Introduction: Laying the Groundwork for Digital Transformation in Manufacturing
In today’s rapidly evolving industrial landscape, digital transformation is not just a buzzword—it’s a necessity. For manufacturers, embracing digital technologies is pivotal to staying competitive, driving innovation, and delivering value in a market where customer expectations and operational complexities are continually rising. But what does digital transformation truly entail, and why is it so critical in the manufacturing sector?
Defining Digital Transformation in Manufacturing
At its core, digital transformation in manufacturing involves integrating advanced digital technologies into every aspect of the production process. It encompasses a broad spectrum of changes, from automating workflows and leveraging real-time data to adopting intelligent systems that enable predictive maintenance and optimizing supply chains. It’s not merely about technology adoption—it’s about fundamentally reimagining how manufacturing operates to create smarter, more resilient, and sustainable systems.
The Importance of Digital Transformation
The manufacturing industry has always been at the forefront of innovation, and digital transformation serves as the next evolution in its journey. It is key to overcoming longstanding challenges like inefficient resource utilization, production bottlenecks, and disjointed operations. The integration of technologies such as IoT, AI, robotics, and cloud computing not only enhances operational efficiency but also opens doors to new opportunities, including mass customization and data-driven decision-making.
Key Benefits of Digital Transformation in Manufacturing
The impact of digital transformation in manufacturing can be profound. Here are some of the most notable benefits:
- Improved Efficiency: Automation and connected systems streamline operations, reduce downtime, and optimize resource usage.
- Enhanced Innovation: Advanced technologies enable rapid prototyping, smart product designs, and greater agility in responding to market demands.
- Cost Reduction: Predictive maintenance and process automation lower operational costs by preventing equipment failures and reducing waste.
- Competitiveness: Data-driven insights improve decision-making and customer responsiveness, helping manufacturers stay ahead of the curve.
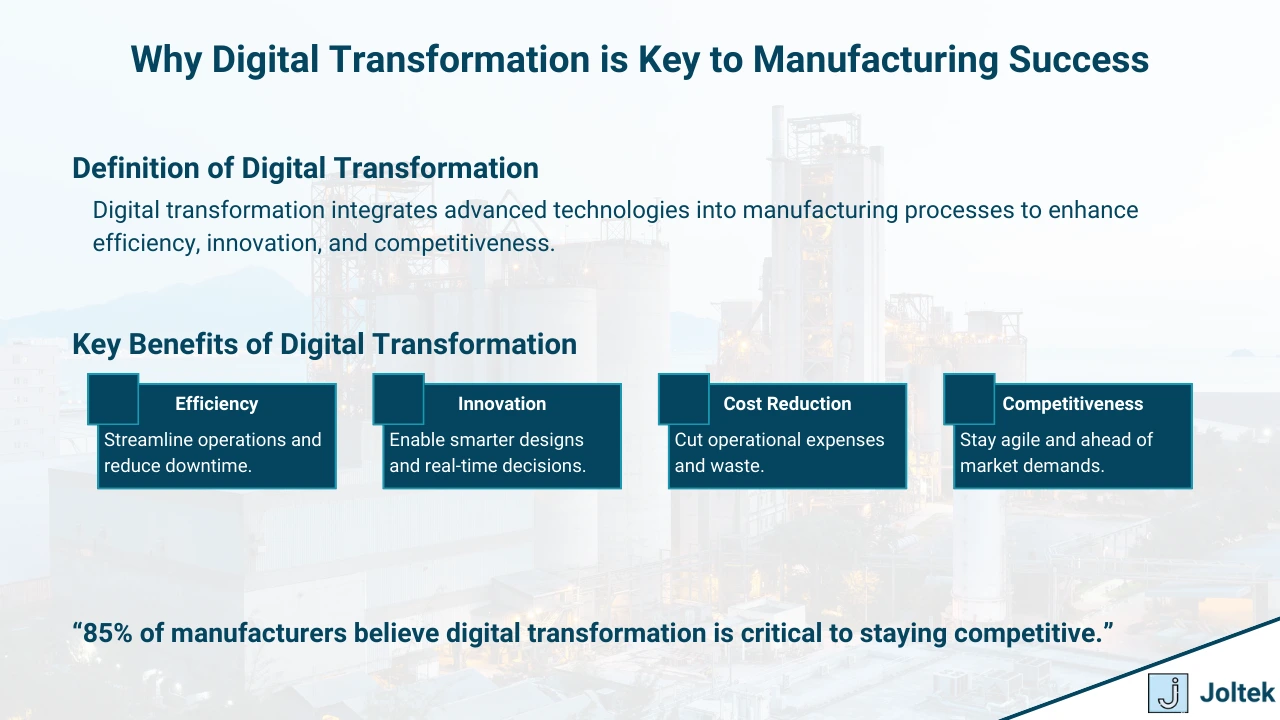
The Importance of a Structured Transformation Plan
While the promise of digital transformation is compelling, the path to achieving it is complex. Without a structured plan, manufacturers risk falling into common pitfalls such as misaligned investments, operational disruptions, or technology adoption without clear ROI. A well-crafted roadmap ensures that efforts are focused, aligned with business goals, and scalable over time.
Risks of Unplanned Digital Transformation
When approached haphazardly, digital transformation can lead to:
- Inefficiencies: Lack of integration or proper training can create more bottlenecks than solutions.
- Wasted Resources: Poorly chosen technologies or undefined goals can drain financial and human capital without delivering tangible outcomes.
- Employee Resistance: Without stakeholder buy-in and adequate training, workforce adoption can falter, stalling progress.
Digital transformation is not a one-size-fits-all solution; it requires careful assessment, prioritization, and alignment with organizational goals. By laying a strong foundation, manufacturers can maximize benefits while minimizing risks, setting the stage for sustainable growth and innovation.
Section 1: Setting the Foundation
Digital transformation begins with a deep understanding of where your manufacturing business currently stands. This foundational step lays the groundwork for any successful initiative by providing a clear picture of existing operations, identifying weaknesses, and highlighting opportunities for improvement.
1.1 Assessing Current State
The first step in setting the foundation is to conduct a comprehensive audit of your existing technologies, processes, and infrastructure. This involves carefully examining the equipment and tools currently in use, as well as the software systems that support manufacturing operations. For many manufacturers, the challenge lies in balancing older, legacy technologies with the demands of modern digital systems. For instance, while some equipment may still perform adequately, it might lack compatibility with data collection or IoT solutions. Similarly, outdated processes that rely heavily on manual intervention can become bottlenecks in the journey toward automation.
In addition to evaluating hardware and processes, it’s essential to assess workforce readiness. Digital transformation requires more than just technology—it demands a workforce capable of leveraging these new tools effectively. An audit of your workforce’s digital literacy should include an evaluation of employees’ familiarity with software systems, automated workflows, and data analytics. This step is critical because even the most advanced systems can fail to deliver results if workers lack the skills to operate them. Identifying gaps in knowledge will inform training and upskilling initiatives later in the transformation process.
Another critical aspect of assessing the current state is identifying pain points and inefficiencies within operations. Production bottlenecks, for example, can severely hinder output and efficiency. These bottlenecks might result from outdated machinery, poorly designed workflows, or insufficient coordination between departments. By pinpointing the exact cause of delays or inefficiencies, manufacturers can prioritize solutions that will have the greatest impact.
Maintenance challenges also frequently emerge during this phase. Reactive maintenance—where repairs are made only after equipment breaks down—can lead to significant downtime and increased costs. By analyzing patterns of equipment failure and unplanned downtime, manufacturers can determine where predictive maintenance solutions, powered by IoT and data analytics, might offer substantial benefits.
Finally, data silos present a significant barrier to efficiency in many manufacturing environments. When critical data, such as inventory levels, machine performance metrics, and production schedules, are stored in isolated systems, it becomes difficult for decision-makers to access the insights they need. This lack of integration often leads to errors, delays, and missed opportunities. Understanding the extent and impact of these silos is a crucial step toward creating a centralized and actionable data strategy.
1.2 Establishing Vision and Goals
Once a clear understanding of the current state has been established, the next step is to define the overarching vision and goals for the digital transformation. A well-defined vision provides a strategic direction, ensuring that every initiative aligns with the company’s long-term objectives. This step also involves setting specific, measurable goals to track progress and ensure accountability.
Defining Objectives of Transformation
The goals of digital transformation in manufacturing often revolve around improving operational efficiency, enhancing customer satisfaction, promoting sustainability, and ensuring compliance with regulations. Each of these objectives plays a critical role in shaping the overall vision.
Operational efficiency is typically at the heart of digital transformation efforts. Manufacturers aim to streamline workflows, reduce waste, and optimize resource utilization. Advanced technologies, such as IoT-enabled machinery and AI-driven analytics, can help identify inefficiencies in production processes and implement solutions that reduce costs and increase throughput.
Another key objective is customer satisfaction. In a world where consumer demands are constantly evolving, manufacturers must become more agile and responsive. Digital tools enable real-time tracking of production and supply chain operations, ensuring that products are delivered on time and customized to meet specific customer needs. Additionally, predictive maintenance minimizes production delays, resulting in higher reliability and trust among customers.
Sustainability and compliance are becoming increasingly important in manufacturing. Digital transformation offers powerful tools for reducing energy consumption, minimizing waste, and adhering to environmental regulations. For instance, real-time energy monitoring systems can identify areas of excessive energy use, while automated quality control systems reduce material waste by catching defects early in the process. By aligning transformation efforts with sustainability goals, manufacturers can not only reduce costs but also improve their environmental impact and brand reputation.
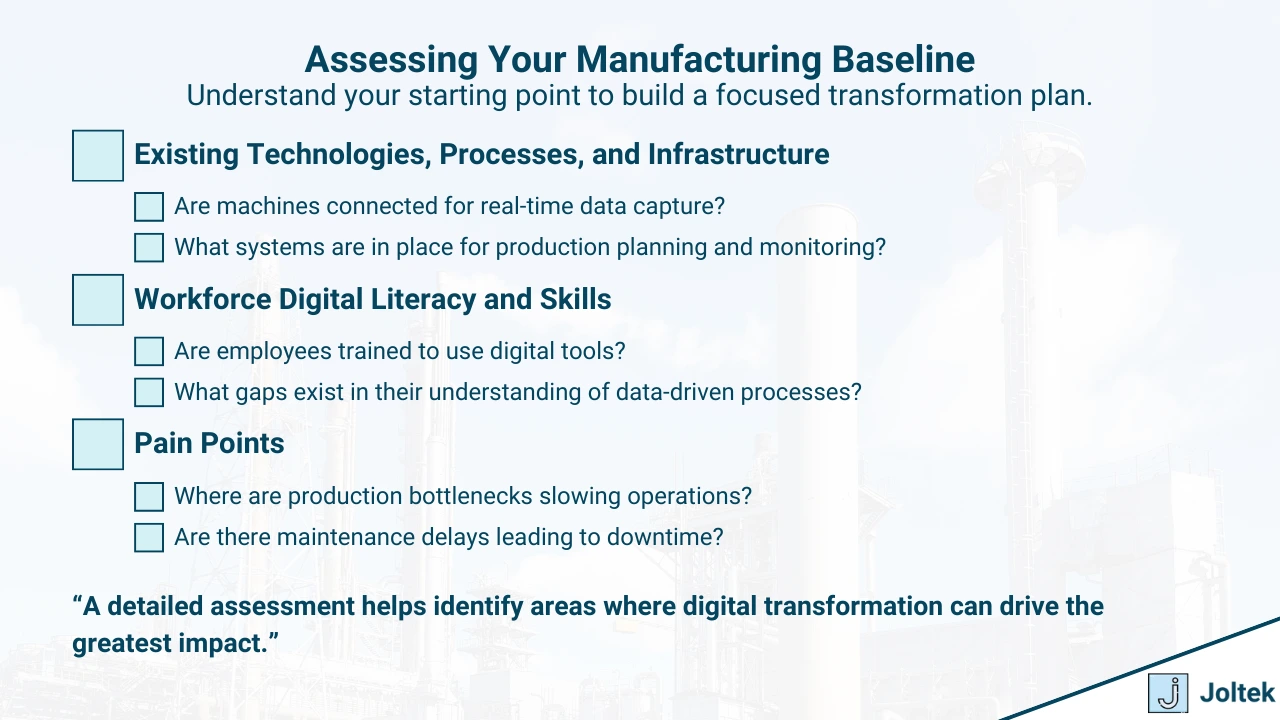
Setting Measurable KPIs
To ensure that the transformation delivers tangible results, it is essential to establish clear and measurable key performance indicators (KPIs). These metrics provide a way to track progress, evaluate the success of individual initiatives, and make data-driven decisions throughout the transformation journey.
One commonly used KPI is overall equipment effectiveness (OEE), which measures the productivity of machinery by combining data on availability, performance, and quality. A high OEE indicates that equipment is running efficiently and producing high-quality products with minimal downtime.
Downtime reduction is another critical metric. By implementing predictive maintenance and real-time monitoring, manufacturers can significantly reduce unplanned equipment failures and ensure smooth production processes. Tracking downtime trends can help pinpoint persistent issues and guide future improvements.
Waste reduction serves as both an economic and environmental KPI. By optimizing production processes, manufacturers can minimize material waste, improve yields, and reduce their overall environmental footprint. Digital tools such as AI-driven defect detection and smart inventory management systems play a significant role in achieving this goal.
With a well-defined vision and clear KPIs in place, manufacturers can ensure that their digital transformation efforts remain focused, measurable, and impactful. These objectives provide a roadmap for evaluating progress and aligning every initiative with broader business strategies.
1.3 Engaging Key Stakeholders
A successful digital transformation in manufacturing requires the involvement and alignment of key stakeholders across the organization. These stakeholders play critical roles in ensuring that the transformation plan is not only well-designed but also effectively executed. By engaging the right people early in the process, manufacturers can foster collaboration, build consensus, and address potential challenges before they become obstacles.
Identifying Stakeholders
Digital transformation touches every aspect of a manufacturing organization, from strategy and technology to day-to-day operations. Identifying the key stakeholders and understanding their roles in the process is essential to create a cohesive plan.
Leadership serves as the cornerstone of the transformation effort. Executives and senior leaders are responsible for aligning digital initiatives with the organization’s overall strategic objectives. Their support is vital for securing the necessary funding and resources while setting the tone for change across the company. Leaders must champion the transformation, clearly communicate its importance, and ensure it remains a top priority.
IT teams are the architects of technological integration. They evaluate, implement, and maintain the digital systems that form the backbone of the transformation. Their expertise ensures that new technologies are compatible with existing infrastructure, secure, and scalable for future growth. IT teams also play a key role in addressing cybersecurity concerns and ensuring data integrity.
Operations managers provide a bridge between strategy and execution. They assess the feasibility of implementing new technologies on the shop floor, identifying potential operational disruptions and crafting solutions to mitigate them. Their insights ensure that digital tools are aligned with production goals and can be seamlessly integrated into existing workflows.
Shop floor workers are the end users of many digital transformation initiatives, making their buy-in and adoption critical to success. These employees interact directly with new systems, tools, and processes. Ensuring usability and providing comprehensive training helps build their confidence and reduces resistance to change. Engaging workers early can also uncover valuable feedback about what works best in real-world conditions.
Creating a Governance Framework for Decision-Making
Once stakeholders are identified, it’s important to establish a governance framework to guide decision-making throughout the transformation process. This framework defines roles, responsibilities, and processes for evaluating and approving initiatives, ensuring accountability and alignment with organizational goals.
A robust governance framework typically includes a cross-functional steering committee composed of representatives from leadership, IT, operations, and other critical departments. This committee oversees the transformation plan, prioritizes initiatives, allocates resources, and resolves conflicts. Regular meetings and progress reviews ensure that the transformation stays on track and adapts to emerging challenges or opportunities.
Transparent communication is a cornerstone of effective governance. Stakeholders at all levels should have access to updates, milestones, and key decisions. This fosters trust and ensures that everyone involved understands their role in the transformation journey.
By engaging the right stakeholders and creating a structured governance framework, manufacturers can build a strong foundation for collaboration and accountability. These efforts not only drive alignment across the organization but also help overcome resistance and ensure smooth execution of the transformation plan.
Section 2: Crafting the Digital Transformation Plan
With a clear understanding of the organization’s current state, vision, and stakeholder alignment, the next step is to develop a practical and focused digital transformation plan. This phase involves prioritizing initiatives that will deliver measurable results while setting the stage for long-term growth and scalability.
2.1 Prioritizing Initiatives
Not all digital transformation projects carry the same level of urgency or impact. To ensure a structured and efficient approach, manufacturers must carefully evaluate and segment potential initiatives based on their expected outcomes and feasibility.
Segmentation of Initiatives
The first step is to categorize initiatives into two primary groups: quick wins and long-term strategies.
Quick wins are projects that can be implemented relatively quickly and with minimal resources. These initiatives deliver immediate, tangible benefits and help build momentum for broader transformation efforts. For example, adding IoT sensors to a specific production line to monitor machine performance in real-time could be a manageable starting point. Such projects also serve as proof-of-concept, demonstrating the value of digital tools to stakeholders and employees.
In contrast, long-term strategies involve complex, large-scale transformations that require significant investment and planning. These initiatives often redefine core business processes and have a more substantial impact on the organization’s competitive edge. Examples include deploying advanced robotics for automated manufacturing or integrating an AI-driven supply chain optimization system. While these efforts take longer to yield results, their potential ROI can be transformative.
High-ROI Opportunities
Another critical factor in prioritization is the potential return on investment (ROI). By evaluating the costs, risks, and expected benefits of each initiative, manufacturers can focus on projects that promise the highest value. High-ROI opportunities often address major inefficiencies or provide competitive advantages, such as reducing production downtime, increasing throughput, or improving customer responsiveness.
Example Initiatives
When prioritizing initiatives, it’s helpful to explore specific examples that align with common objectives in manufacturing digital transformation:
- Implementing IoT for Predictive Maintenance
Predictive maintenance is a practical application of IoT that addresses one of the most pressing challenges in manufacturing—unplanned downtime. By equipping machinery with IoT sensors, manufacturers can continuously monitor equipment performance and detect potential issues before they lead to failures. This not only reduces repair costs but also extends the lifespan of critical assets and improves overall operational efficiency. - Adopting ERP Systems for Better Resource Planning
Enterprise resource planning (ERP) systems are another foundational technology for manufacturing transformation. These platforms centralize and integrate data across departments, enabling real-time insights into inventory, production schedules, and supply chain performance. With an ERP system, manufacturers can improve resource allocation, streamline workflows, and enhance decision-making capabilities. Modern cloud-based ERP solutions also offer scalability and flexibility, making them ideal for organizations looking to grow.
By segmenting and prioritizing initiatives like these, manufacturers can ensure that their digital transformation efforts deliver meaningful results early while paving the way for broader, long-term changes.
2.2 Technology Selection
Selecting the right technologies is one of the most critical steps in crafting a digital transformation plan. With countless options available, manufacturers must carefully evaluate which tools and platforms align best with their operational needs and strategic goals. This involves not only identifying suitable technologies but also ensuring they can integrate seamlessly into existing systems and scale with future growth.
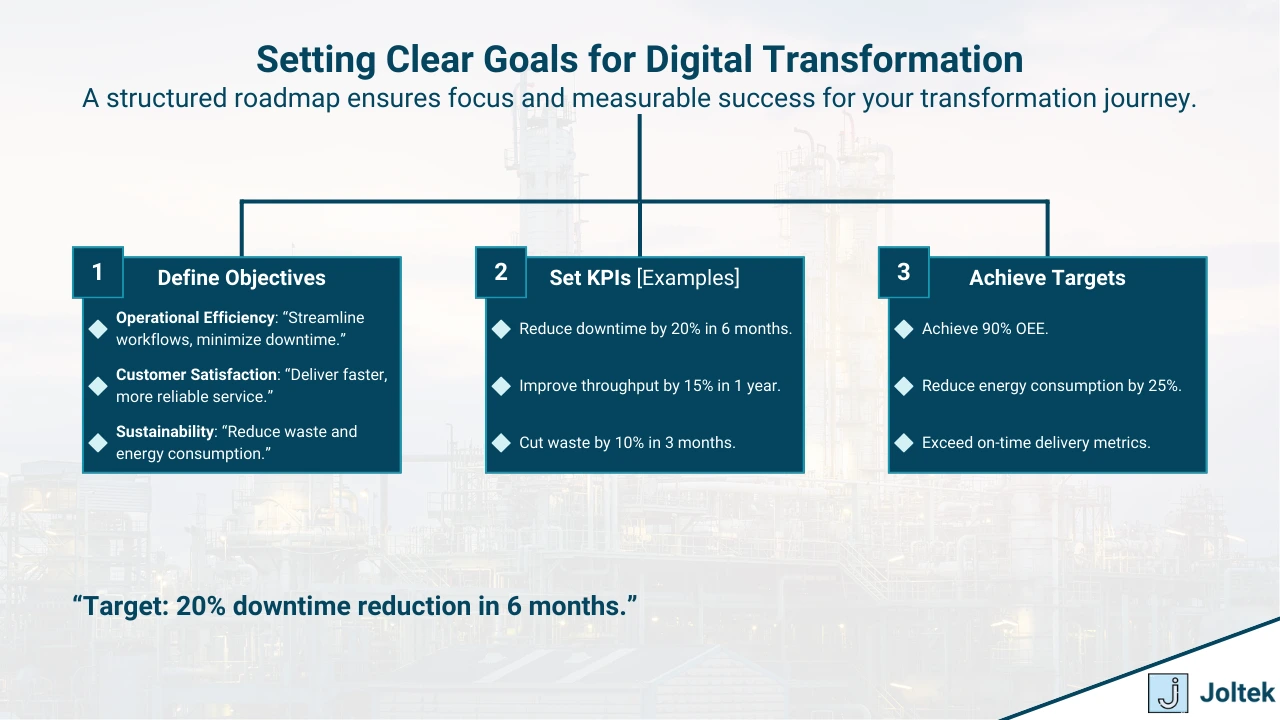
Evaluating and Selecting Technologies
Several cutting-edge technologies are driving digital transformation in manufacturing. Each offers unique capabilities to address specific challenges, enhance efficiency, and unlock new opportunities.
IoT, AI, and Machine Learning
The Internet of Things (IoT) connects machines, devices, and systems, enabling real-time data collection and analysis. When paired with artificial intelligence (AI) and machine learning, IoT data can be used to predict equipment failures, optimize workflows, and uncover patterns that would otherwise go unnoticed. For example, AI-driven analytics can analyze sensor data from production lines to forecast demand and dynamically adjust schedules, improving overall efficiency.
Digital Twins and Simulation Tools
Digital twins create virtual replicas of physical assets, such as machines or entire production facilities. These tools allow manufacturers to simulate operations, test changes, and predict outcomes without disrupting actual production. By using digital twins, organizations can optimize performance, reduce risks, and make data-driven decisions about process improvements or new product designs.
Advanced Robotics and Automation
Automation is at the core of modern manufacturing transformation. Advanced robotics, powered by AI, can handle complex tasks with precision, speed, and reliability. From collaborative robots (cobots) that work alongside human operators to fully autonomous systems, robotics solutions can significantly enhance productivity while reducing labor costs and human error.
Criteria for Evaluation
Choosing the right technologies requires careful consideration of several key factors to ensure that the solutions deliver value both now and in the future.
Scalability
Digital transformation is not a one-time project; it’s an ongoing process that evolves with the business. Technologies must be scalable to accommodate growth, whether that means expanding to additional production lines, integrating with new systems, or handling increased data volumes. For example, cloud-based platforms often provide the flexibility to scale resources up or down as needed.
Interoperability
Manufacturing environments typically involve a mix of legacy equipment and modern systems. New technologies must be able to integrate seamlessly with existing infrastructure to avoid costly disruptions. Solutions that adhere to open standards and offer robust APIs are often better suited for achieving interoperability.
Vendor Support and Security
The success of a technology implementation often depends on the quality of vendor support. Reliable vendors should offer comprehensive training, technical assistance, and ongoing updates to ensure the technology remains effective and secure. Additionally, robust cybersecurity measures are essential to protect sensitive manufacturing data from breaches, particularly as more systems become connected through IoT.
By carefully evaluating technologies based on their capabilities, scalability, interoperability, and vendor support, manufacturers can make informed decisions that maximize the value of their investments. This thoughtful selection process ensures that every tool or platform contributes to the organization’s long-term transformation goals.
2.3 Building a Scalable Data Strategy
Data lies at the heart of digital transformation, serving as the foundation for informed decision-making, process optimization, and predictive capabilities. A robust and scalable data strategy ensures that manufacturers can effectively capture, process, and utilize information to drive operational improvements and support long-term growth.
Data as the Backbone of Transformation
One of the most transformative aspects of digital manufacturing is the ability to collect and leverage real-time production data. With IoT sensors embedded in machinery and systems, manufacturers can continuously monitor critical parameters such as equipment performance, energy usage, and product quality. This real-time data enables proactive responses to issues, such as addressing equipment inefficiencies before they lead to downtime.
Once data is collected, it must be presented in a way that facilitates actionable insights. Centralized dashboards play a pivotal role in this process. These dashboards aggregate data from multiple sources—such as production lines, supply chains, and inventory systems—into a single, user-friendly interface. With this centralized approach, decision-makers can access real-time performance metrics, identify trends, and quickly respond to emerging challenges or opportunities. For example, a dashboard might highlight a spike in energy consumption, prompting immediate investigation and resolution.
Addressing Data Challenges
Despite its immense potential, building a data strategy comes with challenges, particularly in the manufacturing sector where legacy systems and regulatory requirements can create hurdles.
Integration of Legacy Systems
Many manufacturers operate in environments where older, analog machinery coexists with modern, digital tools. Integrating these legacy systems into a cohesive data ecosystem can be a daunting task. However, solutions such as IoT gateways, middleware, and APIs can help bridge this gap. These technologies enable older equipment to communicate with newer platforms, ensuring that critical data is not lost or siloed. For example, an IoT gateway might convert analog machine outputs into digital data streams that can be analyzed in real-time.
Ensuring Data Privacy and Compliance
As data becomes increasingly central to manufacturing operations, ensuring its security and compliance with regulatory standards is paramount. Cybersecurity risks, such as data breaches or ransomware attacks, can disrupt operations and expose sensitive information. To mitigate these risks, manufacturers must implement robust data encryption, access controls, and regular system audits.
Additionally, compliance with data protection regulations—such as GDPR in Europe or CCPA in California—requires careful handling of personal and operational data. Manufacturers must establish clear policies for data storage, access, and sharing to remain compliant while maintaining operational efficiency.
By focusing on capturing real-time production data, creating actionable dashboards, and addressing challenges like legacy system integration and data security, manufacturers can build a scalable data strategy that supports their digital transformation efforts. This approach not only drives operational improvements but also ensures that the organization is prepared for future technological advancements.
3.1 Developing a Pilot Program
Execution begins with testing the waters—this is where a well-designed pilot program comes into play. A pilot project allows manufacturers to implement a smaller-scale version of their digital transformation initiative, reducing risk and offering valuable insights before a full-scale rollout. This phase is essential for identifying potential challenges, refining solutions, and building confidence among stakeholders.
Selecting a Pilot Project
The success of a pilot program hinges on selecting the right project. The scope should be narrow enough to ensure manageability but impactful enough to demonstrate the value of the transformation initiative. A focused project minimizes complexity while providing measurable outcomes that can serve as proof of concept.
For instance, deploying IoT sensors on a single production line can be an excellent starting point. These sensors can monitor equipment performance in real-time, providing data on metrics such as uptime, energy consumption, and temperature fluctuations. By limiting the pilot to one line, manufacturers can control costs and gain insights without disrupting broader operations. Additionally, the lessons learned from this specific scenario can inform larger implementations across the facility.
Defining Success Criteria and Benchmarks
Establishing clear success criteria is crucial for evaluating the effectiveness of a pilot program. These criteria should align with the broader goals of the digital transformation plan, such as improving efficiency, reducing downtime, or enhancing product quality.
For example, in the IoT pilot project mentioned earlier, success might be defined by achieving a specific percentage reduction in unplanned downtime over a three-month period. Other benchmarks could include improvements in overall equipment effectiveness (OEE), reduced energy consumption, or faster response times to maintenance alerts. The key is to select metrics that are both measurable and meaningful to the organization’s strategic objectives.
It’s also important to set a timeline for the pilot program and establish checkpoints for reviewing progress. Regular assessments ensure that the project stays on track and allows for adjustments as needed. Stakeholders should be kept informed throughout the process, fostering transparency and alignment.
A well-executed pilot program not only provides valuable data but also builds momentum for broader transformation efforts. By starting small and defining clear benchmarks, manufacturers can mitigate risks, gain insights, and demonstrate the tangible benefits of digital initiatives.
3.2 Scaling Successful Pilots
Once a pilot program has demonstrated its value and feasibility, the next step is to expand the initiative across the organization. Scaling successful pilots ensures that the benefits observed in a limited scope—such as increased efficiency, reduced downtime, or improved quality—are realized on a broader scale. This phase requires careful planning to account for the complexities of larger-scale implementation.
Rolling Out Across Departments or Facilities
Scaling a pilot begins by replicating its success in other departments or facilities. The lessons learned during the pilot phase provide a roadmap for broader implementation, helping to mitigate risks and streamline the process.
For instance, if an IoT-enabled predictive maintenance program was tested on a single production line, the next step might involve deploying the technology across multiple lines within the same facility. After achieving stability, the solution can then be extended to other locations, ensuring consistency in processes and outcomes.
However, the rollout process must account for the unique challenges and variables of each new environment. Different production lines or facilities may have distinct workflows, equipment, or levels of digital readiness. A thorough assessment of each context is critical to adapting the solution effectively. For example, training requirements may differ across teams, or additional equipment modifications might be needed for compatibility.
Standardizing the implementation process wherever possible can help maintain consistency and reduce redundancies. At the same time, creating a flexible framework allows for adjustments to accommodate local variations.
Customizing Solutions Based on Pilot Feedback
Feedback from the pilot program is invaluable for refining and customizing solutions during the scaling phase. Any issues encountered—whether related to technology, workflows, or user adoption—should be analyzed and addressed before broader deployment.
For example, if operators in the pilot reported difficulties interpreting IoT data dashboards, these insights could prompt the development of more intuitive user interfaces or additional training programs. Similarly, technical glitches identified during the pilot can guide system optimizations to ensure smoother operation at scale.
Customization also involves tailoring the solution to the specific needs of each department or facility. While the core technology or process might remain the same, the way it’s implemented may vary. For instance, some facilities might require additional sensors or different maintenance protocols to account for variations in equipment or usage patterns.
Effective communication and collaboration across departments are critical during this phase. Engaging teams early and incorporating their feedback fosters a sense of ownership, improving adoption rates and long-term success.
By scaling successful pilots methodically and customizing solutions based on real-world insights, manufacturers can maximize the impact of their digital transformation initiatives. This approach ensures that the benefits of innovation are felt consistently across the organization while minimizing risks and disruptions.
3.3 Workforce Enablement
No digital transformation can succeed without the active participation and support of the workforce. Employees are the ones who operate the tools, adopt the workflows, and drive the changes required to realize the full potential of transformation initiatives. Workforce enablement ensures that employees have the knowledge, skills, and mindset needed to embrace new technologies and thrive in a digital-first environment.
Training Employees on New Tools and Workflows
Introducing new tools and workflows often requires comprehensive training to ensure employees can use them effectively. Training programs should be tailored to the specific needs of different roles within the organization. For example, shop floor operators might need hands-on training to use IoT dashboards or automated machinery, while managers may require instruction on interpreting data analytics reports to make strategic decisions.
Effective training goes beyond technical instructions—it also emphasizes the “why” behind the transformation. Employees should understand how the new tools will benefit them directly, whether by reducing repetitive tasks, improving safety, or enhancing overall job performance. This understanding helps build enthusiasm and reduces resistance to change.
Employers can leverage a variety of methods to deliver training, including workshops, e-learning modules, on-the-job mentoring, and vendor-led sessions. Ongoing support, such as a help desk or on-demand tutorials, ensures employees feel confident even after the initial training phase.
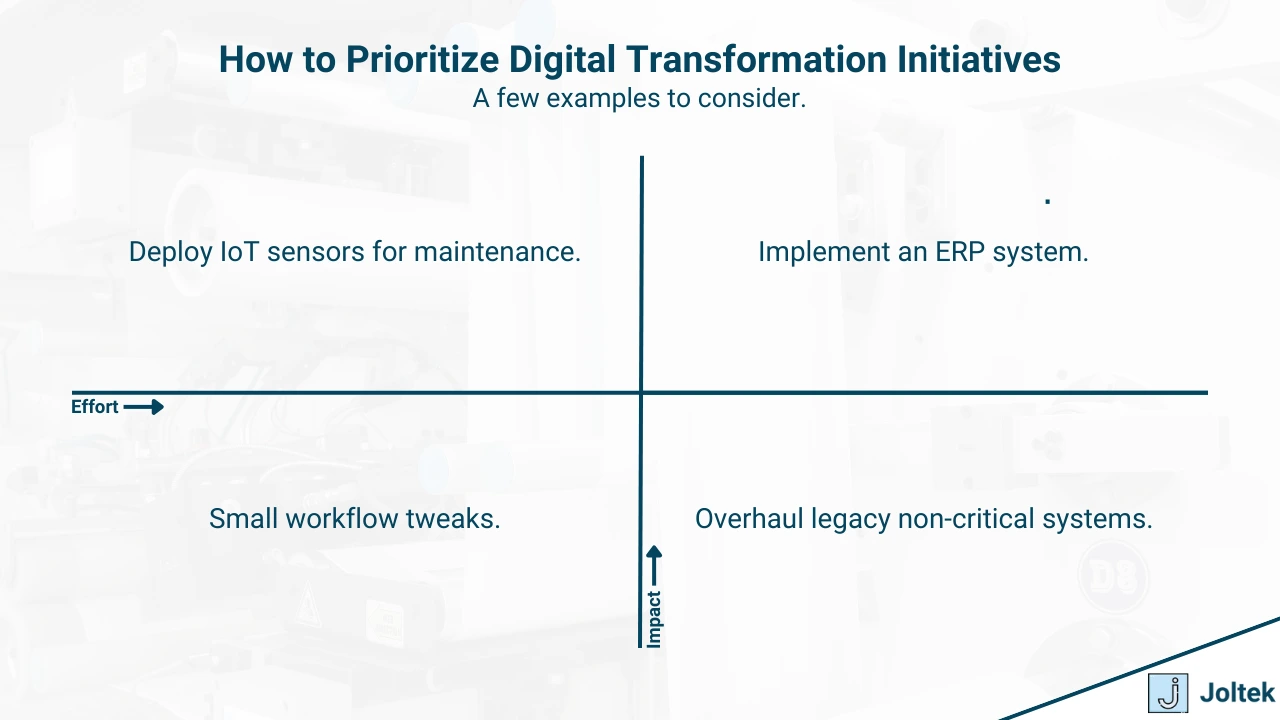
Upskilling Initiatives for Handling Digital Tools
As manufacturing becomes increasingly digitized, some roles may evolve to require more advanced skills, such as data interpretation, programming, or equipment troubleshooting. Upskilling initiatives address this need by equipping employees with the expertise required to operate in a digital-first environment.
For example, maintenance staff might need to learn how to interpret IoT sensor data to predict equipment failures, while quality assurance teams may need training in using AI-driven defect detection systems. These programs not only improve individual capabilities but also help retain talent by demonstrating the company’s investment in their professional growth.
Upskilling can also prepare employees for new roles created by digital transformation, such as data analysts, automation engineers, or digital workflow specialists. By promoting internal mobility, organizations can maximize the potential of their existing workforce while reducing the need for external hires.
Building a Culture of Continuous Improvement
Beyond skills training, workforce enablement involves fostering a culture that embraces change and prioritizes continuous improvement. Digital transformation is not a one-time event—it’s an ongoing process that requires employees to adapt to new technologies, workflows, and challenges over time.
To build this culture, leadership must actively encourage feedback, experimentation, and innovation. Employees should feel empowered to suggest improvements, experiment with new methods, and share lessons learned. For example, teams might hold regular retrospectives to discuss what’s working, what isn’t, and how to refine their processes.
Recognition and rewards can also play a key role in reinforcing a culture of improvement. Acknowledging employees who excel at adopting new tools or finding innovative ways to leverage technology helps motivate others to do the same.
Workforce enablement ensures that employees are not only equipped to handle the immediate demands of digital transformation but are also prepared to navigate its ongoing evolution. By investing in training, upskilling, and cultural development, manufacturers can create a resilient and adaptable workforce that drives long-term success.
3.4 Partnering for Success
Digital transformation in manufacturing often requires expertise and resources beyond what internal teams can provide. Strategic partnerships with technology providers and consultants play a vital role in ensuring the success of transformation initiatives. These collaborations bring specialized knowledge, technical support, and tools to help manufacturers implement solutions effectively and sustain them over time.
Collaboration with Technology Providers and Consultants
Technology providers and consultants are invaluable partners in designing and executing digital transformation projects. These external experts offer insights into the latest advancements, best practices, and industry trends that manufacturers might not be familiar with.
Collaborating with technology providers enables manufacturers to choose and implement the right solutions for their needs. Providers often have extensive experience with similar projects and can recommend technologies tailored to specific challenges, such as IoT platforms for predictive maintenance or ERP systems for supply chain optimization. Their expertise ensures smoother integration with existing systems and minimizes disruptions during implementation.
Consultants, on the other hand, bring a broader perspective. They help manufacturers align technology investments with strategic goals, assess risks, and prioritize initiatives. For instance, a consultant might conduct a cost-benefit analysis to determine which digital tools will deliver the highest ROI or assist in developing a roadmap for phased implementation.
These partnerships are especially valuable for addressing complex challenges, such as integrating legacy systems, implementing cybersecurity protocols, or scaling pilots across multiple facilities. By leveraging the experience of external partners, manufacturers can accelerate their transformation journey while avoiding common pitfalls.
Establishing Vendor Support Contracts
A critical component of successful partnerships is ensuring ongoing support from technology vendors. Vendor support contracts formalize the relationship and provide manufacturers with the resources needed to maintain, optimize, and troubleshoot their systems.
Comprehensive vendor support often includes services such as regular software updates, 24/7 technical assistance, and proactive system monitoring. These services help prevent downtime, address vulnerabilities, and keep systems running at peak efficiency. For example, a vendor might remotely monitor IoT sensors in a manufacturing facility and alert the team to potential issues before they escalate.
Support contracts also facilitate knowledge transfer. Vendors can provide training sessions for employees, ensuring they understand how to use the technology effectively. They may also offer user-friendly documentation, tutorials, and access to online communities for troubleshooting and learning.
When establishing vendor contracts, manufacturers should consider factors such as service level agreements (SLAs), response times for critical issues, and scalability options. Clear terms and expectations help build a strong, reliable partnership that evolves as the manufacturer’s needs grow.
By collaborating with technology providers and consultants and securing robust vendor support contracts, manufacturers can enhance the implementation and sustainability of their digital transformation efforts. These partnerships provide the technical expertise and ongoing assistance needed to navigate complex challenges and ensure long-term success.
4.1 Continuous Monitoring
Digital transformation is not a one-and-done initiative—it requires ongoing oversight to ensure that new tools and processes continue to deliver value. Continuous monitoring allows manufacturers to track the performance of their digital systems, measure progress against goals, and identify areas for improvement. This dynamic approach helps organizations stay agile and responsive in a rapidly evolving industrial landscape.
Using KPIs to Measure Progress
Key performance indicators (KPIs) play a central role in monitoring the success of digital transformation efforts. These metrics provide a quantitative view of how well the organization is achieving its objectives, whether it’s improving efficiency, reducing costs, or enhancing product quality.
For instance, a manufacturer might monitor KPIs such as downtime reduction and throughput improvement to assess the impact of IoT-enabled predictive maintenance. If downtime decreases by 20% and production output increases as expected, it’s a clear sign that the initiative is delivering value. Similarly, tracking metrics like overall equipment effectiveness (OEE) or energy consumption can reveal whether automated systems are optimizing operations as planned.
Real-time dashboards, powered by data visualization tools, are invaluable for KPI tracking. These dashboards aggregate data from across the organization, presenting it in a clear, actionable format. This enables decision-makers to quickly identify trends, compare performance across departments, and address deviations from goals.
Regular Performance Reviews with Stakeholders
While KPIs provide the data, regular performance reviews with stakeholders turn that data into actionable insights. These reviews serve as checkpoints to evaluate progress, discuss challenges, and align on next steps. Engaging key stakeholders—including leadership, operations managers, IT teams, and shop floor supervisors—ensures that everyone involved in the transformation effort remains informed and invested.
During these reviews, stakeholders can assess whether the transformation initiatives are meeting expectations or require adjustments. For example, if predictive maintenance solutions are not reducing downtime as anticipated, stakeholders might explore potential causes, such as insufficient sensor coverage or inaccurate data analysis. Collaborative discussions foster problem-solving and ensure that all perspectives are considered in decision-making.
Performance reviews also provide an opportunity to celebrate successes and recognize the contributions of employees. Highlighting achievements, such as meeting or exceeding KPI targets, reinforces the value of the transformation effort and motivates teams to maintain their commitment.
Continuous monitoring, supported by meaningful KPIs and regular stakeholder reviews, ensures that digital transformation efforts remain on track and deliver sustained value. By maintaining a feedback loop of measurement and analysis, manufacturers can adapt to challenges, seize new opportunities, and build resilience in an ever-changing industry.
4.2 Iterative Optimization
Digital transformation is a journey, not a destination. Even after successful implementation, gaps or challenges may arise during real-world application. Iterative optimization ensures that manufacturers continuously improve their systems, processes, and technologies to adapt to evolving demands and maximize the value of transformation efforts.
Addressing Gaps or Challenges from Initial Rollouts
Initial rollouts, even when carefully planned, can reveal unforeseen challenges. These might include unexpected compatibility issues, inefficiencies in workflows, or lower-than-expected user adoption. Continuous monitoring during and after implementation helps uncover these gaps, providing actionable insights for improvement.
For example, if IoT sensors deployed during a pilot phase fail to capture accurate data due to environmental conditions, adjustments might include upgrading hardware or recalibrating sensors. Similarly, if employees encounter difficulties using a new system, manufacturers can refine training programs or simplify interfaces to improve usability.
Open communication with stakeholders is critical during this phase. Feedback from shop floor workers, operations managers, and IT teams often highlights pain points that data alone might not reveal. Addressing these gaps iteratively ensures the transformation stays on course and delivers the intended results.
Refining Processes and Updating Systems Based on Feedback
Feedback-driven refinement is a cornerstone of iterative optimization. By analyzing performance data and stakeholder input, manufacturers can make incremental updates to systems and processes. These updates might involve reconfiguring software, automating additional steps in production workflows, or fine-tuning machine learning algorithms for better accuracy.
Regularly revisiting KPIs helps measure the effectiveness of these refinements. If a specific adjustment—such as changing machine settings based on predictive analytics—leads to measurable improvements in throughput or quality, it validates the optimization efforts. This iterative cycle of feedback and improvement ensures that the organization continues to adapt and thrive in a dynamic market.
4.3 Ensuring Long-Term Sustainability
A successful digital transformation must be future-proof, aligning with industry trends and preparing for ongoing technological advancements. Ensuring sustainability requires both a strategic outlook and proactive adaptation to new developments.
Aligning Transformation with Industry Trends and Regulations
Manufacturing trends, such as the push for sustainability, increasing automation, and the adoption of circular economy practices, are reshaping the industry. Manufacturers must align their transformation efforts with these trends to remain competitive and compliant.
For example, many manufacturers are incorporating green technologies to reduce energy consumption and carbon emissions. Digital tools like real-time energy monitoring and AI-driven optimization play a key role in achieving these goals. Additionally, compliance with evolving regulations, such as environmental standards or data protection laws, must be integrated into the transformation strategy to avoid legal and reputational risks.
Preparing for Future Advancements
The pace of technological innovation demands that manufacturers remain adaptable and forward-looking. Emerging technologies like 5G, autonomous manufacturing, and advanced robotics hold the potential to further revolutionize operations. Preparing for these advancements involves building scalable systems and fostering a culture of continuous learning within the organization.
For instance, 5G connectivity promises to enhance the speed and reliability of IoT systems, enabling real-time decision-making on an unprecedented scale. Manufacturers that have already implemented IoT infrastructure will be better positioned to leverage this advancement with minimal disruption. Similarly, adopting flexible automation systems today lays the groundwork for integrating autonomous manufacturing solutions in the future.
Future-proofing also requires ongoing investments in workforce development, ensuring employees are equipped to handle the next wave of digital tools and processes. Upskilling initiatives and partnerships with technology providers can help organizations stay ahead of the curve.
By addressing gaps iteratively and aligning transformation efforts with long-term industry trends, manufacturers can ensure their digital initiatives remain relevant and impactful. These strategies not only sustain success but also position the organization to capitalize on future opportunities.
Conclusion
Digital transformation in manufacturing is a powerful catalyst for innovation, efficiency, and growth. However, its success hinges on a well-structured plan. Without a thoughtful and phased approach, organizations risk encountering inefficiencies, wasted resources, and resistance to change. By laying a solid foundation, engaging stakeholders, selecting the right technologies, and continuously optimizing processes, manufacturers can unlock the full potential of digital transformation.
The opportunities for innovation are immense. From leveraging IoT to predict equipment failures, to employing AI for data-driven decision-making, and using digital twins to simulate operations, the possibilities are limited only by imagination and readiness. These advancements not only improve operational efficiency but also open new avenues for customer satisfaction, sustainability, and competitiveness in an evolving global market.
Starting small is key. A focused pilot project provides a controlled environment for testing technologies, addressing challenges, and gathering insights. As these initiatives demonstrate their value, manufacturers can scale them across the organization, ensuring both scalability and consistency. This approach reduces risk while building confidence and momentum.
The journey of digital transformation is ongoing, and the steps outlined here provide a practical roadmap for navigating its complexities. Manufacturers ready to embrace this change will find themselves better equipped to adapt, innovate, and thrive in the future of industry.
Now is the time to act. Begin with a single step—a pilot program, a technology upgrade, or a workforce training initiative—and grow from there. The path may be challenging, but the rewards are transformational, setting the stage for a more efficient, innovative, and resilient manufacturing operation.
Are you ready to embark on this journey? Your digital transformation begins today.
Call to Action
“Is your manufacturing business ready for digital transformation? Start crafting your tailored plan today to embrace innovation, drive efficiency, and stay ahead in the competitive landscape. Don’t wait—take the first step toward a smarter, more sustainable future!”