Introduction
The demand for automation expertise is at an all-time high as manufacturing and process industries grapple with the challenges of modernizing their operations. With rapid advancements in robotics, IoT-enabled systems, and machine learning, companies are increasingly looking to automation to boost productivity, reduce costs, and remain competitive in a rapidly changing global market. However, this shift isn’t just about adopting new tools or technologies—it’s about transforming entire systems and processes, requiring expertise that bridges both traditional and modern approaches to manufacturing.
The rise of smart factories and Industry 4.0 concepts has created a need for professionals who understand the intricacies of both legacy systems and cutting-edge automation solutions. While roles in automation were once the domain of specialized controls engineers, today’s environment calls for a broader skill set, blending process optimization, technical expertise, and leadership abilities. This is where process engineers have an incredible advantage. With their foundational knowledge of production workflows, system efficiencies, and safety protocols, they are uniquely positioned to step into automation leadership roles and guide this transformation.
Process engineers are already equipped with skills that are critical to automation: problem-solving, data-driven decision-making, and an ability to see the big picture of how systems operate. These skills form the foundation for transitioning into automation-focused roles. By acquiring additional technical capabilities—such as PLC programming, SCADA system integration, and industrial protocol expertise—process engineers can extend their impact beyond process optimization and into designing and implementing advanced automation systems.
Moreover, the growing intersection of IT and OT (Operational Technology) has created new opportunities for professionals who can navigate both worlds. The ability to collaborate across departments, understand data-driven innovation, and bridge the gap between business goals and technical solutions is increasingly becoming a hallmark of automation leaders. This makes the process engineer’s understanding of system performance and production efficiencies all the more relevant in today’s manufacturing landscape.
However, transitioning into automation leadership isn’t without challenges. It requires mastering new technical skills, developing a deeper understanding of emerging technologies, and, most importantly, growing as a leader. Leaders in automation must not only deliver results but also inspire teams, foster collaboration, and anticipate future industry trends. This shift from individual contributor to strategic leader is often the most difficult part of the transition, but it is also the most rewarding.
This article will explore how process engineers can successfully transition into automation leadership roles by focusing on key skills, tools, and strategies. We’ll discuss how to build a solid foundation in automation technologies, navigate the complexities of team building, and align technical innovations with business objectives. Additionally, we’ll examine the importance of data-driven decision-making, the role of IT/OT convergence, and the ways in which automation leaders can future-proof their careers by embracing continuous learning and collaboration.
As the manufacturing industry continues to evolve, automation leadership is becoming a critical driver of success. Whether you’re a seasoned process engineer looking to expand your role or an aspiring automation leader seeking guidance, this guide will provide actionable insights to help you thrive in an increasingly automated world.
The Foundation: Skills of a Process Engineer
Process engineers play a pivotal role in manufacturing and process industries, acting as the architects of efficiency, safety, and system optimization. Their work focuses on improving the performance of production systems, reducing waste, and ensuring that operations meet stringent safety and quality standards. These responsibilities not only form the backbone of modern manufacturing but also provide an excellent foundation for transitioning into automation-focused roles.
The Role of a Process Engineer in Manufacturing
At its core, the role of a process engineer involves designing, implementing, and optimizing processes that transform raw materials into finished goods. Whether it’s a food production line, a chemical manufacturing plant, or a pharmaceutical facility, process engineers work to maximize throughput, minimize downtime, and ensure compliance with environmental and safety regulations. Their responsibilities often include:
- System Design and Optimization: Developing production systems that balance efficiency, scalability, and cost-effectiveness.
- Safety Management: Ensuring that processes meet occupational safety and environmental standards.
- Troubleshooting and Continuous Improvement: Identifying inefficiencies, solving complex problems, and implementing sustainable improvements.
Process engineers must also collaborate closely with multidisciplinary teams, including maintenance, operations, and quality assurance, to ensure that production goals are met without compromising safety or quality.
Core Skills That Translate Well to Automation
The transition from process engineering to automation is a natural progression for many professionals because the core skills developed in process engineering align closely with the needs of automation roles. These skills include:
- Problem-Solving and Root Cause Analysis
- Process engineers excel at identifying and solving problems in complex systems. Whether it’s diagnosing bottlenecks in a production line or resolving equipment failures, their ability to break down issues into manageable components is critical.
- This analytical mindset is equally valuable in automation, where engineers must debug control systems, troubleshoot PLCs, and optimize SCADA configurations. The structured problem-solving approaches learned in process engineering—like the 5 Whys or Fishbone diagrams—are directly applicable to automation challenges.
- Understanding of Production Processes and Systems
- A process engineer’s in-depth knowledge of manufacturing workflows provides a strong foundation for designing and implementing automation solutions. They understand how various components—like conveyors, pumps, valves, and sensors—interact within a production system.
- This system-level perspective helps automation professionals design control strategies that align with operational goals. For example, understanding fluid dynamics in a piping system makes it easier to program a PLC to regulate flow rates accurately.
- Data-Driven Decision-Making
- Process engineers are accustomed to using data to monitor performance, identify trends, and drive improvements. From analyzing production metrics to conducting statistical process control (SPC), data plays a central role in their work.
- This skill is crucial in automation, where engineers must collect, interpret, and act on data from sensors, PLCs, and MES systems. Data-driven decision-making enables automation leaders to implement predictive maintenance, improve OEE (Overall Equipment Effectiveness), and optimize production schedules.
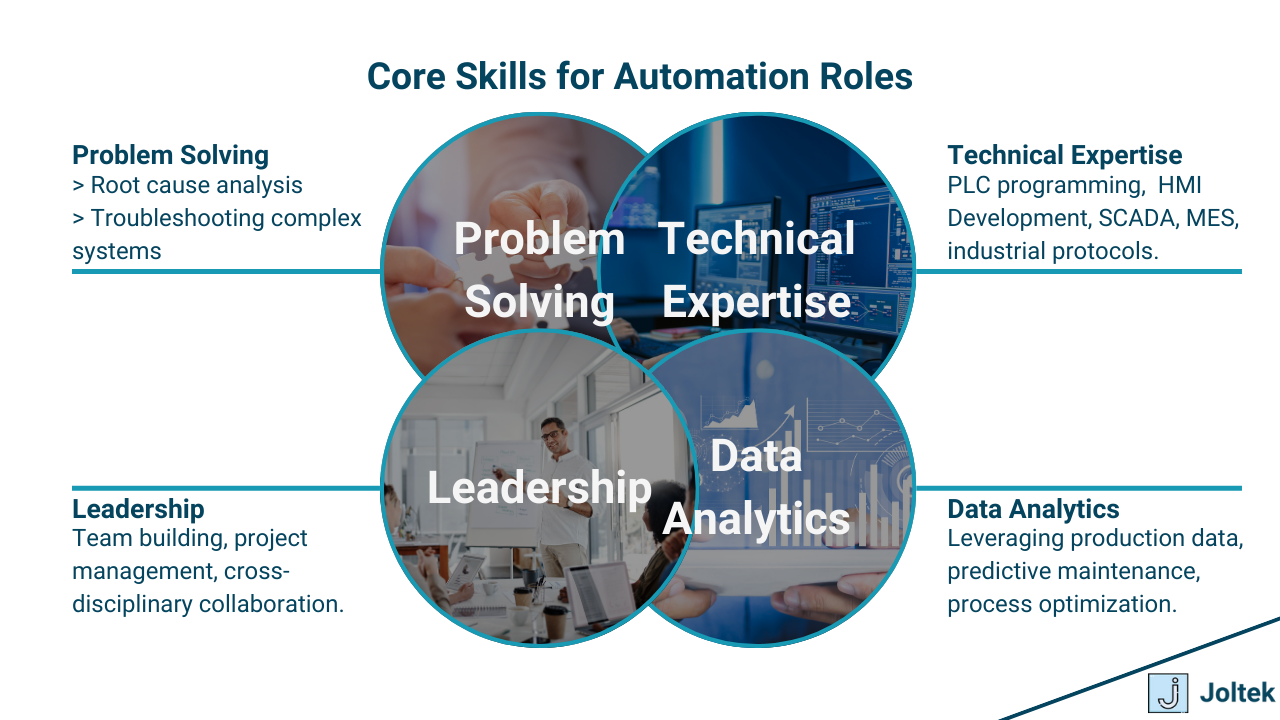
Why These Skills Are Critical for Automation
The overlap between process engineering and automation engineering lies in their shared goal: optimizing systems for maximum efficiency and reliability. Process engineers bring an invaluable understanding of how manufacturing processes operate, which gives them an edge when designing or troubleshooting automation systems. Their ability to think both critically and systemically makes them well-suited for the technical and strategic challenges of automation.
By building on their existing expertise and acquiring additional technical skills—like programming, control system design, and networking—process engineers can seamlessly transition into automation roles. The next section will explore how to develop these new skills and make the leap into automation engineering and leadership.
Transitioning to Automation Engineering
The move from process engineering to automation engineering is a natural step for many professionals looking to expand their impact and embrace the future of manufacturing. While process engineers bring valuable knowledge of production workflows and system optimization, transitioning to automation requires the acquisition of specific technical skills and a shift in mindset. Here, we explore the key technical competencies needed, actionable steps to make the transition, and how to overcome common challenges.
Key Technical Skills Required for Automation Roles
Automation engineering demands a mix of programming, hardware, and systems integration expertise. The following are essential skills for professionals looking to transition into this field:
PLC Programming and Hardware Integration
- Proficiency in programming PLCs (Programmable Logic Controllers) is foundational for automation roles. PLCs serve as the “brain” of automated systems, controlling machinery, sensors, and actuators.
- Platforms like Siemens TIA Portal, Rockwell Studio 5000, and Codesys are commonly used in the industry. Understanding how to write, debug, and optimize ladder logic, structured text, and function block diagrams is critical.
- Hardware integration skills, such as connecting PLCs to drives, sensors, and other field devices, are equally important.
Control System Design and Implementation
- Automation engineers are responsible for designing control systems that ensure safe, reliable, and efficient operation. This includes selecting the right hardware, designing control panels, and developing system architectures.
- Familiarity with safety standards (e.g., ISO 13849, NFPA 79) and experience with system commissioning and troubleshooting are valuable assets.
Familiarity with SCADA, MES, and Industrial Protocols
- Supervisory Control and Data Acquisition (SCADA) systems and Manufacturing Execution Systems (MES) are critical layers in modern automation, enabling real-time monitoring, control, and data analysis.
- Knowledge of industrial communication protocols like PROFINET, EtherNet/IP, Modbus, and OPC UA is essential for ensuring seamless communication between devices and systems.
Steps to Make the Transition
Transitioning into automation engineering requires a combination of proactive learning and leveraging opportunities within your current organization. Here’s how to make the leap:
- Upskilling Through Courses, Certifications, and Hands-On Experience
- Explore online courses, training programs, and certifications from reputable platforms and vendors. Examples include:
- Siemens certification programs for PLC programming and automation systems.
- Rockwell Automation training on Studio 5000 and FactoryTalk software.
- Inductive Automation’s Ignition training for SCADA and MES applications.
- Practice on affordable hardware like micro PLCs (e.g., Siemens S7-1200, Allen-Bradley Micro800) and simulation software to build hands-on experience.
- Explore online courses, training programs, and certifications from reputable platforms and vendors. Examples include:
- Seeking Mentorship and Cross-Functional Opportunities
- Connect with experienced automation professionals within your organization or through industry networks like LinkedIn. Mentors can guide you in navigating technical challenges and career decisions.
- Volunteer for cross-functional projects involving automation systems, such as upgrades, retrofits, or new installations. This provides exposure to real-world applications and strengthens your resume.
- Learning on the Job
- Advocate for automation training opportunities within your current role. Many organizations are willing to invest in employees looking to expand their skill sets.
- Collaborate with maintenance teams, controls engineers, or system integrators to gain practical insights into automation systems.
Overcoming Challenges
While the transition to automation is rewarding, it comes with challenges that require determination and adaptability. Here’s how to address common obstacles:
- Learning New Software and Hardware Systems
- Automation systems are diverse, and every organization has unique tools and platforms. Focus on building foundational skills that can transfer across technologies, such as programming concepts and communication protocols.
- Leverage online forums, vendor documentation, and community resources to troubleshoot issues and accelerate learning.
- Adapting to a Faster-Paced Problem-Solving Environment
- Automation engineering often involves real-time problem-solving in high-pressure situations, such as minimizing downtime during equipment failures.
- Practice developing efficient troubleshooting techniques and maintaining a calm, methodical approach under pressure. Shadowing experienced engineers in these scenarios can be invaluable.
- Balancing Breadth and Depth of Knowledge
- Automation requires both a broad understanding of systems and specialized knowledge in certain areas, such as programming or networking. Focus on mastering key tools while remaining open to learning new technologies as needed.
Building Toward Automation Leadership
By mastering these technical skills and overcoming the initial challenges, process engineers can transition successfully into automation roles and beyond. The next step is to leverage this expertise to lead impactful projects and build teams capable of tackling complex automation challenges—topics we’ll explore in the following sections.
Key Milestones in Automation Leadership
Transitioning into automation leadership marks a significant career milestone. It involves moving beyond technical expertise to focus on strategy, team building, and delivering value at scale. As automation leaders take on greater responsibilities, they must lead impactful projects, manage diverse teams, and shift their mindset from technical contributor to strategic decision-maker.
Leading Projects in Automation
Automation leaders are often responsible for transformative projects that redefine how organizations operate.
Greenfield builds, for instance, involve designing and implementing automation systems for entirely new facilities. These projects require leaders to oversee every phase, from selecting platforms and hardware to commissioning operations. Success in these projects demonstrates the ability to manage complex systems while aligning them with organizational goals.
System integrations are another critical area, where leaders ensure seamless connectivity between new and legacy systems. This often involves adopting protocols like OPC UA or MQTT to unify disparate systems and enable data-driven operations.
Process optimizations focus on improving the efficiency and reliability of existing systems. These efforts may include implementing predictive maintenance, increasing production rates, or automating manual processes to reduce variability and waste.
Owning projects end-to-end is essential in all these examples. Leaders must balance technical knowledge with the ability to coordinate across disciplines, ensuring that projects meet technical and business requirements.
Building and Managing Automation Teams
Effective automation leaders recognize that success depends on building and managing skilled teams.
Hiring the right talent involves finding individuals with diverse skill sets across hardware, software, and systems integration. Balancing these areas ensures that the team can address the wide-ranging demands of automation projects. Leaders also prioritize hiring individuals who are adaptable, collaborative, and eager to learn.
Mentorship plays a vital role in upskilling team members and fostering a collaborative culture. Leaders invest in programs that enable experienced engineers to guide and train less experienced colleagues. By encouraging hands-on learning and providing constructive feedback, leaders ensure that their teams grow in capability and confidence.
A successful team is one where each member’s strengths are recognized and utilized effectively. Leaders must provide opportunities for team members to tackle challenges that align with their skills while encouraging professional development.
Evolving from Technical Expert to Leader
Becoming an automation leader requires a significant shift in mindset and responsibilities.
One key aspect is transitioning from individual contribution to strategic decision-making. Leaders focus on setting priorities, defining project goals, and aligning team efforts with broader organizational objectives. This involves understanding business needs, communicating the value of automation initiatives to stakeholders, and ensuring resources are allocated effectively.
Leaders also need to delegate responsibilities and trust their teams to execute tasks. While technical involvement remains important, successful leaders concentrate on guiding their teams, providing support, and ensuring that projects align with strategic goals.
Understanding and leveraging team strengths is critical. Leaders identify the unique abilities of their team members and provide opportunities for growth. This not only improves team performance but also fosters innovation and a sense of ownership among team members.
The Path Forward
Leading projects, building teams, and evolving into a strategic leader are key milestones in automation leadership. These steps prepare leaders to address complex challenges and shape the future of manufacturing and automation. By focusing on strategy, team development, and impactful project execution, automation leaders can drive meaningful change in their organizations and industries.
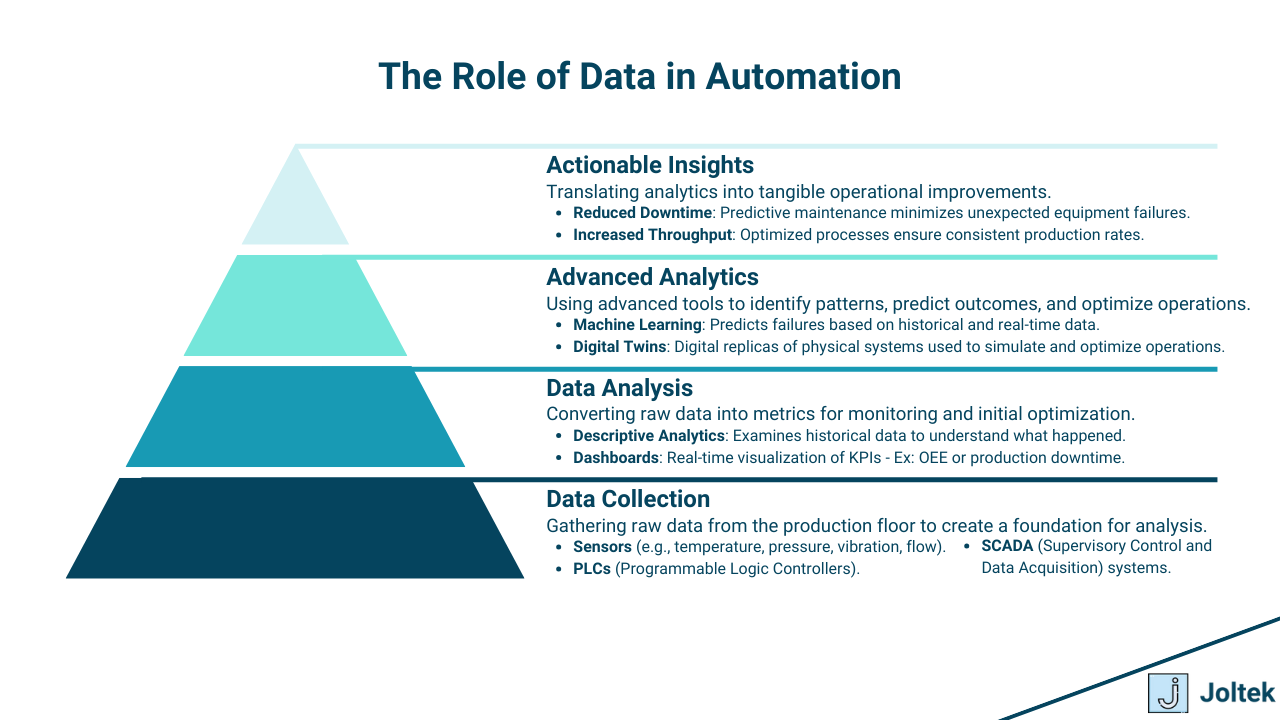
Data-Driven Innovation in Automation
Data is at the heart of modern automation, driving improvements in efficiency, reliability, and decision-making. The ability to collect, analyze, and act on data has transformed how manufacturing systems operate, making it possible to achieve levels of optimization that were previously unattainable. For automation leaders, leveraging data effectively is not just a technical requirement but a strategic imperative.
The Importance of Data in Modern Automation
Data collection and analysis form the foundation of any successful automation initiative. Production data provides the insights needed to identify inefficiencies, improve throughput, and maintain quality. Without accurate, real-time data, organizations are left relying on guesswork to solve complex problems.
MES (Manufacturing Execution Systems) and SCADA (Supervisory Control and Data Acquisition) systems play a critical role in this process. These tools enable real-time monitoring and reporting, giving operators and engineers the ability to visualize key performance indicators (KPIs) such as machine utilization, cycle times, and energy consumption. By integrating MES and SCADA systems, organizations can bridge the gap between the shop floor and higher-level business systems, ensuring that data flows seamlessly across the enterprise.
The Journey to Predictive Maintenance
One of the most transformative applications of data in automation is predictive maintenance. Traditional maintenance approaches—reactive or time-based—often lead to costly downtime or unnecessary repairs. Predictive maintenance uses data and analytics to anticipate failures, allowing organizations to address issues before they occur.
Setting up historians and data lakes is a critical first step in this journey. A historian collects and archives time-series data from PLCs, sensors, and other devices, while a data lake stores structured and unstructured data for advanced analytics. Together, these systems create a comprehensive repository of operational data.
Artificial intelligence (AI) and machine learning (ML) can then analyze this data to identify patterns and predict equipment failures. For example, an ML algorithm might detect that a motor is drawing higher-than-normal current, suggesting an impending failure. By addressing the issue proactively, organizations can reduce unplanned downtime and extend equipment life.
Predictive maintenance also extends beyond individual machines. By analyzing system-level data, automation leaders can optimize entire production lines, improving throughput and reducing waste.
Challenges and Solutions
While the benefits of data-driven innovation are clear, implementing these solutions comes with its own set of challenges:
- Handling Legacy Systems and Data Silos
- Many organizations operate a mix of old and new equipment, making it difficult to collect consistent, high-quality data. Legacy systems often lack modern communication protocols or integration capabilities.
- Solutions include using protocol converters, IoT gateways, or middleware to connect legacy equipment to modern networks. Standardizing data formats and centralizing storage can help eliminate silos.
- Balancing Immediate Needs with Long-Term Goals
- Automation leaders often face pressure to deliver quick wins while also planning for future capabilities. This can create a conflict between addressing short-term issues and investing in scalable, future-proof solutions.
- The key is to adopt a phased approach. Start by addressing critical pain points, such as reducing downtime or improving reporting accuracy. As the organization gains confidence in its data capabilities, gradually expand to more advanced solutions like predictive analytics and AI.
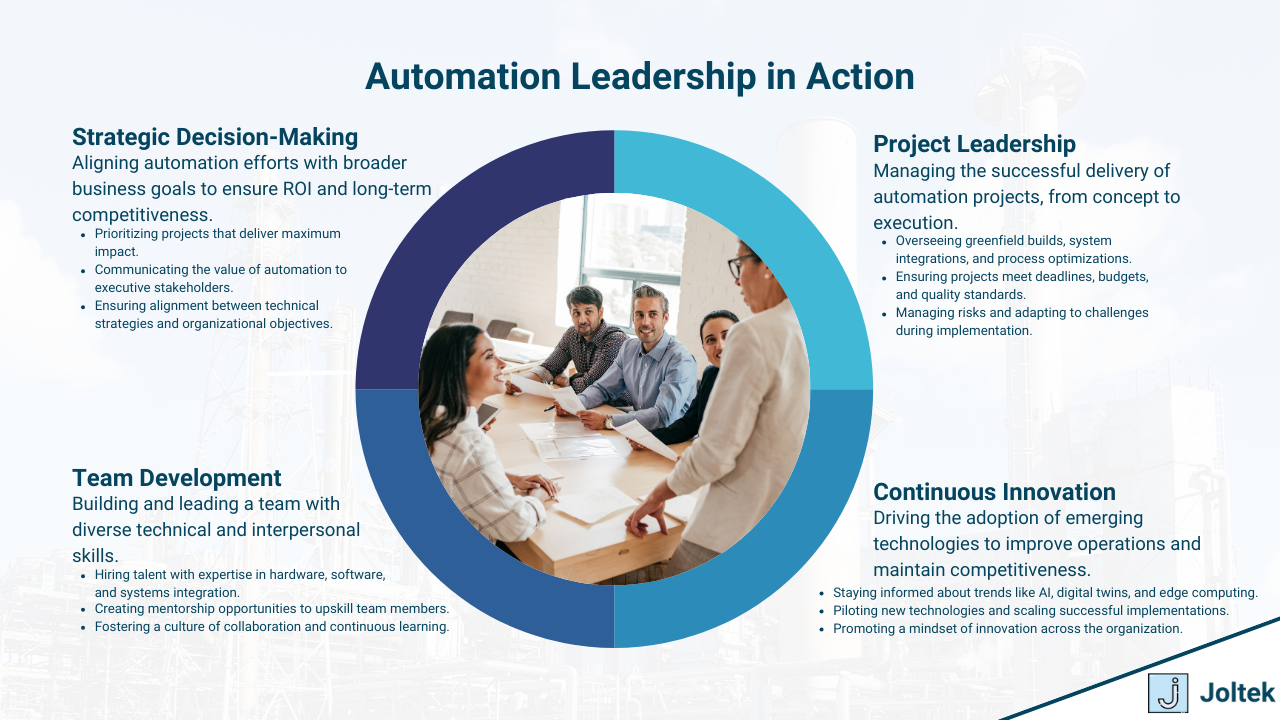
The Role of Automation Leaders
For automation leaders, embracing data-driven innovation means more than just implementing new technologies—it’s about fostering a culture of continuous improvement. Leaders must ensure that teams are equipped to work with data, whether by training operators to use MES dashboards or hiring data analysts to develop advanced models.
The ability to leverage data effectively can transform manufacturing systems, enabling organizations to achieve greater efficiency, reliability, and agility. By overcoming challenges and focusing on long-term value, automation leaders can position their organizations for success in an increasingly data-driven world.
IT/OT Convergence and Automation Leadership
As industries become more interconnected and data-driven, the convergence of Information Technology (IT) and Operational Technology (OT) has become a critical area of focus. IT/OT convergence involves integrating enterprise-level IT systems, like ERP and cloud infrastructure, with shop-floor OT systems, such as PLCs, SCADA, and MES. This fusion enables seamless data flow, better decision-making, and improved operational efficiency. However, achieving this convergence requires careful navigation of the distinct priorities, cultures, and technologies of both domains.
For automation leaders, IT/OT convergence represents both an opportunity and a challenge. By fostering collaboration and adopting modern practices, they can bridge the gap and unlock the full potential of integrated systems.
Bridging the Gap Between IT and OT
IT and OT teams traditionally operate in silos, with distinct goals and approaches. Understanding these differences is key to effective collaboration.
- IT Teams prioritize data security, scalability, and compliance with enterprise standards. Their focus is often on long-term system stability, data analytics, and centralized control.
- OT Teams, on the other hand, emphasize real-time performance, process reliability, and safety on the production floor. They are accustomed to working with specialized hardware, proprietary protocols, and deterministic systems.
Automation leaders must act as translators, helping both teams understand each other’s priorities and working together to design integrated solutions. For example:
- Security protocols from IT must be adapted to ensure minimal disruption to real-time OT operations.
- OT’s need for low-latency, high-reliability communication must be balanced with IT’s focus on scalability and cloud integration.
Collaborative efforts should focus on creating systems that are secure, high-performing, and user-friendly. Regular cross-functional meetings, shared goals, and clear communication are essential for success.
Incorporating Software Development Practices into Automation
As IT and OT converge, software development practices are becoming increasingly relevant in automation projects. These practices can enhance system reliability, scalability, and maintainability.
- Version Control: Tools like Git or Subversion can help track changes to PLC programs, HMI configurations, and SCADA systems. This reduces errors, improves collaboration, and simplifies troubleshooting.
- Unit Testing: Borrowed from software engineering, unit testing ensures that individual components of automation systems (e.g., function blocks, AOIs) perform as expected before deployment. This minimizes on-site commissioning issues.
- Scalable Architectures: Designing modular and scalable systems allows organizations to adapt to future needs without significant rework. For example, using reusable templates in Ignition or AOIs in Rockwell systems ensures consistency and efficiency.
- Agile Methodologies: Agile principles, such as iterative development, rapid prototyping, and continuous feedback, can be adapted to industrial automation projects. This approach ensures that projects remain aligned with changing requirements and deliver incremental value.
The Role of Cloud and Edge Computing in Modern Automation
Cloud and edge computing are transforming how automation systems are designed and deployed, offering new opportunities for IT/OT integration.
- Cloud Computing: Cloud platforms enable centralized data storage, advanced analytics, and remote monitoring. For example, predictive maintenance algorithms can run in the cloud, leveraging historical data from multiple facilities to identify trends and optimize performance.
- Edge Computing: Edge devices process data closer to the source, reducing latency and bandwidth requirements. This is critical for real-time applications, such as controlling machines or detecting anomalies on production lines.
- Hybrid Models: Many organizations adopt hybrid architectures, where edge devices handle immediate, time-critical tasks while sending aggregated data to the cloud for long-term analysis and reporting.
Automation leaders must evaluate their organization’s specific needs to determine the right balance of cloud and edge computing. Factors such as latency, security, and data ownership should guide these decisions.
The Role of Automation Leaders
Automation leaders are instrumental in driving IT/OT convergence and adopting modern practices. Their responsibilities include:
- Facilitating collaboration between IT and OT teams by fostering mutual understanding and shared objectives.
- Advocating for software development practices that improve reliability, scalability, and maintainability in automation systems.
- Guiding the adoption of cloud and edge technologies to enhance system performance and enable data-driven decision-making.
By bridging the gap between IT and OT, automation leaders can help their organizations achieve greater efficiency, flexibility, and innovation, positioning them for success in the rapidly evolving landscape of industrial automation.
The Future of Automation Leadership
As industrial automation evolves, the role of automation leaders is expanding to encompass not only technical expertise but also strategic foresight and adaptability. The integration of advanced technologies, the emphasis on sustainability, and the need for cross-disciplinary collaboration are shaping a future that demands a new breed of leadership. Automation leaders who can anticipate trends, build agile teams, and navigate complex challenges will drive innovation and create competitive advantages for their organizations.
Emerging Trends in Industrial Automation
The future of automation is being shaped by several transformative trends, each offering new opportunities and challenges for leaders in the field:
- AI, Digital Twins, and Advanced Analytics
Artificial intelligence (AI) and machine learning (ML) are revolutionizing industrial automation by enabling predictive maintenance, anomaly detection, and process optimization. Digital twins—virtual replicas of physical systems—offer powerful tools for real-time monitoring, simulation, and scenario planning. Automation leaders must harness these technologies to unlock efficiencies and improve decision-making at every level of operations. - The Push Toward Renewable Energy and Sustainable Manufacturing
As industries face mounting pressure to reduce their environmental impact, renewable energy and sustainable practices are becoming central to automation strategies. Leaders must integrate energy-efficient systems, adopt renewable energy sources, and optimize resource usage through smart automation solutions. The role of automation in decarbonizing manufacturing processes is expected to grow significantly in the coming years.
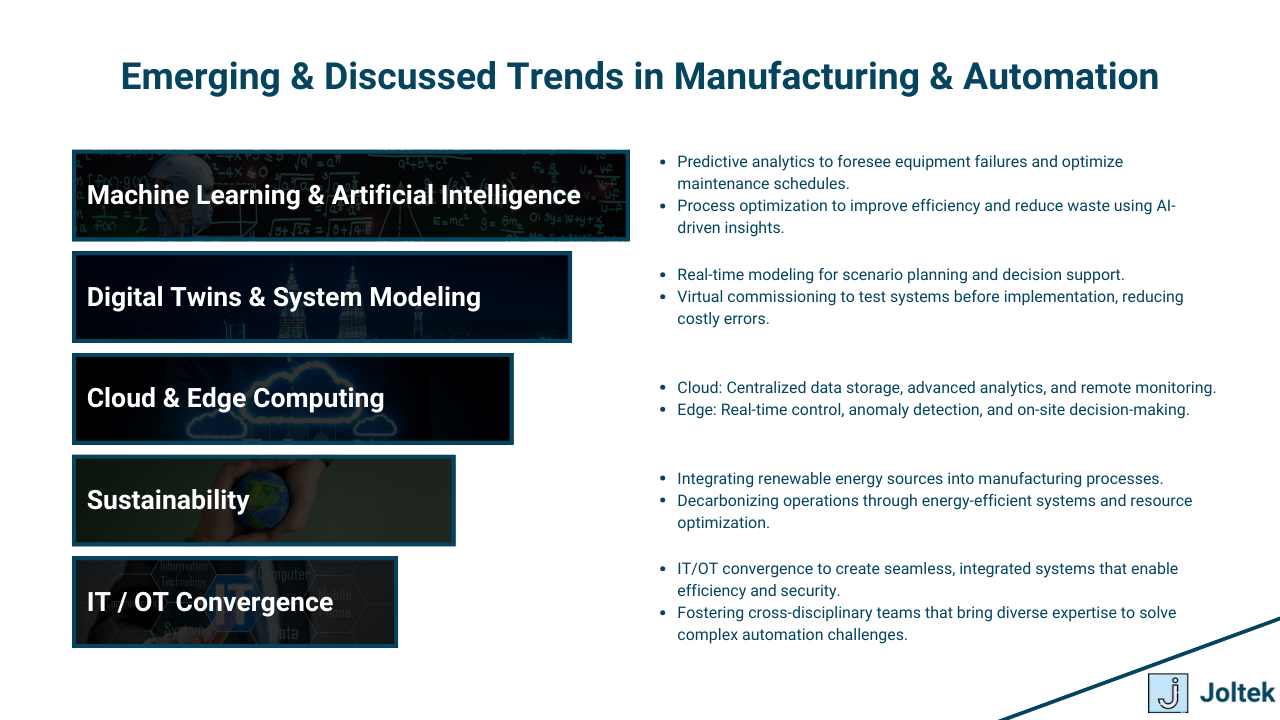
Skills for the Future
The evolving nature of industrial automation calls for leaders who possess a broad range of technical and interpersonal skills. Key competencies for future automation leaders include:
- Cross-Disciplinary Knowledge
The convergence of IT and OT, along with the adoption of cloud computing, AI, and edge technologies, requires leaders to understand multiple disciplines. A strong grasp of software engineering, data science, and traditional automation systems will be critical for navigating the complexities of modern industrial environments. - Building a Culture of Continuous Learning and Adaptability
The pace of technological change means that automation teams must continually update their skills. Leaders must foster a culture of learning by encouraging professional development, embracing new tools and methodologies, and staying informed about industry advancements. Adaptability and resilience will be essential as organizations encounter new challenges and opportunities.
Predictions for the Industry
The future of automation leadership will be defined by increasing complexity, demand for innovation, and the need for strategic thinking. Some key predictions include:
- Growing Demand for Automation Leaders
Organizations will increasingly seek leaders who can bridge the gap between technical expertise and strategic management. These individuals will be tasked with aligning automation initiatives with broader business goals, driving ROI, and ensuring long-term sustainability. - A Greater Focus on Collaborative Leadership
As automation systems become more interconnected, leaders will need to collaborate with stakeholders across IT, operations, and executive management. This requires strong communication skills, the ability to mediate between conflicting priorities, and the vision to align teams around shared objectives. - The Rise of Automation as a Strategic Function
Automation will no longer be viewed as a support function but as a core driver of innovation and competitive advantage. Leaders in this space will play a pivotal role in shaping their organization’s direction and ensuring its success in an increasingly digital and sustainable world.
The Role of Automation Leaders
To thrive in the future of industrial automation, leaders must balance technical expertise with strategic vision. They must champion emerging technologies, lead initiatives that prioritize sustainability, and cultivate a workforce prepared for continuous change. By embracing these responsibilities, automation leaders can help their organizations achieve operational excellence, reduce their environmental impact, and adapt to the challenges of the 21st century.
The journey ahead is both exciting and demanding. Automation leadership will be at the forefront of shaping industries, redefining processes, and building a future where technology and sustainability go hand in hand. The next generation of leaders will be those who can anticipate trends, inspire innovation, and navigate the complexities of an increasingly automated world.
Conclusion
The world of industrial automation is evolving rapidly, offering engineers and leaders unprecedented opportunities to shape the future of manufacturing and process industries. Key themes such as technical upskilling, leadership growth, and cross-disciplinary collaboration are not just trends but essential pillars for success in this ever-changing landscape. Engineers who embrace these challenges and prepare themselves for the demands of automation leadership will be well-positioned to thrive.
The journey to becoming an automation leader starts with a commitment to lifelong learning. Whether it’s mastering PLC programming, understanding SCADA and MES systems, or adopting modern practices like version control and predictive analytics, technical upskilling is the foundation of effective leadership. Equally important is the ability to grow as a leader—building and managing diverse teams, fostering mentorship, and evolving from a technical expert to a strategic decision-maker.
Collaboration lies at the heart of successful automation initiatives. Bridging the gap between IT and OT, fostering communication across teams, and integrating cutting-edge technologies with legacy systems are challenges that require openness and shared understanding. Leaders who can facilitate this collaboration will not only drive innovation but also build resilient organizations ready to meet the challenges of the future.
For engineers considering a transition into automation leadership, now is the time to take ownership of your career path. Embrace opportunities to build both technical and leadership skills. Seek mentorship, take on cross-functional projects, and explore new technologies that push the boundaries of your expertise. Engage with automation communities, participate in industry discussions, and share your knowledge and insights.
The future of industrial automation is being written today, and every engineer and leader has a role to play. By preparing yourself for the challenges ahead and contributing to the collective advancement of the industry, you can help shape a more efficient, sustainable, and innovative world. The time to act is now—step forward and take your place as a leader in the next generation of automation.