Introduction to Industry 4.0 and Its Software Landscape
Definition and Scope of Industry 4.0
Industry 4.0, often referred to as the Fourth Industrial Revolution, signifies a transformative era in manufacturing marked by the integration of digital technologies, data-driven decision-making, and cyber-physical systems. This evolution stems from the digitization of manufacturing and leverages advancements like the Internet of Things (IoT), Artificial Intelligence (AI), data analytics, and robotics. In essence, Industry 4.0 represents a new level of interconnectedness across machines, processes, and systems to create “smart factories” that optimize production, improve flexibility, and respond to demands more dynamically.
The concept transcends the boundaries of traditional manufacturing by integrating systems throughout the entire value chain—from suppliers to customers. Industry 4.0 has profound implications for productivity, efficiency, and innovation, transforming not only factory floors but also business models, supply chains, and workforce structures. The Fourth Industrial Revolution aims to achieve a seamless blend of the digital and physical worlds, creating an ecosystem where technology augments human work and fosters new levels of collaboration and efficiency.
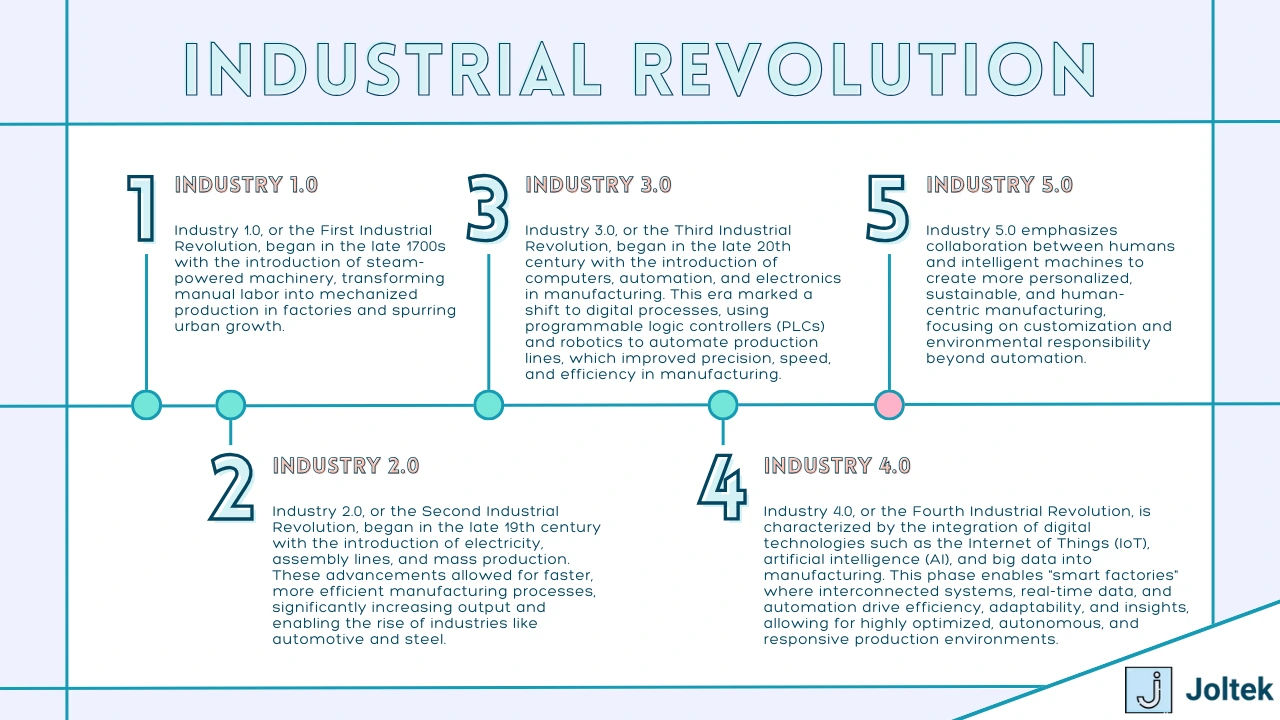
Importance of Software in Realizing Industry 4.0
At the core of Industry 4.0’s transformative potential is software. While hardware enables connectivity and data collection, it is the software that interprets data, enables process automation, and drives strategic decisions. Industry 4.0 software encompasses a variety of applications, from Manufacturing Execution Systems (MES) and Enterprise Resource Planning (ERP) systems to IoT platforms and advanced analytics tools. Each plays a crucial role in gathering, processing, and presenting data for actionable insights.
Software solutions enable manufacturers to achieve visibility across their operations, integrate data from disparate sources, and apply AI and analytics to optimize processes in real-time. With software, manufacturing shifts from being reactive to predictive, empowering organizations to foresee potential issues, reduce downtime, and improve product quality. For Industry 4.0 to succeed, companies must adopt a layered software approach that can scale and adapt as new technologies emerge, ensuring flexibility and resilience in a rapidly changing industrial landscape.
Evolution of Industry 4.0 Software and Current State of the Market
Industry 4.0 software has undergone significant evolution, influenced by technological advancements and changing industry demands. Early stages of Industry 4.0 saw isolated digital tools that could handle specific functions, such as SCADA systems for process control or basic MES for tracking production. However, these systems often operated in silos, limiting data integration and cross-functional insights. As data and digitalization became central to competitive advantage, companies began to seek integrated, interoperable solutions that could facilitate a connected, data-driven manufacturing environment.
Today’s Industry 4.0 software has evolved into a sophisticated ecosystem that includes MES, ERP, SCADA, IoT platforms, analytics, and AI tools, all working cohesively to deliver end-to-end visibility and control. Modern Industry 4.0 solutions are cloud-enabled, allowing manufacturers to leverage scalable infrastructure and advanced computational capabilities without the constraints of on-premises systems. The current market reflects a shift towards software-as-a-service (SaaS) models, offering flexibility, lower upfront costs, and continuous updates.
A defining feature of today’s Industry 4.0 software landscape is its focus on connectivity and interoperability. Unified Namespace (UNS) concepts and data lakes are now gaining traction as solutions that allow data from multiple sources to be centralized, contextualized, and accessed across the organization. This connected approach is essential for enabling real-time decision-making and achieving the agile, responsive manufacturing environment that Industry 4.0 envisions.
Key Stakeholders and Decision-Makers Who Benefit from Industry 4.0 Software
The adoption and integration of Industry 4.0 software involve various stakeholders across multiple levels within an organization, each bringing unique perspectives and priorities. These key stakeholders include:
- C-Suite Executives: CEOs, COOs, and CIOs are concerned with the strategic impact of Industry 4.0 software on business outcomes, such as profitability, agility, and competitive positioning. They focus on how software investments will enhance operational efficiency, drive growth, and contribute to long-term value.
- Plant Managers and Operations Leaders: Plant managers oversee day-to-day production and are focused on achieving improvements in throughput, quality, and resource utilization. They seek software solutions that deliver real-time insights, streamline processes, and reduce downtime, ultimately enabling them to achieve operational excellence.
- IT and OT Professionals: IT (Information Technology) and OT (Operational Technology) teams are responsible for implementing, maintaining, and securing Industry 4.0 software. With the convergence of IT and OT systems, these teams collaborate to integrate and support software solutions that enable seamless data flow and automation across the enterprise.
- Data Scientists and Analysts: Data specialists leverage Industry 4.0 software to derive actionable insights from massive amounts of data generated by industrial processes. Their role is crucial in transforming raw data into predictive analytics, quality improvements, and process optimizations.
- Consultants and External Advisors: Often, organizations turn to consultants with expertise in Industry 4.0 to guide strategy, implementation, and optimization efforts. These external advisors provide an objective assessment, helping organizations navigate complex software ecosystems and adopt best practices that align with their unique goals.
- End-users and Operators: On the front lines of manufacturing, operators and other end-users interact with software to monitor processes, respond to alerts, and input data. Their involvement is essential to ensure the software is user-friendly and provides the necessary support for their roles.
Core Strategies for Industry 4.0 Transformation
Developing an Industry 4.0 Vision and Roadmap for Companies
A clear vision and roadmap are fundamental for companies pursuing Industry 4.0 transformation. An Industry 4.0 vision outlines the organization's long-term aspirations, detailing how it plans to leverage digital technologies to enhance operations, drive growth, and deliver value. This vision serves as a North Star, guiding decisions on technology adoption, resource allocation, and change management.
Creating an Industry 4.0 roadmap involves setting achievable milestones and timelines for implementing digital tools, upskilling the workforce, and aligning resources. This roadmap should also include an assessment of the organization’s current digital maturity, outlining necessary steps to bridge the gap between its current state and the desired future state. Elements of a well-designed roadmap may include:
- Digital Maturity Assessment: An evaluation of current technological capabilities and infrastructure.
- Identification of Key Initiatives: Prioritizing specific projects, such as deploying IoT devices, enhancing data analytics capabilities, or adopting cloud-based systems.
- Timeline and Milestones: Establishing clear phases and benchmarks to measure progress.
- Resource Allocation: Determining budgets, personnel, and external partnerships needed for success.
- Change Management Plan: Preparing the organization for cultural and operational changes necessary for digital transformation.
Strategic Alignment Between IT and OT in Industry 4.0
One of the significant challenges in implementing Industry 4.0 is achieving alignment between Information Technology (IT) and Operational Technology (OT) departments. Traditionally, IT and OT have operated in silos, with IT focused on data management, cybersecurity, and business systems, while OT has focused on process control, equipment operation, and plant safety. Industry 4.0 requires these two domains to collaborate closely to ensure that data flows seamlessly across the organization and that digital technologies can be integrated into manufacturing operations.
To align IT and OT, organizations can adopt a unified data strategy that leverages shared standards and protocols to ensure compatibility between systems. Regular cross-departmental meetings and joint training sessions can also help build mutual understanding between these groups, fostering a collaborative environment. The following strategies support IT-OT alignment:
- Unified Data Strategy: Establishing a single source of truth for data and shared standards to facilitate integration.
- Joint Governance Models: Creating cross-functional teams to oversee digital transformation initiatives, involving representatives from both IT and OT.
- Interoperability Standards: Leveraging open protocols and platforms that allow IT and OT systems to communicate seamlessly.
- Regular Communication: Establishing forums for continuous dialogue and collaborative problem-solving between IT and OT.
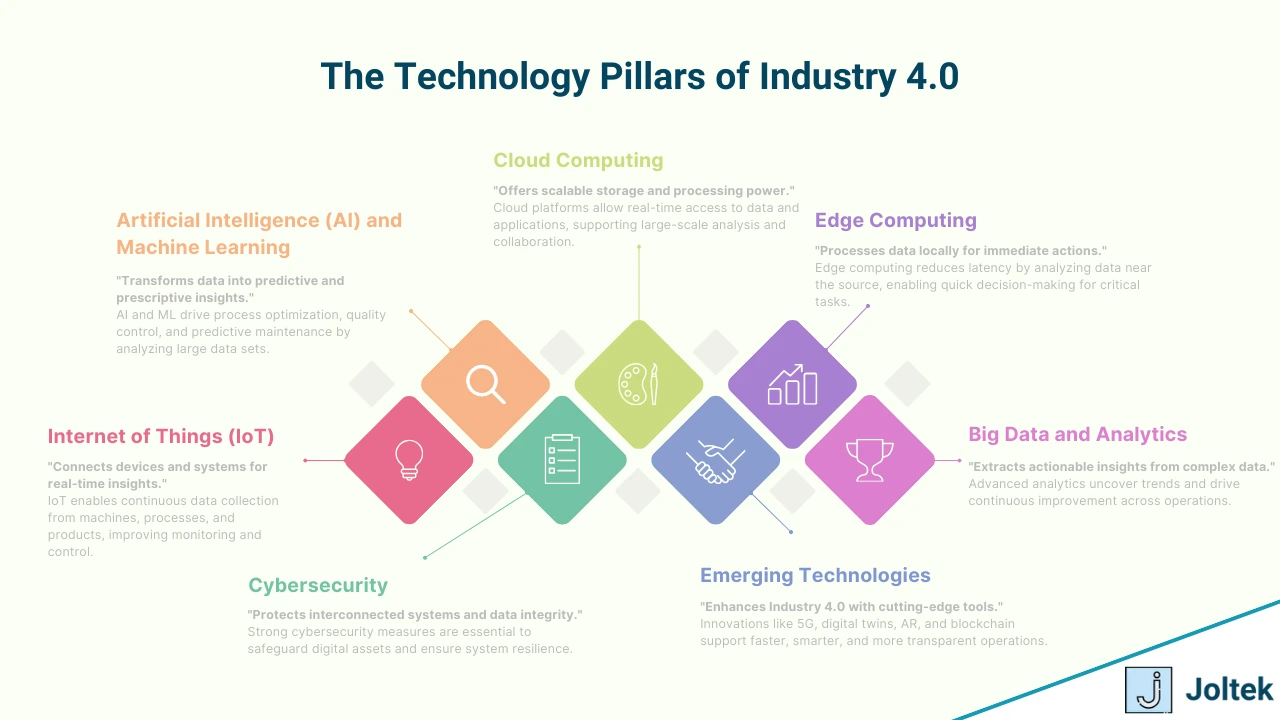
Identifying Goals: Operational Efficiency, Sustainability, Agility, and Innovation
Setting clear, measurable goals is crucial for guiding Industry 4.0 initiatives. These goals should align with the broader organizational objectives and address the unique challenges and opportunities within the manufacturing environment. Some of the most common goals include:
- Operational Efficiency: One of the primary drivers of Industry 4.0 adoption is the desire to improve operational efficiency. This can be achieved by reducing downtime, optimizing resource use, and streamlining production processes. Software solutions like Manufacturing Execution Systems (MES) and IoT-enabled devices provide real-time insights, allowing companies to make data-driven adjustments that enhance productivity.
- Sustainability: Industry 4.0 offers tools and strategies for manufacturers to reduce their environmental impact. This includes optimizing energy usage, minimizing waste, and enabling predictive maintenance to extend equipment lifespan. By integrating sustainability as a goal, companies can also meet regulatory standards and align with societal expectations for responsible manufacturing.
- Agility: The ability to respond quickly to market changes, customer demands, and supply chain disruptions is a competitive advantage. Industry 4.0 technologies such as digital twins and predictive analytics empower organizations to anticipate potential issues and adapt operations as needed. Agility enables manufacturers to remain competitive in fast-evolving markets.
- Innovation: Industry 4.0 enables companies to innovate in product design, production processes, and customer engagement. For example, digital twins and simulation tools allow companies to experiment with new designs and process flows in a virtual environment, reducing time to market for new products.
The Role of Consulting in Defining and Achieving Strategic Objectives
For many organizations, the complexity of Industry 4.0 transformation makes consulting an invaluable resource. Consultants provide expertise in both the technical and strategic aspects of digital transformation, helping companies identify opportunities, mitigate risks, and establish best practices. Consultants also play a key role in aligning internal teams, assessing digital maturity, and building custom solutions that address specific business needs.
Consultants can guide organizations through several critical aspects of Industry 4.0, including:
- Readiness Assessments: Evaluating the organization’s current capabilities and identifying gaps in infrastructure, skills, and processes.
- Benchmarking: Comparing the organization’s performance against industry standards and competitors to identify areas for improvement.
- Solution Architecture: Designing a technology stack tailored to the company’s needs, encompassing IoT platforms, MES, ERP, and other Industry 4.0 software solutions.
- Implementation Planning: Creating a phased plan for rolling out Industry 4.0 initiatives with a focus on minimizing disruption to operations.
- Change Management and Training: Supporting cultural change, providing training, and fostering buy-in among employees to ensure successful adoption.
By leveraging consulting expertise, organizations can accelerate their Industry 4.0 journeys, avoid common pitfalls, and maximize the return on their technology investments.
The Technology Pillars of Industry 4.0
Industry 4.0 is built on a foundation of key technologies that enable the interconnected, data-driven, and adaptive environments of modern manufacturing. This section covers the core technologies and emerging innovations that are central to Industry 4.0.
Overview of Essential Technologies Powering Industry 4.0
Internet of Things (IoT) and Industrial IoT (IIoT) for Real-Time Monitoring
The Internet of Things (IoT) is the network of connected devices that collect and share data, while Industrial IoT (IIoT) applies this concept specifically to industrial environments. IoT and IIoT devices include sensors, cameras, and smart actuators embedded in manufacturing equipment, allowing companies to monitor conditions and operations in real-time.
In manufacturing, IIoT enables predictive maintenance, where data from sensors helps identify wear patterns or anomalies in equipment, reducing unplanned downtime. It also provides a real-time view of the production environment, enabling companies to monitor energy usage, environmental conditions, and process parameters continuously. With IIoT, factories become transparent, adaptable, and efficient.
Artificial Intelligence (AI) and Machine Learning (ML) for Predictive Analytics
Artificial Intelligence (AI) and Machine Learning (ML) are essential for turning vast amounts of data into actionable insights. In Industry 4.0, AI and ML drive predictive analytics, allowing manufacturers to anticipate problems before they occur. For instance, machine learning models can analyze historical data on equipment performance to predict when maintenance will be needed, minimizing downtime.
Additionally, AI and ML are used to optimize production processes. By analyzing data from multiple sources, these technologies can recommend process improvements, adapt operations dynamically, and enhance quality control by identifying defects in real-time. AI-powered image recognition systems, for example, can detect flaws on production lines, enhancing quality assurance.
Cloud Computing for Scalable Solutions
Cloud computing offers the computational power and storage necessary to manage large-scale Industry 4.0 initiatives. By utilizing cloud platforms, companies can access scalable resources without investing heavily in on-premises infrastructure. Cloud solutions facilitate data storage, application hosting, and complex analytics, allowing manufacturers to process and analyze data from multiple sites or equipment globally.
Cloud computing also supports collaboration and remote monitoring by enabling access to real-time data and insights from anywhere. With software-as-a-service (SaaS) solutions, manufacturers can implement advanced capabilities for MES, ERP, and IoT platforms with minimal upfront costs and benefit from regular updates and maintenance provided by cloud vendors.
Edge Computing for Latency-Sensitive Applications
While cloud computing provides scalable solutions, certain Industry 4.0 applications demand ultra-low latency, such as real-time control systems or high-speed quality inspections. Edge computing addresses these needs by bringing computation closer to the source of data generation, enabling faster processing and reducing the dependency on cloud connections.
In edge computing, data is processed on devices located at or near the production site, allowing for immediate decision-making and control. For instance, edge computing allows a robotic arm to adjust in real-time to variations in material or process without needing to send data to a remote server. This localized approach is particularly valuable in environments where even milliseconds of delay could impact performance or safety.
Big Data Analytics and Data Lakes
Big data analytics enables manufacturers to extract value from large and complex data sets. In Industry 4.0, big data can come from various sources, including IoT devices, production systems, and customer feedback channels. By applying advanced analytics, manufacturers can discover patterns, trends, and insights that drive efficiency, enhance product quality, and support strategic decision-making.
Data lakes provide a storage solution for the vast and varied data generated in Industry 4.0 environments. Unlike traditional databases, which are structured, data lakes can store raw, unprocessed data in various formats. This flexibility allows companies to collect and analyze data from different sources and revisit it as new analytics needs arise. Data lakes serve as a foundational element for machine learning, predictive maintenance, and other data-driven applications.
Cybersecurity as a Foundational Layer
In the interconnected world of Industry 4.0, cybersecurity is paramount. As more devices connect to networks, the potential vulnerabilities increase, exposing manufacturing environments to cyber threats. Industry 4.0 cybersecurity involves protecting data, ensuring the integrity of control systems, and preventing unauthorized access to connected devices.
Effective cybersecurity strategies include:
- Network Segmentation: Dividing networks to isolate sensitive data and reduce risk.
- Access Control: Using authentication and role-based access to restrict system entry.
- Encryption: Ensuring data privacy both at rest and in transit.
- Monitoring and Threat Detection: Continuously observing network activity to detect suspicious behavior and respond promptly.
Investing in robust cybersecurity infrastructure is essential to protect intellectual property, ensure safety, and maintain trust with customers and partners.
Emerging Technologies in Industry 4.0
5G for High-Speed Connectivity
5G technology is poised to transform Industry 4.0 by providing high-speed, low-latency connectivity. With speeds significantly faster than previous generations, 5G enables real-time data transfer, supporting applications that demand high throughput and low lag, such as robotics, automated guided vehicles (AGVs), and augmented reality (AR) solutions on the factory floor. For manufacturers, 5G also facilitates remote monitoring and control, allowing for a more flexible and connected production environment.
Digital Twins for Enhanced Simulation and Process Optimization
Digital twins are virtual replicas of physical assets, systems, or processes that provide a dynamic simulation environment. They allow manufacturers to test changes, forecast outcomes, and optimize operations without disrupting real-world production. Digital twins are used to model equipment performance, assess production flows, and refine product designs in a risk-free digital environment.
For example, a digital twin of a production line enables operators to adjust parameters, simulate the impact of changes, and find optimal settings for efficiency or product quality. Digital twins empower manufacturers to experiment with scenarios, identify bottlenecks, and improve overall process control.
Augmented Reality (AR) for Workforce Training and Support
Augmented Reality (AR) enhances the real-world environment by overlaying digital information, providing operators with instructions, insights, and troubleshooting guidance directly on their view. AR can improve training programs by immersing employees in simulated production tasks, enabling them to learn complex processes in a hands-on manner.
In maintenance or repair scenarios, AR can display equipment data, step-by-step repair guides, or remote assistance from experts. This technology boosts workforce productivity, shortens training times, and supports real-time problem-solving on the shop floor.
Blockchain in Manufacturing for Traceability and Transparency
Blockchain technology offers a decentralized, tamper-proof record of transactions and can be used in manufacturing to improve traceability, transparency, and accountability. Blockchain’s potential applications in Industry 4.0 include tracking supply chains, ensuring the authenticity of parts, and securing data transfers between devices.
For instance, in industries requiring strict compliance with safety and quality standards, blockchain can track the origin, condition, and movement of raw materials and components. Blockchain ensures that data is immutable, enhancing trust among suppliers, manufacturers, and customers.
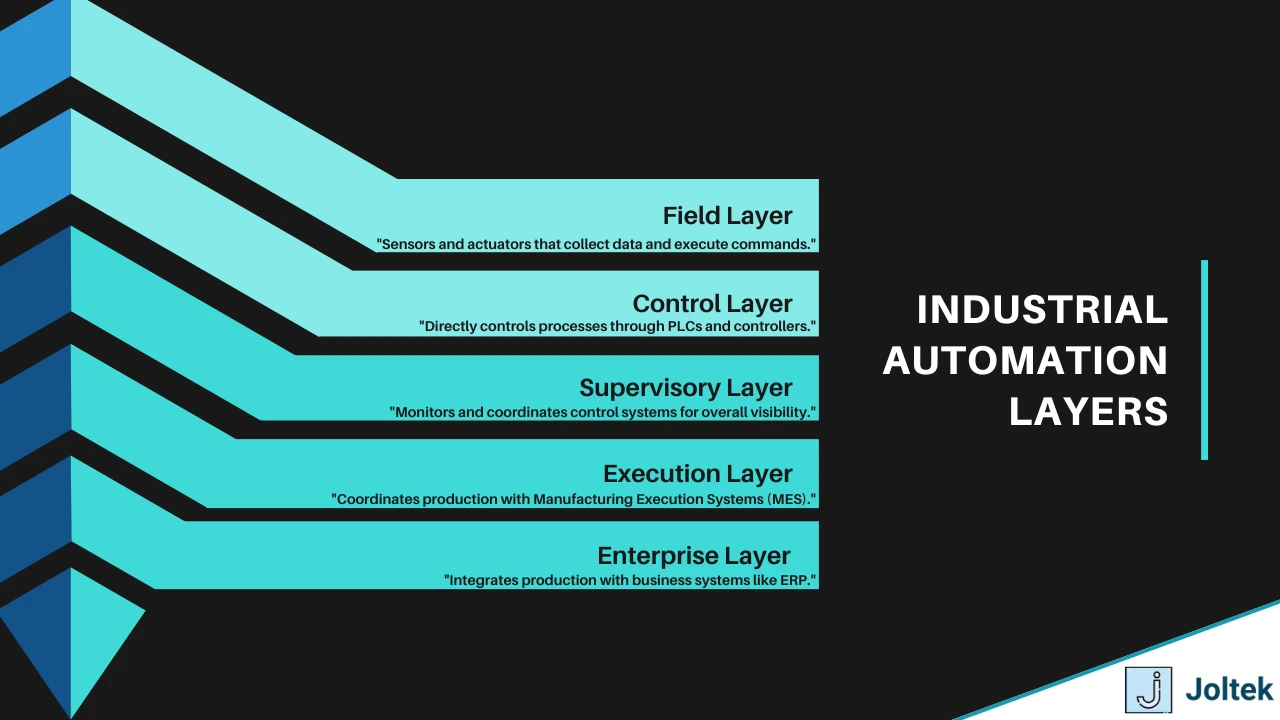
Key Software Solutions in Industry 4.0
In Industry 4.0, software solutions are essential for achieving interconnected, data-driven manufacturing environments. These software tools enable manufacturers to streamline operations, optimize resource usage, and make informed decisions based on real-time data. Here, we explore the key software solutions that drive Industry 4.0 transformation.
Manufacturing Execution Systems (MES) and Manufacturing Operations Management (MOM)
Manufacturing Execution Systems (MES) and Manufacturing Operations Management (MOM) solutions are pivotal in bridging the gap between production and enterprise-level systems. MES tracks and documents the transformation of raw materials into finished products in real-time, providing data on production workflows, quality control, and equipment utilization. MOM software, which includes MES as a subset, offers broader operational functionality, integrating quality management, planning, and resource scheduling.
These systems enhance production visibility, enabling operators to monitor progress, control quality, and optimize resources. MES and MOM are critical for implementing continuous improvement initiatives, as they provide granular insights into production performance and resource usage, helping manufacturers reduce waste and boost efficiency.
Enterprise Resource Planning (ERP) Integration for Supply Chain Agility
Enterprise Resource Planning (ERP) systems manage core business functions, including finance, procurement, inventory, and supply chain. In the context of Industry 4.0, ERP integration plays a critical role in enabling end-to-end supply chain visibility and agility. By connecting ERP with other manufacturing software like MES and IoT platforms, companies can synchronize production with demand, improve inventory management, and enhance supplier collaboration.
ERP integration also allows manufacturers to respond rapidly to market fluctuations by adjusting production schedules, managing inventory in real time, and optimizing procurement. This end-to-end coordination across the supply chain leads to cost savings, improved customer satisfaction, and a more agile manufacturing environment that can respond dynamically to changes.
SCADA and IoT Platforms for Process Visibility
Supervisory Control and Data Acquisition (SCADA) systems have long been used to monitor and control industrial processes. In Industry 4.0, SCADA systems work alongside IoT platforms to provide enhanced visibility across production lines and facilities. SCADA captures real-time data from equipment and processes, while IoT platforms extend this capability by connecting more devices and enabling remote monitoring, analytics, and control.
Together, SCADA and IoT platforms allow operators and decision-makers to gain deep insights into production health, energy consumption, and equipment performance. This visibility empowers manufacturers to detect and resolve issues proactively, improve process efficiency, and minimize downtime. IoT platforms also enable connectivity across geographically dispersed facilities, allowing centralized control and oversight.
Unified Namespace (UNS) as a Real-Time Data Management Approach
The Unified Namespace (UNS) concept is emerging as a powerful approach to data management in Industry 4.0. A UNS acts as a centralized, real-time data repository that unifies information from all connected devices, systems, and applications. Unlike traditional architectures, where data may be siloed or flow in rigid pathways, UNS provides a flexible, real-time data environment accessible to all systems.
With UNS, companies achieve seamless interoperability, as all connected systems can access the same information in real-time without custom integrations. This simplifies system architectures, reduces data silos, and enables a single source of truth, allowing companies to implement real-time monitoring, analytics, and decision-making across the organization. UNS supports IT-OT convergence, facilitating cross-functional data sharing and collaboration.
Predictive Maintenance and Asset Performance Management Software
Predictive maintenance and asset performance management (APM) software are critical for optimizing equipment reliability and lifespan. Predictive maintenance software uses historical and real-time data to forecast equipment failure before it occurs. This approach minimizes unplanned downtime and maintenance costs by allowing companies to service equipment only when necessary rather than on fixed schedules.
APM software provides a broader scope by combining predictive maintenance with performance monitoring and asset health analytics. APM platforms offer insights into factors like energy usage, wear rates, and operational efficiency, helping organizations extend asset life, reduce costs, and achieve a higher return on asset investment. These solutions can significantly boost uptime, safety, and cost-efficiency by proactively managing equipment health.
Digital Twin Software and Simulation Platforms
Digital twin software creates a virtual replica of physical assets, systems, or processes. This digital model can be used to simulate various scenarios, assess potential changes, and optimize operations without impacting real-world production. In Industry 4.0, digital twins are increasingly used to improve design, production, and maintenance processes by providing a sandbox environment for experimentation and optimization.
Simulation platforms, often integrated with digital twin software, allow manufacturers to test new configurations, adjust process parameters, and foresee bottlenecks before they arise. For instance, a digital twin of a production line enables operators to experiment with changes in layout, staffing, or process flow, helping them identify the most efficient configuration. Digital twins support innovation, reduce downtime, and enhance process control.
Data Analytics and AI Platforms for Manufacturing
Data analytics and artificial intelligence (AI) platforms are essential tools for unlocking the value of big data in Industry 4.0. Data analytics enables manufacturers to process and interpret large volumes of data, identifying trends, patterns, and areas for improvement. AI platforms apply machine learning models to this data, enabling predictive capabilities such as demand forecasting, quality control, and anomaly detection.
For example, AI-powered predictive quality systems can analyze production data to identify subtle variations that could lead to defects, allowing operators to adjust parameters before quality issues arise. Data analytics and AI platforms empower manufacturers to make proactive, data-driven decisions that enhance operational efficiency, reduce costs, and improve product quality.
The Hardware Foundation for Industry 4.0
While software drives the data and intelligence in Industry 4.0, hardware forms the physical foundation that enables connectivity, automation, and real-time responsiveness. Industry 4.0 hardware comprises a range of components that work in tandem to capture data, perform computations, enable connectivity, and control production equipment. Below, we discuss the essential hardware components for Industry 4.0 and their role in creating an interconnected manufacturing environment.
Essential Hardware Components
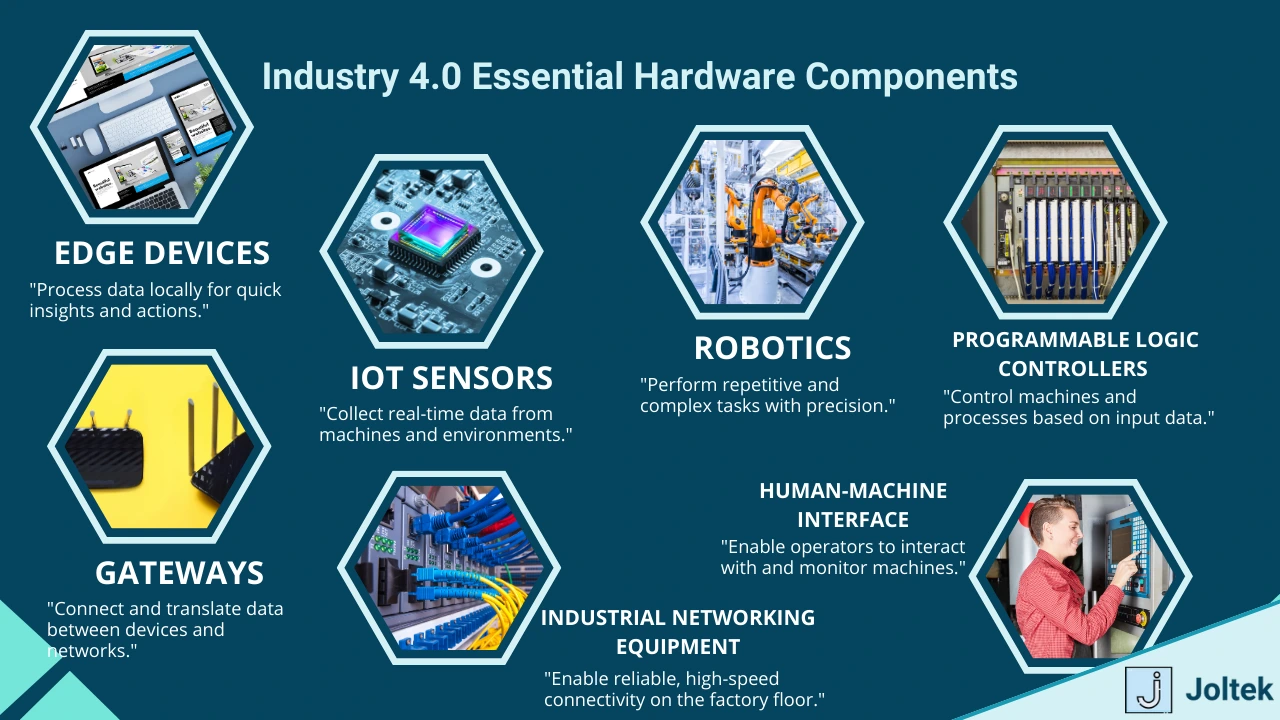
IoT Sensors
IoT sensors are critical to Industry 4.0, as they collect the raw data required to monitor, control, and optimize manufacturing processes. These sensors can measure various parameters, such as temperature, pressure, humidity, vibration, and location, providing insights into machine health, environmental conditions, and operational performance. Deployed across the factory floor, IoT sensors continuously feed data into Industrial IoT (IIoT) platforms or edge devices, enabling real-time visibility and data-driven decision-making.
In predictive maintenance, for example, vibration sensors monitor the health of rotating equipment, alerting operators to potential issues before they lead to failures. Temperature and humidity sensors can help control environmental conditions to ensure optimal storage and production conditions. As Industry 4.0 continues to evolve, sensor technology is becoming more sophisticated, with miniaturized, multi-sensor devices that deliver greater accuracy and reliability.
Edge Devices
Edge devices are computing resources located closer to the data source (i.e., the factory floor), enabling rapid processing and decision-making without the need to send data to the cloud. By processing data locally, edge devices reduce latency, alleviate network congestion, and allow for real-time response to changing conditions.
Edge devices often serve as intermediaries between IoT sensors and central data systems, filtering and aggregating data to provide actionable insights. For example, an edge device can run analytics models to detect anomalies in machine behavior, triggering an alert if an issue is detected. In addition to speed, edge computing also enhances data privacy and security by limiting the need to transfer sensitive data outside the local network.
Gateways
Gateways act as bridges between IoT sensors, edge devices, and cloud platforms, facilitating data communication across diverse protocols and systems. In Industry 4.0, gateways often perform protocol translation, data aggregation, and basic processing to ensure data from various sources can be integrated into a unified system.
Gateways are particularly useful in environments with legacy equipment, as they can connect older machines to modern networks, enabling them to participate in Industry 4.0 ecosystems. This role is crucial for manufacturers who want to maximize the utility of existing assets while integrating them into advanced data-driven architectures. Gateways also support network segmentation, enhancing security by isolating sensitive areas of the network.
Robotics
Robots play an increasingly important role in Industry 4.0 by automating repetitive tasks, enhancing productivity, and improving quality. Industrial robots, such as robotic arms, are commonly used in assembly, welding, and material handling, while collaborative robots (cobots) work alongside human operators to perform tasks in a shared workspace.
Robotics enables flexibility and scalability, as robots can be reprogrammed or adjusted to handle different products, allowing manufacturers to meet demand fluctuations. Robots integrated with IoT and AI systems can adapt to changing conditions, perform quality inspections in real-time, and even self-diagnose issues to minimize downtime. As robotic systems become more advanced, they will continue to enable lights-out manufacturing, where fully autonomous factories operate with minimal human intervention.
Industrial Automation Hardware
Programmable Logic Controllers (PLCs)
PLCs are industrial computers that monitor inputs and outputs to control machines and processes. In Industry 4.0, PLCs play a critical role by enabling automation and connecting production equipment with software systems like MES and SCADA. Modern PLCs are increasingly integrated with IoT capabilities, allowing them to communicate with other connected devices and share real-time data for monitoring and control.
PLCs provide flexibility in automating production lines, supporting complex sequences of operations and interfacing with sensors, actuators, and other control devices. This capability is essential for adaptive manufacturing environments where flexibility and scalability are key.
Human-Machine Interface (HMI)
Human-Machine Interfaces (HMI) are user interfaces that allow operators to interact with production equipment, monitor machine status, and control operations. HMIs display real-time data from PLCs and other control systems, providing a visual representation of production metrics, alarms, and diagnostics.
In Industry 4.0, HMIs are increasingly web-based and remotely accessible, allowing operators to monitor equipment from any location. Advanced HMIs also integrate with IoT platforms to present more detailed analytics, providing actionable insights directly on the operator’s screen. This enhances situational awareness, enabling quicker and more informed decision-making on the factory floor.
Distributed Control Systems (DCS) and SCADA Components
Distributed Control Systems (DCS) and SCADA (Supervisory Control and Data Acquisition) are used to control complex, large-scale processes. DCS are employed primarily in continuous process industries like oil and gas, where precise control of complex processes is critical, while SCADA is more common in discrete manufacturing and utility applications.
In an Industry 4.0 environment, SCADA and DCS systems connect with IoT and cloud platforms, allowing data to be collected, stored, and analyzed centrally. This integration enables real-time visibility into operations, remote monitoring, and better coordination across processes. SCADA and DCS systems often serve as the backbone of control in Industry 4.0, linking automation hardware with analytics platforms for a more cohesive production environment.
Connectivity Hardware
5G Routers
5G routers enable high-speed, low-latency connectivity, essential for real-time applications in Industry 4.0. With 5G, manufacturers can connect numerous IoT devices without significant network congestion, supporting applications that require large data transfers or ultra-low latency, such as real-time video monitoring, robotics, and augmented reality.
5G is also valuable for mobile equipment, such as automated guided vehicles (AGVs), allowing them to communicate seamlessly as they move around the facility. The bandwidth and reliability of 5G make it a preferred solution for future-ready connectivity in industrial environments.
Switches
Network switches enable data transfer between devices within a local area network (LAN). In Industry 4.0, switches support the connectivity needs of IoT sensors, edge devices, and control systems, ensuring fast and reliable data flow across the factory floor. Industrial-grade switches are designed to withstand harsh manufacturing conditions, offering robust and resilient networking capabilities.
Switches are often configured to enable network segmentation, creating isolated zones to enhance cybersecurity and prevent disruptions from spreading across the network. This layered approach to connectivity allows for efficient traffic management and data flow in complex manufacturing environments.
Industrial-Grade Wi-Fi
Industrial-grade Wi-Fi provides wireless connectivity for mobile devices, robots, and IoT sensors within manufacturing facilities. Unlike consumer-grade Wi-Fi, industrial-grade Wi-Fi is designed to operate reliably in environments with high interference, temperature extremes, and rugged conditions.
In Industry 4.0, wireless connectivity allows for greater flexibility, enabling mobile and handheld devices to access real-time data and applications from anywhere in the facility. It also supports workforce mobility, as operators can monitor and control equipment remotely using tablets or smartphones, contributing to faster decision-making and streamlined operations.
Integrating Hardware with Industry 4.0 Software Solutions
Integrating hardware with Industry 4.0 software is essential for achieving seamless data flow and creating a cohesive manufacturing ecosystem. Hardware components such as IoT sensors, PLCs, and edge devices generate data that flows into MES, ERP, SCADA, and IoT platforms. By establishing interoperability standards, such as the Unified Namespace (UNS), manufacturers can ensure that data from disparate hardware components is accessible across all software systems.
Edge devices and gateways serve as points of integration, allowing real-time data to be processed and transmitted to software platforms. To facilitate integration, companies may adopt standard protocols (e.g., OPC UA, MQTT) and platforms that enable hardware and software to work in concert, supporting real-time monitoring, control, and optimization. This integration creates a unified view of the factory, empowering decision-makers with actionable insights and adaptive control over operations.
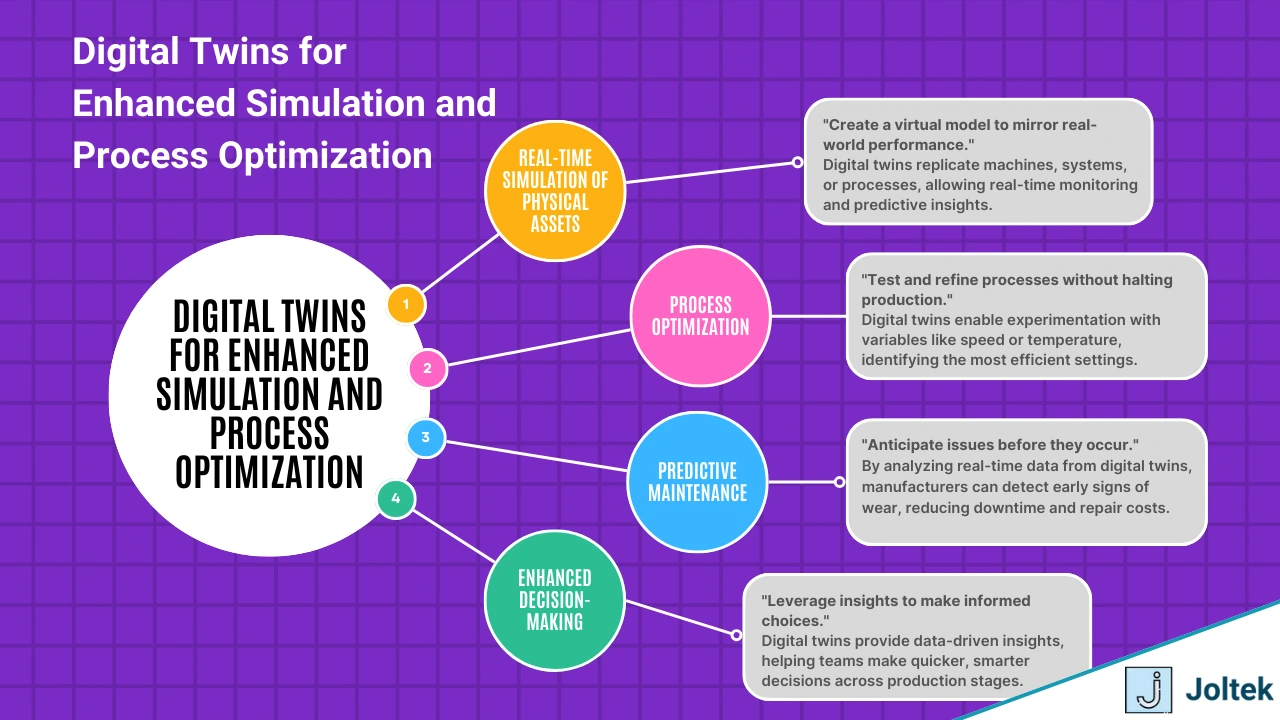
Choosing the Right Technology Stack and Vendor Ecosystem
Selecting the right technology stack and vendor ecosystem is a critical decision for any organization embarking on an Industry 4.0 transformation. The technology stack should support the company’s operational needs, strategic objectives, and growth potential while allowing for scalability, flexibility, and robust integration. This section outlines key considerations for evaluating software solutions, working with multiple vendors, selecting the right vendor, and building a tailored technology stack.
Evaluating Software Solutions Based on Scalability, Flexibility, and Integration Capabilities
When evaluating software solutions for Industry 4.0, companies should prioritize scalability, flexibility, and integration capabilities to ensure the solutions can adapt as operational requirements evolve.
- Scalability: Industry 4.0 transformation is typically a multi-phase journey, with new systems, data sources, and analytical requirements introduced over time. Scalable software solutions can grow alongside the organization, accommodating increasing volumes of data, users, and functionalities without requiring frequent replacements or upgrades. For example, cloud-based MES or IoT platforms can scale more readily than on-premises systems, allowing manufacturers to expand their digital capabilities as their operations grow.
- Flexibility: Flexible software solutions offer configurability and adaptability to unique operational needs. This is especially critical in manufacturing, where processes, products, and customer requirements vary widely across industries and even facilities. Flexible platforms support customization options, allowing companies to adapt workflows, interfaces, and reports according to their specific needs without extensive reprogramming.
- Integration Capabilities: Industry 4.0 demands seamless integration between multiple systems, from ERP and MES to IoT platforms and edge devices. Software solutions should support interoperability through standard protocols (e.g., OPC UA, MQTT) and APIs, enabling the exchange of data across platforms. Robust integration capabilities are essential to create a unified data environment, facilitate IT-OT convergence, and enable real-time insights across the organization.
Working with Multiple Vendors: Pros and Cons of Single vs. Multi-Vendor Strategies
When building an Industry 4.0 technology stack, companies often face a choice between a single-vendor strategy, where most solutions come from one provider, and a multi-vendor approach, where solutions from multiple providers are combined. Each approach has its pros and cons:
- Single-Vendor Strategy
- Pros: Streamlined integration and simplified management, as a single provider typically offers pre-integrated modules that work seamlessly together. Vendors may offer favorable pricing for bundled solutions and comprehensive support for all systems.
- Cons: Limited flexibility, as a single-vendor approach can lock companies into proprietary systems that may not be compatible with future technologies. It may also limit the ability to choose best-in-class solutions, as no single vendor excels in every area of Industry 4.0.
- Multi-Vendor Strategy
- Pros: Greater flexibility to select best-in-class solutions for each functional area, allowing the company to benefit from specialized capabilities. This approach can foster innovation by enabling the adoption of the latest technologies from various vendors.
- Cons: Increased complexity in managing multiple vendor relationships, contracts, and support agreements. Integration can be challenging, especially when systems are not inherently compatible, requiring custom development or middleware solutions to enable interoperability.
Selecting between single and multi-vendor strategies depends on factors such as the company’s size, technical expertise, budget, and long-term digital goals. Some organizations may adopt a hybrid approach, using a core platform from one vendor while integrating additional tools from other providers to meet specific needs.
Key Factors for Vendor Selection: Support, Interoperability, and Future-Proofing
Choosing the right vendor goes beyond evaluating the software itself; it also requires a comprehensive assessment of the vendor’s overall value proposition, which includes support, interoperability, and future-proofing.
- Support: The level of technical support a vendor provides can be a determining factor in the success of Industry 4.0 implementations. Companies should look for vendors that offer extensive onboarding, training, troubleshooting, and ongoing support to help resolve issues quickly. Additionally, access to dedicated account managers and industry-specific expertise can add significant value, ensuring the company maximizes the potential of its technology investment.
- Interoperability: Vendors that prioritize interoperability are more likely to support the seamless integration of their solutions with third-party platforms, legacy systems, and future technologies. Companies should inquire about the vendor’s approach to interoperability, such as adherence to open standards and the availability of APIs, as this ensures that the solution can fit within a broader Industry 4.0 ecosystem.
- Future-Proofing: Digital transformation is an ongoing process, so it is essential to select vendors committed to continuous improvement and innovation. Companies should assess whether the vendor actively invests in R&D, regularly releases updates, and stays ahead of emerging industry trends. Vendors with a roadmap aligned with the company’s vision provide confidence that the solution will remain relevant and competitive over time.
Selecting a vendor also involves evaluating factors such as the vendor’s financial stability, industry reputation, customer references, and alignment with the company’s values and goals.
Creating a Best-Fit Technology Stack Tailored to the Company's Maturity Level and Goals
Building a technology stack that aligns with the company’s digital maturity and strategic goals ensures that investments in Industry 4.0 will yield long-term value. Here’s a step-by-step approach to creating a tailored technology stack:
- Assess Digital Maturity: Evaluate the company’s current capabilities, infrastructure, and workforce readiness to adopt new technologies. This assessment helps identify gaps in the existing setup and informs the choice of solutions that align with the company’s digital maturity.
- Define Strategic Goals: Clear, specific goals help guide technology stack choices. For example, if a company’s primary objective is predictive maintenance, the technology stack should include advanced sensors, edge devices, predictive analytics software, and an IIoT platform.
- Select Core and Supporting Solutions: The technology stack should be structured with core solutions (e.g., MES, ERP, IoT platforms) that form the backbone of Industry 4.0, as well as supporting solutions (e.g., AI and analytics tools, cybersecurity systems) that enhance these core functions. Each component should be chosen for its ability to contribute to strategic goals.
- Plan for Phased Implementation: Digital transformation can be overwhelming if tackled all at once. Companies can adopt a phased approach, starting with foundational technologies and gradually adding advanced capabilities. This allows for smoother integration and enables teams to build expertise over time.
- Prioritize Interoperability and Flexibility: Building a technology stack with interoperable, flexible solutions enables companies to adapt to changing needs, integrate new technologies, and avoid vendor lock-in. Open standards, modular architectures, and API-driven integration approaches support this flexibility.
- Incorporate Robust Cybersecurity Measures: Cybersecurity should be integrated into every layer of the technology stack, from IoT devices and networks to cloud platforms and data analytics. This proactive approach ensures that data, assets, and production processes are protected as the technology stack evolves.
- Continuously Evaluate and Optimize: The Industry 4.0 landscape evolves rapidly, so companies should regularly assess the performance and relevance of each component within the stack. This ongoing evaluation ensures that the technology stack continues to meet the company’s needs and incorporates advancements in the field.
The Role of Data and Analytics in Industry 4.0
Data and analytics are at the core of Industry 4.0, enabling manufacturers to gain insights into operations, optimize processes, and drive proactive decision-making. This section covers the importance of data management, strategies for effective data handling, and the challenges associated with legacy systems.
The Importance of Data Collection, Standardization, and Contextualization
Data collection is the first step in realizing the benefits of Industry 4.0. By gathering data from various sources—such as sensors, machines, production lines, and ERP systems—manufacturers can gain a comprehensive view of their operations. However, raw data alone is not sufficient; it must be standardized and contextualized to make it meaningful and actionable.
- Standardization: Standardizing data involves ensuring consistency in data format, units, and naming conventions. This consistency is crucial for combining data from different sources and making it usable across various applications, such as analytics platforms or AI models. Standardized data also facilitates interoperability, enabling information exchange between systems and reducing compatibility issues.
- Contextualization: Contextualization involves adding meaning to raw data by linking it with relevant metadata, such as time, location, machine type, or production batch. For example, temperature data is more valuable if it includes context about the specific machine, process stage, or material being processed. Contextualized data helps manufacturers make sense of complex information and derive insights that are specific to each process or asset.
Standardization and contextualization transform raw data into a valuable resource, allowing companies to build a unified data foundation for analytics and decision-making.
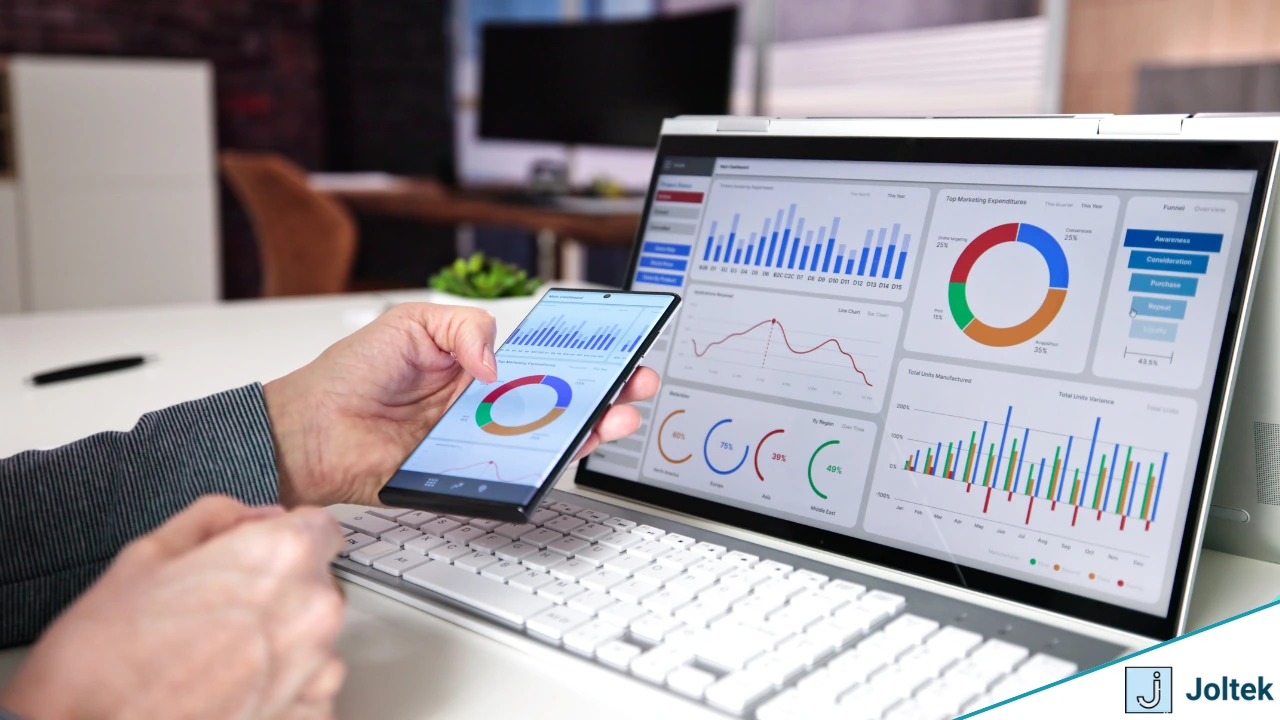
Building a Data Strategy: Collection, Storage, Processing, and Analysis
A well-defined data strategy outlines how an organization will manage data throughout its lifecycle, from collection to analysis. A robust data strategy typically includes the following stages:
- Collection: Identify key data sources, such as IoT sensors, MES, SCADA, and ERP systems. Determine the types of data required, such as machine health, production rates, environmental conditions, or energy usage. Ensure that data collection is reliable, continuous, and secure, with appropriate mechanisms for managing and storing high data volumes.
- Storage: Select appropriate storage solutions that balance capacity, speed, and cost. Data lakes and cloud storage solutions are commonly used in Industry 4.0 to handle large volumes of unstructured data, providing flexibility for future analysis. The storage infrastructure should support both real-time and historical data access, enabling in-depth analysis and trend identification.
- Processing: Processing involves transforming raw data into a structured format for analysis, which may include data cleaning, aggregation, and contextualization. In Industry 4.0, edge processing is often employed to perform basic analytics close to the source, allowing immediate action in latency-sensitive applications. Cloud and centralized platforms are used for more complex processing tasks, such as training AI models or conducting deep historical analysis.
- Analysis: Data analysis transforms processed data into actionable insights. This stage includes real-time monitoring, predictive analytics, anomaly detection, and root cause analysis. By analyzing both real-time and historical data, manufacturers can identify patterns, forecast demand, optimize processes, and improve overall operational efficiency. The results of these analyses drive continuous improvement and proactive decision-making.
A comprehensive data strategy ensures that companies can harness the full potential of their data, supporting informed decision-making across all levels of the organization.
Overcoming Data Silos with Centralized Data Management
Data silos occur when information is isolated within departments, systems, or locations, preventing cross-functional access and analysis. In Industry 4.0, overcoming data silos is crucial for creating a connected, transparent, and data-driven manufacturing environment. Centralized data management strategies are key to breaking down silos and achieving a holistic view of operations.
- Unified Namespace (UNS): UNS is an approach to creating a central, real-time data repository that integrates data from all connected systems and devices. By establishing a single source of truth, UNS enables real-time access to data across the organization, facilitating collaboration and cross-functional insights.
- Data Lakes: Data lakes are centralized storage solutions designed to handle vast amounts of structured and unstructured data. Data lakes allow companies to store raw data from various sources, enabling cross-functional teams to access, analyze, and derive insights from the same data pool. Data lakes are particularly useful for advanced analytics and machine learning applications that require diverse data sources.
- APIs and Middleware: Application Programming Interfaces (APIs) and middleware solutions enable data exchange between disparate systems, facilitating integration without requiring extensive reprogramming. By implementing APIs, manufacturers can connect legacy systems with modern platforms, enabling data sharing and interoperability.
Centralized data management not only breaks down data silos but also enhances data accessibility, enabling decision-makers at all levels to leverage comprehensive, real-time information.
Real-Time Analytics and Decision-Making
One of the most significant advantages of Industry 4.0 is the ability to analyze data in real time, empowering organizations to respond instantly to changing conditions. Real-time analytics allows manufacturers to monitor key performance indicators (KPIs), detect anomalies, and make informed decisions as events unfold.
- Anomaly Detection and Alerts: Real-time analytics can identify deviations from expected patterns, such as abnormal temperature fluctuations, unusual machine vibrations, or unexpected production delays. By detecting anomalies early, manufacturers can address potential issues before they escalate, reducing downtime and minimizing production losses.
- Process Optimization: Real-time data enables dynamic adjustments to production parameters, such as adjusting machine speeds, temperatures, or materials based on live feedback. This immediate optimization capability leads to higher productivity, reduced waste, and improved product quality.
- Predictive Maintenance: Real-time data, combined with predictive analytics, allows manufacturers to anticipate equipment failures before they happen. Predictive maintenance uses real-time sensor data to monitor equipment health and detect early signs of wear or failure, enabling proactive repairs and minimizing unplanned downtime.
Real-time analytics enhances operational agility, enabling manufacturers to stay responsive, proactive, and resilient in dynamic environments.
The Challenge of Unmodernized Systems and Data Access
Despite the advantages of Industry 4.0, many manufacturing environments still rely on legacy systems that were not designed for digital connectivity. These unmodernized systems present challenges for data collection, integration, and analysis:
- Limited Connectivity: Older systems, such as legacy PLCs or standalone machines, may lack built-in connectivity, making it difficult to integrate them with modern IoT platforms. Retrofitting legacy equipment with IoT sensors or edge devices can help bridge this gap, allowing companies to capture data from older assets.
- Incompatible Protocols: Legacy systems may use proprietary or outdated communication protocols that are incompatible with modern networks. Gateways and middleware solutions can perform protocol translation, enabling data exchange between legacy equipment and Industry 4.0 systems.
- Data Fragmentation: Older systems often operate in isolation, leading to fragmented data that cannot be easily accessed or combined. Centralizing this data requires custom integrations or data aggregation tools that can pull information from disparate sources into a unified platform.
- Cost and Complexity of Upgrades: Upgrading or replacing legacy systems to be Industry 4.0-compatible can be costly and disruptive. Many manufacturers adopt a phased approach, gradually modernizing equipment and systems as part of their digital transformation strategy. Alternatively, edge devices and data collection solutions can be used to extract data from legacy systems without major upgrades.
Addressing the challenges of unmodernized systems is essential for achieving a connected, data-driven environment in Industry 4.0. Companies that find effective solutions for data access and integration can unlock the value of data across all their assets, from the latest IoT devices to decades-old machines.
Implementation and Integration: Challenges and Solutions
The success of Industry 4.0 depends on effective implementation and integration across systems, departments, and processes. This section addresses common challenges, strategies for IT-OT convergence, integration architecture best practices, and lessons from real-world implementations.
Overcoming Legacy System Integration Challenges
Legacy systems, often lacking connectivity and modern protocols, pose significant obstacles to Industry 4.0 transformation. However, manufacturers can employ several strategies to integrate these systems with newer technologies:
- IoT Gateways and Protocol Converters: IoT gateways bridge the gap between legacy equipment and modern Industry 4.0 platforms. Protocol converters allow older systems using proprietary or outdated protocols (e.g., MODBUS, Profibus) to communicate with modern IoT platforms using standardized protocols such as OPC UA or MQTT.
- Retrofitting and Edge Devices: Retrofitting legacy equipment with IoT sensors and edge devices enables data collection without altering the original equipment. Edge devices can process and transmit data from legacy systems to cloud or centralized platforms, enabling real-time monitoring and control. This approach minimizes disruption and provides a cost-effective way to modernize operations.
- Middleware Solutions: Middleware platforms aggregate and integrate data from disparate systems, allowing for interoperability across new and legacy systems. By acting as an intermediary, middleware solutions can connect legacy systems with modern applications, centralizing data access and enhancing compatibility.
- Phased Modernization: Rather than replacing all legacy equipment at once, companies can adopt a phased approach, gradually upgrading or replacing outdated systems as budgets and operational constraints allow. Phased modernization balances the need for technological advancement with practical considerations, reducing the impact on production and minimizing costs.
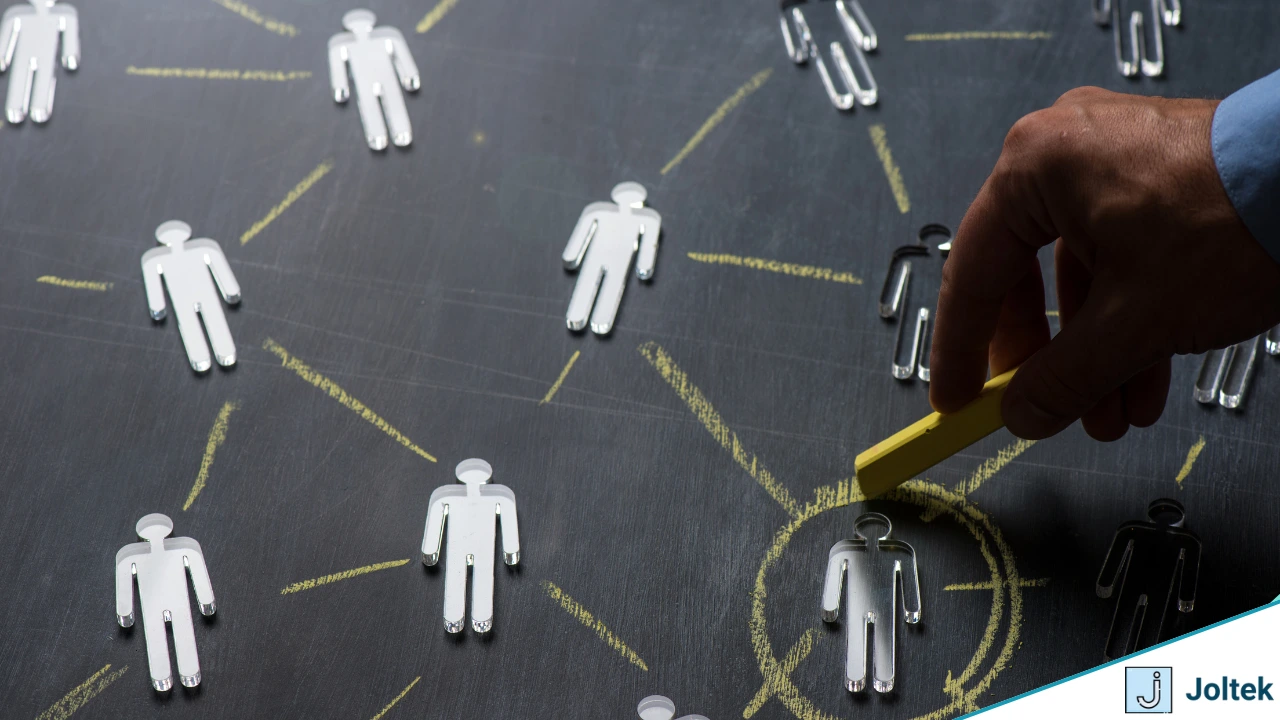
IT-OT Convergence: Bridging Gaps Between Information Technology and Operational Technology
In traditional manufacturing environments, Information Technology (IT) and Operational Technology (OT) have operated separately, each with its own priorities, systems, and objectives. IT-OT convergence is essential in Industry 4.0, as it allows data to flow seamlessly between the enterprise and the factory floor, creating a unified environment for real-time decision-making.
- Cultural Alignment: One of the primary challenges of IT-OT convergence is cultural. IT focuses on data security, standardization, and enterprise-level applications, while OT prioritizes safety, machine control, and production efficiency. To bridge this gap, organizations can establish cross-functional teams, hold regular workshops, and promote communication between IT and OT professionals. Clear alignment on shared goals and mutual understanding of each team’s priorities can foster a more collaborative environment.
- Unified Data Standards: Implementing standardized data protocols, such as OPC UA, MQTT, or UNS, allows IT and OT systems to communicate seamlessly. These standards enable interoperability and help create a single source of truth across the organization, reducing data silos and improving transparency.
- Security and Compliance: As IT and OT systems converge, cybersecurity becomes more complex. OT systems that were once isolated are now exposed to potential cyber threats. To mitigate these risks, organizations should implement robust security measures, such as network segmentation, access control, and continuous monitoring. Collaborating on security standards ensures that both IT and OT priorities are addressed without compromising safety or production.
Setting Up a Scalable Integration Architecture
A scalable integration architecture is essential for handling the increasing volume and complexity of data in Industry 4.0 environments. Here are some best practices for setting up such an architecture:
- Modular Design: Modular architectures allow manufacturers to add or remove components as needed, adapting to changing requirements without overhauling the entire system. For example, a modular approach might involve separate modules for data ingestion, processing, and analytics, each of which can scale independently.
- Data Lake for Centralized Storage: Data lakes provide a scalable storage solution that can handle raw, structured, and unstructured data from various sources. By storing data in a centralized repository, organizations can break down data silos and enable cross-functional access, supporting advanced analytics and machine learning applications.
- Edge Computing for Distributed Processing: Edge computing enables data processing closer to the source, reducing latency and alleviating the burden on central servers. A hybrid approach—combining edge and cloud computing—allows organizations to process time-sensitive data at the edge while sending less critical data to the cloud for deeper analysis.
- Unified Namespace (UNS): The UNS approach creates a real-time data repository that integrates data from all connected devices, systems, and applications. UNS allows multiple systems to access shared data in real-time, providing flexibility and facilitating cross-functional decision-making. It also simplifies system architectures by reducing the need for point-to-point integrations.
Case Studies of Successful Implementations
Case Study 1: Predictive Maintenance in Automotive Manufacturing An automotive manufacturer implemented predictive maintenance by integrating legacy machines with IoT sensors and an AI-powered analytics platform. Retrofitting legacy equipment with sensors enabled real-time data collection on temperature, vibration, and other critical parameters. By using edge computing for local data processing and sending aggregated data to the cloud, the company reduced downtime by 20%, saving millions in maintenance costs.
Case Study 2: IT-OT Convergence in Food and Beverage Production A food and beverage company integrated its ERP and MES systems to improve production scheduling and quality control. By implementing OPC UA and MQTT protocols, the company enabled real-time data exchange between IT and OT systems. The integration facilitated better visibility into production metrics, allowing for dynamic adjustments based on demand. The project improved production efficiency by 15% and reduced waste by aligning scheduling with inventory levels and production capacity.
Case Study 3: Data Lake and Advanced Analytics in Pharmaceutical Manufacturing A pharmaceutical manufacturer implemented a data lake to centralize data from its lab equipment, MES, and ERP systems. By using data analytics on this centralized repository, the company improved its product quality monitoring and compliance reporting. The data lake allowed for real-time monitoring of process parameters and enabled predictive quality analytics, resulting in fewer deviations and increased compliance.
Common Pitfalls and How to Avoid Them
- Insufficient Change Management: Industry 4.0 transformation requires significant changes in workflows, processes, and culture. Without effective change management, resistance to new technologies can hinder adoption. Companies should engage stakeholders early, provide adequate training, and communicate the benefits of the transformation to gain buy-in.
- Overlooking Cybersecurity: Integrating IT and OT systems exposes production environments to cybersecurity risks. Failing to implement adequate cybersecurity measures can lead to vulnerabilities. Organizations should adopt a proactive cybersecurity strategy, including network segmentation, regular vulnerability assessments, and strict access controls.
- Lack of Clear Goals and KPIs: Implementing Industry 4.0 technologies without clear goals or performance metrics can lead to misaligned priorities and wasted resources. Companies should establish specific objectives, such as reducing downtime or improving yield, and define KPIs to measure progress.
- Data Silos and Inconsistent Standards: Data silos can prevent seamless data flow and limit cross-functional insights. Adopting consistent data standards and centralized data management solutions, such as data lakes or UNS, can mitigate this issue and enable interoperability across systems.
- Underestimating Integration Complexity: Industry 4.0 involves integrating numerous systems and devices, which can be more complex than anticipated. Working with experienced partners or consultants can help manufacturers plan and execute integration more effectively, reducing delays and improving outcomes.
The People Factor: Building a Skilled Workforce
People are at the heart of Industry 4.0 transformation. While advanced technologies and interconnected systems enable new capabilities, a skilled and adaptable workforce is essential for sustaining progress. This section explores strategies for addressing skill gaps, fostering a learning culture, building interdisciplinary teams, and implementing training programs that support digital transformation.
Skill Gaps and Workforce Development for Industry 4.0
As manufacturing shifts towards digital, data-centric processes, traditional skills must be supplemented with new competencies in data analytics, digital tools, cybersecurity, and automation. Some of the critical skill gaps in Industry 4.0 include:
- Data Analytics and Machine Learning: Understanding data is essential for optimizing processes, predictive maintenance, and real-time decision-making. Skilled personnel are needed to interpret data, build and manage analytics models, and develop AI applications that support production.
- Cybersecurity: With IT-OT convergence, cybersecurity is a top priority in protecting interconnected systems. Manufacturing teams need cybersecurity expertise to safeguard operations, handle data security challenges, and ensure compliance with security standards.
- IoT and Connected Devices: Knowledge in IoT architecture, sensors, and connectivity protocols is critical to deploying and managing Industry 4.0 systems effectively. Skills in IoT device management, edge computing, and integration with existing networks are essential for maintaining a connected manufacturing environment.
- Software Development and Programming: Many Industry 4.0 applications require custom software configurations or integrations. Skills in programming, particularly for automation languages (e.g., Python, PLC programming), are valuable for managing and customizing applications, optimizing workflows, and adapting systems as needs evolve.
To address these skill gaps, companies can invest in hiring new talent with these competencies and developing internal workforce skills through targeted training programs. Collaborating with universities, industry groups, and technical schools can also help companies access emerging talent and bridge skills gaps over the long term.
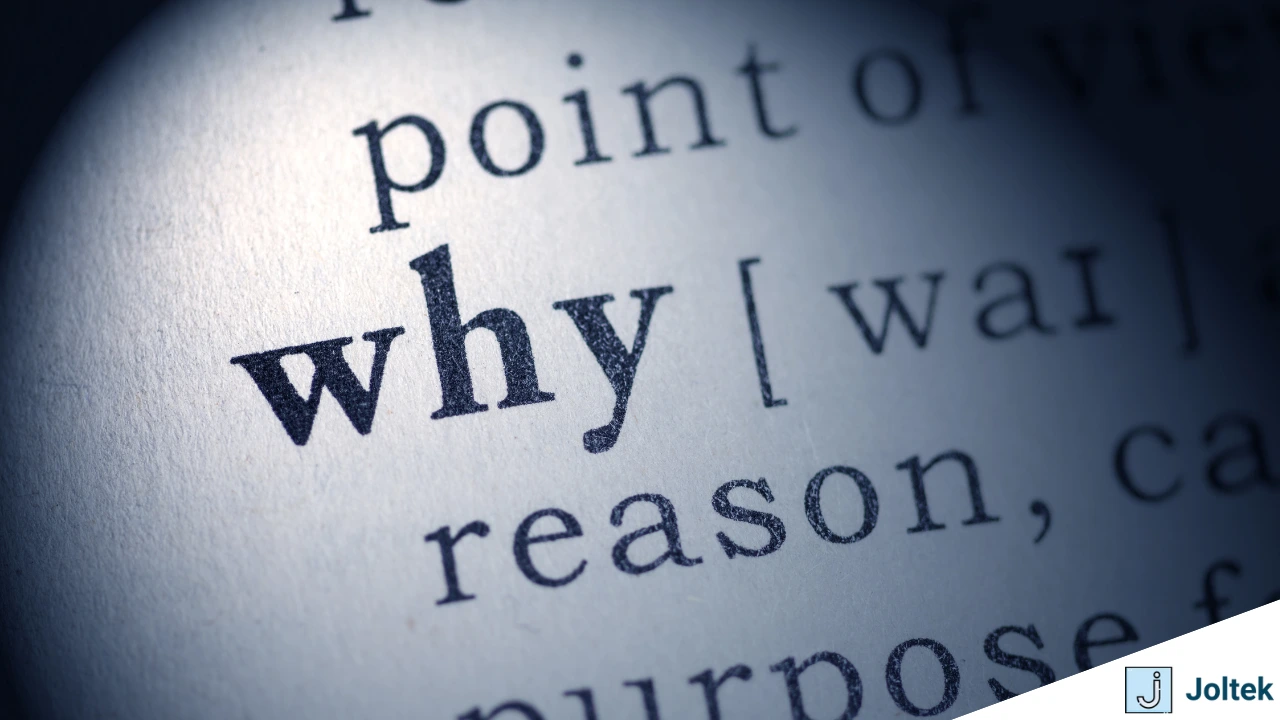
Creating a Culture of Continuous Learning and Innovation
A culture of continuous learning is essential for thriving in an Industry 4.0 environment. As technologies evolve, companies must foster a mindset that embraces change, innovation, and skill development. Strategies for building a learning culture include:
- Encouraging Experimentation: Encourage employees to explore new tools, pilot new methods, and experiment with innovative ideas. By providing a safe environment for testing and learning, companies can uncover creative solutions and empower employees to drive improvements.
- Incentivizing Learning and Development: Recognize and reward employees who pursue skill development and contribute to the organization’s digital goals. Incentives can include performance bonuses, promotions, or public recognition, motivating employees to invest in their growth and align with the company’s transformation objectives.
- Leadership Commitment: Leaders play a crucial role in establishing a learning culture by demonstrating openness to new ideas and committing resources to learning and development initiatives. When executives prioritize training and innovation, employees are more likely to see these values as central to the organization’s mission.
Fostering a culture of continuous learning and innovation ensures that employees are adaptable and engaged, helping companies navigate technological change more effectively.
Importance of Interdisciplinary Teams in Digital Transformation
Industry 4.0 initiatives require collaboration across disciplines, including engineering, IT, data science, and operations. Interdisciplinary teams are essential because they bring together diverse expertise, enabling comprehensive approaches to complex challenges. Key benefits of interdisciplinary teams include:
- Holistic Problem Solving: Bringing together IT, OT, and data specialists allows teams to approach challenges from multiple perspectives, leading to more effective and sustainable solutions. For example, an interdisciplinary team can address both the technical and operational implications of integrating new IoT devices into legacy systems.
- Improved Communication and Collaboration: Digital transformation often involves bridging the gap between IT and OT departments, as well as between technical and non-technical staff. Interdisciplinary teams create a natural platform for these interactions, promoting knowledge sharing and building trust.
- Faster Decision-Making: When multiple experts collaborate on a project, they can address questions, resolve conflicts, and make decisions more quickly. Interdisciplinary teams are often more agile and capable of adapting to changes, which is critical in fast-paced manufacturing environments.
To build effective interdisciplinary teams, companies should select members with complementary skills, designate clear roles and responsibilities, and provide team-building support to enhance collaboration. These teams can drive digital transformation projects, such as implementing new analytics tools, piloting automation solutions, or improving data integration practices.
Training and Upskilling Programs for Existing Employees
Upskilling current employees is a cost-effective and practical way to build a skilled workforce for Industry 4.0. Training programs help employees adapt to new roles and prepare for the technological demands of the future. Effective training and upskilling programs include:
- Technical Training: Offer targeted training in areas such as data analytics, cybersecurity, IoT, and programming. Training can take various forms, including workshops, certifications, online courses, and hands-on practice. Partnerships with educational institutions and industry training providers can expand access to high-quality technical training.
- Soft Skills Development: Industry 4.0 transformation requires employees to be adaptable, collaborative, and innovative. Training in critical thinking, problem-solving, project management, and communication skills helps employees work effectively in interdisciplinary teams and respond to new challenges.
- On-the-Job Learning: Encourage employees to learn on the job by participating in digital transformation projects or job rotations that expose them to new skills and processes. On-the-job learning can be reinforced with mentorship programs, where experienced employees or specialists guide others in skill development.
- Micro-Learning Modules: To accommodate busy schedules, companies can offer short, focused learning sessions or micro-learning modules on specific Industry 4.0 topics. These can be delivered via mobile or online platforms, allowing employees to engage in continuous learning without disrupting daily responsibilities.
- Certification Programs: Certification programs in specialized areas, such as IoT, cybersecurity, or data science, validate employees’ skills and provide a structured learning pathway. Industry-recognized certifications also build confidence and credibility, demonstrating that the company is committed to maintaining a highly skilled workforce.
Investing in training and upskilling programs helps companies retain experienced employees, fills critical skill gaps, and fosters loyalty by demonstrating a commitment to employee growth.
Security and Compliance in Industry 4.0 Software
The interconnected nature of Industry 4.0 environments introduces new cybersecurity risks and compliance requirements. As manufacturers connect systems, devices, and data, they expose their operations to potential threats that can impact data integrity, operational continuity, and regulatory compliance. This section explores key cybersecurity challenges, best practices for protecting data, compliance considerations, and the role of third-party vendors in maintaining security.
Cybersecurity Challenges and Best Practices for Industry 4.0
Industry 4.0 environments face complex cybersecurity challenges due to the integration of IT and OT systems, reliance on IoT devices, and increased data exchange between networks. Key challenges include:
- IT-OT Convergence Risks: The convergence of IT and OT systems opens up vulnerabilities in traditionally isolated OT environments. As OT systems (e.g., SCADA, PLCs) connect to enterprise networks, they become exposed to cybersecurity threats typically associated with IT, such as malware, ransomware, and unauthorized access.
- IoT Device Security: IoT devices in manufacturing are often deployed with minimal security measures, making them susceptible to attacks. Many IoT devices lack robust authentication, encryption, and update mechanisms, leaving them vulnerable to cyber threats.
- Data Privacy and Integrity: With Industry 4.0, data is constantly collected, processed, and transmitted across networks, creating risks to data privacy and integrity. Unauthorized access to sensitive production data can result in competitive disadvantage, compromised intellectual property, or even safety risks in critical industries.
Best Practices for Industry 4.0 Cybersecurity:
- Network Segmentation: Divide the network into isolated segments (e.g., IT, OT, IoT) to prevent unauthorized access to sensitive areas. Network segmentation minimizes the impact of a security breach by containing it within a specific segment.
- Multi-Factor Authentication (MFA): Implement MFA for all critical systems to ensure that only authorized personnel have access to sensitive information. This reduces the risk of unauthorized access even if login credentials are compromised.
- Regular Security Audits: Conduct regular vulnerability assessments and penetration testing to identify potential security weaknesses. Security audits help ensure that all systems, devices, and protocols are up to date and compliant with security standards.
- Patch Management: Keep all devices and systems updated with the latest security patches to address known vulnerabilities. A patch management policy helps protect against malware and exploits that target unpatched systems.
- Employee Training: Train employees on cybersecurity best practices, including phishing prevention, safe handling of sensitive data, and recognizing potential threats. Awareness programs strengthen the human aspect of cybersecurity by reducing accidental vulnerabilities.
- Zero Trust Architecture: Implement a zero-trust approach where every user, device, and application must authenticate and be verified continuously. This strategy enhances security by assuming that no entity is trusted by default, minimizing risks in a highly interconnected environment.
Protecting Data Integrity and Preventing Unauthorized Access
Protecting data integrity and preventing unauthorized access are fundamental to securing Industry 4.0 environments. Since data is at the heart of decision-making, predictive maintenance, and quality control, maintaining its accuracy and confidentiality is essential. Strategies for protecting data integrity and access include:
- Encryption: Encrypt data both at rest and in transit to ensure that unauthorized parties cannot access it. Data encryption protects sensitive information, including operational metrics, product specifications, and customer data, from interception or theft.
- Access Control Policies: Implement role-based access controls (RBAC) to limit user permissions based on job roles and responsibilities. Access control policies ensure that only authorized personnel can access critical systems, reducing the risk of insider threats and accidental data exposure.
- Data Integrity Monitoring: Use data integrity monitoring tools to detect unauthorized modifications, deletions, or corruptions in data. These tools can alert security teams to suspicious activities, allowing for immediate investigation and remediation.
- Auditing and Logging: Maintain logs of all access and data transactions, and regularly audit these logs for irregularities. Auditing provides a clear record of activities that can be used to trace unauthorized access and support compliance with regulatory requirements.
Compliance Requirements in Different Manufacturing Industries
Different manufacturing industries have specific compliance requirements to protect product quality, safety, and data privacy. Some of the most common compliance standards and regulations include:
- GDPR (General Data Protection Regulation): GDPR is applicable to companies that handle personal data of individuals within the European Union. For manufacturers, this means ensuring that employee and customer data collected in Industry 4.0 systems is securely stored, processed with consent, and accessible only to authorized personnel.
- NIST Cybersecurity Framework: The National Institute of Standards and Technology (NIST) framework provides guidelines for improving cybersecurity practices across critical infrastructure sectors, including manufacturing. It offers best practices for risk assessment, incident response, and continuous improvement in cybersecurity.
- ISO/IEC 27001: ISO 27001 is an international standard for information security management, specifying requirements for establishing, implementing, and maintaining an information security management system (ISMS). Compliance with ISO 27001 demonstrates that a manufacturer has established robust controls to protect sensitive information.
- Industry-Specific Standards (e.g., FDA for Pharmaceuticals, CISA for Critical Infrastructure): Regulated industries like pharmaceuticals, food and beverage, and energy must adhere to additional standards that address both cybersecurity and operational safety. For example, the FDA’s regulations for pharmaceutical manufacturers require strict data integrity and traceability to ensure product safety and efficacy.
Manufacturers should understand the compliance standards applicable to their industry and implement policies, procedures, and technologies that ensure adherence to these regulations. Non-compliance can lead to financial penalties, reputational damage, and operational disruptions.
Role of Third-Party Vendors and Consultants in Ensuring Security
Third-party vendors and consultants play a critical role in helping manufacturers meet Industry 4.0 security and compliance requirements. Their expertise and resources can supplement in-house capabilities, ensuring that security is integrated effectively at every stage of Industry 4.0 transformation.
- Security Assessments and Audits: External security experts can conduct assessments to evaluate vulnerabilities, assess risks, and identify areas for improvement. These assessments provide an objective view of the organization’s security posture and highlight specific actions for enhancement.
- Implementation of Security Solutions: Third-party vendors often offer specialized cybersecurity solutions, such as firewalls, intrusion detection systems, and identity management platforms, that protect Industry 4.0 environments. Their solutions may include advanced features that integrate seamlessly with Industry 4.0 systems and address unique manufacturing requirements.
- Compliance Guidance: Navigating compliance requirements can be challenging, especially in highly regulated industries. Compliance consultants can help organizations interpret and implement standards like GDPR, NIST, and ISO 27001, providing guidance on best practices and required documentation.
- Incident Response and Recovery: In the event of a cybersecurity incident, third-party security firms can provide support for incident response, containment, and recovery. This includes threat analysis, root cause identification, and implementing measures to prevent future incidents. Incident response services help manufacturers minimize downtime and mitigate the impact of security breaches.
- Continuous Monitoring and Threat Intelligence: Some vendors offer managed security services, providing continuous monitoring, threat intelligence, and proactive threat detection. By outsourcing security monitoring to specialized firms, manufacturers benefit from real-time protection and insights into emerging threats without requiring extensive in-house resources.
Partnering with trusted third-party vendors and consultants provides manufacturers with access to specialized expertise, advanced security tools, and compliance support, enhancing overall security resilience.
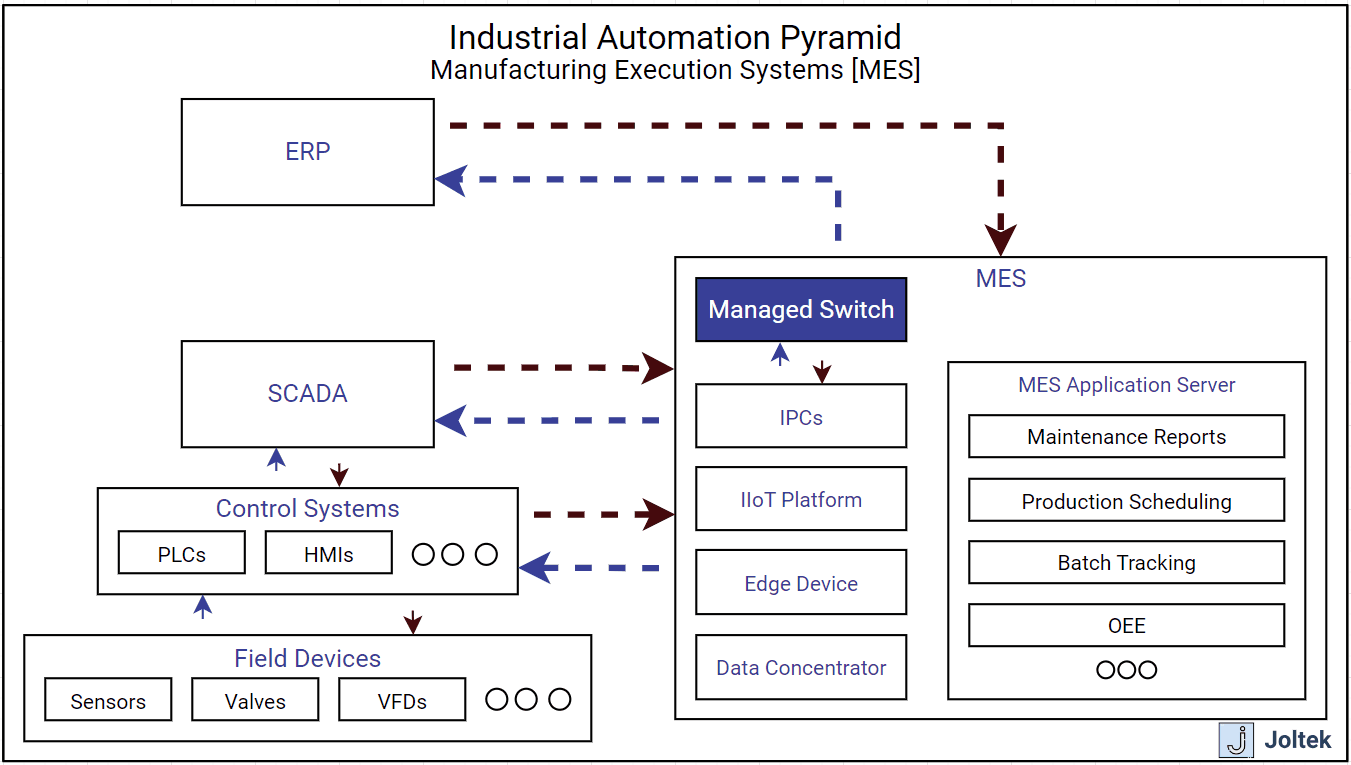
Measuring ROI and Business Outcomes of Industry 4.0 Software
Measuring the return on investment (ROI) and business outcomes of Industry 4.0 software is critical for decision-makers who need to justify investments, track performance, and demonstrate value to stakeholders. This section covers key performance indicators (KPIs), impact analysis, long-term benefits, and strategies for showing ROI.
Defining KPIs and Metrics for Tracking Industry 4.0 Success
Key performance indicators (KPIs) enable manufacturers to quantify the impact of Industry 4.0 initiatives. Effective KPIs should align with the organization’s strategic goals and provide actionable insights. Common KPIs in Industry 4.0 include:
- Operational Efficiency: Metrics like overall equipment effectiveness (OEE), cycle time, and lead time help measure improvements in production efficiency. OEE, for example, provides insight into equipment performance by factoring in availability, performance, and quality.
- Downtime Reduction: Tracking unplanned downtime helps assess the impact of predictive maintenance and real-time monitoring. By comparing downtime before and after implementing Industry 4.0 solutions, companies can quantify efficiency gains.
- Energy Consumption: Energy metrics, such as energy cost per unit produced, support both sustainability goals and cost reduction efforts. Monitoring energy usage allows companies to identify areas for improvement and assess the effectiveness of energy-saving initiatives.
- Product Quality: Metrics like defect rate, rework rate, and first-pass yield are used to measure product quality. Industry 4.0 software, particularly with AI-driven quality inspections, can improve defect detection and reduce rework, enhancing product quality.
- Supply Chain Metrics: Supply chain agility and efficiency can be measured through metrics like inventory turnover, order fulfillment time, and on-time delivery. Real-time data from ERP and IoT systems supports end-to-end supply chain visibility, optimizing inventory levels and reducing lead times.
Defining KPIs and setting baseline measurements help organizations track progress over time, ensuring that Industry 4.0 initiatives align with and contribute to their overarching business goals.
Financial and Operational Impact Analysis
Quantifying the financial and operational impact of Industry 4.0 software is essential to understanding its ROI. Impact analysis includes calculating cost savings, productivity gains, and revenue growth directly attributed to the new software. Key considerations include:
- Cost Savings: Cost savings can come from reduced downtime, improved resource utilization, and streamlined processes. For example, predictive maintenance reduces repair costs and minimizes disruptions, while real-time monitoring improves energy efficiency, cutting utility expenses.
- Productivity Gains: Productivity gains can be measured by evaluating increased throughput, reduced cycle times, and enhanced workforce efficiency. For instance, automated workflows enable production teams to complete tasks faster and with fewer resources, increasing output per hour.
- Revenue Growth: Industry 4.0 solutions can drive revenue growth by enabling faster time-to-market, improved product quality, and greater customer satisfaction. For example, higher first-pass yield reduces rework, accelerating product delivery and enhancing customer satisfaction. Additionally, innovative products and services derived from Industry 4.0 capabilities, such as digital twins or smart products, can open new revenue streams.
- Risk Reduction: By enhancing predictive maintenance and quality control, Industry 4.0 reduces the risk of costly equipment failures, product recalls, and compliance issues. Reduced risk translates into financial savings, as it prevents costly disruptions and enhances brand reputation.
Long-Term Benefits: Sustainability, Productivity, and Innovation
While immediate gains from Industry 4.0 include efficiency and cost savings, the long-term benefits can have transformative effects on the business:
- Sustainability: Industry 4.0 enables manufacturers to adopt more sustainable practices, such as optimizing energy usage, reducing waste, and minimizing emissions. By tracking sustainability metrics over time, companies can demonstrate a positive environmental impact and enhance their brand reputation.
- Productivity: Industry 4.0 solutions improve productivity by automating repetitive tasks, enhancing real-time decision-making, and supporting advanced analytics. These productivity gains compound over time, leading to greater operational resilience, workforce efficiency, and scalability.
- Innovation: Industry 4.0 fosters a culture of continuous improvement and innovation by enabling experimentation, rapid prototyping, and data-driven insights. With access to simulation tools, digital twins, and AI models, companies can innovate faster, explore new product designs, and experiment with new processes without disrupting real-world operations.
Long-term benefits not only enhance competitiveness but also help attract top talent and increase organizational adaptability in dynamic markets.
How Decision-Makers Can Demonstrate ROI to Stakeholders
Demonstrating ROI to stakeholders requires a clear communication strategy that translates technical achievements into business value. Here are strategies for effectively showcasing ROI:
- Quantify Financial Gains: Use concrete financial metrics to demonstrate the impact of Industry 4.0 initiatives. Examples include cost savings in maintenance, reduced downtime, improved labor productivity, and energy savings. Providing detailed before-and-after comparisons helps stakeholders see the direct financial benefits.
- Showcase Key Success Metrics: Highlight KPIs that align with the organization’s strategic objectives, such as improvements in production efficiency, product quality, or sustainability. Linking these metrics to tangible outcomes (e.g., fewer defects, higher output, or lower energy consumption) provides evidence of value.
- Present Use Cases and Success Stories: Share specific examples of successful implementations and their impact. Use cases help stakeholders understand how Industry 4.0 solutions translate into real-world improvements, making the benefits more relatable and impactful.
- Emphasize Long-Term Strategic Value: Explain how Industry 4.0 investments contribute to long-term goals, such as sustainability, innovation, and competitive advantage. By framing Industry 4.0 as a foundation for future growth, decision-makers can convey that these initiatives are not merely expenses but strategic investments.
- Leverage Visualizations: Visualizations, such as graphs, charts, and dashboards, can help stakeholders quickly grasp complex data and trends. Real-time dashboards showing live KPIs, for example, provide a powerful visual representation of the software’s ongoing value.
- Highlight Risk Mitigation Benefits: Emphasize the role of Industry 4.0 in reducing operational risks, such as equipment failure, product recalls, or compliance issues. By quantifying risk reduction in terms of cost avoidance, decision-makers can demonstrate additional, often overlooked, financial value.
- Continuous Monitoring and Reporting: Industry 4.0 initiatives are not static; they evolve and provide ongoing benefits. By implementing a regular reporting schedule that highlights updated KPIs, decision-makers can showcase the software’s sustained impact over time, reinforcing its value to stakeholders.
Consulting Services for Industry 4.0 Transformation
Consulting services play a pivotal role in guiding manufacturers through the complex process of Industry 4.0 transformation. From initial assessments to implementation and optimization, third-party consultants offer valuable expertise and resources, ensuring that companies maximize the potential of their digital initiatives. This section discusses the roles consultants play, the value of audit and assessment services, custom vs. off-the-shelf solutions, and the importance of change management.
Role of Third-Party Consultants in Assessing, Implementing, and Optimizing Industry 4.0
Industry 4.0 transformations require specialized knowledge across numerous domains, including IoT, data analytics, cybersecurity, and IT-OT integration. Consultants bring a range of expertise and hands-on experience, providing companies with the strategic, technical, and operational support needed to succeed. Key roles of consultants include:
- Initial Assessment and Strategy Development: Consultants assess a company’s current digital maturity, identify opportunities for improvement, and develop a tailored Industry 4.0 roadmap. This includes evaluating existing systems, data readiness, workforce skills, and identifying gaps that may hinder progress. The strategy developed serves as a blueprint, aligning initiatives with business objectives and defining the scope, timeline, and required resources.
- Technology Selection and Implementation: Consultants help select the right technology stack based on the organization’s goals, scalability needs, and integration requirements. They work with companies to implement chosen solutions, ensuring seamless integration with existing systems and minimal disruption to operations. Their expertise in technology ecosystems and vendor relationships enables them to recommend best-fit solutions while mitigating risks.
- Optimization and Continuous Improvement: After initial implementation, consultants provide ongoing support to optimize performance, ensure alignment with evolving business needs, and identify opportunities for further improvements. This may involve fine-tuning data analytics models, enhancing cybersecurity measures, or refining workflows to maximize efficiency.
- Training and Knowledge Transfer: Consultants often provide training for internal teams, helping them understand and manage the new systems independently. Effective knowledge transfer ensures that the organization can sustain and build on the transformation once the consultant’s engagement ends.
Audit and Assessment Services for Readiness and Optimization
Before embarking on an Industry 4.0 journey, an audit and assessment service is essential to evaluate the organization’s current state and identify areas that need attention. Key components of audit and assessment services include:
- Digital Maturity Assessment: Consultants assess the digital maturity of the organization, evaluating its readiness to adopt Industry 4.0 technologies. This includes reviewing data infrastructure, connectivity, integration capabilities, and cybersecurity protocols. The assessment identifies potential roadblocks and provides insights into which foundational steps are necessary.
- Infrastructure and System Audit: Auditing existing systems, such as MES, ERP, and SCADA, helps determine their compatibility with new Industry 4.0 technologies. Consultants assess the current infrastructure for scalability, security, and interoperability, recommending upgrades or adjustments to accommodate the anticipated data load and complexity.
- Process and Workflow Analysis: Consultants evaluate current workflows and processes to identify inefficiencies and bottlenecks that Industry 4.0 solutions could address. This analysis highlights areas where automation, data-driven decision-making, or real-time monitoring can enhance productivity.
- Gap Analysis and Recommendations: A gap analysis provides a detailed comparison between the current state and the desired future state. Based on this analysis, consultants offer specific recommendations, including short-term and long-term actions, resource requirements, and priority areas to address.
By conducting a thorough audit, consultants help companies understand their starting point, set realistic goals, and prioritize investments based on strategic value and readiness.
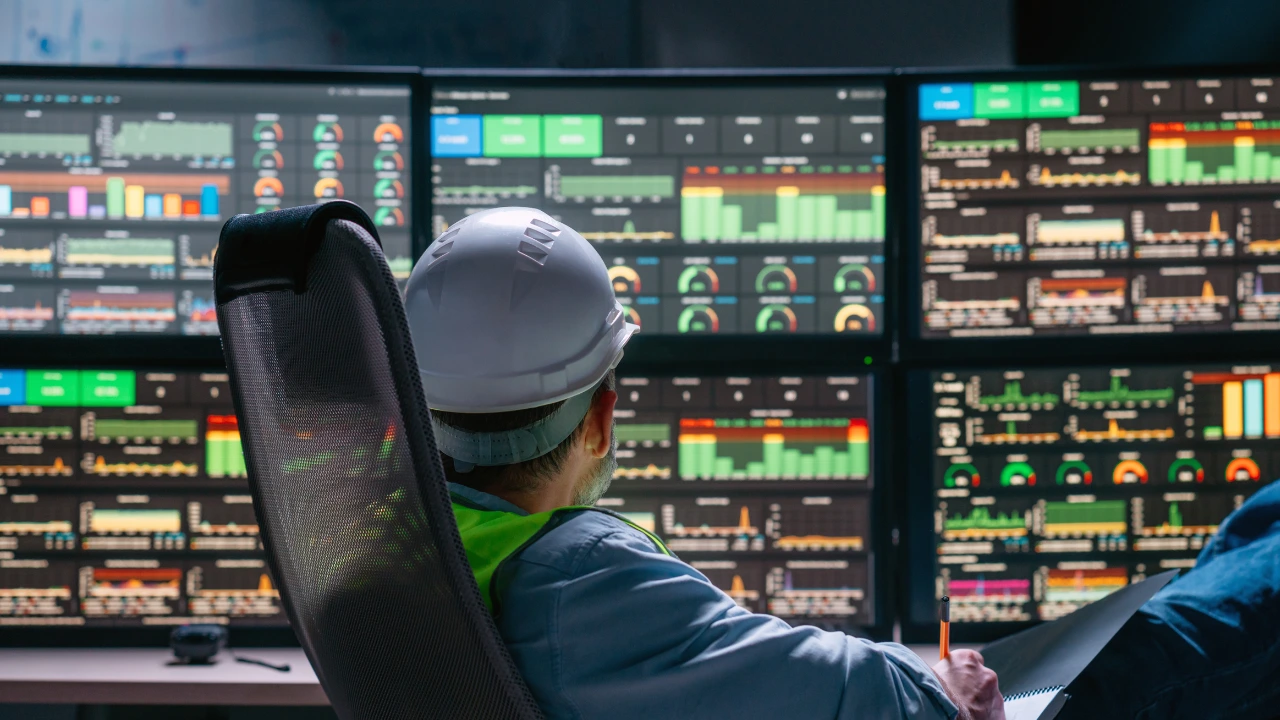
Custom Solutions vs. Off-the-Shelf Software
Choosing between custom solutions and off-the-shelf software is a significant decision in Industry 4.0 transformation. Consultants play a crucial role in helping companies assess the pros and cons of each option based on their unique requirements and constraints:
- Custom Solutions
- Pros: Custom solutions offer maximum flexibility, enabling companies to design software that aligns precisely with their operational needs, workflows, and integration requirements. This approach allows for unique features, tailored interfaces, and specific configurations that address distinct challenges.
- Cons: Developing custom software can be costly and time-intensive, requiring dedicated resources for development, testing, and maintenance. Custom solutions may also require specialized in-house or external support to manage and update.
- Off-the-Shelf Software
- Pros: Off-the-shelf solutions provide faster deployment, lower upfront costs, and ongoing support from the vendor. These solutions often come with standardized features and compatibility with widely used platforms, making them easier to integrate into existing environments.
- Cons: While off-the-shelf software can be configured, it may lack the level of customization required to meet all specific needs. Limited flexibility may require companies to adapt some workflows to the software rather than the other way around.
- Hybrid Approach: In some cases, a hybrid approach can combine off-the-shelf software with customized add-ons or integrations. Consultants can recommend and implement this strategy, ensuring that companies benefit from both customization and ease of deployment.
Consultants help companies weigh these options, considering factors such as cost, time, scalability, integration requirements, and the expected return on investment. Their expertise allows companies to make informed decisions that align with both immediate needs and long-term objectives.
Supporting Organizational Change with Consulting Expertise
Industry 4.0 transformation requires significant changes in culture, processes, and workforce skills. Consultants provide the change management expertise needed to help organizations navigate this shift and foster a culture that embraces innovation. Key aspects of change management support include:
- Stakeholder Engagement and Communication: Consultants work with leadership to define and communicate the vision, goals, and benefits of Industry 4.0 to all stakeholders. Effective communication reduces resistance, builds buy-in, and fosters an understanding of how digital transformation aligns with broader business objectives.
- Change Management Planning: Consultants develop a structured change management plan that includes timelines, milestones, and clear responsibilities. This plan addresses potential resistance points, establishes a process for feedback, and provides mechanisms for tracking progress.
- Training and Skills Development: Consultants create training programs to upskill employees on new tools, processes, and technologies, ensuring that they are prepared to work in a digitally enabled environment. Training may include hands-on workshops, online courses, or certification programs tailored to specific roles and responsibilities.
- Building a Culture of Innovation: Consultants help companies foster a culture that values continuous learning, collaboration, and experimentation. They provide frameworks for encouraging employees to explore new ideas, contribute to digital initiatives, and feel empowered to drive improvements.
- Sustained Support and Optimization: Industry 4.0 transformation is an ongoing process that requires regular assessment and adaptation. Consultants offer ongoing support to optimize systems, update best practices, and ensure that the transformation remains aligned with evolving goals. By working alongside internal teams, consultants help embed change as part of the organizational DNA.
Consulting services support organizational change by providing both a structured approach and the adaptability needed to respond to unexpected challenges. This guidance is essential for sustaining momentum and ensuring that Industry 4.0 transformation delivers lasting value.
Future Trends in Industry 4.0 Software
As technology continues to evolve, Industry 4.0 software will become even more capable, interconnected, and intelligent. This section explores anticipated advancements, the growing role of artificial intelligence (AI) and autonomous systems, the expected evolution of Industry 4.0 software in manufacturing, and strategies for preparing for future disruptions and innovations.
Anticipated Advancements in Software and Technology
Emerging technologies will continue to expand the capabilities of Industry 4.0 software, enabling greater efficiency, scalability, and automation. Some key advancements include:
- Enhanced IoT and Edge Computing: The Internet of Things (IoT) and edge computing will expand with more advanced, low-power sensors and edge devices capable of performing complex computations closer to the data source. These advancements will increase processing speeds, reduce latency, and make real-time decision-making more accessible across manufacturing environments, supporting high-speed applications like predictive maintenance and real-time quality control.
- Unified Data Ecosystems: Industry 4.0 software is moving toward more unified data management frameworks, where the Unified Namespace (UNS) concept and data lakes enable real-time data sharing across platforms. These ecosystems create a single source of truth for organizations, facilitating interoperability, data contextualization, and seamless data flow from the shop floor to enterprise-level systems.
- Improved User Interfaces and Visualization Tools: User experience (UX) and visualization tools will continue to improve, making it easier for operators and decision-makers to interact with complex data. Augmented reality (AR) and virtual reality (VR) will increasingly support training, maintenance, and troubleshooting, allowing employees to visualize equipment and data in immersive, interactive environments.
- Blockchain for Supply Chain Transparency: Blockchain technology is gaining traction for providing secure, transparent records in supply chains. As manufacturing operations increasingly prioritize transparency and traceability, blockchain can facilitate real-time tracking of products, components, and materials, improving compliance and product safety.
- Quantum Computing for Complex Problem-Solving: Although still in development, quantum computing has the potential to revolutionize Industry 4.0 by solving complex optimization problems faster than traditional computers. In the future, quantum computing could enable faster material simulations, production optimization, and AI model training.
The Role of Artificial Intelligence and Autonomous Systems
Artificial intelligence (AI) and autonomous systems will continue to drive Industry 4.0 advancements, pushing the boundaries of automation, decision-making, and process optimization. Key trends include:
- AI-Driven Predictive and Prescriptive Analytics: Predictive analytics, which forecasts potential future events, will evolve into prescriptive analytics, which suggests the best course of action. For example, AI can predict equipment failure and recommend specific maintenance tasks based on analysis of historical and real-time data. This evolution will enable manufacturers to optimize processes proactively, reducing downtime and resource consumption.
- Machine Vision and Quality Control: Machine vision, combined with AI, will become more sophisticated, allowing manufacturers to detect product defects in real-time with greater accuracy. AI models trained to recognize even subtle defects will reduce waste, improve quality control, and increase customer satisfaction.
- Autonomous Systems and Robotics: Autonomous systems, including collaborative robots (cobots) and automated guided vehicles (AGVs), will become more prevalent in manufacturing, supporting flexible, adaptive production. These systems will work alongside human operators and other machines, improving productivity and allowing for greater customization in production.
- Natural Language Processing (NLP) for Human-Machine Interaction: NLP will improve interactions between humans and machines, enabling operators to control and troubleshoot equipment using conversational commands. This advancement will simplify complex tasks, making advanced software more accessible to non-technical employees.
- AI for Supply Chain Optimization: AI algorithms will become more adept at managing supply chain complexities by predicting demand fluctuations, optimizing inventory, and recommending alternative suppliers. By improving supply chain resilience, AI will help manufacturers mitigate risks from disruptions, such as material shortages or logistical delays.
How Industry 4.0 Software Will Continue to Evolve in Manufacturing
Industry 4.0 software will evolve toward creating highly flexible, self-optimizing production environments. Key areas of evolution include:
- Hyper-Connected Factories: Manufacturing environments will become increasingly interconnected, with sensors, machines, software, and employees continuously sharing information. This hyper-connected infrastructure will enable a more holistic approach to production management, allowing for end-to-end visibility and control of all processes.
- Customization and Mass Personalization: As consumer demands shift toward more customized products, Industry 4.0 software will support agile, flexible production lines capable of delivering highly personalized products at scale. Manufacturers will increasingly leverage software that can handle complex production workflows, enabling rapid reconfiguration of production lines and material flows.
- Cyber-Physical Systems (CPS): Industry 4.0 software will enhance cyber-physical systems, integrating computational and physical processes. This convergence will facilitate the development of smart factories, where embedded software and physical equipment work seamlessly to adapt to changing conditions, optimizing production with minimal human intervention.
- Sustainability as a Core Focus: Industry 4.0 software will increasingly prioritize sustainability by optimizing energy use, reducing waste, and supporting eco-friendly production practices. Software will include features specifically designed for sustainability metrics, enabling manufacturers to monitor and minimize their environmental impact and comply with evolving regulatory requirements.
Preparing for Future Disruptions and Innovations
As technology rapidly advances, manufacturers must develop strategies for staying adaptable and resilient to future disruptions. Preparing for these changes involves:
- Adopting a Modular Technology Stack: A modular approach to technology adoption allows companies to add, replace, or upgrade components without disrupting the entire system. Modular software architectures, open-source solutions, and APIs support integration flexibility, enabling organizations to adapt to technological changes with minimal friction.
- Fostering a Culture of Innovation: A culture that embraces change, experimentation, and continuous improvement helps organizations stay resilient in the face of innovation. Companies can encourage innovation by providing employees with access to training, R&D initiatives, and collaborative spaces for testing new ideas.
- Building a Data-Driven Infrastructure: With data at the core of Industry 4.0, manufacturers should invest in data infrastructure that supports real-time analytics, contextualization, and AI applications. By developing robust data governance, quality control, and centralized data repositories, companies create a foundation for future applications of AI, machine learning, and predictive analytics.
- Investing in Cybersecurity: As connectivity increases, so do cybersecurity risks. Manufacturers must adopt proactive cybersecurity strategies, such as zero-trust architecture, threat intelligence, and continuous monitoring, to protect their operations. Building resilience to cyber threats ensures that organizations can withstand future disruptions without compromising production.
- Exploring Partnerships and Ecosystems: Collaboration with technology providers, consultants, and research institutions can accelerate Industry 4.0 adoption. By engaging with an innovation ecosystem, manufacturers gain access to emerging technologies, industry expertise, and funding opportunities that support ongoing transformation.
- Staying Informed of Emerging Technologies: Manufacturers should actively monitor technology trends and assess their relevance to their operations. Regularly evaluating new technologies, such as AI, IoT, and blockchain, and engaging in industry forums or partnerships can help organizations identify disruptive innovations early and plan accordingly.
By focusing on flexibility, data-driven decision-making, cybersecurity, and a culture of innovation, companies can prepare to leverage future advancements in Industry 4.0 software while maintaining resilience to potential disruptions.
Conclusion: A Roadmap to Success with Industry 4.0 Software
The journey to Industry 4.0 transformation is complex and dynamic, but with the right strategy, manufacturers can achieve significant improvements in productivity, flexibility, and competitiveness. This conclusion provides a roadmap to success, emphasizing key considerations for adopting Industry 4.0 software, building a culture of continuous improvement, and empowering decision-makers to lead the way.
Recap of Key Considerations for Successful Adoption
Achieving success with Industry 4.0 software requires a comprehensive approach that addresses technology, people, and process factors. Here are some essential considerations:
- Aligning with Business Objectives: Industry 4.0 software adoption should be driven by specific business goals, such as improving operational efficiency, enhancing product quality, or enabling rapid customization. A clear understanding of these goals ensures that technology investments deliver measurable value.
- Building a Robust Data Strategy: Data is the foundation of Industry 4.0, enabling real-time monitoring, predictive analytics, and AI applications. A strong data strategy—encompassing collection, storage, processing, and analysis—ensures that data can be used effectively across the organization.
- Ensuring Scalability and Flexibility: Industry 4.0 environments must be adaptable, as needs and technologies evolve. Scalable, modular architectures allow manufacturers to expand their capabilities over time, adding new applications, data sources, and devices without disrupting existing systems.
- Focusing on Cybersecurity and Compliance: As systems become more interconnected, the risk of cyber threats grows. Manufacturers must adopt proactive security measures to protect their assets, data, and intellectual property, as well as adhere to compliance standards relevant to their industry.
- Empowering a Skilled Workforce: People are at the core of successful transformation. Investing in training, upskilling, and building interdisciplinary teams ensures that employees are well-prepared to manage and optimize Industry 4.0 systems.
- Partnering with Third-Party Consultants: Industry 4.0 transformation can benefit greatly from external expertise. Consultants bring specialized knowledge, assess readiness, recommend best-fit solutions, and support organizational change, accelerating the journey to digital maturity.
Building a Continuous Improvement Framework
To sustain the benefits of Industry 4.0, manufacturers must embed continuous improvement into their organizational culture. A continuous improvement framework involves:
- Regular Performance Assessments: Establish KPIs and monitor them regularly to track the performance of Industry 4.0 initiatives. Use these assessments to identify improvement areas and adjust strategies accordingly.
- Iterative Optimization: Digital transformation is not a one-time event; it’s an ongoing process. After initial implementation, companies should identify areas for further optimization, from refining data models to enhancing workflows and introducing new technologies.
- Embracing Innovation: Encourage a mindset of innovation by promoting experimentation and providing resources for employees to test new ideas. A culture of innovation ensures that the company remains competitive and adaptable as technologies and markets evolve.
- Feedback Loops and Cross-Functional Collaboration: Establish mechanisms for gathering feedback from operators, technicians, and managers. Cross-functional collaboration allows teams to identify challenges and leverage diverse perspectives to find solutions, creating an environment that thrives on improvement.
- Leveraging Data for Insights: Use data-driven insights to inform decision-making, address bottlenecks, and refine processes. Over time, data analytics and AI will become even more valuable, allowing manufacturers to anticipate trends, predict outcomes, and stay proactive.
Final Advice for Decision-Makers: Adapting, Evolving, and Leading in Industry 4.0
Industry 4.0 transformation requires visionary leadership, adaptability, and a commitment to continuous learning. Here are final pieces of advice for decision-makers:
- Embrace Change and Encourage Agility: Technology and markets are evolving at unprecedented rates, and companies that adapt quickly gain a competitive edge. Decision-makers should embrace change as an opportunity, fostering agility and empowering teams to respond to challenges and opportunities dynamically.
- Invest in Strategic Partnerships: Partnerships with technology vendors, consultants, and educational institutions provide access to resources, innovation, and talent. Strategic alliances help manufacturers stay on the cutting edge of Industry 4.0, enhancing both technical capabilities and workforce skills.
- Lead by Example in a Data-Driven Culture: Decision-makers should set the tone for a data-driven culture, demonstrating a commitment to data-informed decision-making. By championing the use of analytics and evidence-based processes, leaders reinforce the importance of data throughout the organization.
- Stay Informed of Emerging Technologies: Technology trends in AI, IoT, edge computing, and blockchain will continue to shape the future of Industry 4.0. Decision-makers should stay informed and evaluate the relevance of these technologies, preparing to adopt or experiment with them as opportunities arise.
- Prioritize Long-Term Value Over Short-Term Gains: While quick wins are essential for demonstrating progress, Industry 4.0 is a long-term journey. Focus on sustainable improvements that create lasting value, such as building robust data infrastructure, fostering a skilled workforce, and continuously refining processes.
Champion a Vision of Continuous Improvement and Innovation: Digital transformation is not a final destination but a continuous journey. Leaders should champion a vision that prioritizes improvement, encourages innovation, and celebrates progress, ensuring that the organization evolves in alignment with Industry 4.0 goals.