Introduction: Lean Manufacturing Consulting
Manufacturing is a complex and ever-evolving industry where inefficiencies can lead to increased costs, wasted resources, and diminished competitiveness. To stay ahead, companies must adopt strategies that improve productivity, reduce waste, and enhance overall operational efficiency. This is where Lean Manufacturing Consulting comes into play.
Lean consulting helps manufacturers streamline processes, optimize resources, and foster a culture of continuous improvement. Whether a company is looking to reduce costs, increase production efficiency, or improve product quality, a Lean consultant provides the expertise and tools necessary to achieve these goals.
What is Lean Manufacturing Consulting?
Lean Manufacturing Consulting is a specialized service that helps companies implement Lean principles to eliminate waste, improve efficiency, and maximize value for customers. It involves analyzing current operations, identifying areas of improvement, and deploying Lean methodologies tailored to a company's specific needs.
Lean consultants work closely with organizations to assess existing workflows, train employees, and implement strategies that lead to sustained operational improvements. They bring proven tools and frameworks to help companies optimize processes, minimize downtime, and create a culture of continuous improvement.
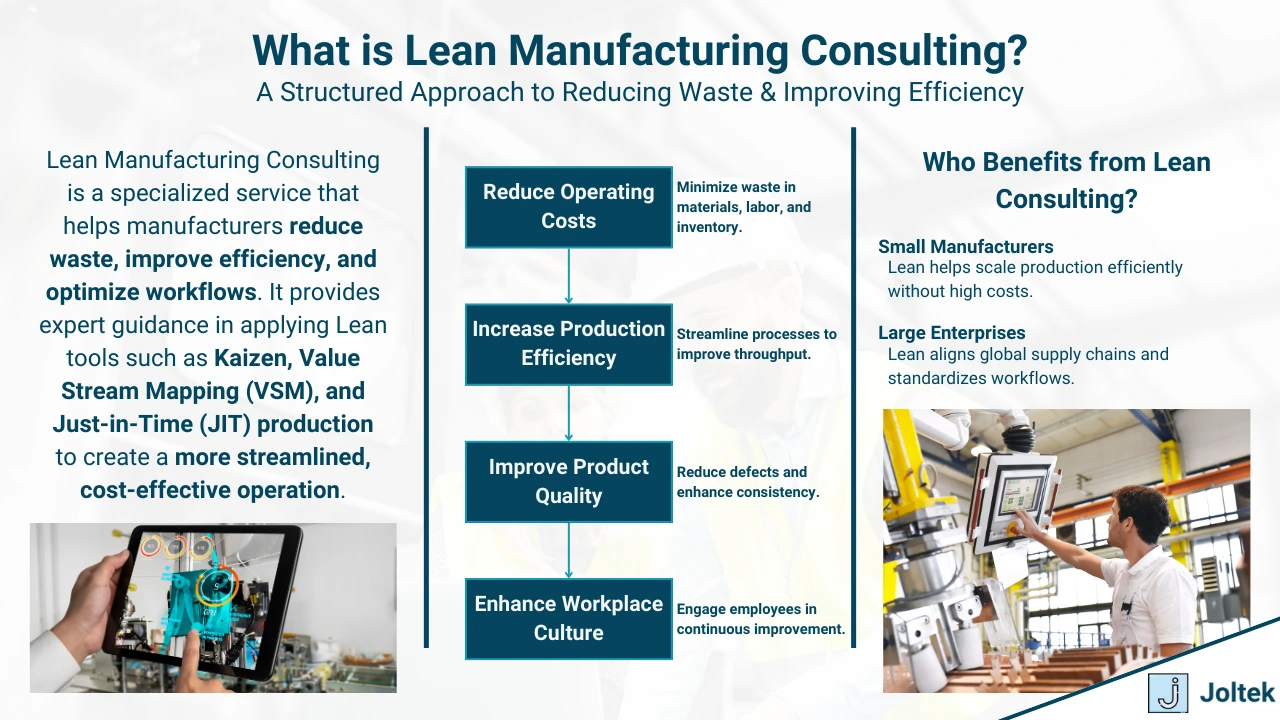
Key Functions of Lean Manufacturing Consulting:
- Identifying waste (Muda, Mura, Muri) and inefficiencies
- Developing and implementing Lean strategies
- Training employees on Lean principles and tools
- Facilitating process optimization and workflow redesign
- Establishing key performance indicators (KPIs) to track improvements
- Ensuring long-term sustainability of Lean initiatives
Why Do Manufacturers Seek Lean Consulting?
Manufacturers turn to Lean consulting for several critical reasons, including cost reduction, operational efficiency, and long-term sustainability. Here are some of the primary motivations:
1. Reducing Operational Costs
Lean consulting helps manufacturers eliminate waste, optimize resource allocation, and improve production efficiency—leading to lower operating costs. By reducing unnecessary inventory, excess motion, overproduction, and defects, companies save money while maintaining high-quality output.
2. Increasing Productivity and Efficiency
A key goal of Lean consulting is to streamline workflows and eliminate bottlenecks. By implementing Just-in-Time (JIT) production, Kanban systems, and Value Stream Mapping (VSM), manufacturers can significantly boost productivity without the need for excessive labor or capital investment.
3. Improving Product Quality and Reducing Defects
Lean methodologies emphasize error-proofing (Poka-Yoke) and continuous process improvements, leading to higher quality products. A Lean consultant can help implement Total Quality Management (TQM) practices that reduce defects and rework costs.
4. Enhancing Employee Engagement and Teamwork
A Lean culture fosters employee involvement and problem-solving. Through Kaizen (continuous improvement initiatives), Lean consultants train employees to identify inefficiencies and contribute to process improvements, making operations more effective and sustainable.
5. Accelerating Time-to-Market
By reducing unnecessary delays in production and supply chain processes, Lean consulting enables manufacturers to respond quickly to market demands and launch products faster, providing a competitive edge.
Who Benefits from Lean Consulting?
Lean consulting is valuable for both small and large manufacturers, but the impact varies based on company size, industry, and operational maturity.
1. Small and Medium-Sized Enterprises (SMEs)
For SMEs, Lean consulting provides the expertise needed to scale operations efficiently without requiring major capital investments. Key benefits include:
- Lower operating costs and improved cash flow
- Better resource utilization without excess inventory
- More agile production processes to compete with larger firms
2. Large Enterprises and Multinational Corporations
Larger manufacturers benefit from Lean consulting by aligning global operations and driving standardized efficiency improvements across multiple facilities. Key advantages include:
- Reduced operational waste and downtime across supply chains
- Standardized best practices in Lean across international sites
- Enhanced collaboration between departments and suppliers
Overview of Key Concepts in Lean Manufacturing
Lean consulting is based on five fundamental principles that guide its methodologies and strategies:
1. Value
Understanding what customers truly value and aligning production processes to deliver maximum value with minimal waste.
2. Value Stream
Mapping all steps in the production process to identify and eliminate non-value-adding activities.
3. Flow
Ensuring smooth production flow by eliminating bottlenecks and improving cycle times.
4. Pull System
Producing only what is needed, when it is needed—minimizing excess inventory and reducing lead times.
5. Perfection (Continuous Improvement)
Encouraging Kaizen (continuous improvements) to refine processes, reduce waste, and drive innovation.
Fundamentals of Lean Manufacturing
Lean manufacturing is a systematic approach to reducing waste and improving efficiency in production. Rooted in the Toyota Production System (TPS), Lean focuses on maximizing customer value while minimizing waste, creating an environment where continuous improvement drives operational excellence.
History and Origins of Lean Manufacturing
The origins of Lean manufacturing trace back to the Toyota Production System (TPS), developed in Japan during the 1940s and 1950s by Taiichi Ohno and Shigeo Shingo. The system was designed to enhance efficiency and productivity while minimizing waste (Muda, Mura, Muri).
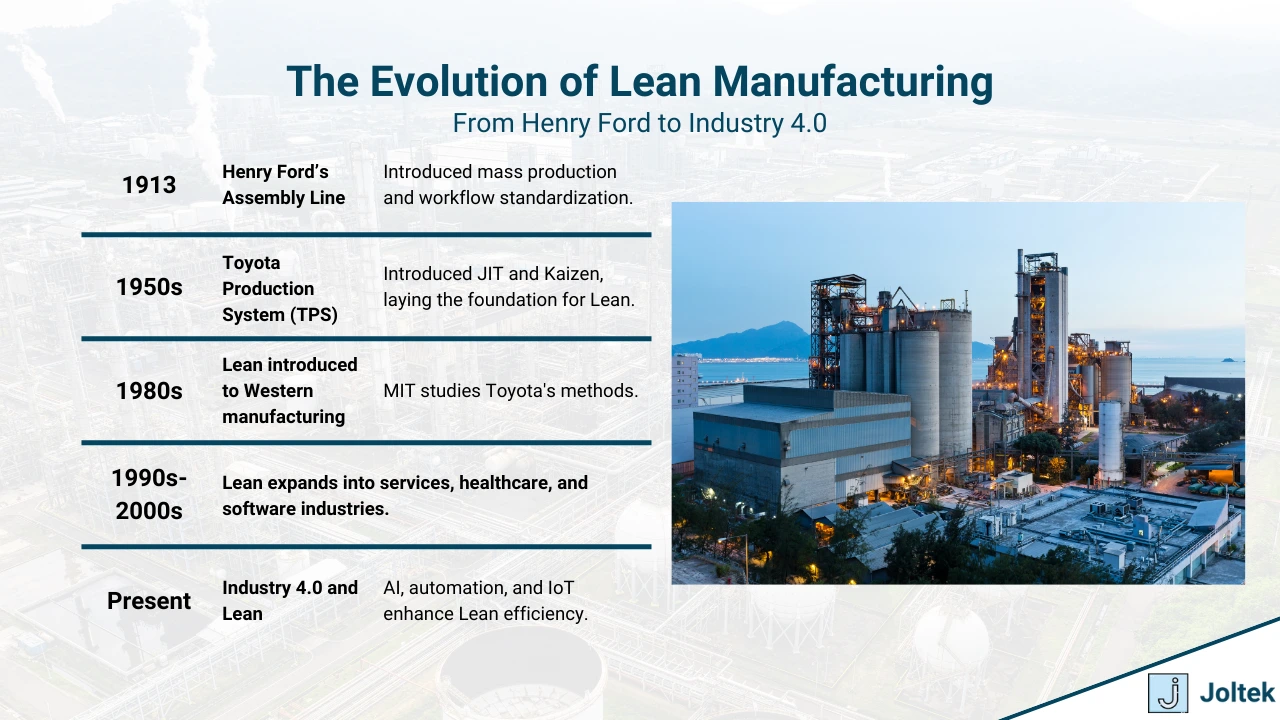
Key Milestones in Lean History:
- Early 1900s: Henry Ford introduces mass production with the assembly line, improving efficiency but lacking flexibility.
- 1950s–1970s: Toyota refines TPS, introducing concepts like Just-in-Time (JIT), Kaizen, and Kanban to enhance production flow and reduce excess inventory.
- 1980s: The term "Lean" is popularized in Western manufacturing after research conducted by MIT’s International Motor Vehicle Program (IMVP), which identifies Toyota’s methods as superior.
- 1990s–2000s: Lean principles extend beyond automotive manufacturing into various industries, including healthcare, aerospace, food processing, and software development.
Core Principles of Lean Manufacturing
Lean manufacturing operates on five fundamental principles designed to eliminate waste, optimize processes, and deliver high-value products efficiently.
1. Value
Value is defined by the customer—it is what they are willing to pay for. Manufacturers must align their processes to create maximum value while eliminating anything that does not contribute to it.
Examples of waste that does not create value:
- Overproduction (producing more than needed)
- Excess inventory
- Unnecessary transportation or motion
- Defective products requiring rework
By understanding customer value, companies can ensure that every process contributes to delivering quality, cost-effective products.
2. Value Stream
A value stream includes all activities involved in designing, producing, and delivering a product. Value Stream Mapping (VSM) is a key Lean tool used to identify and remove non-value-adding activities, ensuring a more efficient process flow.
Key steps in Value Stream Mapping:
- Identify and document all processes involved in production.
- Distinguish between value-added and non-value-added steps.
- Eliminate inefficiencies and optimize workflow.
3. Flow
The flow principle focuses on creating smooth, uninterrupted production processes by eliminating bottlenecks and unnecessary delays. A continuous flow system ensures that materials and products move efficiently through production without stops, starts, or excess handling.
How to improve flow:
- Implement Total Productive Maintenance (TPM) to reduce equipment downtime.
- Use 5S (Sort, Set in Order, Shine, Standardize, Sustain) to organize workspaces for efficiency.
- Design workstations for minimal movement and optimized ergonomics.
4. Pull System
A pull system ensures that production is based on actual demand rather than forecasts, reducing excess inventory and preventing overproduction. The Kanban system, a key Lean tool, helps manage pull-based inventory by signaling when new materials are needed.
Benefits of a pull-based system:
- Reduces waste associated with excess inventory.
- Improves responsiveness to customer demand.
- Ensures materials and products are available just-in-time (JIT) to reduce storage costs.
5. Perfection (Continuous Improvement)
Lean manufacturing is an ongoing process of refinement and optimization. The goal is to continuously eliminate waste and enhance efficiency.
Key tools for continuous improvement:
- Kaizen (Continuous Improvement): Encourages teams to make small, incremental improvements daily.
- Plan-Do-Check-Act (PDCA) Cycle: A structured approach to problem-solving and innovation.
- Gemba Walks: Leaders observe and engage with shop-floor workers to identify areas for improvement.
By fostering a culture of continuous improvement, companies can maintain long-term efficiency and competitiveness.
How Lean and Six Sigma Work Together (Lean Six Sigma)
Lean and Six Sigma are often integrated to form Lean Six Sigma (LSS), a methodology that improves both efficiency and quality by reducing waste and minimizing defects.
Example of Lean Six Sigma in action:
- Lean eliminates non-value-added steps in production.
- Six Sigma ensures consistent quality with minimal defects.
- The result: A faster, more reliable, and cost-efficient process.
Conclusion
Understanding the fundamentals of Lean manufacturing is essential for companies aiming to enhance efficiency, reduce waste, and maintain high quality. By following Lean principles—Value, Value Stream, Flow, Pull, and Continuous Improvement—manufacturers can create streamlined, customer-focused operations.
Additionally, integrating Lean with Six Sigma allows organizations to not only optimize efficiency but also ensure the highest levels of product quality, making them more competitive in today’s global marketplace.
The Role of a Lean Manufacturing Consultant
Lean Manufacturing Consultants play a critical role in helping manufacturers implement Lean principles, improve efficiency, and eliminate waste. They bring structured methodologies, industry experience, and problem-solving expertise to drive operational improvements. Whether a company is just beginning its Lean journey or looking to refine existing processes, Lean consultants provide objective insights and practical solutions to achieve measurable results.
Responsibilities and Key Areas of Expertise
A Lean consultant’s primary responsibility is to assess, design, implement, and sustain Lean strategies tailored to a manufacturer’s unique needs. Their expertise spans multiple domains within operations, production, and supply chain management.
Key Responsibilities of a Lean Manufacturing Consultant:
- Assessing Current Operations
- Conducting Value Stream Mapping (VSM) to identify inefficiencies.
- Analyzing waste (Muda, Mura, Muri) in production and supply chain.
- Reviewing metrics like cycle times, defect rates, and inventory levels.
- Developing Lean Implementation Strategies
- Creating Lean roadmaps and implementation plans.
- Recommending Just-in-Time (JIT), 5S, SMED, and other Lean methodologies.
- Aligning Lean initiatives with business goals and performance metrics.
- Training and Coaching Employees
- Conducting Kaizen workshops and Lean training sessions.
- Encouraging employee involvement in continuous improvement efforts.
- Teaching problem-solving methodologies like PDCA and DMAIC.
- Implementing Lean Tools and Processes
- Setting up Kanban systems for inventory control.
- Optimizing production workflow and reducing changeover times (SMED).
- Establishing standardized work processes and error-proofing (Poka-Yoke).
- Monitoring and Sustaining Improvements
- Implementing Key Performance Indicators (KPIs) and Lean dashboards.
- Conducting Gemba Walks to observe processes in real time.
- Establishing continuous improvement mechanisms for long-term success.
How Consultants Drive Value for Manufacturers
Lean consultants help manufacturers unlock significant value by improving efficiency, reducing costs, and enhancing product quality.
1. Cost Reduction & Waste Elimination
- Identifying and removing non-value-added activities to lower operational expenses.
- Implementing JIT production to reduce excess inventory and storage costs.
- Optimizing labor utilization through better workflows and automation.
2. Productivity & Efficiency Gains
- Improving production flow to reduce bottlenecks and downtime.
- Reducing machine setup times (SMED) for faster changeovers.
- Standardizing work procedures to increase consistency and repeatability.
3. Higher Product Quality & Fewer Defects
- Implementing error-proofing (Poka-Yoke) and Total Quality Management (TQM).
- Reducing defects and rework costs through root cause analysis (5 Whys, Fishbone Diagram).
- Enhancing supply chain alignment to ensure consistent material quality.
4. Faster Time-to-Market & Greater Flexibility
- Enabling agile production systems to respond quickly to changing demand.
- Reducing lead times by eliminating unnecessary steps in production.
- Improving coordination between engineering, production, and logistics teams.
5. Cultural Transformation & Employee Engagement
- Creating a culture of continuous improvement (Kaizen).
- Training employees to identify and solve operational inefficiencies.
- Aligning leadership and frontline workers on Lean thinking and problem-solving.
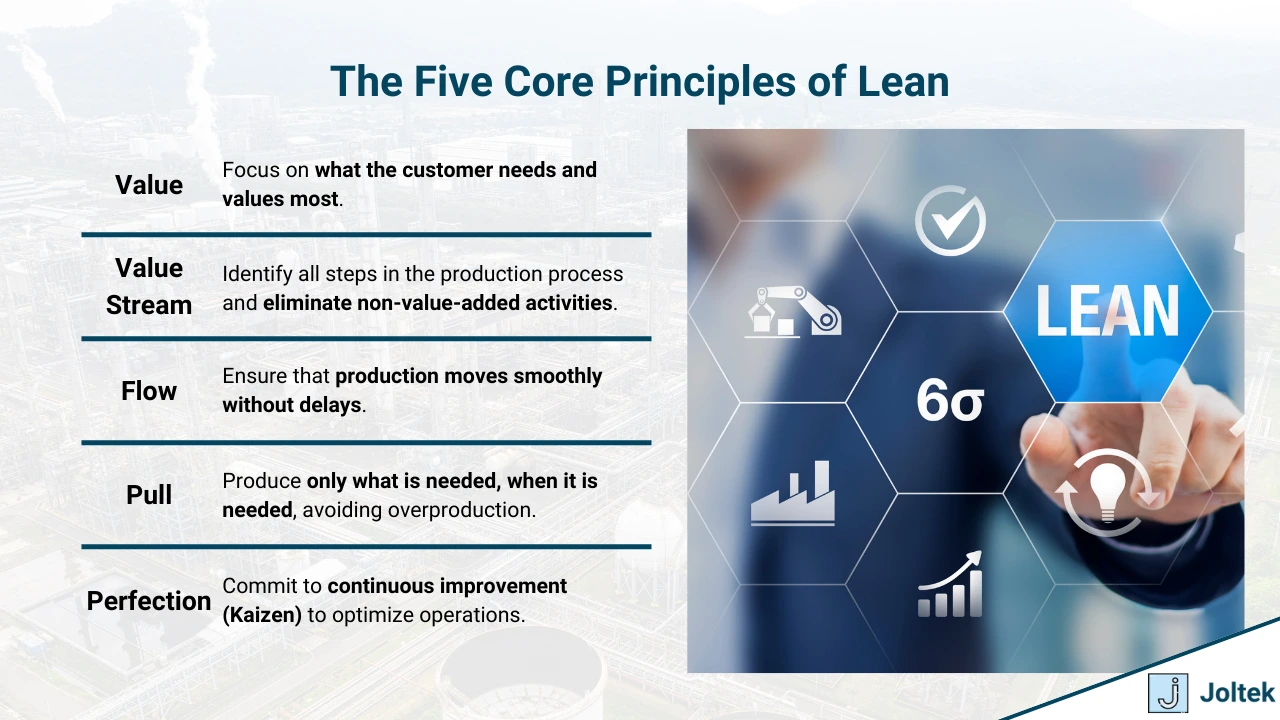
Skills and Qualifications of an Effective Lean Consultant
A successful Lean consultant must have a blend of technical expertise, leadership skills, and hands-on experience in manufacturing.
Essential Skills:
✅ Analytical & Problem-Solving Skills – Ability to analyze complex processes and identify inefficiencies.
✅ Strong Communication & Training Abilities – Capable of training employees and coaching leadership teams.
✅ Data-Driven Decision Making – Experience in using KPIs, metrics, and analytics to track improvements.
✅ Project Management Expertise – Ability to lead Lean transformation projects effectively.
✅ Adaptability & Industry Knowledge – Experience working across different manufacturing sectors.
Key Certifications & Qualifications:
- Lean Six Sigma Black Belt / Green Belt
- Certified Lean Practitioner (CLP)
- Toyota Production System (TPS) Certification
- APICS Certified in Production and Inventory Management (CPIM)
- Experience with Lean tools like Value Stream Mapping, Kanban, 5S, Kaizen, and TPM
In-House Lean Expertise vs. External Consultants: Pros and Cons
Manufacturers often debate whether to hire an external Lean consultant or develop internal Lean expertise. Each approach has its advantages and trade-offs.
✅ Pros of Hiring an External Lean Consultant
✔ Unbiased Perspective – External consultants provide objective insights without internal politics.
✔ Specialized Expertise – Consultants bring deep industry knowledge and experience.
✔ Faster Implementation – Lean transformation is accelerated with expert guidance.
✔ Access to Proven Best Practices – Consultants implement industry-tested methodologies.
❌ Cons of Hiring an External Lean Consultant
✖ Higher Initial Cost – Consulting fees can be expensive upfront.
✖ Short-Term Engagement – Consultants may not be present for long-term sustainment.
✖ Knowledge Transfer Required – Employees need proper training to maintain improvements after the consultant leaves.
✅ Pros of Developing In-House Lean Expertise
✔ Long-Term Cost Savings – No recurring consulting fees.
✔ Sustained Lean Culture – Continuous improvement is embedded in daily operations.
✔ Stronger Employee Engagement – Employees take ownership of Lean initiatives.
❌ Cons of Developing In-House Lean Expertise
✖ Slower Implementation – Without expert guidance, Lean transformations take longer.
✖ Lack of Specialized Knowledge – Internal teams may lack exposure to industry best practices.
✖ Risk of Stagnation – Without external input, Lean efforts may lose momentum over time.
Conclusion
A Lean Manufacturing Consultant plays a pivotal role in transforming manufacturing operations by driving efficiency, reducing costs, and embedding a culture of continuous improvement. While some companies may opt to build internal Lean expertise, an experienced consultant can accelerate transformation, avoid common pitfalls, and deliver faster ROI.
For manufacturers looking to optimize their processes and remain competitive, investing in Lean consulting is a strategic decision that can yield long-term benefits.
Lean Tools and Methodologies Used in Consulting
Lean consultants utilize a variety of tools and methodologies to help manufacturers identify inefficiencies, optimize workflows, and sustain continuous improvement. These tools are designed to eliminate waste, enhance productivity, and improve quality across all aspects of production and operations. Below is a breakdown of some of the most commonly used Lean tools in consulting.
1. Value Stream Mapping (VSM)
What It Is:
Value Stream Mapping (VSM) is a visual representation of all steps in a production or business process. It helps identify waste (Muda), inefficiencies, and bottlenecks that slow down production.
How It Works:
- Step 1: Map the current state (as-is) process.
- Step 2: Identify non-value-added activities.
- Step 3: Design an optimized future-state process.
- Step 4: Implement changes and track improvements.
Benefits:
✅ Reduces cycle times by eliminating unnecessary steps.
✅ Improves workflow efficiency and material movement.
✅ Enhances visibility into process bottlenecks.
2. Kaizen (Continuous Improvement)
What It Is:
Kaizen is a philosophy of continuous improvement that involves small, incremental changes to enhance productivity, quality, and efficiency.
How It Works:
- Employees actively identify inefficiencies in their daily work.
- Teams use PDCA cycles to implement and test improvements.
- Encourages collaboration between departments to refine processes.
Benefits:
✅ Creates a culture of proactive problem-solving.
✅ Reduces waste by continuously refining workflows.
✅ Encourages employee engagement in Lean initiatives.
3. 5S (Sort, Set in Order, Shine, Standardize, Sustain)
What It Is:
5S is a workplace organization method that improves safety, efficiency, and cleanliness by systematically arranging work areas.
How It Works:
- Sort: Remove unnecessary items.
- Set in Order: Organize tools and materials for easy access.
- Shine: Keep the workspace clean and well-maintained.
- Standardize: Create procedures for maintaining organization.
- Sustain: Regularly review and reinforce 5S practices.
Benefits:
✅ Improves workplace safety and organization.
✅ Reduces waste associated with searching for tools.
✅ Enhances productivity by minimizing motion and clutter.
4. Kanban (Pull-Based Inventory Control)
What It Is:
Kanban is a visual scheduling system that helps control inventory and production flow by signaling when new work or materials are needed.
How It Works:
- Uses cards, bins, or digital dashboards to signal demand.
- Workflows are managed using a pull system (products are only produced as needed).
- Helps balance supply with real-time demand.
Benefits:
✅ Prevents overproduction and excessive inventory.
✅ Reduces lead times and ensures smooth production flow.
✅ Improves responsiveness to customer demand.
5. Just-in-Time (JIT) Production
What It Is:
JIT is a production strategy that aligns manufacturing schedules with actual customer demand to reduce waste and improve efficiency.
How It Works:
- Raw materials and components are delivered only when needed.
- Production runs are optimized based on real-time demand.
- Reduces storage costs and excess inventory waste.
Benefits:
✅ Increases efficiency by eliminating excess stock.
✅ Reduces storage costs and material waste.
✅ Improves cash flow and production agility.
6. Total Productive Maintenance (TPM)
What It Is:
TPM is a proactive maintenance strategy that involves all employees in maintaining equipment to prevent breakdowns and defects.
How It Works:
- Operators perform routine maintenance to prevent failures.
- Equipment is continuously monitored using predictive maintenance techniques.
- Focuses on zero unplanned downtime and maximizing machine availability.
Benefits:
✅ Extends equipment lifespan and prevents failures.
✅ Increases production uptime and reduces delays.
✅ Improves overall equipment effectiveness (OEE).
7. Gemba Walks
What It Is:
A Gemba Walk involves leaders and managers visiting the production floor to observe real-time operations and engage with employees.
How It Works:
- Managers visit the "Gemba" (the real place) where work happens.
- They ask questions, observe processes, and gather insights.
- Issues are identified and addressed directly with employees.
Benefits:
✅ Enhances leadership engagement in Lean initiatives.
✅ Identifies hidden inefficiencies and improvement areas.
✅ Encourages collaboration between leadership and frontline workers.
8. Standard Work & Work Instructions
What It Is:
Standard Work is a documented set of best practices that ensures tasks are performed consistently, efficiently, and with high quality.
How It Works:
- Processes are analyzed and optimized for efficiency.
- Work instructions are documented and trained across teams.
- Employees follow standardized procedures to minimize variation.
Benefits:
✅ Improves consistency in production quality.
✅ Reduces training time for new employees.
✅ Ensures repeatable and predictable workflows.
9. PDCA (Plan-Do-Check-Act) Cycle
What It Is:
The PDCA cycle is a structured approach to problem-solving and continuous improvement.
How It Works:
- Plan: Identify problems and create an improvement strategy.
- Do: Implement the proposed changes.
- Check: Measure the results and evaluate effectiveness.
- Act: Adjust processes based on findings and standardize improvements.
Benefits:
✅ Ensures systematic problem-solving and innovation.
✅ Helps organizations track and measure improvements.
✅ Provides a repeatable framework for continuous improvement.
10. Poka-Yoke (Error Proofing)
What It Is:
Poka-Yoke is a mistake-proofing technique designed to prevent defects and errors in manufacturing processes.
How It Works:
- Uses sensors, alarms, or process design to detect and prevent mistakes.
- Ensures critical steps cannot be skipped or performed incorrectly.
- Reduces human errors and costly defects.
Benefits:
✅ Increases first-pass yield and reduces defects.
✅ Minimizes costly rework and scrap.
✅ Enhances product quality and reliability.
11. SMED (Single-Minute Exchange of Die) for Quick Changeovers
What It Is:
SMED is a Lean methodology for reducing changeover times in production, ensuring faster transitions between manufacturing runs.
How It Works:
- Separates internal vs. external setup tasks to minimize downtime.
- Uses quick-change tools and fixtures to speed up transitions.
- Standardizes changeover processes for repeatability.
Benefits:
✅ Reduces machine downtime and increases productivity.
✅ Improves flexibility for small-batch production.
✅ Lowers inventory by enabling just-in-time scheduling.
Conclusion
Lean consultants apply a variety of tools to streamline operations, reduce waste, and improve efficiency. Whether it’s Kaizen for continuous improvement, Kanban for inventory control, or SMED for quick changeovers, these methodologies enable sustainable operational excellence.
By integrating these tools into their processes, manufacturers can achieve cost savings, higher quality, and greater agility in production.
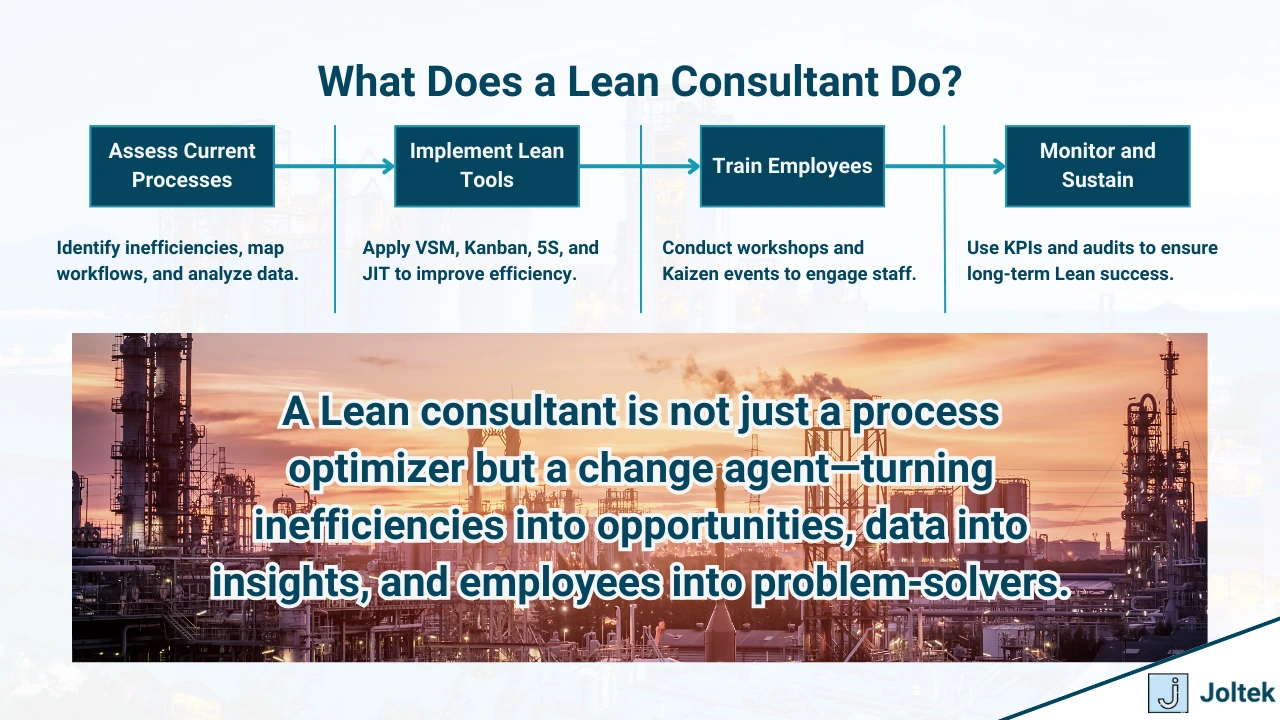
The Lean Manufacturing Consulting Process
Lean manufacturing consulting follows a structured approach to transforming manufacturing operations, eliminating waste, and improving efficiency. This process ensures that Lean principles are successfully integrated into an organization while aligning with business objectives. The consulting process is typically divided into four key steps:
- Initial Assessment & Diagnosis
- Strategy Development
- Implementation
- Monitoring & Continuous Improvement
Each phase plays a crucial role in achieving operational excellence and fostering a culture of continuous improvement.
Step 1: Initial Assessment & Diagnosis
The first phase of Lean consulting focuses on evaluating the current state of operations to identify inefficiencies, process bottlenecks, and areas for improvement. A thorough assessment provides a baseline understanding of the organization’s existing challenges and helps in formulating an effective Lean strategy.
Identifying Waste (Muda, Mura, Muri)
A key component of the assessment phase is identifying different types of waste that hinder efficiency. Waste in Lean manufacturing is categorized into three major types:
- Muda (Non-Value-Added Waste) refers to activities that do not add value to the customer. Common examples include excess inventory, unnecessary movement of materials, waiting times between production steps, and overproduction. Eliminating muda is one of the primary goals of Lean implementation.
- Mura (Unevenness) occurs when production is inconsistent, causing fluctuations in workflow. Uneven workloads result in inefficiencies, delays, and increased costs. A Lean consultant helps organizations balance production demand to avoid such fluctuations.
- Muri (Overburden) relates to excessive strain placed on employees or machines, often due to unrealistic production schedules, improper workload distribution, or inefficient processes. Overburdened systems lead to employee fatigue, increased maintenance costs, and a higher likelihood of equipment failures.
Assessing Current Processes and Performance
A Lean consultant evaluates production workflows, quality control measures, equipment effectiveness, and labor efficiency to determine areas where improvements can be made. This assessment includes an analysis of key performance indicators such as cycle time, defect rates, lead times, and inventory levels. By mapping current processes, the consultant gains insights into inefficiencies that affect productivity and overall operational performance.
Data Collection and Gap Analysis
Data-driven decision-making is a core aspect of Lean consulting. Consultants gather and analyze production data, customer demand patterns, and operational metrics to measure the gap between the organization’s current performance and its desired future state. This analysis provides a clear foundation for identifying key improvement opportunities and designing an effective Lean strategy.
Step 2: Strategy Development
Once the assessment phase is complete, the next step is to develop a structured Lean implementation strategy. This phase focuses on defining objectives, selecting the appropriate Lean methodologies, and creating an actionable roadmap.
Defining Lean Objectives and KPIs
An effective Lean strategy begins with clear, measurable objectives that align with the company’s business goals. These objectives might include reducing production lead times, minimizing waste, increasing first-pass yield, or improving equipment effectiveness. Key performance indicators (KPIs) are established to track progress, such as defect rates, production cycle times, inventory turnover, and on-time delivery performance.
Creating an Implementation Roadmap
A Lean roadmap provides a step-by-step plan for executing the strategy without disrupting ongoing operations. It outlines the sequence of Lean tool deployment, assigns responsibilities to key stakeholders, and sets a timeline for achieving specific milestones. A well-structured roadmap ensures that the transition to Lean manufacturing is managed efficiently and effectively.
Step 3: Implementation
The implementation phase is where Lean principles are actively applied across the organization. This step involves training employees, deploying Lean tools, and making process improvements to enhance operational efficiency.
Training and Workshops for Employees
For Lean to be successful, employees must understand the fundamental principles and methodologies involved. Consultants conduct training sessions and workshops to educate employees on Lean concepts, such as waste reduction, standardized work procedures, and continuous improvement practices. These sessions also focus on fostering a Lean mindset that encourages problem-solving and proactive engagement with process improvements.
Applying Lean Tools and Methodologies
During implementation, a variety of Lean tools are introduced to optimize processes. The specific methodologies used will depend on the organization’s needs but often include:
- 5S Workplace Organization to improve efficiency and reduce clutter in workspaces.
- Kanban and Pull Systems to streamline inventory management and reduce excess stock.
- Just-in-Time (JIT) Production to synchronize manufacturing with actual customer demand.
- Poka-Yoke (Error Proofing) techniques to minimize defects and improve product quality.
- SMED (Single-Minute Exchange of Die) to reduce machine setup and changeover times.
These tools help manufacturers achieve a more agile and efficient production system that minimizes waste and enhances overall productivity.
Process Re-Engineering and Optimization
In addition to introducing Lean tools, process re-engineering focuses on redesigning workflows to eliminate bottlenecks and inefficiencies. Consultants work closely with production teams to implement workflow improvements that enhance throughput, reduce downtime, and improve overall process reliability. This step may also involve equipment optimization, better scheduling techniques, and improvements in workplace ergonomics.
Step 4: Monitoring & Continuous Improvement
The final phase of Lean consulting ensures that the improvements made during implementation are sustained and continuously refined over time. This involves tracking performance, gathering feedback, and fostering a culture of continuous improvement.
Performance Tracking and Metrics
Real-time data tracking and reporting systems are used to monitor key performance indicators established during the strategy development phase. Metrics such as production efficiency, defect rates, and downtime are analyzed regularly to ensure that Lean improvements are delivering measurable results.
Feedback Loops and Iterative Improvements
Continuous improvement is a core principle of Lean manufacturing. Lean consultants establish mechanisms for ongoing process refinement through structured feedback loops. The PDCA (Plan-Do-Check-Act) cycle is commonly used to ensure that improvements are continually evaluated and adjusted based on performance data. Kaizen events and cross-functional collaboration sessions are also conducted to identify further opportunities for optimization.
Cultural Shift Towards Continuous Improvement
For Lean to have a lasting impact, it must become embedded in the company’s culture. Consultants work with leadership teams to develop internal Lean champions who can sustain momentum and drive ongoing improvements. Training programs, regular Lean assessments, and employee engagement initiatives help reinforce a continuous improvement mindset throughout the organization.
Conclusion
The Lean Manufacturing Consulting Process is a structured journey toward operational excellence. By following a systematic approach that includes assessment, strategy development, implementation, and continuous improvement, manufacturers can achieve sustainable efficiency gains and cost reductions. The key to success lies in aligning Lean initiatives with business objectives, engaging employees in problem-solving, and maintaining a culture of continuous improvement.
Implementing Lean is not a one-time effort but an ongoing transformation that requires commitment at all levels of the organization. Companies that embrace Lean principles as part of their long-term operational strategy will be better positioned to compete in an increasingly dynamic and demanding manufacturing landscape.
Common Challenges in Lean Transformation
While Lean manufacturing offers significant benefits, its successful implementation is not without challenges. Many organizations struggle to sustain Lean improvements due to factors such as resistance to change, lack of leadership commitment, and poor alignment with business objectives. Understanding these challenges can help companies proactively address them and ensure a smooth Lean transformation.
Resistance to Change from Employees and Management
One of the most significant obstacles in Lean transformation is resistance to change from both employees and management. Lean requires a shift in mindset, work habits, and company culture, which can be met with skepticism and reluctance.
Employees may resist Lean initiatives due to:
- Fear of job loss or increased workload.
- Uncertainty about new processes and performance expectations.
- Skepticism about whether Lean will bring meaningful improvements.
Management may be hesitant to fully embrace Lean due to:
- Concerns about initial disruptions to production schedules.
- A belief that existing processes are "good enough".
- A lack of understanding of Lean principles and long-term benefits.
To overcome resistance, organizations must communicate the benefits of Lean clearly, involve employees in decision-making, and provide proper training. Leadership must set the example by demonstrating their commitment to Lean initiatives.
Lack of Leadership Support and Commitment
A successful Lean transformation depends on strong leadership support. Without active engagement from senior executives and managers, Lean initiatives often fail to gain momentum or are abandoned prematurely.
Common leadership challenges in Lean transformation include:
- Viewing Lean as a short-term cost-cutting exercise rather than a long-term strategy.
- Failure to allocate sufficient resources, such as training programs and Lean specialists.
- Lack of accountability in sustaining Lean initiatives after initial improvements.
To drive Lean success, leadership must:
- Align Lean with the company’s strategic objectives.
- Lead by example, actively participating in Lean initiatives.
- Provide ongoing coaching, training, and reinforcement to employees.
Without leadership commitment, Lean often becomes a disconnected set of improvement projects rather than a transformational way of operating.
Poor Data Collection and Measurement Systems
Lean relies heavily on data-driven decision-making, but many organizations struggle with inadequate data collection and tracking systems. Without accurate data, it is difficult to measure progress, identify areas for improvement, and sustain Lean initiatives.
Common data-related issues include:
- Lack of real-time visibility into production performance.
- Inconsistent tracking of key performance indicators (KPIs) such as cycle times, defect rates, and inventory levels.
- Relying on outdated or manual data collection methods that lead to errors and inefficiencies.
To address these challenges, organizations must:
- Implement robust data collection systems that provide real-time insights.
- Use digital dashboards and analytics tools to track Lean performance.
- Train employees on proper data entry and interpretation to ensure accuracy.
Reliable data collection is essential for evaluating Lean progress and making informed decisions to sustain improvements.
Misalignment Between Lean Goals and Business Objectives
For Lean transformation to be successful, it must be aligned with the broader business strategy and financial objectives. However, many companies implement Lean initiatives without clearly linking them to key business goals, leading to frustration and lack of direction.
Common misalignment issues include:
- Focusing only on cost reduction instead of long-term value creation.
- Implementing Lean in isolated departments without company-wide integration.
- Neglecting customer needs by prioritizing efficiency over product quality.
To avoid these pitfalls, companies must:
- Ensure that Lean initiatives support overall business priorities, such as profitability, customer satisfaction, and innovation.
- Establish clear KPIs that measure both operational improvements and financial impact.
- Involve cross-functional teams to integrate Lean principles across all departments.
When Lean is properly aligned with business objectives, it delivers sustainable competitive advantages rather than short-term efficiency gains.
Overcomplication of Lean Implementation
Lean is based on simple, practical principles, yet many organizations make the mistake of overcomplicating the implementation process. Complex Lean programs can overwhelm employees, create confusion, and slow down progress.
Common causes of overcomplication include:
- Implementing too many Lean tools at once without prioritizing based on business needs.
- Creating excessive documentation and procedures that hinder agility.
- Focusing on theoretical Lean concepts rather than practical application.
To keep Lean implementation manageable and effective, companies should:
- Start with high-impact, easy-to-implement Lean tools, such as 5S, Value Stream Mapping, and Standard Work.
- Focus on solving specific operational problems rather than applying Lean as a rigid framework.
- Use a phased approach, scaling Lean initiatives gradually to ensure long-term adoption.
A simpler, well-structured Lean transformation is more likely to succeed than a complex, overengineered one.
Sustainability: Preventing Lean Initiatives from Fading Over Time
One of the biggest challenges in Lean transformation is sustaining improvements beyond the initial implementation phase. Many companies experience early success with Lean but struggle to maintain momentum, leading to regression back to old habits.
Factors that contribute to Lean initiatives fading over time include:
- Lack of ongoing training and reinforcement, leading to employees reverting to previous practices.
- Failure to integrate Lean into daily routines, treating it as a one-time project rather than a continuous effort.
- Loss of executive focus, where leadership shifts attention to other priorities once short-term results are achieved.
To ensure long-term sustainability, organizations should:
- Embed Lean principles into the company’s culture through continuous education and engagement.
- Establish Lean leadership roles responsible for maintaining improvement initiatives.
- Conduct regular performance reviews and Lean audits to track progress and make necessary adjustments.
- Encourage a bottom-up Lean culture, where employees at all levels are actively involved in identifying and solving inefficiencies.
Lean is not a destination but an ongoing journey. Companies that treat Lean as a continuous improvement mindset rather than a temporary initiative are more likely to sustain long-term benefits.
Conclusion
Implementing Lean manufacturing is a complex transformation that requires careful planning, strong leadership, and a commitment to continuous improvement. Resistance to change, lack of leadership support, poor data collection, and misalignment with business goals are common challenges that can hinder Lean success. Additionally, overcomplicating Lean implementation and failing to sustain improvements over time can cause Lean initiatives to lose effectiveness.
To overcome these challenges, companies must take a pragmatic and structured approach, ensuring that Lean is properly integrated into their business strategy. Strong leadership engagement, employee involvement, effective data systems, and a commitment to ongoing improvement are key factors in driving a successful and sustainable Lean transformation. Organizations that proactively address these challenges will be better positioned to achieve long-term operational excellence and competitiveness in the manufacturing industry.
Case Studies & Success Stories in Lean Consulting
Lean manufacturing has been successfully implemented across various industries, helping companies reduce waste, improve efficiency, and enhance product quality. The following case studies highlight real-world examples of Lean consulting success, demonstrating how manufacturers have leveraged Lean principles to achieve significant operational and financial improvements.
Toyota: The Birthplace of Lean and a Continuous Improvement Benchmark
Toyota is widely regarded as the pioneer of Lean manufacturing, having developed the Toyota Production System (TPS) that later became the foundation for modern Lean methodologies. Toyota’s success with Lean principles has been instrumental in making it one of the most efficient and profitable automotive manufacturers in the world.
The company implemented Just-in-Time (JIT) production to minimize inventory and reduce lead times, while also fostering a culture of continuous improvement through Kaizen initiatives. The introduction of Kanban systems helped manage workflow and inventory more efficiently, ensuring that materials were supplied only as needed.
As a result, Toyota reduced production lead times by 50%, significantly cut inventory costs, and achieved a consistently high level of vehicle quality. The key lesson from Toyota’s success is that embedding a culture of continuous improvement and employee involvement is crucial for sustaining Lean transformation over time.
General Electric (GE) and Lean Six Sigma: Driving Productivity Across Industries
General Electric (GE) successfully combined Lean and Six Sigma methodologies to drive operational efficiency and cost reduction. Under the leadership of Jack Welch, GE implemented Lean Six Sigma across its global operations, using a data-driven approach to reduce defects and improve efficiency.
The company optimized manufacturing processes by standardizing work instructions, applying Value Stream Mapping (VSM) to eliminate inefficiencies, and using Six Sigma’s DMAIC (Define, Measure, Analyze, Improve, Control) framework to enhance quality control.
These initiatives resulted in an operational cost reduction of $12 billion over five years, a 60% decrease in product defect rates, and a 30-40% improvement in lead times. The key takeaway from GE’s success is that combining Lean with Six Sigma provides a structured, data-driven approach to process optimization.
Boeing: Reducing Waste and Streamlining Aerospace Production
Boeing, one of the world’s largest aerospace manufacturers, faced significant production inefficiencies and delays in aircraft assembly. By implementing Lean manufacturing principles, the company was able to reduce waste, improve productivity, and streamline assembly processes.
Boeing applied the 5S methodology to improve workplace organization, used SMED (Single-Minute Exchange of Die) techniques to reduce changeover times, and implemented Total Productive Maintenance (TPM) to enhance equipment reliability.
These changes resulted in a 37% reduction in aircraft assembly time, a 50% reduction in manufacturing waste, and a 20% improvement in labor efficiency. Boeing’s experience demonstrates that Lean is highly effective in complex, large-scale manufacturing environments where process efficiency is critical to profitability.
Nike: Lean in the Apparel and Footwear Industry
Nike faced challenges related to long production lead times, excess inventory, and labor inefficiencies in its global supply chain. By adopting Lean manufacturing, the company transformed its operations and improved responsiveness to market demand.
Nike shifted from batch production to flow manufacturing, which significantly reduced waste. The company also introduced Kanban systems to synchronize supply with real-time demand and optimized supply chain processes through Lean supplier collaboration strategies.
As a result, Nike reduced lead times by 40%, increased factory productivity by 20%, and cut material waste by over 30%. The key takeaway is that Lean is not limited to traditional manufacturing but can also drive supply chain efficiency and sustainability improvements.
Intel: Lean Transformation in Semiconductor Manufacturing
Intel, a leading semiconductor manufacturer, faced high production costs and inefficiencies in wafer fabrication. By implementing Lean, Intel optimized its production processes, improved yield rates, and increased profitability.
Intel restructured its manufacturing layout to minimize movement and enhance efficiency, applied Poka-Yoke (error-proofing) techniques to reduce defects, and adopted Just-in-Time (JIT) inventory management to lower material costs.
These initiatives led to a 25% reduction in manufacturing cycle times, a 15% improvement in first-pass yield, and a significant increase in profit margins through optimized resource utilization. Intel’s case shows that Lean principles can be effectively applied in precision-driven, high-tech industries where process consistency and waste reduction are essential.
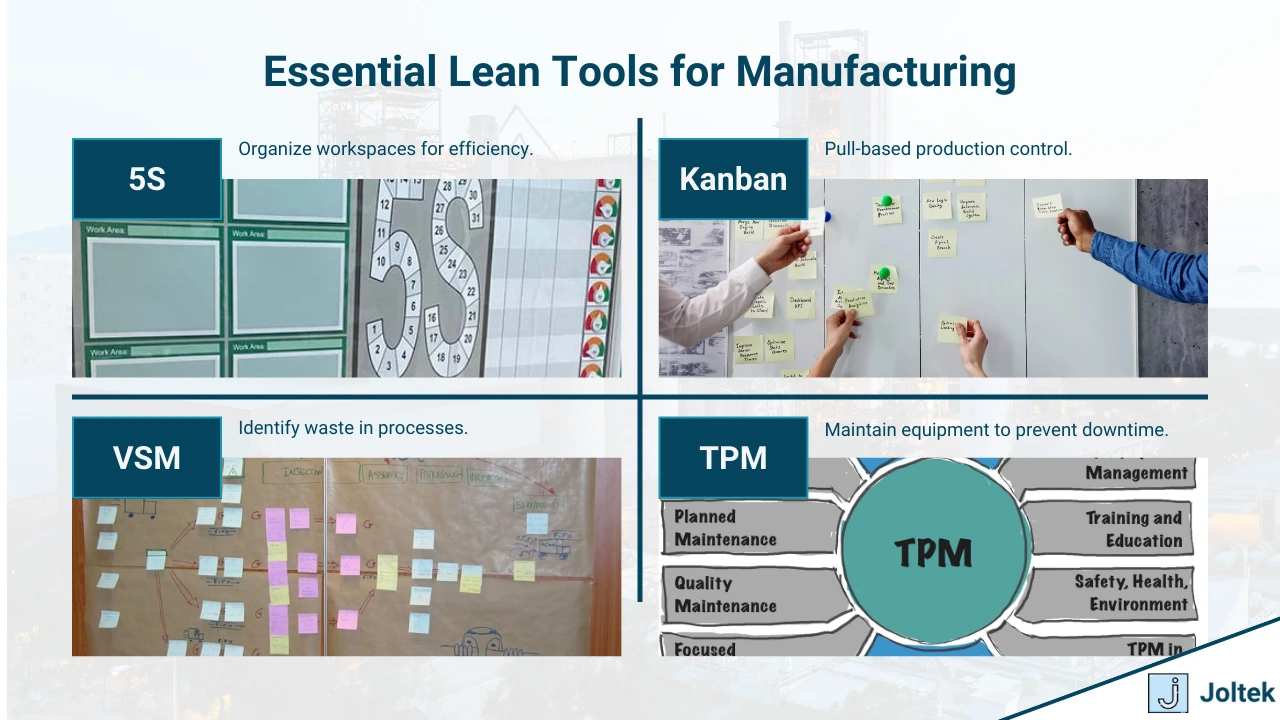
Key Takeaways from Successful Lean Transformations
Lean consulting has proven to be highly effective across multiple industries, with several common themes emerging from successful implementations. First, Lean is applicable beyond manufacturing, with companies like Nike using Lean principles to improve supply chain efficiency. Second, leadership commitment is essential, as seen in Toyota and GE, where executives played an active role in Lean transformations.
Another critical takeaway is the importance of data-driven decision-making. Organizations that integrated Lean with real-time data collection and analytics, such as GE and Intel, saw greater success in reducing waste and improving efficiency. Additionally, employee engagement and continuous improvement (Kaizen) are key to sustaining Lean initiatives, as demonstrated by Toyota’s long-term success.
Finally, the combination of Lean and digital transformation has proven to be a powerful strategy. Companies that leveraged automation, AI, and real-time monitoring systems in their Lean journey achieved even greater efficiency and quality improvements.
Conclusion
The case studies of Toyota, GE, Boeing, Nike, and Intel illustrate how Lean consulting can drive significant improvements in efficiency, cost reduction, and product quality. These success stories highlight the importance of strong leadership, data-driven decision-making, and employee engagement in ensuring sustainable Lean transformation.
While Lean implementation presents challenges, companies that commit to a structured, continuous improvement approach can achieve long-term operational excellence. By learning from the successes of global industry leaders, manufacturers can apply Lean principles effectively and drive measurable improvements in their own operations.
Lean Consulting for Different Industries
Lean principles are widely applicable across various industries, each with its own unique challenges and operational demands. While the core goal remains the same—reducing waste, improving efficiency, and enhancing value delivery—Lean consulting is tailored to meet industry-specific needs. Below is an overview of how Lean is applied in key industries, along with the benefits and best practices for each sector.
Lean in Automotive Manufacturing
The automotive industry is the birthplace of Lean manufacturing, with Toyota pioneering the Toyota Production System (TPS). Lean consulting in this sector focuses on process efficiency, waste elimination, and just-in-time production to maintain cost-effectiveness and high-quality standards.
Key Lean Applications:
- Just-in-Time (JIT) Production: Ensures parts and components arrive exactly when needed, reducing inventory costs.
- Kanban Systems: Helps manage production flow and supplier coordination.
- Total Productive Maintenance (TPM): Minimizes equipment downtime and extends asset lifespan.
- Standard Work & Process Optimization: Enhances consistency and reduces variation in production processes.
Benefits:
- Reduction in production lead times, improving overall efficiency.
- Lower operational costs by eliminating excess inventory and overproduction.
- Enhanced product quality through standardized work and error-proofing techniques.
Lean in Food & Beverage
The food and beverage industry presents unique challenges such as perishable inventory, strict regulatory compliance, and demand fluctuations. Lean consulting helps streamline operations while maintaining high levels of safety and quality.
Key Lean Applications:
- Value Stream Mapping (VSM): Identifies inefficiencies in raw material procurement, processing, and distribution.
- 5S Workplace Organization: Improves hygiene and workflow efficiency in production areas.
- Quick Changeovers (SMED): Reduces equipment downtime between different product runs.
- Poka-Yoke (Error Proofing): Prevents contamination and production errors.
Benefits:
- Reduced food waste and optimized raw material usage.
- Increased production flexibility to respond to changing consumer preferences.
- Enhanced compliance with food safety regulations through standardized processes.
Lean in Pharmaceuticals & Medical Devices
The pharmaceutical and medical device industries are heavily regulated, requiring strict adherence to quality standards, traceability, and process control. Lean consulting focuses on reducing process inefficiencies while maintaining compliance with regulatory bodies like the FDA and ISO.
Key Lean Applications:
- Standard Work & SOP Development: Ensures compliance with Good Manufacturing Practices (GMP).
- Kanban & JIT Inventory Management: Reduces excess stock while ensuring critical materials are always available.
- Six Sigma Integration: Improves process control and minimizes defects in drug and device production.
- Gemba Walks & Root Cause Analysis: Helps identify inefficiencies and enhance production reliability.
Benefits:
- Improved quality control and reduction in defects.
- Faster product development cycles and streamlined regulatory approval processes.
- Increased production capacity without compromising safety or compliance.
Lean in Aerospace & Defense
The aerospace and defense industry requires high precision, long production cycles, and stringent quality controls. Lean consulting helps optimize supply chains, reduce manufacturing lead times, and improve product quality.
Key Lean Applications:
- Value Stream Mapping (VSM): Identifies bottlenecks in complex aerospace manufacturing processes.
- Total Productive Maintenance (TPM): Increases uptime of high-cost machinery.
- Error Proofing (Poka-Yoke): Reduces rework and ensures defect-free components.
- Standardized Work & Digital Work Instructions: Ensures compliance with defense and aerospace standards.
Benefits:
- Shorter production cycles, improving delivery timelines.
- Increased efficiency and reduced manufacturing costs for high-precision components.
- Improved regulatory compliance through process standardization.
Lean in Consumer Goods & Packaging
Consumer goods and packaging manufacturers must balance high-volume production with fast-changing market demands. Lean consulting in this sector focuses on flexibility, cost reduction, and production agility.
Key Lean Applications:
- Quick Changeovers (SMED): Enables manufacturers to switch between product variants efficiently.
- Just-in-Time (JIT) Production: Reduces excess inventory while ensuring availability of high-demand items.
- 5S & Visual Management: Enhances workflow organization and production floor efficiency.
- Automation & Lean Integration: Implements robotics and digital tools to streamline repetitive tasks.
Benefits:
- Increased responsiveness to consumer trends and product customization needs.
- Lower inventory costs and minimized stock obsolescence.
- Improved production consistency and higher throughput.
Lean in Supply Chain & Logistics
Lean consulting in supply chain and logistics focuses on reducing lead times, improving transportation efficiency, and eliminating waste across distribution networks. This ensures that goods move through the supply chain in the most cost-effective and timely manner.
Key Lean Applications:
- Kanban for Demand-Driven Supply Chains: Reduces overstock and prevents shortages.
- Cross-Docking Strategies: Minimizes storage time and accelerates order fulfillment.
- Lean Route Optimization: Uses data analytics to minimize transportation inefficiencies.
- Digital Supply Chain Visibility: Leverages real-time tracking and AI-driven demand forecasting.
Benefits:
- Reduced transportation and warehousing costs.
- Improved order accuracy and faster delivery times.
- Enhanced supply chain resilience and agility in responding to demand fluctuations.
Lean in Warehousing & Distribution
Warehousing and distribution facilities play a crucial role in ensuring smooth product flow from manufacturers to customers. Lean consulting helps optimize warehouse layouts, inventory management, and fulfillment speed.
Key Lean Applications:
- 5S for Warehouse Organization: Enhances picking efficiency and minimizes retrieval times.
- Kanban & Pull-Based Inventory Systems: Ensures replenishment based on real demand.
- Automated Storage & Retrieval Systems (AS/RS): Reduces manual handling and improves order accuracy.
- Cycle Counting & Continuous Inventory Audits: Prevents stock discrepancies and improves inventory control.
Benefits:
- Faster order processing and reduced picking errors.
- Lower warehousing costs due to optimized space utilization.
- Improved inventory accuracy and stock availability.
Conclusion
Lean principles are widely applicable across industries, each requiring customized strategies to meet specific operational challenges. In automotive and aerospace, Lean focuses on process efficiency and quality control, while in food and pharmaceuticals, it ensures compliance and waste reduction. Consumer goods manufacturers benefit from agility and responsiveness, while supply chain and warehousing operations use Lean to streamline logistics and improve inventory management.
By leveraging Lean consulting tailored to their industry, organizations can achieve cost savings, reduce lead times, and enhance overall operational performance. Lean is not just a set of tools but a strategic approach to continuous improvement, driving long-term competitiveness and sustainability across all sectors.
The Business Impact of Lean Consulting
Lean consulting delivers significant financial, operational, and cultural benefits to organizations that adopt its principles. By eliminating waste, improving efficiency, and fostering a culture of continuous improvement, companies can achieve measurable improvements in profitability, production speed, quality, and employee engagement. This section explores the key business impacts of Lean consulting and how organizations can quantify their return on investment (ROI).
Cost Reduction and Increased Profitability
One of the primary reasons companies invest in Lean consulting is to reduce operating costs and improve profitability. By streamlining production processes, eliminating waste, and optimizing resource allocation, Lean helps manufacturers achieve higher financial efficiency.
Key cost-saving benefits include:
- Lower inventory carrying costs through Just-in-Time (JIT) production, which reduces excess stock.
- Reduced labor costs by eliminating non-value-added activities and improving productivity.
- Minimized production waste by identifying defects and inefficiencies in the manufacturing process.
- Energy and resource efficiency improvements that lower utility and raw material expenses.
Many companies experience cost reductions of 20-40% after Lean implementation, significantly increasing profit margins and financial stability.
Reduction in Lead Times and Increased Throughput
Lean methodologies are designed to improve production flow and eliminate bottlenecks, allowing companies to increase throughput and reduce lead times. Faster production cycles lead to quicker order fulfillment, improved customer satisfaction, and greater capacity utilization.
Key Lean strategies that improve lead times include:
- Value Stream Mapping (VSM) to identify and remove process inefficiencies.
- Kanban and Pull Systems to synchronize production with demand, reducing idle time.
- SMED (Single-Minute Exchange of Die) to cut equipment changeover times and enhance production flexibility.
- Total Productive Maintenance (TPM) to reduce unplanned downtime and improve equipment reliability.
Companies that implement Lean often achieve lead time reductions of 30-50%, allowing them to respond faster to customer demands while lowering work-in-progress inventory.
Improved Product Quality and Defect Reduction
Lean consulting helps organizations reduce defects, improve consistency, and enhance overall product quality. By applying error-proofing techniques, standardized work processes, and continuous improvement methodologies, companies can minimize production defects and costly rework.
Key Lean practices that improve quality include:
- Poka-Yoke (Error Proofing): Reduces human errors in assembly and manufacturing.
- Six Sigma Integration: Helps identify and eliminate process variation.
- Standardized Work Instructions: Ensures repeatable and consistent production outcomes.
- Root Cause Analysis (5 Whys, Fishbone Diagrams): Identifies and prevents recurring defects.
Companies that adopt Lean consulting often see defect reductions of 25-60%, leading to lower warranty costs, higher customer satisfaction, and improved brand reputation.
Enhanced Employee Engagement and Workplace Culture
Lean is not just about process improvement—it also fosters a collaborative, problem-solving workplace culture. Engaged employees are more likely to identify inefficiencies, contribute to process improvements, and take ownership of their work.
Key cultural benefits of Lean include:
- Increased employee involvement through Kaizen events and Gemba Walks, where workers actively participate in process improvements.
- Greater job satisfaction as employees feel empowered to contribute to decision-making.
- Improved teamwork and communication across departments, reducing silos and inefficiencies.
- Safer working conditions through 5S workplace organization and standardization.
Studies have shown that companies with strong Lean cultures experience higher employee retention rates, lower absenteeism, and increased workforce productivity.
Environmental Benefits: Reducing Waste and Energy Consumption
Lean consulting also has a significant environmental impact by reducing material waste, optimizing energy use, and promoting sustainable manufacturing practices. As companies face increasing pressure to improve sustainability, Lean principles provide a framework for eco-efficient production.
Key environmental benefits include:
- Lower material waste through optimized production processes and defect reduction.
- Reduced energy consumption by improving machine utilization and eliminating idle times.
- Minimized overproduction, which leads to fewer discarded products and packaging waste.
- Improved recycling and reusability of materials, cutting down on landfill waste.
Many organizations implementing Lean achieve waste reductions of 30-50%, supporting their sustainability initiatives while also lowering operational costs.
ROI: Measuring the Financial Impact of Lean Consulting
Companies investing in Lean consulting must ensure that their efforts generate a measurable return on investment. The ROI of Lean implementation can be assessed through key financial and operational metrics, such as:
- Cost Savings: Reduction in operational expenses, including labor, inventory, and defect costs.
- Productivity Gains: Increase in output per worker and per machine, improving revenue potential.
- Lead Time Reductions: Faster turnaround on customer orders, improving cash flow and competitive advantage.
- Quality Improvements: Lower defect rates, fewer product recalls, and decreased warranty costs.
- Customer Satisfaction: Improved on-time delivery and better product quality, leading to increased sales and brand loyalty.
A well-executed Lean transformation can generate ROI of 3x to 10x within the first few years, depending on the scale and scope of implementation. Organizations that track Lean KPIs consistently find that cost reductions and efficiency improvements directly contribute to long-term financial success.
Conclusion
Lean consulting provides tangible business benefits by reducing costs, improving operational efficiency, and enhancing product quality. Companies that implement Lean effectively experience lower lead times, increased throughput, and better resource utilization, leading to higher profitability and market competitiveness.
Beyond financial gains, Lean also fosters a culture of continuous improvement, where employees are more engaged and empowered to contribute to innovation. Additionally, Lean helps organizations align with sustainability goals by reducing waste, optimizing energy use, and promoting responsible manufacturing practices.
By measuring the ROI of Lean initiatives and aligning Lean strategies with business objectives, organizations can achieve long-term success and maintain a sustainable competitive advantage in their industry. Lean is not just a methodology—it is a proven strategy for driving growth, efficiency, and excellence in manufacturing and beyond.
Selecting a Lean Manufacturing Consultant
Choosing the right Lean manufacturing consultant is a critical decision that can determine the success or failure of a company’s Lean transformation. An experienced consultant brings expertise, a structured approach, and industry best practices to improve operational efficiency. However, not all consultants offer the same value, and companies must carefully assess candidates to ensure they select the best fit for their needs.
This section outlines key qualifications to look for, how to evaluate consulting firms versus independent consultants, common red flags, expected costs, and the typical timeline for a Lean transformation.
Key Qualifications to Look For
A Lean consultant must have a deep understanding of Lean principles, manufacturing processes, and change management strategies. The following qualifications and skills are essential when selecting a consultant:
- Extensive Experience in Manufacturing – The consultant should have hands-on experience in factory operations, supply chain management, and Lean implementation in industrial environments.
- Lean Six Sigma Certification – While not mandatory, certifications such as Lean Six Sigma Black Belt or Master Black Belt demonstrate expertise in both Lean and data-driven process improvement.
- Proven Track Record – The consultant should provide case studies or references showcasing successful Lean transformations in similar industries.
- Knowledge of Industry-Specific Regulations – In highly regulated sectors like pharmaceuticals, medical devices, and food manufacturing, expertise in compliance and industry standards is crucial.
- Ability to Train and Engage Employees – A Lean transformation requires cultural change. Consultants must have experience conducting Kaizen events, workshops, and leadership training.
- Strong Analytical and Problem-Solving Skills – Expertise in Value Stream Mapping (VSM), Root Cause Analysis, and Standardized Work Development is critical.
A consultant who possesses these qualifications will be well-equipped to drive measurable improvements and ensure long-term sustainability of Lean initiatives.
How to Evaluate Consulting Firms vs. Independent Consultants
Companies must decide whether to hire a Lean consulting firm or work with an independent consultant. Each option has distinct advantages and trade-offs.
Hiring a Lean Consulting Firm
Larger firms often have a team of consultants with diverse expertise, offering a more structured approach to Lean transformation.
Advantages:
- Access to multiple experts across different Lean specialties.
- Established methodologies and frameworks for Lean implementation.
- Strong reputation and proven case studies.
- Ability to scale projects across multiple facilities.
Disadvantages:
- Higher costs compared to independent consultants.
- Potential for less flexibility in customization.
- The company may not always get access to the firm’s top consultants.
Hiring an Independent Lean Consultant
Independent consultants often provide a more hands-on and customized approach, focusing closely on the specific needs of the company.
Advantages:
- More cost-effective than large consulting firms.
- Greater flexibility and adaptability to company-specific challenges.
- Direct access to a single, experienced expert rather than a rotating team.
Disadvantages:
- Limited resources compared to larger firms.
- May not have industry-wide recognition or extensive case studies.
- Less ability to handle large-scale enterprise transformations.
Companies should evaluate their budget, project scope, and desired level of support before deciding between a consulting firm and an independent expert.
Red Flags and Common Pitfalls in Hiring a Consultant
Not all Lean consultants deliver the promised results. Companies should be cautious of the following red flags when hiring a Lean manufacturing consultant:
- Lack of Hands-On Industry Experience – Theoretical knowledge alone is not enough. A consultant should have practical, real-world experience in Lean implementation.
- Overuse of Buzzwords Without Substance – Beware of consultants who focus on trendy Lean terminology without providing concrete examples of past successes.
- One-Size-Fits-All Approach – Lean strategies must be customized to a company’s unique operations. Consultants who push generic templates often fail to deliver meaningful results.
- Resistance to Employee Engagement – A good Lean consultant actively involves employees at all levels. If a consultant focuses only on high-level management strategies and ignores shop-floor engagement, their impact will be limited.
- Lack of Data-Driven Methodologies – Lean success relies on measurable improvements. A consultant should emphasize data collection, KPI tracking, and process analytics.
- Unrealistic Promises – Consultants who guarantee immediate results or massive cost savings without understanding the company’s current state may lack credibility.
Selecting a consultant who demonstrates practical knowledge, adaptability, and a data-driven approach is crucial for a successful Lean transformation.
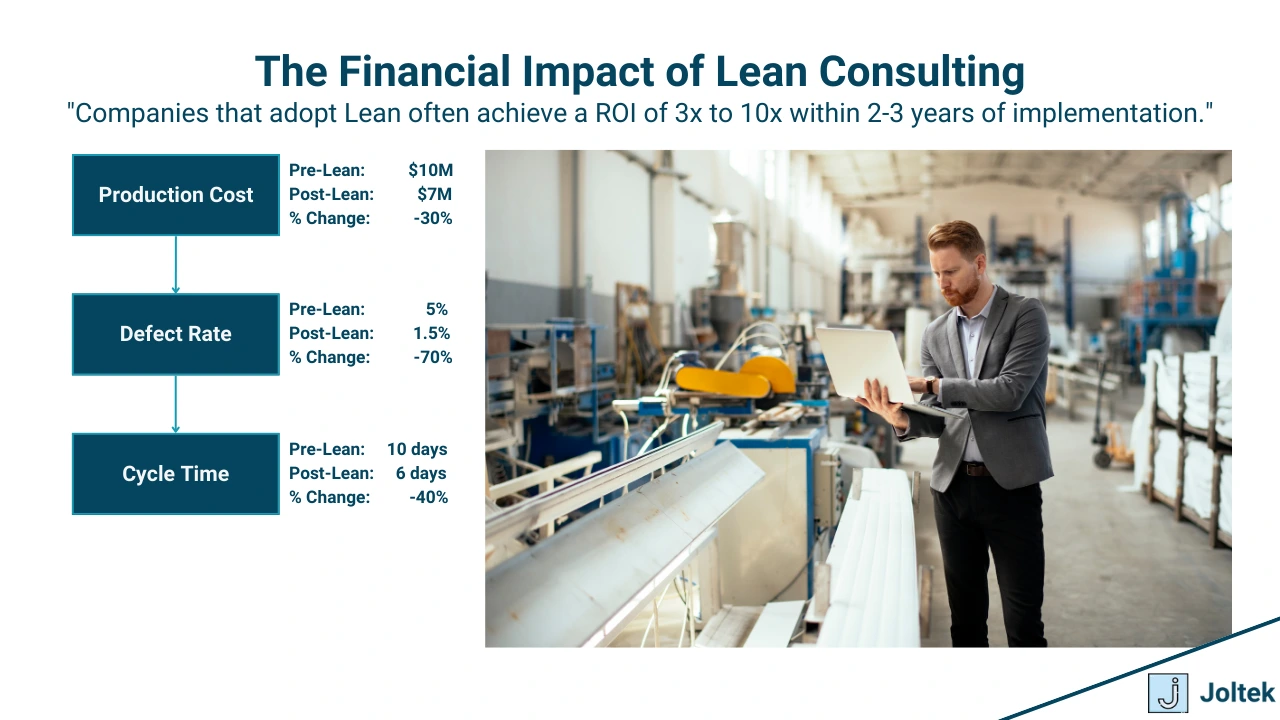
Expected Costs of Lean Consulting Services
The cost of Lean consulting varies based on the consultant’s experience, the complexity of the project, and the duration of the engagement. Below are typical pricing structures for Lean consulting services:
- Hourly Rate: $150 – $500 per hour, depending on expertise and industry.
- Daily Rate: $1,500 – $5,000 per day for on-site training, assessments, or Kaizen events.
- Project-Based Fees: $20,000 – $250,000, depending on the scale of implementation. Large enterprise transformations may exceed this range.
- Retainer Agreements: Some companies opt for long-term consulting support, typically ranging from $10,000 – $50,000 per month.
Factors influencing cost include:
- The size and complexity of the organization.
- The scope of Lean implementation (single department vs. enterprise-wide transformation).
- The need for customized training programs and software integration.
While Lean consulting requires an upfront investment, companies often experience ROI of 3x to 10x within the first few years due to cost savings, increased efficiency, and improved product quality.
How Long a Lean Transformation Typically Takes
The duration of a Lean transformation depends on the organization’s size, current operational maturity, and the depth of implementation. While small-scale projects can deliver quick wins, a full Lean transformation requires sustained effort over months or years.
Typical Lean transformation timelines:
- Short-Term Kaizen Events (1-2 Weeks): Focus on solving a specific problem, such as reducing changeover times or improving workstation efficiency.
- Department-Level Implementation (3-6 Months): Involves Value Stream Mapping, process redesign, and employee training for a specific department or production line.
- Enterprise-Wide Lean Transformation (1-3 Years): A company-wide Lean journey, including cultural change, leadership training, and continuous improvement initiatives.
For sustainable results, Lean should not be treated as a one-time project but an ongoing process of continuous improvement. Organizations that embed Lean principles into their culture experience long-term operational excellence.
Conclusion
Selecting the right Lean manufacturing consultant is a crucial step in ensuring a successful and sustainable transformation. Companies should prioritize consultants with practical industry experience, strong problem-solving skills, and a track record of measurable success.
While consulting firms provide structured methodologies and broad expertise, independent consultants offer flexibility and hands-on involvement. Organizations must carefully assess their needs, budget, and desired level of support before making a decision.
Avoiding common pitfalls such as generic solutions, lack of employee engagement, and unrealistic expectations can help companies maximize the value of their Lean investment. Understanding the cost structure of Lean consulting and setting realistic expectations regarding transformation timelines ensures long-term success.
A well-chosen Lean consultant can help organizations reduce costs, improve efficiency, and create a culture of continuous improvement, leading to sustained competitive advantage in today’s dynamic manufacturing landscape.
Lean and Industry 4.0: The Future of Lean Consulting
The evolution of manufacturing is increasingly driven by Industry 4.0 technologies, which complement and enhance Lean principles. While traditional Lean methodologies focus on eliminating waste, improving flow, and optimizing processes, digital transformation introduces real-time data, automation, and advanced analytics to further improve efficiency. The integration of Lean and Industry 4.0 is reshaping manufacturing, making operations more agile, intelligent, and responsive to changing demands.
This section explores how Lean consulting is evolving with Industrial IoT, AI-driven analytics, robotics, and smart manufacturing technologies to create the next generation of operational excellence.
How Digital Transformation and Technology Enhance Lean
Lean principles emphasize waste reduction, process efficiency, and continuous improvement. However, many Lean implementations still rely on manual data collection and human-driven decision-making, which can introduce errors and limit responsiveness. Industry 4.0 technologies bridge these gaps by:
- Providing real-time operational visibility through sensors, Industrial IoT (IIoT), and data analytics.
- Automating repetitive tasks to reduce human error and improve cycle times.
- Leveraging predictive analytics to anticipate and prevent machine failures, reducing downtime.
- Enhancing supply chain responsiveness by synchronizing inventory with demand signals.
- Supporting continuous improvement efforts through AI-driven process optimization.
Digital transformation does not replace Lean principles; rather, it augments and accelerates Lean implementation by making data-driven decision-making more accurate, timely, and scalable.
Lean and Industrial IoT (IIoT)
Industrial IoT (IIoT) plays a crucial role in modern Lean transformations by providing real-time data from machines, production lines, and supply chains. Traditionally, Lean relies on manual process observations and periodic performance reviews, but IIoT allows organizations to monitor and optimize operations in real-time.
Key Applications of IIoT in Lean Manufacturing
- Predictive Maintenance (PdM): IIoT sensors monitor machine conditions and alert teams to potential failures before they cause downtime, aligning with Lean’s focus on Total Productive Maintenance (TPM).
- Real-Time Value Stream Mapping (VSM): Instead of manually tracking material flow, IIoT provides live data on cycle times, bottlenecks, and work-in-progress (WIP) inventory.
- Automated Kanban & Pull Systems: IIoT-connected inventory systems automatically trigger replenishment when stock levels drop, eliminating excess inventory and waste.
- Energy Efficiency Optimization: Smart sensors track energy consumption and detect areas of inefficiency, supporting Lean’s environmental and cost-saving goals.
By integrating IIoT, Lean consulting evolves from reactive problem-solving to proactive and predictive operational improvements.
Lean and Advanced Analytics / AI in Manufacturing
Artificial Intelligence (AI) and advanced analytics enhance Lean by uncovering inefficiencies that may not be immediately visible through traditional Lean methods. AI-driven insights allow organizations to make data-backed decisions faster and more effectively.
How AI Enhances Lean:
- Root Cause Analysis (RCA): AI analyzes production data to identify patterns that lead to defects, automating what traditionally required manual 5 Whys or Fishbone Diagrams.
- Process Optimization: Machine learning algorithms continuously refine production schedules, cycle times, and bottlenecks for greater efficiency.
- Quality Control & Defect Prevention: AI-powered computer vision systems inspect products for defects, preventing faulty goods from moving through the supply chain.
- Demand Forecasting: AI-driven analytics predict customer demand fluctuations, aligning production schedules with Lean’s Just-in-Time (JIT) principles.
Instead of relying solely on human observations and historical data, AI allows Lean consultants to develop real-time, continuously improving process optimizations.
Lean and Robotics & Automation
Lean consulting increasingly involves robotics and automation to eliminate waste, increase efficiency, and standardize production processes. While some argue that automation contradicts Lean’s principle of minimizing excess costs, when implemented correctly, robotics aligns with Lean’s goal of eliminating non-value-adding activities.
How Robotics Supports Lean Principles:
- Automated Material Handling: Reduces unnecessary motion and transportation waste by optimizing how raw materials and components move through production.
- Cobots (Collaborative Robots): Work alongside humans to perform repetitive or ergonomically challenging tasks, reducing defects and improving worker safety.
- Automated Changeovers (SMED Enhancement): Robotics streamline machine setup times, reducing downtime and improving flexibility in production.
- Assembly Line Efficiency: Robotic process automation (RPA) reduces cycle time variability, ensuring consistent production flow.
Lean consulting now incorporates automation strategies that complement human work, allowing organizations to scale efficiency without unnecessary labor costs.
How Lean Integrates with Smart Manufacturing
Smart manufacturing represents the convergence of Lean principles, digital transformation, and connected technologies. It enables organizations to move beyond traditional Lean approaches by leveraging real-time intelligence, automation, and cloud-based analytics.
Key Features of Smart Manufacturing in a Lean Environment:
- End-to-End Visibility: Live dashboards provide real-time insights into production performance, inventory levels, and supply chain operations.
- Adaptive Lean Systems: AI-driven self-optimizing production lines continuously adjust parameters for maximum efficiency.
- Connected Workflows: Digital twin simulations allow manufacturers to test and refine Lean improvements in a virtual environment before deploying changes on the shop floor.
- Worker Augmentation: Smart wearables and augmented reality (AR) assist employees in executing standard work procedures with minimal errors.
By integrating Lean with Industry 4.0 technologies, manufacturers gain the ability to implement continuous improvement at an unprecedented scale and speed.
Conclusion
Lean consulting is evolving beyond traditional process improvement methodologies into a digitally enabled, data-driven practice. The integration of Industrial IoT, AI, automation, and smart manufacturing amplifies the benefits of Lean by enabling real-time monitoring, predictive insights, and adaptive process optimization.
Industrial IoT enhances Lean by providing real-time visibility into production inefficiencies, while AI and advanced analytics drive deeper insights into waste reduction. Robotics and automation streamline repetitive tasks and increase efficiency without eliminating Lean’s focus on flexibility. Finally, smart manufacturing creates an interconnected production environment, allowing companies to optimize performance continuously.
The future of Lean consulting lies in its seamless integration with Industry 4.0, enabling manufacturers to achieve greater efficiency, agility, and competitiveness in an increasingly digital world. Companies that embrace this transformation will benefit from higher profitability, faster production cycles, and improved overall operational performance, securing their position as industry leaders in the years ahead.
Conclusion
Lean consulting has proven to be one of the most effective methodologies for improving manufacturing efficiency, reducing waste, and enhancing overall operational performance. Whether companies seek to cut costs, streamline production, improve product quality, or optimize their supply chain, Lean provides a structured, proven approach to achieving these goals. However, successful Lean implementation requires more than just deploying a set of tools—it demands a cultural shift, leadership commitment, and continuous improvement mindset.
This final section highlights key takeaways for manufacturers considering Lean consulting, outlines actionable next steps, emphasizes the role of leadership, and provides insights into the ongoing evolution of Lean manufacturing.
Key Takeaways for Manufacturers Considering Lean Consulting
Manufacturers exploring Lean consulting should understand that Lean is not a one-time project but a continuous journey. Companies that integrate Lean into their operational strategy gain long-term benefits in productivity, cost savings, and market competitiveness.
Key takeaways include:
- Lean consulting helps companies eliminate waste, improve efficiency, and drive continuous improvement. Whether targeting inventory reduction, lead time optimization, or defect minimization, Lean provides a structured approach to solving operational challenges.
- Customization is essential for success. One-size-fits-all Lean solutions often fail; a good consultant will tailor Lean methodologies to a company’s unique operational needs and industry requirements.
- Employee engagement is critical. Lean is most effective when workers at all levels participate in problem-solving and process improvements. Without workforce buy-in, Lean initiatives struggle to gain traction.
- Industry 4.0 technologies are reshaping Lean consulting. The integration of Industrial IoT, AI, and automation enhances traditional Lean principles, providing real-time insights, predictive analytics, and automated efficiency improvements.
- Lean is a long-term strategy, not a quick fix. Companies that view Lean as a sustained improvement effort rather than a short-term cost-cutting initiative see the most significant and lasting benefits.
Understanding these core principles helps manufacturers maximize the impact of Lean consulting and achieve sustainable operational excellence.
Next Steps for Companies Looking to Implement Lean
For companies ready to begin their Lean journey, the following structured approach ensures a smooth and effective transition:
- Conduct a Lean Readiness Assessment
- Identify pain points in production, supply chain, or quality control.
- Evaluate current levels of waste, inefficiency, and process variability.
- Assess leadership commitment and employee engagement readiness.
- Define Clear Lean Objectives and Metrics
- Establish specific, measurable goals (e.g., reducing defects by 30%, cutting lead times by 40%).
- Align Lean initiatives with overall business objectives to ensure strategic impact.
- Select the Right Lean Consultant or Internal Champion
- Choose an experienced Lean consultant with industry expertise and a track record of success.
- Alternatively, develop internal Lean leaders through training and certification programs.
- Start with High-Impact, Quick-Win Projects
- Implement 5S workplace organization, Kanban inventory systems, or SMED changeover reductions to generate early success.
- Use Kaizen events to foster a culture of continuous improvement and involve employees in Lean problem-solving.
- Integrate Lean with Digital Transformation Initiatives
- Explore Industrial IoT, AI, and automation to enhance Lean efficiency.
- Invest in real-time data collection and analytics to support Lean decision-making.
- Sustain and Scale Lean Improvements
- Establish long-term Lean leadership roles to maintain momentum.
- Conduct regular Lean audits to track progress and reinforce improvements.
- Encourage ongoing employee training and engagement to ensure Lean principles remain embedded in daily operations.
By following these steps, manufacturers can implement Lean successfully, generate measurable improvements, and sustain long-term operational excellence.
The Role of Leadership in Sustaining Lean Initiatives
Leadership commitment is the most critical factor in ensuring the long-term success of Lean initiatives. Without strong leadership, Lean improvements often lose momentum, and organizations risk reverting to old inefficiencies.
Key responsibilities of leadership in Lean transformation include:
- Setting the vision and aligning Lean with business goals. Lean should be positioned as a strategic initiative, not just a cost-cutting exercise.
- Leading by example. Executives and plant managers should actively participate in Lean activities, such as Gemba Walks and Kaizen events.
- Providing necessary resources. Sustained Lean improvements require investment in training, technology, and process optimization.
- Empowering employees to drive continuous improvement. Leaders should create a work environment where employee contributions to Lean improvements are recognized and rewarded.
- Monitoring progress and ensuring accountability. Establishing KPIs, dashboards, and performance reviews ensures that Lean initiatives remain on track.
Companies where leadership actively supports and champions Lean principles see the most consistent, long-term benefits from their Lean transformations.
Final Thoughts on the Evolution of Lean Manufacturing
Lean manufacturing has continuously evolved since its origins in the Toyota Production System (TPS). Initially focused on waste elimination and process efficiency, Lean has now expanded to embrace digital transformation, automation, and Industry 4.0 technologies.
Key trends shaping the future of Lean consulting include:
- The fusion of Lean and digital manufacturing. The integration of AI, Industrial IoT, and automation is making Lean faster, more precise, and more adaptable.
- Increased focus on sustainability. Modern Lean initiatives go beyond efficiency improvements to include waste reduction, energy optimization, and environmentally friendly production practices.
- Data-driven Lean strategies. Real-time analytics and predictive modeling are replacing traditional manual observations, leading to smarter, more responsive Lean operations.
- Lean in non-manufacturing sectors. While Lean originated in manufacturing, its principles are now being applied in healthcare, software development, logistics, and service industries.
As Lean continues to evolve, companies that embrace both traditional Lean principles and modern digital advancements will remain competitive in an increasingly complex and fast-paced global marketplace.
Conclusion
Lean consulting provides a proven framework for operational excellence, helping manufacturers achieve cost reduction, process efficiency, quality improvement, and cultural transformation. However, success requires a structured approach, strong leadership, and continuous employee engagement.
For companies considering Lean, the key is to start small, scale improvements, and integrate Lean with emerging digital technologies. Leadership must champion Lean efforts, ensure accountability, and foster a culture where continuous improvement becomes a fundamental part of the organization’s DNA.
As Industry 4.0 continues to reshape manufacturing, Lean principles remain more relevant than ever. By combining traditional Lean methodologies with AI, automation, and real-time analytics, companies can unlock even greater efficiency and agility in their operations.
Manufacturers that commit to Lean as a long-term strategic approach—rather than a temporary initiative—will be best positioned to drive sustained growth, profitability, and competitive advantage in the future of manufacturing.