Introduction
In the manufacturing sector, compliance risk assessment is a systematic process of identifying, analyzing, and addressing potential risks associated with regulatory and operational compliance. It serves as a cornerstone for organizations to ensure that their operations align with legal, ethical, and industry standards, safeguarding their long-term success.
The importance of compliance risk assessment cannot be overstated. It plays a critical role in achieving several objectives that are vital for manufacturing businesses:
- Ensuring adherence to regulations: Regulatory requirements in manufacturing can range from environmental standards and worker safety protocols to product quality specifications. A robust compliance risk assessment helps organizations navigate this complex landscape, reducing the likelihood of legal penalties or operational disruptions.
- Mitigating operational and financial risks: Non-compliance often leads to fines, production halts, or supply chain interruptions. By proactively addressing potential risks, companies can protect their financial health and maintain smooth operations.
- Protecting organizational reputation and customer trust: In today’s competitive market, reputation is everything. Customers and stakeholders expect manufacturers to uphold high standards of compliance. Any deviation can erode trust and tarnish the brand’s image.
- Facilitating continuous improvement and business continuity: Beyond meeting immediate regulatory demands, compliance risk assessments foster a culture of continuous improvement. By identifying areas for enhancement, manufacturers can ensure sustainable growth and resilience against future challenges.
In essence, compliance risk assessment is not just about avoiding penalties; it is a strategic tool for building a resilient, trustworthy, and efficient organization in an ever-evolving regulatory landscape.
General Compliance in Manufacturing
Compliance in manufacturing encompasses adherence to a broad range of regulatory, industry, and organizational standards. It ensures manufacturers meet legal, ethical, and operational requirements to sustain their businesses and maintain a competitive edge. Below, we explore the critical aspects of compliance management in the manufacturing sector.
Regulatory Compliance
Manufacturing industries must navigate a complex web of regulations, including environmental laws, workplace safety standards, and product quality requirements. Key regulations such as OSHA (Occupational Safety and Health Administration) in the U.S., REACH (Registration, Evaluation, Authorization, and Restriction of Chemicals) in the EU, and sector-specific mandates like FDA guidelines for medical devices demand strict adherence.
Proactive compliance strategies, such as staying updated on regulatory changes and fostering a culture of compliance, are essential to mitigate risks and ensure smooth operations.
Compliance Audits
Compliance audits are a structured approach to evaluating whether a manufacturing organization adheres to applicable regulations and standards. These audits typically involve:
- Assessing policies, procedures, and records to verify compliance.
- Identifying gaps and recommending corrective actions.
Tools like compliance management software help track audit results, generate reports, and monitor progress over time, making audits more effective and less burdensome.
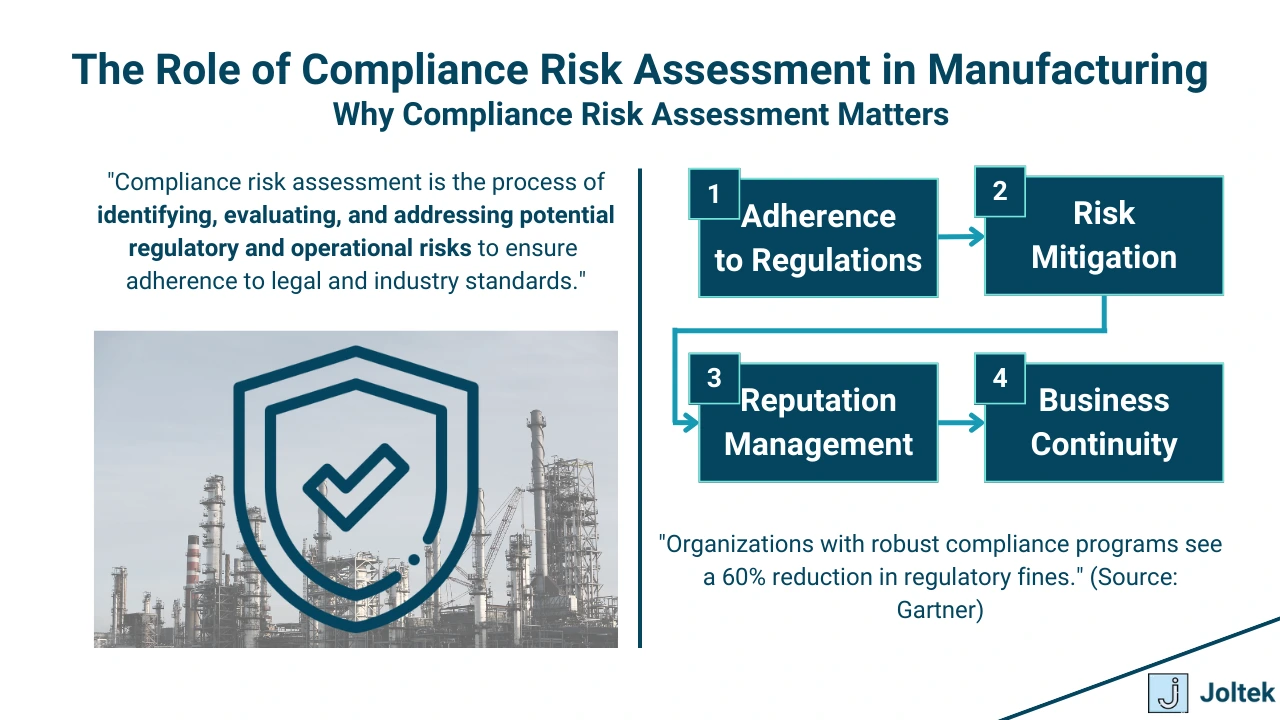
Compliance Frameworks
An integrated compliance framework helps streamline compliance management by bringing various regulatory, operational, and industry standards under one umbrella. For multinational manufacturers, adopting global standards like ISO 19600 (Compliance Management Systems) ensures consistent practices across borders and reduces the complexity of managing regional variations.
Industry Standards and Certification Requirements
Industry-specific certifications, such as ISO 9001 for quality management, ISO 14001 for environmental management, and FDA approvals, validate a manufacturer's commitment to excellence. These certifications not only enhance operational efficiency but also improve market credibility, fostering customer trust and opening new business opportunities.
Compliance Management and Monitoring
Technology plays a pivotal role in modern compliance management. Automated systems enable real-time monitoring of compliance metrics, reducing the risk of human error. Developing key performance indicators (KPIs) specific to compliance, such as incident rates or audit findings resolved within a set timeframe, provides measurable benchmarks for success.
Penalties for Non-Compliance
The consequences of non-compliance can be severe, ranging from hefty fines and operational shutdowns to reputational damage. For instance, companies like Volkswagen faced billions in penalties and significant public backlash for non-compliance with emissions regulations. Such cases highlight the importance of investing in robust compliance strategies to avoid similar pitfalls.
In conclusion, a well-structured approach to compliance ensures that manufacturers not only meet their regulatory obligations but also build a foundation for sustainable growth, operational excellence, and stakeholder confidence.
Risk Assessment in Manufacturing
Risk assessment in manufacturing is a critical process for identifying, evaluating, and mitigating potential risks that could disrupt operations or lead to non-compliance. By understanding and addressing risks at various levels, manufacturers can enhance their resilience, maintain regulatory adherence, and safeguard their operational efficiency. This section outlines the key elements of compliance risk assessment in manufacturing.
Risk Identification and Prioritization
The first step in risk assessment is identifying compliance risks across all operational levels, from supply chain management to production processes. These risks might include:
- Environmental hazards: Non-compliance with emissions or waste disposal standards.
- Workplace safety risks: Potential violations of safety protocols or equipment standards.
- Product quality concerns: Issues with material specifications or adherence to regulatory approvals.
Once identified, risks are categorized based on their nature—legal, operational, financial, or reputational. Prioritization techniques, such as risk scoring or heat maps, are employed to focus efforts on the most critical risks with the highest likelihood and impact.
Risk Mitigation Strategies
Effective risk mitigation involves developing detailed response plans tailored to each risk category. Strategies may include:
- Implementing new safety measures or protocols.
- Investing in training programs to enhance employee awareness of compliance standards.
- Upgrading equipment or technology to meet current regulations.
The challenge lies in balancing risk reduction with operational efficiency. Overzealous measures might hinder productivity, while inadequate ones leave the organization vulnerable.
Risk Assessment Tools and Frameworks
Manufacturers use various tools and frameworks to conduct thorough risk assessments:
- Quantitative methods: These involve numerical data, such as calculating potential financial losses or failure probabilities.
- Qualitative methods: These rely on expert judgment to assess risks in scenarios where data is scarce or subjective factors dominate.
Risk matrices and Failure Modes and Effects Analysis (FMEA) are popular tools for evaluating and ranking risks. These methodologies provide structured approaches to identify failure points, estimate their impact, and prioritize corrective actions.
Hazard Assessment and Threat Modeling
Manufacturing environments are often laden with hazards, such as exposure to hazardous materials, equipment malfunctions, or cybersecurity vulnerabilities in connected systems. Hazard assessments help identify these risks, while threat modeling provides a framework for anticipating potential threats and designing preemptive measures.
For example:
- Common manufacturing hazards: Chemical spills, machinery failures, and ergonomic risks.
- Threat modeling techniques: Simulation of "what-if" scenarios to evaluate the impact of potential failures and plan responses.
In conclusion, risk assessment in manufacturing is not a one-time activity but a continuous process. By leveraging structured methodologies, advanced tools, and proactive mitigation strategies, manufacturers can create a safer, more compliant, and efficient operational environment.
Manufacturing-Specific Compliance
Manufacturing compliance is a multifaceted responsibility, requiring adherence to numerous standards and regulations specific to the industry. From worker safety to environmental stewardship, each compliance area presents unique challenges and opportunities for manufacturers to enhance their operations.
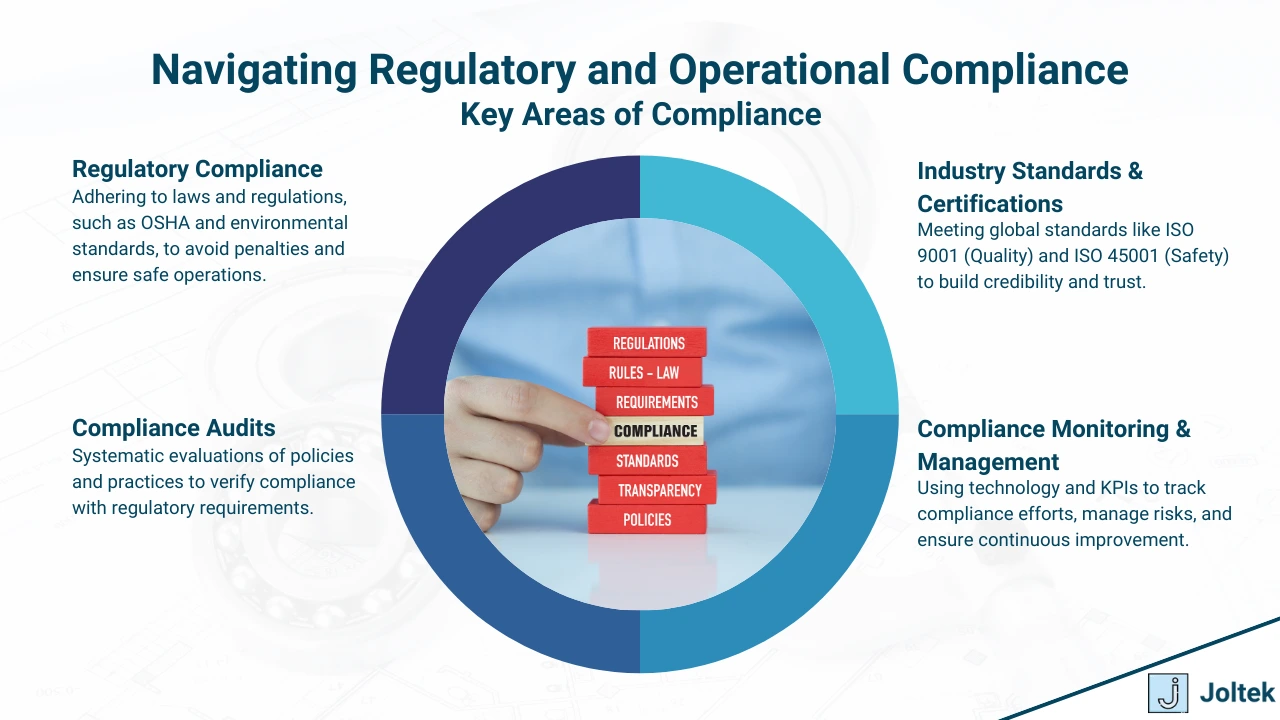
OSHA Compliance
Occupational Safety and Health Administration (OSHA) standards are designed to ensure safe and healthy working conditions for employees. These standards cover a wide range of safety concerns, including equipment use, hazardous materials handling, and emergency preparedness.
Common compliance challenges include:
- Keeping up with frequent regulatory updates.
- Ensuring consistent employee training and awareness.
- Addressing safety concerns in aging facilities.
Solutions such as regular safety audits, implementing robust incident reporting systems, and investing in modern protective equipment can help manufacturers meet OSHA requirements.
ISO Standards
ISO certifications like ISO 9001 (Quality Management), ISO 14001 (Environmental Management), and ISO 45001 (Occupational Health and Safety) set global benchmarks for operational excellence.
Strategies for seamless ISO integration include:
- Establishing cross-functional teams to manage certification processes.
- Conducting gap analyses to identify areas requiring improvement.
- Embedding ISO standards into daily operations through training and documentation.
These certifications not only demonstrate compliance but also enhance customer confidence and operational efficiency.
FDA Regulations
For manufacturers in regulated industries like pharmaceuticals, medical devices, and food production, the U.S. Food and Drug Administration (FDA) mandates strict compliance with 21 CFR Part 11 (Electronic Records) and Part 820 (Quality Systems).
Effective FDA compliance strategies include:
- Maintaining meticulous documentation to withstand regulatory scrutiny.
- Using validated software systems to manage electronic records.
- Conducting mock inspections to prepare for actual FDA audits.
Proactive engagement with FDA guidelines can reduce the risk of violations and production disruptions.
Environmental Compliance
Environmental regulations focus on controlling emissions, reducing waste, and promoting sustainable manufacturing practices. Adherence to frameworks like the Clean Air Act and the Resource Conservation and Recovery Act (RCRA) is essential.
Manufacturers can leverage green practices such as energy-efficient equipment, waste recycling programs, and life-cycle assessments to minimize their environmental impact while achieving regulatory compliance.
Supply Chain Compliance
In an era of globalized manufacturing, supply chain compliance is critical for ensuring transparency and accountability across all tiers of suppliers. This includes adhering to ethical sourcing practices, avoiding conflict materials, and complying with import/export regulations.
Addressing global supply chain risks requires:
- Conducting supplier audits to verify compliance with standards.
- Implementing digital tools for real-time supply chain monitoring.
- Establishing robust contracts with clear compliance clauses.
Product Lifecycle Compliance
Managing compliance throughout a product’s lifecycle—from design and production to distribution and disposal—is increasingly important.
Key considerations include:
- Ensuring all materials and processes meet regulatory standards during production.
- Maintaining traceability through detailed documentation and labeling.
- Designing products for recyclability to comply with end-of-life regulations.
Comprehensive lifecycle management not only aids in compliance but also supports sustainable practices and customer satisfaction.
In summary, manufacturing-specific compliance demands a holistic approach, combining technical expertise, regulatory knowledge, and strategic foresight. By addressing these areas effectively, manufacturers can mitigate risks, improve operational resilience, and maintain a competitive advantage.
Technology in Compliance
Technology plays a transformative role in compliance management, enabling manufacturers to navigate complex regulatory landscapes efficiently and securely. From automation to data-driven insights, technological tools and innovations are reshaping how compliance is achieved and sustained.
Compliance Software and Data Integrity
Modern compliance software streamlines and automates processes, reducing manual effort and the risk of human error. These tools offer functionalities such as:
- Real-time monitoring: Identifying compliance issues as they arise.
- Audit trails: Ensuring traceability of actions and decisions.
- Automated reporting: Generating compliance documentation quickly and accurately.
Maintaining accurate and secure data is a cornerstone of compliance. Errors or breaches in data integrity can lead to regulatory violations, financial losses, and reputational damage. Using encryption, regular backups, and data validation tools ensures the reliability and security of compliance-related data.
Cybersecurity Compliance
With the increasing digitization of manufacturing, safeguarding Industrial Control Systems (ICS) and Supervisory Control and Data Acquisition (SCADA) systems is paramount. Cybersecurity compliance involves:
- Adhering to frameworks: Standards like NIST Cybersecurity Framework and IEC 62443 provide guidelines for securing operational technology (OT) environments.
- Implementing best practices: Regular software updates, access controls, and network segmentation to prevent unauthorized access and mitigate cyber threats.
Non-compliance with cybersecurity standards can result in devastating breaches, jeopardizing both operational continuity and regulatory standing.
IoT Compliance and Blockchain for Traceability
The proliferation of IoT devices in manufacturing introduces unique compliance challenges, including data privacy and device security. Managing IoT compliance involves ensuring that connected devices adhere to standards for data protection and operational safety.
Blockchain technology offers a powerful solution for enhancing supply chain transparency and traceability. By creating immutable records of transactions and product histories, blockchain helps manufacturers:
- Verify the origin and authenticity of materials.
- Track compliance throughout the supply chain.
- Demonstrate accountability to regulators and customers.
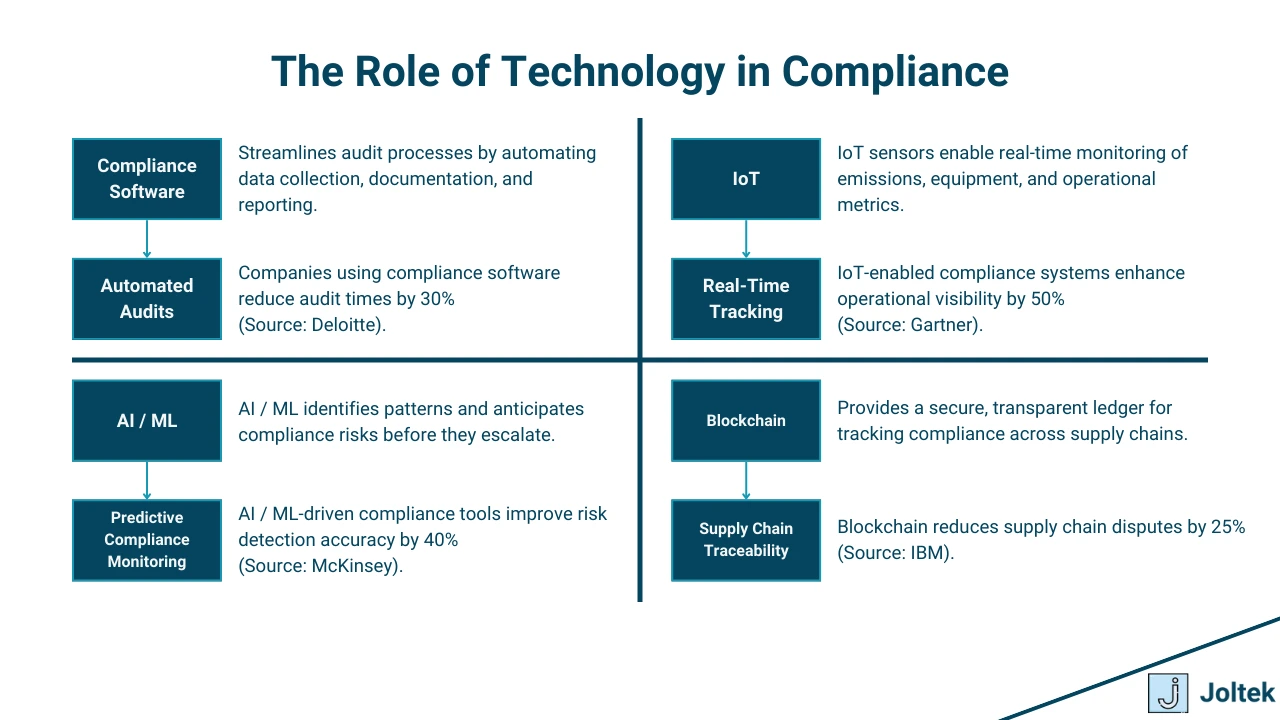
AI-Driven Compliance Tools
Artificial intelligence (AI) is revolutionizing compliance management by enabling more efficient monitoring, analysis, and reporting. Key applications include:
- Automated anomaly detection: Identifying deviations from compliance norms in real-time.
- Predictive analytics: Anticipating risks and recommending preventive measures.
- Natural language processing (NLP): Simplifying regulatory text interpretation to ensure better adherence.
However, AI adoption comes with limitations and ethical considerations, such as:
- The potential for biases in AI algorithms leading to inaccurate assessments.
- Ensuring AI systems operate transparently and within regulatory boundaries.
In conclusion, technology is not just a tool but a strategic enabler for compliance in manufacturing. By adopting advanced systems and frameworks, manufacturers can enhance their ability to meet regulatory requirements, improve efficiency, and build resilience in a rapidly evolving operational environment.
Specific Manufacturing Topics
Compliance in manufacturing spans several critical areas that directly impact product quality, safety, and sustainability. This section explores specific topics that manufacturers must address to maintain operational and regulatory excellence.
Quality Management Systems (QMS)
A Quality Management System (QMS) is a structured framework for ensuring consistent product quality and compliance with industry standards. QMS encompasses processes such as:
- Document control: Standardizing procedures and maintaining records for traceability.
- Corrective actions: Identifying and rectifying non-conformities to prevent recurrence.
- Continuous improvement: Using data insights to enhance quality and efficiency.
QMS plays a pivotal role in maintaining compliance by embedding regulatory requirements into daily operations. For example, companies in the automotive industry use IATF 16949-certified QMS to meet global quality standards. Case studies have shown that organizations implementing robust QMS often experience reduced defect rates, fewer compliance violations, and improved customer satisfaction.
GMP and HACCP Compliance
Good Manufacturing Practices (GMP) and Hazard Analysis and Critical Control Points (HACCP) are essential frameworks for ensuring product safety and regulatory compliance, particularly in food, beverage, and pharmaceutical industries.
- GMP focuses on maintaining hygienic facilities, proper documentation, and validated processes.
- HACCP emphasizes identifying and controlling potential hazards at critical points in the production process.
Implementing GMP and HACCP involves:
- Conducting hazard analyses to identify risks.
- Establishing monitoring systems to track critical control points.
- Training employees on compliance protocols.
Challenges in these industries include managing complex supply chains, ensuring traceability, and adapting to evolving regulations like FSMA (Food Safety Modernization Act) and EU GMP guidelines.
Energy Compliance and Emissions Tracking
As sustainability becomes a global priority, energy compliance and emissions tracking are critical for manufacturers to align with international standards like ISO 50001 (Energy Management) and governmental mandates like the EU Emissions Trading System (ETS).
Advanced technologies enable real-time tracking of energy use and emissions, helping manufacturers:
- Identify inefficiencies and reduce energy costs.
- Monitor greenhouse gas emissions to meet regulatory thresholds.
- Generate reports to demonstrate compliance to stakeholders.
For example, IoT-enabled sensors and cloud-based analytics platforms provide granular insights into energy consumption, allowing manufacturers to optimize operations while meeting sustainability goals.
In summary, addressing these specific manufacturing topics not only ensures compliance but also drives operational improvements, builds customer trust, and positions manufacturers as leaders in their respective industries.
Cross-Functional Considerations
Compliance in manufacturing requires the collaboration of various departments and stakeholders. Cross-functional considerations are vital to fostering a culture of compliance, minimizing risks, and ensuring accountability across all levels of the organization.
Training and Awareness
Employee training is the foundation of a successful compliance strategy. Regular training sessions ensure that employees are well-versed in regulatory requirements and internal compliance policies. Key elements of effective compliance training include:
- Customized programs: Tailoring training to the roles and responsibilities of different teams.
- Ongoing education: Providing updates as regulations evolve or new standards are introduced.
- Interactive formats: Leveraging hands-on workshops, e-learning platforms, and scenario-based training to enhance engagement.
Leadership plays a critical role in fostering a compliance-driven culture. When leaders prioritize compliance, set clear expectations, and model ethical behavior, they inspire employees to follow suit, making compliance a shared organizational responsibility.
Incident Reporting and Internal Audits
A robust incident reporting mechanism is essential for identifying and addressing compliance issues promptly. Key features include:
- Anonymity and accessibility: Allowing employees to report concerns without fear of retaliation through accessible and confidential channels.
- Timely resolution: Ensuring that reported incidents are investigated and resolved efficiently.
Regular internal audits complement incident reporting by proactively identifying risks before they escalate. Internal audits involve:
- Reviewing processes and documentation for compliance gaps.
- Testing controls to ensure effectiveness.
- Generating actionable insights to improve policies and procedures.
Proactive audits not only enhance compliance but also prepare organizations for external inspections by regulatory bodies.
Vendor and Third-Party Risk Management
Vendors and third-party partners play a significant role in manufacturing operations, and their compliance is equally critical. Strategies for managing third-party risks include:
- Comprehensive due diligence: Evaluating a vendor’s compliance history, certifications, and processes before engagement.
- Clear contractual obligations: Including compliance clauses in contracts to hold vendors accountable.
- Ongoing monitoring: Using tools like vendor management software to track performance and compliance metrics.
Technologies like blockchain can also enhance third-party risk management by providing transparent and tamper-proof records of supplier transactions and certifications.
In conclusion, cross-functional considerations ensure that compliance is not siloed within specific departments but integrated into the fabric of the organization. By focusing on training, internal oversight, and vendor accountability, manufacturers can create a resilient compliance ecosystem that minimizes risks and promotes continuous improvement.
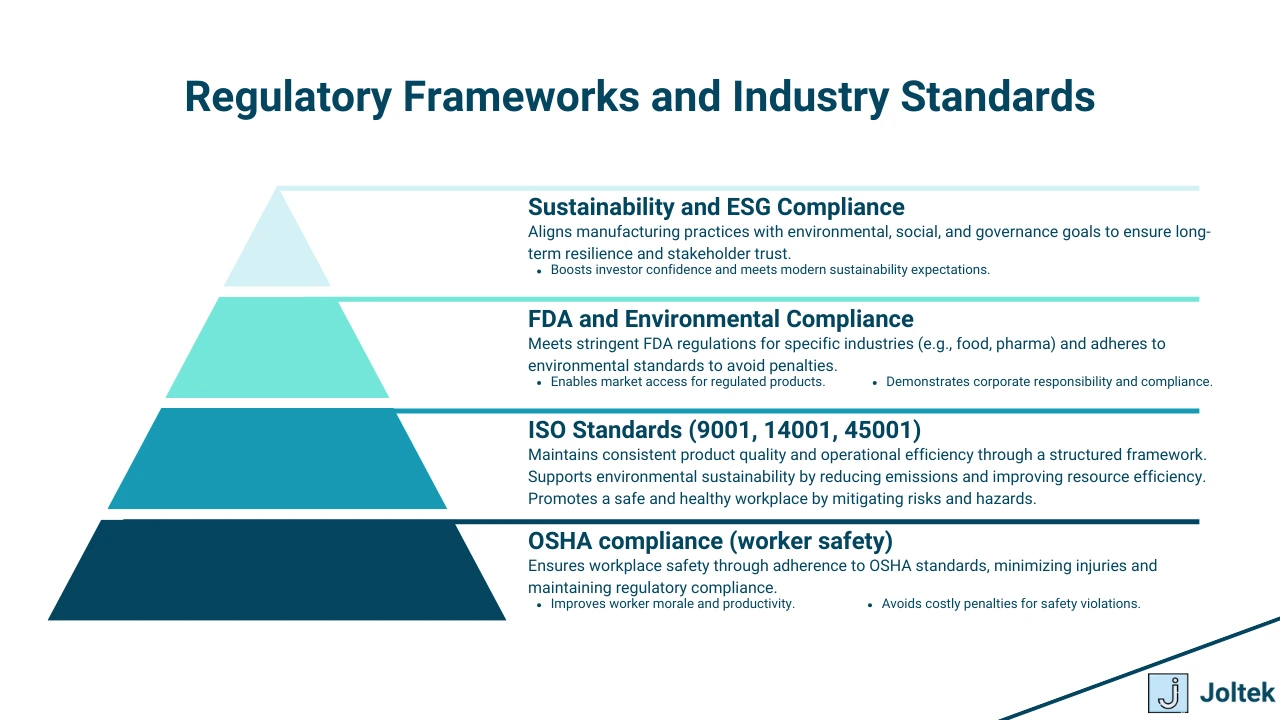
Emerging Trends in Compliance
As manufacturing evolves in response to global challenges and technological advancements, compliance is also transforming. Emerging trends such as ESG integration, sustainability, AI-driven tools, and climate-related reporting are shaping the future of compliance, offering opportunities to align regulatory adherence with broader business goals.
ESG (Environmental, Social, Governance) Compliance
Environmental, Social, and Governance (ESG) initiatives have become a cornerstone of modern compliance strategies. Organizations are now linking ESG efforts to compliance risk assessments, focusing on:
- Environmental: Meeting emissions targets, minimizing waste, and adhering to sustainability standards like ISO 14001.
- Social: Upholding labor laws, ensuring workplace safety, and promoting diversity and inclusion.
- Governance: Maintaining ethical practices, robust data security, and transparent reporting.
By integrating ESG into compliance frameworks, manufacturers can address stakeholder expectations, reduce risks, and enhance their brand reputation.
Circular Economy Compliance
The circular economy promotes the reuse, recycling, and regeneration of materials to minimize waste. Compliance in this context involves aligning sustainability goals with regulatory requirements. Key actions include:
- Designing products for recyclability to meet extended producer responsibility (EPR) laws.
- Tracking material flows to ensure compliance with resource efficiency standards.
- Partnering with suppliers and recyclers to close the material loop.
Adopting circular economy principles not only ensures compliance but also positions manufacturers as leaders in sustainable innovation.
AI and Machine Learning in Compliance
Artificial intelligence and machine learning are revolutionizing compliance management by enabling predictive and automated solutions. Key applications include:
- Predictive compliance models: AI analyzes historical data and identifies patterns to predict potential compliance risks before they occur.
- Real-time monitoring: Machine learning algorithms track operations and detect anomalies indicative of non-compliance.
- Natural language processing (NLP): Automating the interpretation of complex regulatory documents to extract actionable insights.
While AI offers significant advantages, manufacturers must address ethical concerns, such as data privacy and algorithmic bias, to fully harness its potential.
Climate Risk Disclosure
Climate-related risks have become a compliance priority, with frameworks like the Task Force on Climate-Related Financial Disclosures (TCFD) setting standards for transparent reporting. Manufacturers are now required to:
- Assess and disclose the financial impact of climate risks on their operations.
- Develop strategies for mitigating climate-related disruptions.
- Align reporting with TCFD and similar frameworks to meet investor and regulatory expectations.
Climate risk disclosure not only ensures compliance but also helps manufacturers identify vulnerabilities and adapt to a rapidly changing environment.
In conclusion, these emerging trends in compliance highlight the need for manufacturers to adopt forward-thinking strategies. By integrating ESG, embracing sustainability, leveraging AI, and addressing climate risks, organizations can stay ahead of regulatory changes while achieving broader business and societal goals.
Best Practices and Strategies
To effectively manage compliance in manufacturing, organizations must adopt proven best practices and strategies that ensure thorough documentation, measurable program success, and optimized resource allocation. This section provides actionable insights into building a sustainable compliance framework.
Documenting and Reporting Compliance Findings
Clear and comprehensive documentation is vital for demonstrating compliance and identifying areas for improvement. Best practices for creating actionable compliance reports include:
- Standardized templates: Use consistent formats to streamline data collection and analysis.
- Detailed observations: Record findings with context, including descriptions of issues, root causes, and potential impacts.
- Actionable recommendations: Provide clear steps for addressing non-compliance and mitigating risks.
- Audience-focused reporting: Tailor reports to different stakeholders, such as leadership, auditors, or operational teams, to ensure relevance and clarity.
Effective compliance reporting not only satisfies regulatory requirements but also drives accountability and continuous improvement.
Measuring the Effectiveness of Compliance Programs
The success of a compliance program hinges on its ability to achieve intended outcomes. Key metrics for evaluating compliance efforts include:
- Incident rates: Number of compliance violations, safety incidents, or audit findings over a specific period.
- Resolution times: Average time taken to address and close compliance issues.
- Training effectiveness: Employee participation rates and post-training assessments to gauge knowledge retention.
- Audit outcomes: Percentage of compliance audits passed without major findings.
Regularly reviewing these metrics helps organizations identify trends, allocate resources effectively, and demonstrate progress to stakeholders.
Balancing Costs and Risks
Compliance efforts must strike a balance between financial investments and risk mitigation. Strategies to optimize compliance spending while minimizing risks include:
- Risk-based prioritization: Allocate resources to address high-risk areas that have the greatest potential impact on operations and reputation.
- Technology adoption: Leverage automation tools and data analytics to reduce manual effort and improve efficiency.
- Continuous training: Invest in employee education to prevent costly errors and build a compliance-oriented culture.
- Collaboration with third parties: Partner with consultants or external auditors for specialized expertise and fresh perspectives.
By balancing costs with risks, manufacturers can maintain robust compliance programs without overextending budgets.
In conclusion, best practices in compliance management involve meticulous documentation, data-driven evaluation, and strategic resource allocation. By implementing these strategies, manufacturers can not only meet regulatory requirements but also enhance operational efficiency and resilience.
Real-World Applications
Real-world examples of compliance management in manufacturing offer critical insights into both successful strategies and the consequences of neglecting regulatory requirements. By examining case studies, challenges, and the contrast between proactive and reactive compliance, manufacturers can develop more robust and effective approaches.
Case Studies
Successful compliance implementations demonstrate the tangible benefits of a structured and proactive approach. For example, a leading automotive manufacturer adopted ISO 9001 and ISO 14001 standards to integrate quality and environmental management systems into their production lines. This not only improved product quality but also significantly reduced material waste and operational inefficiencies. By utilizing a centralized compliance management system, the company streamlined audits, improved documentation accuracy, and reduced the burden of manual processes.
In the pharmaceutical industry, compliance with FDA regulations like 21 CFR Part 11 is crucial for ensuring data integrity and process transparency. A global pharmaceutical company achieved this by implementing electronic systems validated for regulatory compliance. The transition eliminated errors associated with paper-based record-keeping, ensuring adherence to FDA standards while enhancing operational efficiency. Such examples underscore the importance of aligning compliance efforts with organizational goals to achieve sustainable success.
However, the consequences of non-compliance are equally instructive. In one notable case, an automaker faced billions of dollars in penalties and severe reputational damage for falsifying emissions test results. This emissions scandal highlighted the risks of unethical practices and inadequate internal oversight. Similarly, a food manufacturer’s failure to fully implement HACCP protocols led to widespread product recalls and legal action, emphasizing the critical need for hazard analysis and stringent control measures in high-stakes industries.
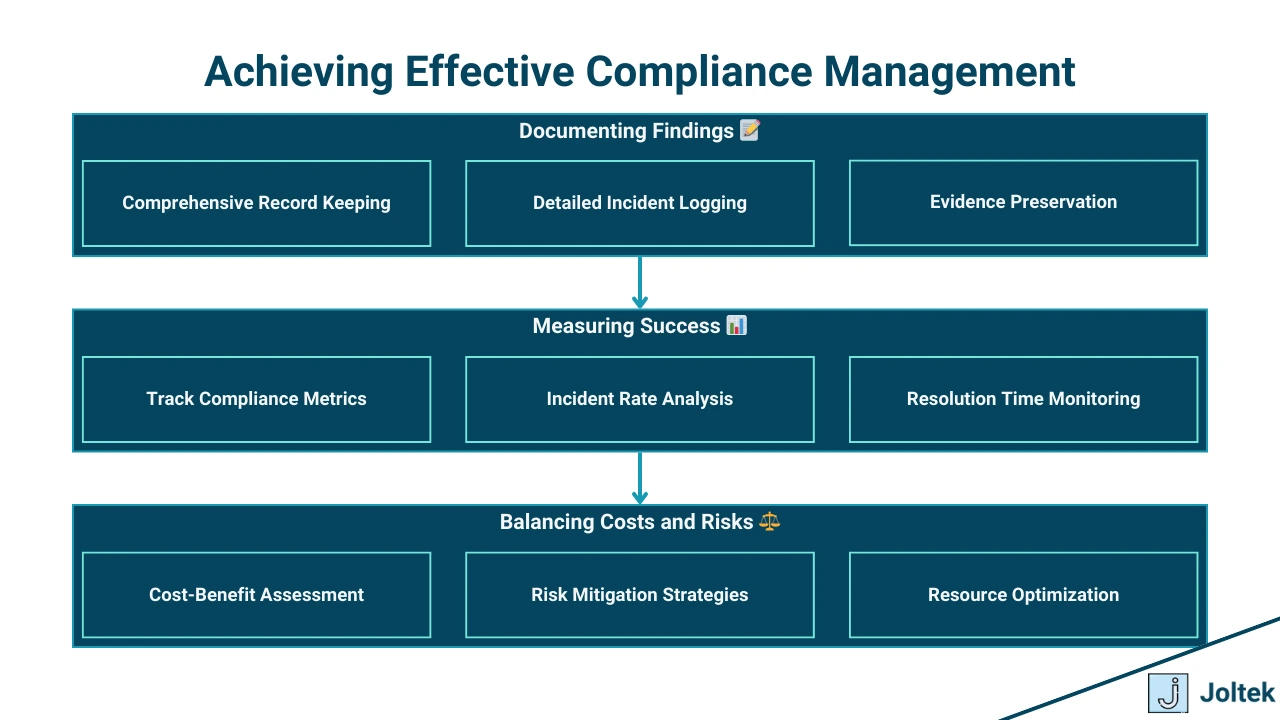
Challenges and Pitfalls
Despite the importance of compliance, manufacturers often face significant challenges in managing it effectively. One common pitfall is the incomplete identification of risks. Many organizations focus on obvious hazards but overlook subtle or emerging threats, such as cybersecurity vulnerabilities in connected systems. Poor documentation practices are another recurring issue. Without accurate and comprehensive records, demonstrating compliance during audits becomes a daunting task. Moreover, relying on manual processes increases the likelihood of human error and inefficiencies, particularly in complex regulatory environments.
To overcome these challenges, manufacturers can adopt several strategies. Investing in modern compliance technologies, such as automated tracking and reporting tools, minimizes errors and enhances operational visibility. Enhanced training programs ensure that employees across all levels understand their compliance responsibilities. Cross-functional collaboration between departments, such as quality assurance and IT, further strengthens compliance frameworks by addressing gaps and ensuring consistent practices across the organization.
Proactive vs. Reactive Compliance
The contrast between proactive and reactive compliance approaches illustrates the importance of forward planning. Proactive compliance involves anticipating risks, implementing preventive measures, and fostering a culture of accountability. Organizations that embrace this approach often experience fewer violations, reduced costs, and improved operational efficiency. For instance, manufacturers who regularly audit their processes and update their compliance practices based on evolving regulations are better equipped to avoid disruptions.
In contrast, reactive compliance tends to focus on addressing issues only after they arise. This approach is often crisis-driven and can lead to costly penalties, reputational damage, and inefficient solutions. A manufacturing company that ignored audit findings, for example, faced operational shutdowns and financial losses when regulators identified repeated violations. Such cases highlight the dangers of waiting for external enforcement and the missed opportunities for improvement through early intervention.
In conclusion, real-world applications of compliance in manufacturing reveal the critical role of structured, proactive strategies. Learning from success stories, addressing common pitfalls, and prioritizing preventive measures allow manufacturers to navigate the complexities of compliance while safeguarding their operational and reputational integrity.
Conclusion
Compliance in manufacturing is not a static requirement but an ongoing process that evolves with regulatory changes, technological advancements, and operational complexities. Throughout this discussion, we have explored the multifaceted nature of compliance, from risk assessment and industry-specific requirements to the role of technology and emerging trends.
A key insight is the importance of integrating compliance into the fabric of organizational operations. Proactive compliance efforts, supported by robust systems, cross-functional collaboration, and a culture of accountability, are far more effective than reactive measures. Case studies show that organizations that prioritize compliance as a strategic objective not only avoid penalties but also enhance their operational efficiency, brand reputation, and competitive edge.
Emerging trends, such as ESG initiatives and AI-driven tools, present both challenges and opportunities. Manufacturers must stay ahead of these developments, leveraging technology and sustainability practices to align compliance with broader business goals.
As a call to action, manufacturers are encouraged to view compliance as a strategic framework rather than a box-ticking exercise. This involves:
- Continuous improvement: Regularly updating processes and training programs to meet evolving regulations.
- Investment in technology: Adopting advanced compliance tools to enhance monitoring, reporting, and risk mitigation.
- Leadership engagement: Establishing a compliance-driven culture with active involvement from top management.
By adopting these practices, manufacturers can ensure not only adherence to regulations but also long-term resilience and success in an increasingly complex and competitive landscape. Compliance is more than an obligation—it is a pathway to operational excellence and sustainable growth.
References
Below is a curated list of references and additional reading materials that support the concepts and insights presented in this document. These resources provide a deeper understanding of compliance in manufacturing and related best practices:
Regulatory Frameworks and Standards
- ISO Standards
- ISO 9001: Quality Management Systems - https://www.iso.org/standard/62085.html
- ISO 14001: Environmental Management Systems - https://www.iso.org/standard/60857.html
- ISO 45001: Occupational Health and Safety Management Systems - https://www.iso.org/standard/63787.html
- OSHA Standards
- Occupational Safety and Health Administration (OSHA) Regulations - https://www.osha.gov/laws-regs
- FDA Compliance
- FDA 21 CFR Part 11 - Electronic Records; Electronic Signatures - https://www.fda.gov/regulatory-information/search-fda-guidance-documents/part-11-electronic-records-electronic-signatures-scope-and-application
- FDA 21 CFR Part 820 - Quality System Regulation - https://www.fda.gov/medical-devices/postmarket-requirements-devices/quality-system-qs-regulationmedical-device-good-manufacturing-practices
- NIST Cybersecurity Framework
- National Institute of Standards and Technology (NIST) Cybersecurity Framework - https://www.nist.gov/cyberframework
- IEC 62443 Standards
- Industrial Automation and Control Systems Security - https://www.iec.ch/standards/62443
Case Studies and Best Practices
- Automotive Compliance Success:
- International Automotive Task Force (IATF) 16949 Standards - https://www.iatfglobaloversight.org
- Pharmaceutical Compliance:
- GMP Regulations and Guidelines - https://www.who.int/publications-detail-redirect/9789241549924
- Environmental Compliance Case Studies:
- U.S. Environmental Protection Agency (EPA) Success Stories - https://www.epa.gov/sustainability/sustainability-success-stories
Emerging Trends and Additional Resources
- ESG Compliance:
- United Nations Sustainable Development Goals (SDGs) - https://sdgs.un.org/
- TCFD (Task Force on Climate-Related Financial Disclosures) Recommendations - https://www.fsb-tcfd.org/
- AI in Compliance:
- Artificial Intelligence for Regulatory Compliance: Opportunities and Challenges - https://www2.deloitte.com/insights/us/en/industry/technology/ai-for-regulatory-compliance.html
- Blockchain for Traceability:
- Blockchain in Manufacturing Supply Chains - https://www.ibm.com/blockchain/solutions/supply-chain
- Circular Economy and Compliance:
- Ellen MacArthur Foundation - Circular Economy Insights - https://www.ellenmacarthurfoundation.org
General Compliance Tools and Resources
- Compliance Management Software:
- List of Compliance Software Tools - https://www.g2.com/categories/compliance
- Internal Audit Best Practices:
- Institute of Internal Auditors (IIA) Resources - https://www.theiia.org
- Global Compliance News and Updates:
- Lexology: Compliance Insights - https://www.lexology.com
These resources provide further insights into regulatory requirements, best practices, and emerging trends, helping manufacturers strengthen their compliance frameworks and stay ahead of industry challenges.