Introduction to Industrial Robotics
What Are Industrial Robots and Why Are They Essential?
Industrial robots are programmable, automated machines designed to perform complex tasks with precision, speed, and consistency. Unlike traditional machinery, these robots can adapt to various applications, making them indispensable in industries like manufacturing, logistics, automotive, and electronics. From assembling products on a factory floor to optimizing supply chains in warehouses, industrial robots have become a cornerstone of modern production processes.
As companies face increasing pressure to enhance efficiency, reduce costs, and meet the demands of a globalized market, industrial robotics are no longer optional—they are essential. The integration of robotics enables businesses to stay competitive, improve safety by automating hazardous tasks, and achieve higher levels of quality and scalability.
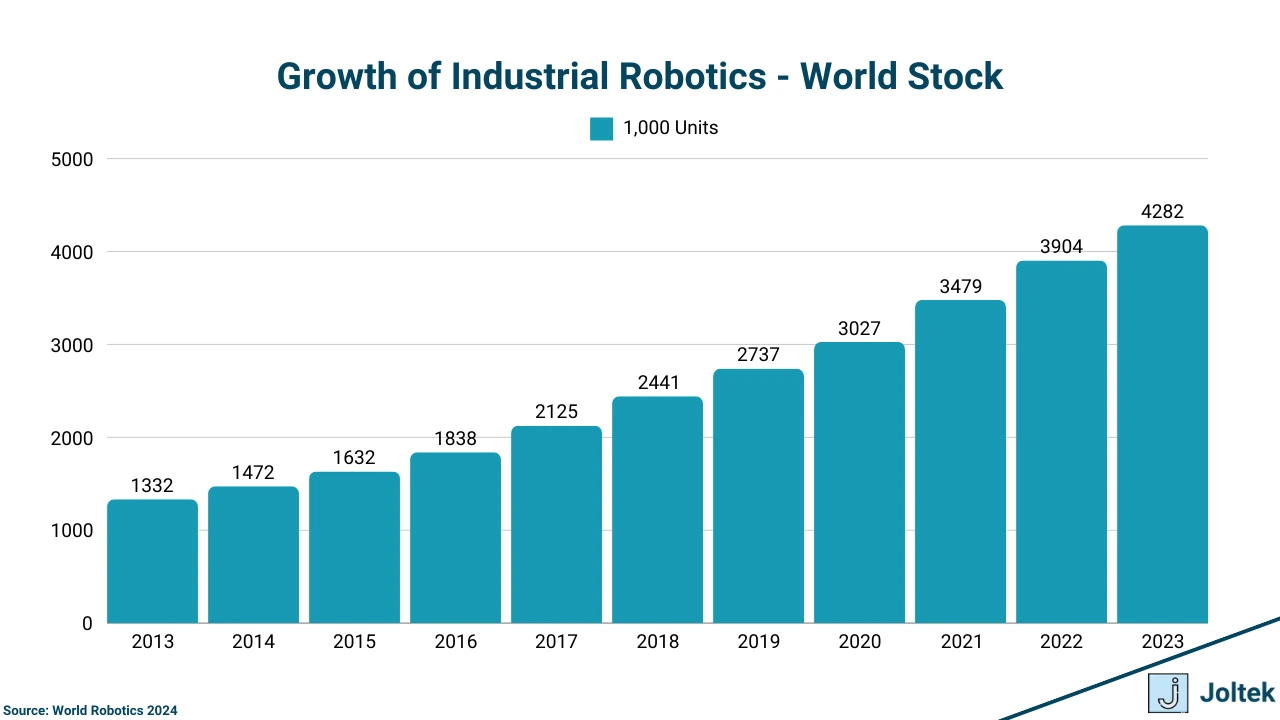
A Brief History of Industrial Robotics
The journey of industrial robotics began in the mid-20th century and has evolved into a sophisticated, multi-billion-dollar industry. Key milestones include:
- 1954: George Devol invents the first programmable robotic arm, the foundation of modern industrial robotics.
- 1961: The Unimate, the world’s first industrial robot, is deployed at General Motors, revolutionizing the automotive industry by automating dangerous tasks like die-casting and welding.
- 1980s: Robotics expand beyond automotive, entering electronics and heavy manufacturing, driven by innovations in computing and sensors.
- 2000s: Collaborative robots (cobots) are introduced, designed to work safely alongside humans, opening the door for robotics in small and medium-sized enterprises (SMEs).
- Today: AI and machine learning are driving the next wave of robotics innovation, enabling smarter, more adaptable systems.
These advancements have positioned industrial robotics as a transformative force across multiple industries.
The Current Landscape of Industrial Robotics
The numbers tell a compelling story. In 2022, global industrial robot sales exceeded 500,000 units, a record-breaking figure that reflects the growing demand for automation. According to the International Federation of Robotics (IFR), the industrial robotics market is expected to grow at a compound annual growth rate (CAGR) of 10% between 2023 and 2030, driven by adoption in sectors like logistics, food and beverage, and electronics.
Regions like Asia-Pacific lead the charge, with countries such as China, Japan, and South Korea accounting for over 70% of robot installations. Meanwhile, North America and Europe are rapidly catching up, driven by investments in advanced manufacturing and warehouse automation.
Why This Guide Matters
With the rapid evolution of robotics, businesses are faced with an overwhelming number of choices: different types of robots, a variety of programming protocols, and a host of vendors promising cutting-edge solutions. Choosing the right system for your needs—whether you’re operating a small facility or a global enterprise—requires a clear understanding of the options available and the factors that matter most.
This guide is designed to help you:
- Understand the different types of industrial robots and their applications.
- Evaluate leading vendors and their offerings.
- Explore use cases and emerging trends.
- Learn about the programming languages and protocols powering industrial robotics.
- Make informed decisions based on your facility’s size, industry, and unique requirements.
Whether you’re a technical expert or a decision-maker, this comprehensive guide will equip you with the insights needed to navigate the complex world of industrial robotics and drive your business forward.
Types of Industrial Robots
Industrial robots are as diverse as the industries they serve, with each type of robot uniquely suited for specific tasks. Understanding these distinctions is critical for businesses aiming to enhance efficiency and precision in their operations. Below is an in-depth look at the major categories of industrial robots, their characteristics, and their applications.
Articulated Robots
Articulated robots are perhaps the most recognizable in industrial settings. These robots feature rotary joints that allow them to mimic the range of motion of a human arm. With anywhere from four to six axes (or more), articulated robots excel in complex and versatile tasks, offering exceptional flexibility.
Articulated robots are widely used in automotive assembly lines for tasks like welding and painting. Their ability to handle heavy payloads while maintaining precision makes them indispensable for industries requiring high levels of accuracy. Despite their higher cost, their adaptability and robustness often deliver significant long-term value.
SCARA Robots
Selective Compliance Assembly Robot Arm (SCARA) robots are designed for high-speed, repetitive tasks within a single plane. Their compact design makes them ideal for environments with limited space, and they are known for their ability to rapidly execute pick-and-place operations with accuracy.
SCARA robots are heavily utilized in electronics manufacturing, where placing delicate components requires both speed and precision. Their lower cost and straightforward deployment make them attractive for small-to-medium enterprises looking to automate their operations without a significant upfront investment.
Cartesian Robots
Cartesian robots, also known as gantry robots, operate along three linear axes: X, Y, and Z. Their simple design and movement make them highly reliable for tasks that require straight-line precision, such as CNC machining and 3D printing.
These robots are especially popular in applications like material handling and stacking. Their ease of programming and cost-effective design appeal to industries focused on precision manufacturing, particularly when rotational movement is unnecessary.
Delta Robots
Delta robots are known for their speed and lightweight structure. With three arms connected to a base, these robots are built for high-speed applications like sorting and packaging. Their ability to handle delicate items with precision has made them a staple in the food, pharmaceuticals, and electronics industries.
For example, delta robots are used to sort confectioneries on a production line or package electronic components in blister packs. While their application is limited to lightweight tasks, their unparalleled speed and precision make them highly effective in their niche.
Collaborative Robots (Cobots)
Collaborative robots, or cobots, are redefining human-robot interaction by working alongside humans in shared workspaces. Unlike traditional robots, cobots are equipped with advanced sensors and safety protocols to prevent accidents, enabling them to safely assist in tasks like assembly and quality testing.
Cobots are especially beneficial for small manufacturers due to their ease of programming, scalability, and lower cost compared to traditional industrial robots. They enhance productivity without the need for extensive infrastructure changes, making them a flexible solution for businesses across various industries.

Why Understanding Robot Types Matters
Selecting the right robot is critical to achieving operational efficiency and maximizing ROI. While articulated robots may be the gold standard for heavy-duty tasks, SCARA or cobots may be more appropriate for precision assembly or smaller-scale operations. By understanding the strengths and limitations of each type, decision-makers can tailor their investments to their specific needs, ensuring a balanced approach to automation.
Key Applications of Industrial Robotics
Where Robots Excel in Industry
Industrial robotics have revolutionized modern manufacturing and logistics, delivering unprecedented levels of efficiency, precision, and safety. From welding intricate automotive parts to automating warehouse operations, these versatile machines are reshaping industries worldwide. Below, we explore the key applications of industrial robots, showcasing their transformative impact.
Welding and Assembly
Overview:
Robots excel in welding and assembly tasks that require precision, consistency, and speed. Articulated robots, with their multi-jointed arms, are particularly adept at handling complex welds or assembling components in tight spaces.
Real-World Example:
In the automotive industry, robots are used to weld car frames, ensuring consistent joint quality and reducing production times. Tesla’s manufacturing lines are a prime example, where robots perform a mix of spot welding, seam welding, and assembly tasks with high efficiency.
Benefits:
- Improved weld quality and reduced defects.
- Faster assembly cycles compared to manual processes.
- Enhanced worker safety by automating hazardous tasks.
Material Handling and Palletizing
Overview:
Material handling robots streamline operations by automating the movement of goods, loading/unloading machines, and palletizing products for shipment. Cartesian and articulated robots are commonly used for these tasks.
Real-World Example:
In the food and beverage sector, material handling robots sort and palletize bottles, cans, and packages with precision, minimizing the risk of product damage. Coca-Cola’s facilities use robots to palletize thousands of beverage cases daily, ensuring rapid and accurate stacking.
Benefits:
- Reduced labor costs and increased throughput.
- Consistent stacking and handling of products.
- Enhanced efficiency in supply chain operations.
Painting and Coating
Overview:
Painting and coating are tasks that demand a flawless finish and uniform application, making them ideal for robotic automation. Articulated robots equipped with spray nozzles are often used for this purpose.
Real-World Example:
In aerospace manufacturing, robots apply coatings to aircraft fuselages with precision, ensuring consistent thickness and coverage. This reduces material waste and ensures compliance with stringent safety standards.
Benefits:
- Consistent and high-quality finishes.
- Reduced exposure of workers to hazardous chemicals.
- Lower material waste and increased environmental compliance.
Inspection and Quality Control
Overview:
Robots equipped with advanced sensors, cameras, and AI algorithms are increasingly used for non-destructive testing and visual inspections, identifying defects that may be missed by the human eye.
Real-World Example:
Electronics manufacturers use vision-enabled robots to inspect circuit boards for micro-defects. Samsung’s production lines employ robots for quality control, ensuring flawless assembly of smartphones and other devices.
Benefits:
- Improved product quality and customer satisfaction.
- Faster inspection cycles compared to manual checks.
- Increased traceability through automated data collection.
Pick-and-Place Operations
Overview:
Pick-and-place robots, such as SCARA and delta robots, are designed for high-speed sorting and placement tasks, making them indispensable in fast-paced industries like packaging and electronics.
Real-World Example:
In the pharmaceutical industry, robots sort and package medications with high precision, ensuring compliance with stringent health regulations. Delta robots in particular excel in picking lightweight items and placing them into packaging at speeds unmatched by humans.
Benefits:
- Accelerated production speeds.
- Reduced errors in sorting and packaging.
- Cost-effective automation for repetitive tasks.
Logistics and Warehouse Automation
Overview:
Logistics and warehouse automation have been transformed by robots capable of picking, packing, sorting, and transporting goods. Collaborative robots (cobots) and autonomous mobile robots (AMRs) play a significant role in this domain.
Real-World Example:
Amazon’s warehouses employ thousands of robots to move shelves, pick orders, and assist workers in packing, reducing delivery times significantly. This hybrid human-robot system has set a new standard in e-commerce logistics.
Benefits:
- Optimized inventory management and faster order fulfillment.
- Reduced operational costs and errors.
- Scalability for handling peak demands in e-commerce and retail.
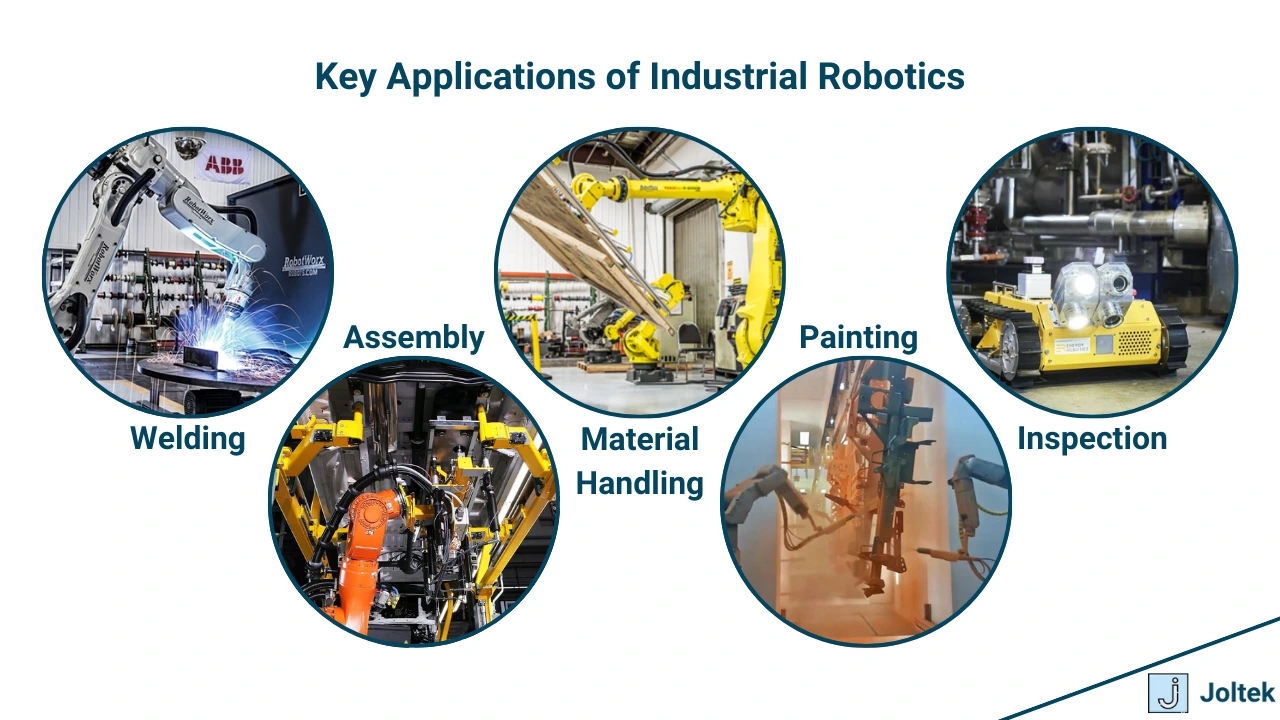
Use Case Highlight: Industry-Specific Transformations
- Automotive: Robots handle welding, painting, and assembly, improving production speed and reducing defects.
- Electronics: Robots perform precise pick-and-place tasks, ensuring accuracy in assembling delicate components.
- Food and Beverage: Robots automate palletizing, packaging, and sorting, maintaining hygiene and efficiency.
The Numbers Behind the Growth
According to the International Federation of Robotics (IFR):
- In 2022, the automotive industry accounted for 30% of global industrial robot installations, followed by electronics at 25%.
- Logistics robots saw a significant rise, with installations growing by 45% year-over-year, driven by e-commerce demand.
These figures underscore the growing adoption of robotics across industries, highlighting their critical role in modern manufacturing and logistics.
Choosing the Right Industrial Robot for Your Needs
Factors to Consider for Small and Large Facilities
Selecting the right industrial robot can make or break your automation strategy. The decision hinges on several critical factors, from the complexity of your application to the scalability of your operation. In this section, we’ll explore the key criteria businesses must evaluate to ensure the best fit for their needs, whether they operate in a small facility or a large-scale manufacturing plant.
Application Type and Complexity
The first step in choosing an industrial robot is understanding the task it will perform. Robots designed for simple pick-and-place tasks differ significantly from those required for complex welding or assembly operations.
- Simple Applications: SCARA and delta robots excel in high-speed, repetitive tasks like sorting and packaging.
- Complex Applications: Articulated robots with multi-axis motion are ideal for tasks like welding, painting, and intricate assembly.
Key Tip: Define the level of precision, speed, and flexibility required for your operations. For example, if you need to handle varied product shapes, a robot with advanced adaptability like a collaborative robot (cobot) may be your best choice.
Space Constraints
The physical space in your facility is another critical factor. Some robots require extensive room for movement, while others are compact and designed for tight spaces.
- Limited Space: SCARA robots and cobots are compact and can be easily integrated into crowded production lines.
- Large Areas: Articulated robots and Cartesian robots may require significant room for installation and operation.
Key Tip: Evaluate not only the floor space but also the vertical clearance needed for robotic arms or gantry systems.
Payload Capacity and Reach
The weight and size of the materials or products a robot needs to handle directly impact your selection.
- High Payloads: Articulated robots with robust designs can handle heavy objects, making them ideal for industries like automotive or aerospace.
- Light Payloads: Delta robots are perfect for lightweight, high-speed applications such as sorting small items.
Key Tip: Ensure the robot’s reach aligns with the dimensions of your production area to avoid unnecessary repositioning or extensions.
Scalability for Future Needs
Investing in a robot should be a forward-looking decision. Consider whether the robot you choose can adapt to future changes in production volume or complexity.
- For SMEs: Cobots offer modularity and scalability, making them a cost-effective option for businesses anticipating gradual growth.
- For Large Facilities: Articulated robots with advanced programming capabilities provide flexibility for complex, multi-task operations.
Key Tip: Look for robots that can be reprogrammed or retrofitted as your business grows or your product lines diversify.
Cost vs. ROI
Budget constraints are a reality for any business, but it’s essential to balance upfront costs with the long-term return on investment (ROI).
- Initial Cost: SCARA and delta robots tend to have lower purchase and installation costs.
- Long-Term ROI: Articulated robots and Cartesian robots may have higher initial costs but deliver significant ROI through increased efficiency and reduced labor expenses.
Key Tip: Factor in the total cost of ownership (TCO), including maintenance, programming, and training expenses, when calculating ROI.
Integration with Existing Systems
The robot you choose must seamlessly integrate with your existing production line and IT systems. This includes compatibility with software, communication protocols, and other machinery.
- For Manual Lines: Cobots are easier to integrate due to their collaborative nature and minimal infrastructure requirements.
- For Automated Lines: Advanced robots with support for protocols like EtherCAT, Profinet, or Modbus can ensure smooth integration.
Key Tip: Work with a systems integrator to ensure the robot aligns with your existing technology and infrastructure.
Small vs. Large Facilities
The needs of small and large facilities vary significantly. Tailoring your approach ensures you get the most value from your investment.
- Small Facilities (SMEs): Focus on cost-effective, flexible solutions like cobots or SCARA robots that can be easily reconfigured as your needs evolve.
- Large Facilities: Invest in high-performance articulated or Cartesian robots for tasks requiring heavy payloads, precision, and scalability across multiple shifts.
Example: A small food production company might use a SCARA robot to package baked goods, while a large automotive manufacturer employs articulated robots for welding and assembly on high-speed production lines.
Comparing Vendors: Key Players in the Market
Evaluating Industrial Robotics Vendors
Selecting the right vendor for your industrial robotics needs is just as important as choosing the right robot. Vendors play a critical role in ensuring smooth implementation, ongoing support, and scalability for your operations. Below, we provide an overview of leading industrial robotics vendors and the key factors you should consider when evaluating them.
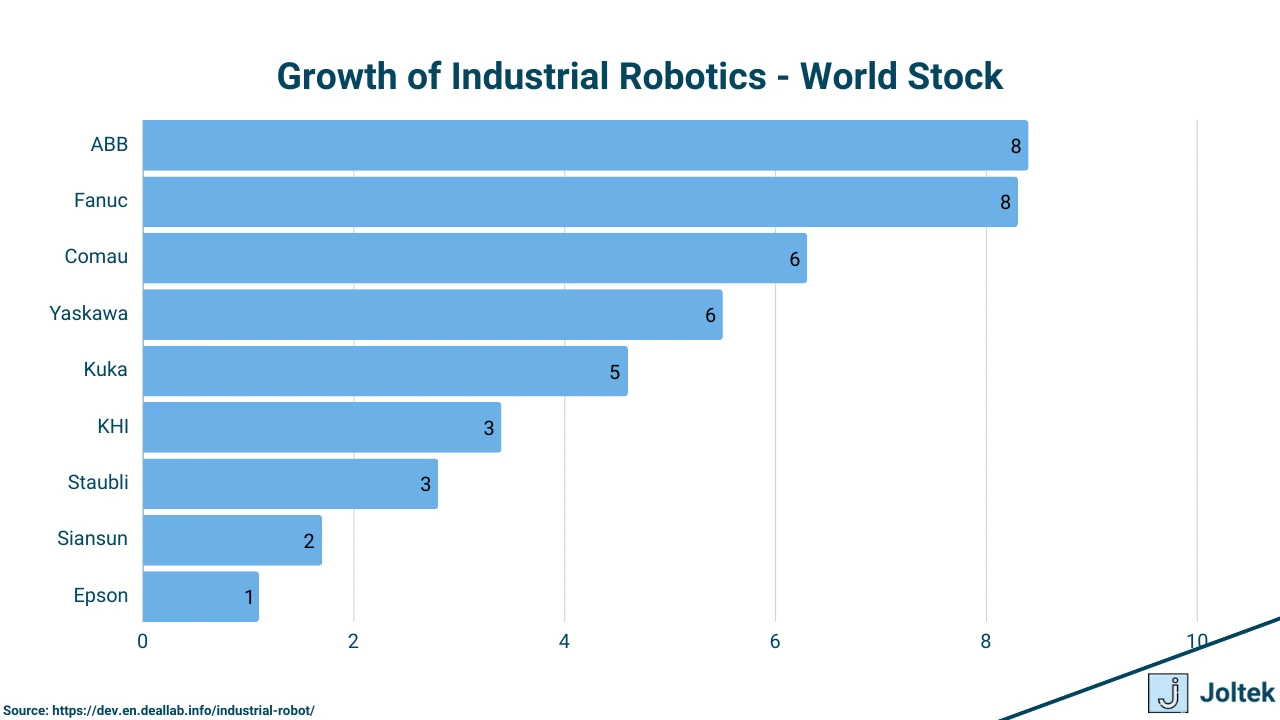
Leading Vendors in Industrial Robotics
Fanuc
Overview: Fanuc is one of the largest manufacturers of industrial robots globally, with a wide portfolio of solutions for industries like automotive, electronics, and packaging.
Key Strengths:
- Extensive range of articulated robots for welding, assembly, and palletizing.
- Renowned for reliability and longevity.
- Offers advanced software platforms, such as Fanuc ROBOGUIDE, for simulation and programming.
Case Study: Fanuc’s robots have been used extensively in Tesla’s Gigafactories for high-speed, high-precision assembly tasks.
ABB
Overview: ABB is a leader in industrial automation, offering solutions for manufacturing, logistics, and robotics integration. Their focus on sustainability and smart systems has set them apart.
Key Strengths:
- Cutting-edge programming with ABB RAPID language.
- Strong integration capabilities with IoT systems through ABB Ability.
- Comprehensive support services and global reach.
Testimonial: A leading electronics manufacturer praised ABB’s robots for reducing production downtime by 20% through predictive maintenance features.
KUKA
Overview: KUKA specializes in flexible and customizable robotics solutions, with a strong presence in automotive and general manufacturing. Their robots are known for their precision and ease of integration.
Key Strengths:
- Advanced control systems with KUKA Robot Language (KRL).
- Highly modular designs for versatile deployment.
- Focus on human-robot collaboration with their LBR iiwa cobot.
Case Study: KUKA robots are widely used by BMW for welding and assembly in their automated production lines, improving cycle times and consistency.
Yaskawa/Motoman
Overview: Yaskawa, operating under the Motoman brand, is renowned for its welding and material handling robots, offering solutions tailored to diverse industries.
Key Strengths:
- Advanced welding robots with integrated laser scanning.
- High payload capacity for heavy-duty applications.
- User-friendly programming with MotoSim and MotoPlus tools.
Testimonial: A heavy equipment manufacturer highlighted Yaskawa’s robots for their durability and accuracy in handling oversized components.
Universal Robots (Cobots)
Overview: Universal Robots pioneered the collaborative robot (cobot) space, creating robots that are safe, affordable, and easy to deploy. They cater primarily to SMEs.
Key Strengths:
- Plug-and-play integration for quick setup.
- Intuitive programming via the Polyscope interface.
- Competitive pricing, making cobots accessible to smaller businesses.
Case Study: A small bakery implemented Universal Robots cobots to handle repetitive packaging tasks, increasing production efficiency by 30% without expanding its workforce.
Boston Dynamics (Logistics-Focused Robots)
Overview: Known for their innovative robotics designs, Boston Dynamics has shifted focus to logistics with robots like Stretch and Spot.
Key Strengths:
- Specializes in mobile robots for warehouse and logistics automation.
- Advanced perception and navigation capabilities.
- Highly adaptable for tasks like pallet unloading and dynamic inspections.
Testimonial: A major e-commerce company integrated Boston Dynamics’ Stretch robots into its warehouses, reducing human labor for repetitive unloading tasks and increasing safety.
Key Factors to Compare Vendors
When evaluating vendors, consider the following factors to ensure a successful partnership:
- Support and Maintenance Services
- Look for vendors with strong post-sales support, including regular maintenance, software updates, and quick response times for repairs.
- Programming Capabilities and Ease of Use
- Evaluate the programming languages and tools offered by the vendor. For example, Fanuc’s ROBOGUIDE or ABB’s RAPID can impact how quickly your team adapts to using the robots.
- System Integration and Compatibility
- Ensure the vendor’s robots integrate seamlessly with your existing systems, including ERP, MES, and IoT platforms. Compatibility with communication protocols like EtherCAT or Profinet is critical.
- Customization Options
- Vendors like KUKA and ABB offer customizable robotics solutions that can be tailored to your specific industry needs, from gripper design to software customization.
Practical Insight
User Reviews and Testimonials:
- Many SMEs praise Universal Robots for their cobots' simplicity and cost-effectiveness, making them a popular choice for first-time automation adopters.
- Larger manufacturers often commend Fanuc and ABB for their scalability and reliability in high-volume production environments.
Case Studies:
- Automotive Sector: KUKA’s integration with BMW’s production lines resulted in 15% faster assembly times.
- Logistics: Boston Dynamics’ Stretch robots helped a major retailer reduce unloading time by 50% during peak seasons.
Making the Right Choice
Choosing the right vendor depends on your specific needs, including the complexity of your application, budget, and long-term goals. By carefully evaluating vendors based on the criteria above and leveraging real-world insights, you can make an informed decision that drives efficiency and productivity in your operations.
Programming Industrial Robots
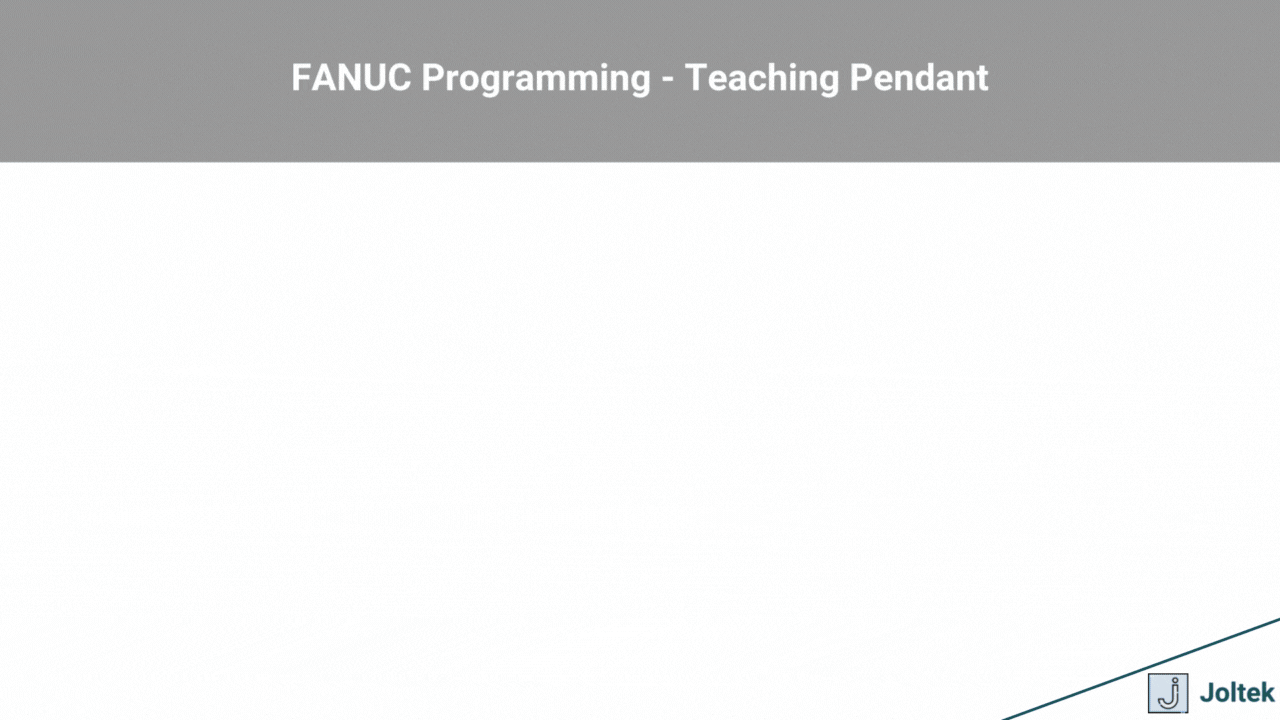
Languages and Protocols in Robotics Programming
Industrial robots require precise programming to perform complex tasks with accuracy and efficiency. Understanding the programming languages and communication protocols used in robotics is crucial for seamless integration and operation. This section delves into the most commonly used programming languages and protocols, highlighting their applications and suitability for various industries.
Popular Programming Languages for Industrial Robots
RAPID (ABB)
Overview: RAPID is ABB’s proprietary programming language designed for its robotic systems. Known for its straightforward syntax and versatility, it allows users to program a wide range of tasks, from simple pick-and-place operations to complex, multi-step sequences.
Applications:
- Used extensively in automotive and electronics manufacturing.
- Supports advanced motion control and integration with ABB’s IoT platform, ABB Ability.
Advantages:
- Easy to learn for beginners.
- Strong support for simulation and debugging tools.
KRL (KUKA Robot Language)
Overview: KUKA’s proprietary language, KRL, is designed for high customization and flexibility in robotic applications. It provides detailed control over robot movements, making it suitable for intricate tasks like welding and painting.
Applications:
- Widely used in automotive assembly and custom automation setups.
- Ideal for tasks requiring precise motion control.
Advantages:
- Highly customizable.
- Strong integration capabilities with third-party systems.
TP Programming (Fanuc Teach Pendant)
Overview: Fanuc robots are programmed using a teach pendant interface, which provides a user-friendly environment for creating motion paths and logic operations.
Applications:
- Common in material handling, palletizing, and welding.
- Often used for repetitive tasks in high-speed production environments.
Advantages:
- Intuitive interface for on-the-fly programming.
- Minimal training required for operators.
Python (for AI-driven or Custom Integrations)
Overview: Python has gained popularity in industrial robotics due to its flexibility and integration with AI and machine learning tools. It is often used for developing custom robotic applications or connecting robots to external systems like databases or IoT platforms.
Applications:
- AI-driven robotics for vision systems and decision-making tasks.
- Custom integration with warehouse management systems.
Advantages:
- Open-source and widely supported.
- Extensive libraries for AI, data analysis, and IoT integration.
ROS (Robot Operating System)
Overview: ROS is an open-source robotics middleware that provides a collection of tools and libraries for building robot applications. It is particularly popular in research and prototyping environments.
Applications:
- Multi-robot coordination in logistics and warehousing.
- Developing autonomous robots for research and industrial use.
Advantages:
- Highly modular and scalable.
- Open-source community support ensures continuous updates and improvements.
Communication Protocols
Robots rely on communication protocols to interact with other machines, sensors, and control systems. Choosing the right protocol ensures seamless integration and data exchange.
EtherCAT
Overview: EtherCAT is a high-performance protocol used for real-time communication in industrial automation.
Applications:
- Motion control and precise synchronization in robotics.
- Used in industries like automotive and semiconductor manufacturing.
Advantages:
- Extremely fast and reliable.
- Supports complex multi-axis control.
Profinet
Overview: Profinet is an Ethernet-based protocol commonly used for industrial automation. It allows robots to communicate with programmable logic controllers (PLCs) and other devices.
Applications:
- Factory automation and robot-to-machine communication.
- Widely used in packaging and assembly lines.
Advantages:
- Easy integration with Siemens PLCs.
- High data throughput.
Modbus
Overview: Modbus is a lightweight and widely adopted protocol used for simple communication between industrial devices.
Applications:
- Connecting robots to HMIs and SCADA systems.
- Suitable for monitoring and control in smaller setups.
Advantages:
- Simple and cost-effective.
- Compatible with a wide range of devices.
MQTT
Overview: MQTT is a lightweight messaging protocol often used for IoT applications. Its publish-subscribe model makes it ideal for connecting robots to cloud systems.
Applications:
- IoT-enabled robotics for real-time monitoring and analytics.
- Warehouse automation and remote robot control.
Advantages:
- Low bandwidth requirements.
- Excellent scalability for large deployments.
Making the Right Choice
Selecting the right programming language and communication protocol depends on your specific requirements, such as application complexity, integration needs, and workforce expertise. Whether you’re programming a robot for precision welding or integrating IoT-enabled robots into a logistics system, understanding these tools is critical for success.
Trends and Future of Industrial Robotics
Emerging Innovations and Predictions
Industrial robotics is at the forefront of technological evolution, continuously adapting to meet the demands of modern industries. Emerging trends and innovations are shaping the future of robotics, offering transformative solutions that go beyond traditional automation. From AI-driven robotics to sustainable energy-efficient designs, here are the key trends and predictions defining the future of industrial robotics.
AI Integration for Smarter Robotics
Artificial intelligence is revolutionizing industrial robotics by enabling machines to learn, adapt, and optimize performance in real time.
- Adaptive Learning: AI-powered robots can analyze vast amounts of data to refine their movements and improve efficiency, even in unstructured environments.
- Vision Systems: Advanced AI vision systems allow robots to identify and handle objects with unprecedented precision, making them ideal for tasks like quality inspection and complex assembly.
Example: Amazon utilizes AI-driven robotics in its warehouses, where robots equipped with vision and machine learning can sort and handle items dynamically, significantly reducing operational delays.
Impact: AI integration is expected to reduce downtime by up to 20% and improve overall production efficiency by 15% in industries like manufacturing and logistics.
Increased Adoption of Cobots in SMEs
Collaborative robots (cobots) are breaking barriers for small and medium enterprises (SMEs) by offering cost-effective and flexible automation solutions.
- Ease of Use: Cobots are designed for quick deployment and minimal programming, making them accessible to businesses with limited technical expertise.
- Affordability: Lower costs compared to traditional industrial robots make cobots a viable option for smaller businesses.
Example: A small electronics manufacturer implemented cobots for pick-and-place operations, reducing labor costs by 30% and achieving a return on investment within one year.
Projection: According to the International Federation of Robotics (IFR), cobot adoption is projected to grow by 20% annually, with SMEs driving the majority of this growth.
Robots as a Service (RaaS)
The Robots as a Service (RaaS) model is reshaping how businesses adopt robotics by lowering the upfront costs associated with purchasing and implementing robots.
- Subscription-Based Models: Companies pay for robot usage on a subscription basis, avoiding significant capital expenditures.
- Scalability: Businesses can scale their automation needs up or down based on demand.
Example: A logistics firm adopted RaaS for seasonal order surges, renting additional robots during peak periods to manage increased workloads.
Market Insight: The RaaS market is expected to reach $34 billion by 2030, driven by the growing need for flexible automation solutions in industries like e-commerce and manufacturing.
Sustainability and Energy-Efficient Robotics
As industries prioritize sustainability, robotics manufacturers are designing energy-efficient systems to reduce carbon footprints and operational costs.
- Reduced Energy Consumption: Modern robots consume less energy while maintaining high performance.
- Recyclable Materials: Manufacturers are incorporating recyclable components into robot designs to minimize environmental impact.
Example: ABB’s energy-efficient robots are used in automotive manufacturing, reducing energy usage by 25% compared to older models.
Impact: Sustainable robotics is expected to play a significant role in helping industries meet global carbon reduction targets, particularly in energy-intensive sectors like automotive and heavy manufacturing.
Market Projections and Future Outlook
The industrial robotics market is poised for exponential growth, driven by technological advancements and increased adoption across industries.
- Market Size: According to Grand View Research, the global industrial robotics market is expected to reach $75 billion by 2030, growing at a compound annual growth rate (CAGR) of 10.5% from 2023 to 2030.
- Key Drivers: Growth will be fueled by rising demand for automation in sectors like logistics, food and beverage, and electronics, along with innovations in AI and IoT.
Preparing for the Future
As robotics continues to evolve, businesses must stay ahead by:
- Investing in AI-driven and energy-efficient solutions.
- Exploring flexible models like RaaS for scalable automation.
- Embracing cobots to unlock new opportunities in smaller-scale operations.
By aligning with these trends, companies can not only enhance productivity but also future-proof their operations against the demands of an increasingly automated world.
Case Studies and Success Stories
Real-World Examples of Robotics in Action
Industrial robotics has left a transformative mark across various industries, with companies leveraging robotic solutions to streamline operations, improve safety, and boost productivity. Below are some detailed examples showcasing how robotics is revolutionizing manufacturing, logistics, and beyond.
Automotive Manufacturing: Welding with Precision
Use Case:
In automotive manufacturing, robots are indispensable for welding operations. Articulated robots equipped with advanced sensors and vision systems perform spot welding and seam welding with unparalleled precision.
Example:
Toyota employs over 3,000 robots across its manufacturing plants worldwide. In its Kentucky facility, welding robots have reduced production time for car frames by 25%, ensuring consistent weld quality while reducing material waste.
Impact:
- Improved Quality: Robots eliminate inconsistencies associated with manual welding.
- Enhanced Safety: Automating welding reduces human exposure to high heat and hazardous fumes.
- Higher Throughput: Robots operate continuously, minimizing downtime during production cycles.
Food Manufacturing: Cobots Boosting Safety and Efficiency
Use Case:
Small and medium-sized food factories are increasingly adopting collaborative robots (cobots) to enhance safety and streamline repetitive tasks.
Example:
A small bakery in Denmark implemented cobots from Universal Robots for repetitive packaging tasks. The cobots work alongside employees to package baked goods, increasing production efficiency by 30% while improving worker safety by reducing repetitive strain injuries.
Impact:
- Scalable Operations: Cobots can be quickly reprogrammed for different packaging sizes or new product lines.
- Cost Savings: The bakery achieved ROI within a year by reducing overtime labor costs.
- Enhanced Worker Satisfaction: Employees now focus on creative and value-adding tasks instead of monotonous work.
E-Commerce Logistics: Warehouse Automation at Scale
Use Case:
Robotics has transformed warehouse operations for e-commerce giants like Amazon, enabling faster order fulfillment and efficient inventory management.
Example:
Amazon’s robotics division, Amazon Robotics, has deployed over 520,000 mobile robots in its warehouses globally. These robots transport shelves of goods to human packers, reducing the time it takes to locate and pick items.
Impact:
- Increased Order Fulfillment Speed: Robots have reduced picking time by 50%, enabling same-day and next-day deliveries.
- Lower Operational Costs: Automated warehouses require fewer employees per square foot.
- Scalability: During peak seasons, Amazon deploys additional robots to manage increased order volumes efficiently.
Electronics Manufacturing: Precision and Quality Assurance
Use Case:
In electronics manufacturing, where precision is paramount, robotics ensures consistent assembly of delicate components and thorough quality inspections.
Example:
Foxconn, a major supplier for Apple, uses thousands of robots in its assembly lines. Robots handle tasks like soldering, screwing, and product testing, ensuring high-quality standards for devices like iPhones and MacBooks.
Impact:
- Higher Productivity: Robots enable 24/7 operations without fatigue.
- Fewer Defects: Automated quality checks identify micro-defects, reducing returns and rework.
- Improved Scalability: Foxconn adapts production capacity quickly to meet global demand.
Pharmaceutical Industry: Precision in Packaging and Inspection
Use Case:
Pharmaceutical companies are deploying robotics to ensure precision in packaging and stringent compliance with health and safety regulations.
Example:
Pfizer uses delta robots to sort and package medications at high speeds. These robots operate in sterile environments, maintaining the integrity of products while ensuring accurate labeling and packaging.
Impact:
- Regulatory Compliance: Robots meet stringent health and safety standards required in the pharmaceutical industry.
- Faster Processing: Packaging speeds have increased by 40%, allowing Pfizer to meet market demands more effectively.
- Error Reduction: Automated systems reduce labeling errors, ensuring patient safety.

Making the Right Decision: A Buyer’s Guide
How to Choose and Implement Robotics Successfully
Investing in industrial robotics is a significant step toward increasing productivity and staying competitive. However, the success of this investment depends on careful planning, informed decision-making, and effective implementation. Here’s a step-by-step guide to help businesses choose and deploy robotics tailored to their needs.
Conducting a Needs Assessment
Before diving into automation, it’s critical to assess your business requirements and identify specific pain points.
Key Questions to Ask:
- What tasks are repetitive, labor-intensive, or prone to human error?
- Are there bottlenecks in your current processes that automation could resolve?
- What outcomes are you aiming for (e.g., cost savings, increased throughput, improved safety)?
Example: A food manufacturer identified packaging as a bottleneck and opted for a SCARA robot to streamline the process.
Partnering with System Integrators
A system integrator can help design, install, and integrate robotics into your operations. Their expertise ensures seamless coordination between robots, existing machinery, and IT systems.
Benefits of System Integrators:
- Custom solutions tailored to your unique requirements.
- Expertise in programming, installation, and troubleshooting.
- Reduced downtime during deployment and testing.
Tip: Choose a system integrator with experience in your industry and familiarity with the specific robotics platform you’re adopting.
Budgeting for Total Cost of Ownership (TCO)
The cost of industrial robotics extends beyond the initial purchase price. Calculating the total cost of ownership (TCO) is essential to ensure a realistic financial plan.
Key Cost Components:
- Purchase price of the robot and ancillary equipment.
- Installation and integration costs.
- Maintenance, repairs, and software updates.
- Training costs for employees.
Example: A small manufacturer determined that while a cobot had a higher upfront cost, its low maintenance requirements and energy efficiency delivered a higher ROI over five years compared to traditional robots.
Training and Workforce Integration
Robotics can only deliver value if the workforce is prepared to operate and collaborate with them. Training programs are essential to build employee confidence and ensure smooth operations.
Training Focus Areas:
- Programming and troubleshooting robots.
- Safety protocols and emergency procedures.
- Leveraging robots to optimize workflows.
Tip: Collaborative robots (cobots) are often easier to train for, making them ideal for businesses with limited technical resources.
Testing and Iterating
Deploying robotics isn’t a one-and-done process. Thorough testing and iterative improvements are critical to maximizing the system’s potential.
Steps to Follow:
- Start with a pilot phase to evaluate robot performance in a controlled environment.
- Collect data on efficiency, error rates, and operational impact.
- Make adjustments to optimize robot settings, workflows, and integration.
Example: An electronics manufacturer ran a pilot with delta robots for packaging and adjusted the programming to accommodate changes in product dimensions, reducing errors by 15%.
Checklist: Steps to Choose and Implement Robotics
Step
Key Actions
Conduct Needs Assessment
Identify tasks to automate and desired outcomes.
Partner with Integrators
Collaborate with experienced system integrators for seamless deployment.
Budget for TCO
Account for all costs: purchase, installation, maintenance, and training.
Train Workforce
Provide training to ensure employees can operate and maintain the robots.
Test and Iterate
Pilot and refine the system before full deployment.
Making the Decision
Industrial robotics is a transformative investment, but success lies in preparation and strategic implementation. By following these steps, businesses can maximize the ROI from their robotic systems while minimizing disruptions during the transition.
Conclusion
Industrial Robotics: The Path to Efficiency and Innovation
Industrial robotics is no longer a luxury reserved for large enterprises—it is a necessity for businesses looking to remain competitive in today’s fast-paced and demanding markets. Robots drive efficiency, enhance precision, and foster innovation across industries, from automotive assembly lines to logistics warehouses.
Throughout this guide, we’ve explored the diverse types of industrial robots, their key applications, and actionable steps to implement them successfully. Whether you’re managing a small facility or a global operation, the potential for transformation through robotics is immense.
Take the First Step Toward Automation
The decision to adopt robotics should start with a careful evaluation of your specific needs, challenges, and goals. Consider:
- What tasks can automation improve in your operations?
- How can robotics enhance efficiency while reducing costs?
- What type of robot and vendor best aligns with your requirements?
By thoughtfully answering these questions and leveraging the insights shared in this guide, you can embark on a journey that not only boosts productivity but also sets your business apart as an industry leader.
Call to Action
Ready to explore your options? Whether you’re looking to implement your first robotic system or expand an existing one, we’re here to help. Contact us today for tailored advice, resources, and solutions to drive your automation goals forward.
Your next step toward efficiency, innovation, and growth starts now.