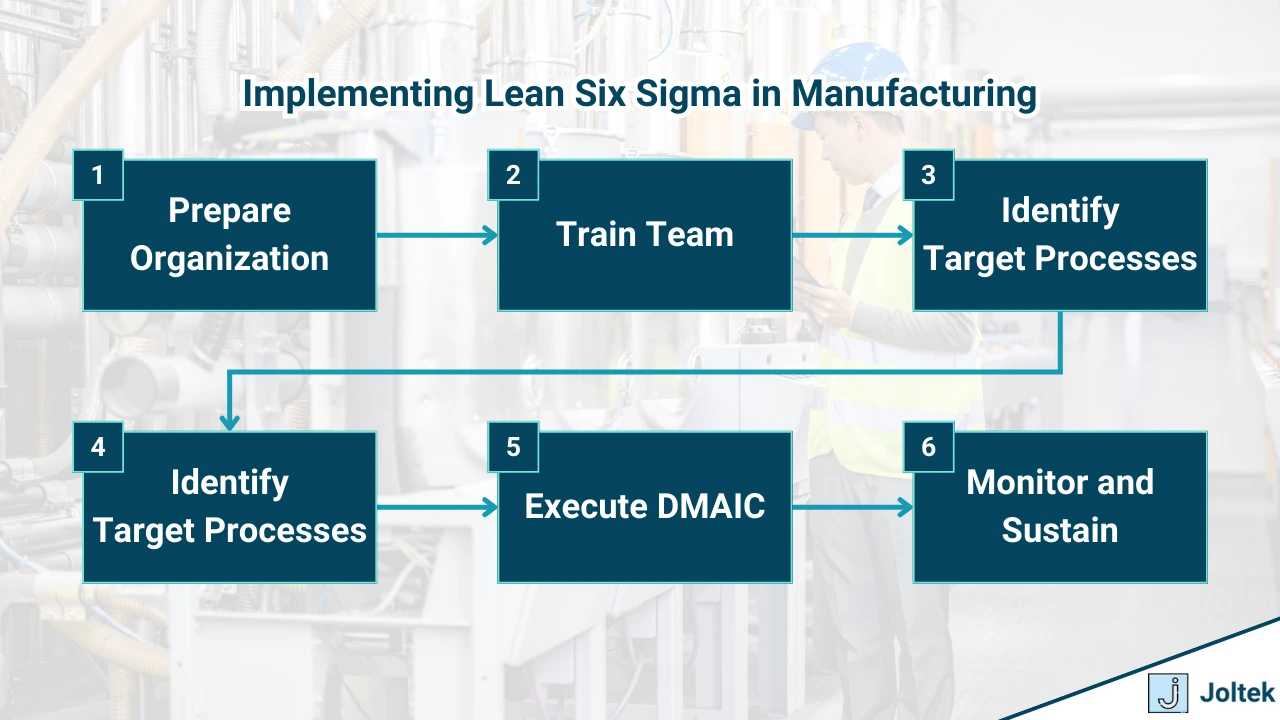
Advantages and Disadvantages
Key Benefits
Operational Excellence
Lean Six Sigma drives operational excellence by streamlining processes, eliminating inefficiencies, and creating a culture of continuous improvement. It ensures that operations are optimized for both speed and precision, leading to better alignment with business goals.
Enhanced Quality Control
The focus on reducing process variation and defects leads to consistent high-quality outputs. By using data-driven methodologies such as Statistical Process Control (SPC), companies can achieve and maintain strict quality standards, even in complex production environments.
Cost Savings
By identifying and removing waste in all its forms—whether it’s material waste, rework, or overproduction—Lean Six Sigma delivers significant cost reductions. Additionally, improved efficiency and quality reduce warranty claims, returns, and other associated costs.
Workforce Empowerment
A key element of Lean Six Sigma is engaging employees at all levels. Through training and active participation in problem-solving initiatives, employees feel empowered and invested in the success of the organization. This boosts morale and productivity, fostering a culture of ownership and accountability.
Customer Satisfaction
With its dual focus on efficiency and quality, Lean Six Sigma enables companies to deliver faster, better, and more reliable products to customers. This directly translates into higher satisfaction, stronger brand loyalty, and a competitive edge in the marketplace.
Challenges and Limitations
High Initial Investment
Implementing Lean Six Sigma requires a significant upfront investment in training, certification, tools, and resources. Organizations must also dedicate time and effort to create infrastructure for data collection, analysis, and project management.
Cultural Resistance
Introducing Lean Six Sigma often meets resistance from employees and managers, especially in organizations where a culture of change and continuous improvement is not well established. Resistance can stem from fear of added workloads, skepticism about the methodology, or a reluctance to adopt new practices.
Complexity in Implementation
The methodology’s reliance on statistical tools, detailed process analysis, and cross-functional collaboration can make it challenging to implement. Without strong leadership and well-defined project scopes, initiatives can become overly complex or lose focus.
Dependence on Data Accuracy
Lean Six Sigma is highly dependent on accurate and reliable data. Poor data quality, incomplete records, or inconsistent measurement systems can undermine the effectiveness of projects and lead to incorrect conclusions.
Lessons Learned from Failed Projects
Lean Six Sigma projects sometimes fail, and analyzing these failures offers valuable insights:
- Lack of Leadership Support: Projects without active involvement and sponsorship from leadership often lack direction and fail to sustain momentum.
- Unrealistic Expectations: Over-promising results or underestimating the effort required to implement changes can lead to disillusionment among stakeholders.
- Neglecting the Human Element: Failure to engage employees and address cultural resistance often results in poor adoption of Lean Six Sigma practices.
- Inadequate Training and Resources: Teams that lack proper training in tools and methodologies struggle to execute projects effectively, leading to subpar outcomes.
- Not Aligning with Business Goals: Projects that do not align with overarching organizational objectives risk becoming siloed initiatives with little measurable impact.
By recognizing these challenges and learning from past failures, organizations can improve the odds of success and fully harness the benefits of Lean Six Sigma.
Alternatives to Lean Six Sigma
Other Continuous Improvement Methodologies
Total Quality Management (TQM)
TQM is a management approach centered on continuous quality improvement across all organizational processes. It emphasizes customer satisfaction, employee involvement, and process management as core principles. Unlike Lean Six Sigma, which relies on statistical tools and specific project frameworks, TQM focuses more broadly on creating a quality-oriented culture throughout the organization.
Theory of Constraints (TOC)
TOC focuses on identifying and addressing the bottleneck or constraint in a system that limits its overall performance. The methodology uses a process called the Five Focusing Steps to:
- Identify the constraint.
- Exploit the constraint.
- Subordinate other processes to the constraint.
- Elevate the constraint.
- Repeat the process for continuous improvement.
TOC is particularly effective in environments where a single limiting factor is disrupting production or efficiency, such as supply chain bottlenecks or capacity constraints in manufacturing.
Agile and Scrum in Manufacturing
Originally developed for software development, Agile and Scrum principles are increasingly applied in manufacturing to enhance adaptability and speed. Agile focuses on iterative progress, while Scrum uses structured cycles (sprints) to break work into manageable pieces. These methodologies are well-suited for industries with rapidly changing demands or highly customized production requirements.
How These Alternatives Compare
Pros and Cons
- TQM: Broad and holistic but lacks the structured, data-driven tools of Lean Six Sigma. It is ideal for organizations seeking cultural change rather than specific, measurable projects.
- TOC: Highly effective for targeting and alleviating bottlenecks but less comprehensive in addressing waste and variability throughout the entire process. It works best for systems where a single constraint dominates performance.
- Agile/Scrum: Excellent for flexibility and quick adjustments but less suitable for environments requiring strict process control or statistical precision. Agile thrives in high-variability environments, such as custom manufacturing or R&D.
Situations Where They Are More Suitable
- TQM is ideal for organizations starting their journey toward quality improvement, focusing on cultural alignment and employee involvement.
- TOC works well in operations where specific bottlenecks significantly limit output, such as supply chain disruptions or capacity issues.
- Agile and Scrum are better suited for projects requiring high customization, short development cycles, or frequent adjustments, such as prototyping or small-batch production.
Integrating Other Approaches with Lean Six Sigma
Lean Six Sigma can be complemented by other methodologies to address specific challenges or enhance overall performance:
- TQM Integration: Use Lean Six Sigma’s data-driven tools to execute TQM’s broader quality goals. For example, Six Sigma’s DMAIC framework can bring structure to TQM’s continuous improvement philosophy.
- TOC Integration: After identifying and addressing a bottleneck with TOC, use Lean Six Sigma tools to optimize processes surrounding the constraint and sustain improvements.
- Agile Integration: Incorporate Agile’s iterative approach into Lean Six Sigma projects to improve responsiveness and adapt to rapidly changing customer demands. This is particularly useful in sectors like custom manufacturing or product development.
By understanding these alternatives and strategically integrating them with Lean Six Sigma, organizations can tailor their improvement efforts to suit specific needs, achieving greater flexibility and effectiveness in their operational strategies.
The Future of Lean Six Sigma
Emerging Trends
Integration with Industry 4.0
The advent of Industry 4.0—the fourth industrial revolution—is transforming manufacturing through the integration of digital technologies such as the Internet of Things (IoT), cyber-physical systems, cloud computing, and advanced data analytics. Lean Six Sigma is evolving to incorporate these technologies, enhancing its effectiveness in process improvement.
- Real-Time Data Collection and Analysis: IoT devices enable continuous monitoring of equipment and processes, providing real-time data that can be analyzed for immediate insights. This aligns with Six Sigma's focus on data-driven decision-making and allows for quicker identification of process variations and defects.
- Enhanced Value Stream Mapping: Digital tools facilitate more detailed and dynamic Value Stream Mapping (VSM). Interactive dashboards and simulation models help teams visualize processes more effectively, identify waste, and test improvement scenarios virtually before implementation.
- Predictive Maintenance: Industry 4.0 technologies support predictive maintenance by analyzing equipment data to foresee potential failures. This proactive approach reduces downtime and maintenance costs, aligning with Lean principles of eliminating waste and improving efficiency.
Use of AI and Machine Learning in Process Optimization
Artificial Intelligence (AI) and Machine Learning (ML) are increasingly being integrated into Lean Six Sigma methodologies to enhance process optimization.
- Automated Root Cause Analysis: AI algorithms can process vast amounts of data to identify patterns and root causes of defects more efficiently than manual analysis. This accelerates the Analyze phase of the DMAIC cycle.
- Adaptive Process Control: ML models can adjust process parameters in real-time to maintain optimal performance. For example, in a manufacturing process, ML can predict quality outcomes based on input variables and adjust settings to minimize defects.
- Enhanced Decision Support: AI-driven analytics provide deeper insights, enabling teams to make more informed decisions. Predictive analytics can forecast process outcomes, helping to prioritize improvement efforts where they will have the most significant impact.
Lean Six Sigma in a Digital Transformation Era
As organizations undergo digital transformation, Lean Six Sigma adapts to remain relevant and effective.
- Digital Tools for Collaboration: Cloud-based platforms and project management tools facilitate collaboration among cross-functional teams, even when geographically dispersed. This enhances communication and accelerates project timelines.
- Data Accessibility and Integration: Digital transformation efforts often involve integrating disparate data systems. Lean Six Sigma projects benefit from improved data accessibility, allowing for more comprehensive analysis and monitoring.
- Virtual Training and Certification: The rise of online learning platforms has made Lean Six Sigma training more accessible. Interactive modules, virtual simulations, and remote coaching enable organizations to upskill their workforce efficiently.
- Alignment with Digital Strategies: Lean Six Sigma principles support digital transformation by ensuring that new technologies are implemented effectively. The methodology helps organizations avoid digital waste—investing in technology without realizing its full potential.
Sustainability and Environmental Focus
With increasing emphasis on sustainability, Lean Six Sigma is being leveraged to meet environmental objectives alongside operational goals.
- Reducing Environmental Waste: Lean principles naturally focus on eliminating waste, which extends to environmental impacts. Projects may target reductions in energy consumption, water usage, or material waste, contributing to sustainability goals.
- Green Lean Six Sigma: This adaptation specifically integrates environmental considerations into Lean Six Sigma projects. It involves identifying and eliminating sources of environmental waste, such as emissions or hazardous materials, during the improvement process.
- Life Cycle Assessment (LCA): Incorporating LCA into Lean Six Sigma projects allows organizations to evaluate the environmental impact of a product or process throughout its entire life cycle. This comprehensive view supports more sustainable decision-making.
- Regulatory Compliance and Reputation: By systematically addressing environmental impacts, organizations can better comply with regulations and improve their corporate social responsibility profiles. This enhances brand reputation and can provide a competitive advantage.
By embracing these emerging trends, Lean Six Sigma continues to be a critical methodology for driving efficiency and quality in modern manufacturing. Its adaptability ensures that it remains relevant in the face of technological advancements and evolving business priorities, such as digital transformation and sustainability initiatives.
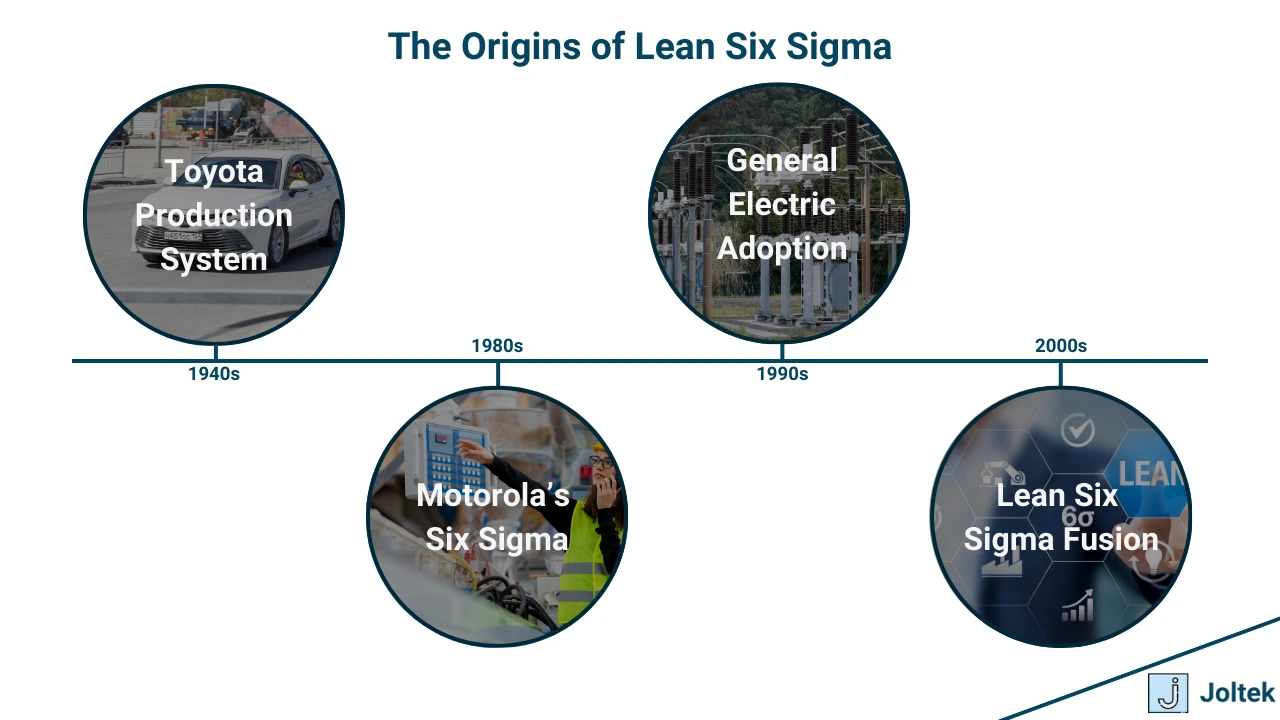
Conclusion
Recap of Key Points
Lean Six Sigma is a powerful methodology that integrates the principles of Lean (focused on eliminating waste and improving flow) and Six Sigma (focused on reducing variation and defects) to drive operational excellence in manufacturing and beyond.
- Its origins stem from two robust systems: Lean from the Toyota Production System and Six Sigma from Motorola, with their fusion creating a holistic approach to process improvement.
- The methodology relies on core principles like Value Stream Mapping, DMAIC, waste elimination, and statistical analysis to enhance efficiency, quality, and customer satisfaction.
- Successful implementation involves organizational readiness, skilled teams, and the use of proven tools like 5S, Control Charts, and SPC.
- Its real-world applications span industries such as automotive, electronics, food and beverage, and medical device manufacturing, yielding measurable improvements in cost, quality, and lead time.
- While it offers numerous advantages, such as cost savings and workforce empowerment, Lean Six Sigma also comes with challenges like cultural resistance and dependence on data accuracy.
- Alternative methodologies, including TQM, TOC, and Agile, provide additional strategies for continuous improvement and can be integrated with Lean Six Sigma for tailored solutions.
- The future of Lean Six Sigma is marked by its synergy with Industry 4.0 technologies, the use of AI and machine learning, and a growing emphasis on sustainability and environmental responsibility.
Why Lean Six Sigma Remains Relevant
Lean Six Sigma remains vital in today’s manufacturing landscape due to its adaptability and measurable impact.
- In an era of digital transformation, it complements Industry 4.0 technologies by providing a structured approach to leveraging data for process optimization.
- Its focus on customer-centric outcomes aligns with modern business priorities, where quality, speed, and value are paramount.
- The methodology’s emphasis on continuous improvement ensures that organizations can remain competitive in dynamic markets.
- As sustainability takes center stage, Lean Six Sigma’s ability to reduce waste and optimize resource use makes it a valuable tool for achieving environmental goals alongside operational objectives.
Final Thoughts and Recommendations
Lean Six Sigma is more than just a methodology—it is a mindset that fosters efficiency, innovation, and excellence. While its principles are well-established, its potential continues to grow as it integrates with emerging technologies and addresses new challenges.
For organizations considering Lean Six Sigma:
- Start by assessing organizational readiness and securing leadership commitment.
- Focus on building a skilled team with proper training and certification.
- Identify high-impact areas for improvement and apply Lean Six Sigma tools systematically.
- Be prepared to address challenges like resistance to change by fostering a culture of collaboration and data-driven decision-making.
- Stay open to integrating Lean Six Sigma with other methodologies or technologies to enhance its effectiveness.
For individuals looking to leverage Lean Six Sigma:
- Pursue certifications to deepen your understanding of its tools and methodologies.
- Gain hands-on experience by participating in or leading projects.
- Stay updated on industry trends, such as AI and sustainability, to remain at the forefront of innovation.
Lean Six Sigma’s ability to deliver tangible results while adapting to modern challenges ensures it will remain a cornerstone of operational excellence for years to come.
Appendices and Resources
Glossary of Terms
- 5S: A Lean tool for workplace organization: Sort, Set in Order, Shine, Standardize, Sustain.
- DMAIC: A structured Six Sigma process improvement methodology: Define, Measure, Analyze, Improve, Control.
- Muda, Mura, Muri: Three types of waste in Lean: non-value-added activities, unevenness, and overburden.
- Control Chart: A tool for monitoring process stability and identifying variation over time.
- Critical to Quality (CTQ): Customer-defined parameters essential to product or service quality.
- Defects Per Million Opportunities (DPMO): A Six Sigma metric for measuring defect rates.
- Kaizen: A Japanese term meaning continuous improvement through small, incremental changes.
- Value Stream Mapping (VSM): A Lean tool to visualize and optimize the flow of materials and information.
Recommended Books and Articles
- Lean Thinking: Banish Waste and Create Wealth in Your Corporation by James P. Womack and Daniel T. Jones
- The Six Sigma Handbook by Thomas Pyzdek and Paul Keller
- Gemba Kaizen: A Commonsense Approach to a Continuous Improvement Strategy by Masaaki Imai
- Lean Six Sigma for Dummies by John Morgan and Martin Brenig-Jones
- The Toyota Way: 14 Management Principles from the World's Greatest Manufacturer by Jeffrey Liker
- Industry case studies and whitepapers available on websites like ASQ.org and Lean.org.
Online Courses and Certifications
- Coursera: Lean Six Sigma certification programs offered by universities like the University of Illinois and Rutgers.
- edX: Six Sigma and Lean courses from institutions like MIT and TU Delft.
- Udemy: Affordable, self-paced Lean Six Sigma training programs.
- ASQ (American Society for Quality): Offers comprehensive certification programs, including Yellow, Green, and Black Belts.
- Lean Six Sigma Institute: Specialized Lean Six Sigma training and certification.
- IASSC (International Association for Six Sigma Certification): Globally recognized Lean Six Sigma certification.
Tools and Templates for Practitioners
- DMAIC Templates: Pre-built templates for each phase of DMAIC to ensure consistent project documentation and execution.
- Value Stream Mapping (VSM) Software: Tools like Lucidchart, Visio, or specialized Lean mapping software like iGrafx.
- Fishbone Diagram Templates: Free or paid templates for root cause analysis using Ishikawa diagrams.
- Control Chart Software: Statistical software like Minitab or JMP to create and analyze control charts.
- Kanban Boards: Digital tools like Trello or physical boards for managing workflows.
- SPC Tools: Statistical Process Control software, such as InfinityQS or ProFicient, for real-time quality monitoring.
These resources provide additional depth and actionable tools for individuals and organizations looking to adopt or expand their Lean Six Sigma practices. Whether you’re starting your journey or refining your expertise, these references will help you apply Lean Six Sigma principles effectively.