Introduction to Automation in Manufacturing
What is Automation in Manufacturing?
Automation in manufacturing refers to the use of technology, robotics, and software-driven systems to perform tasks with minimal human intervention. It encompasses a wide range of applications, from simple mechanized processes to fully integrated smart factories. The primary goal of automation is to enhance efficiency, precision, and scalability while reducing reliance on manual labor. Over the years, automation has evolved from basic mechanical systems to advanced AI-driven production lines that can optimize workflows, predict maintenance needs, and adapt to changing demands.
Why is Automation Important in Manufacturing?
The manufacturing industry is under constant pressure to improve efficiency, reduce costs, and maintain high product quality. Automation plays a crucial role in meeting these challenges by enabling continuous production, reducing human error, and streamlining operations. Automated systems can work around the clock without fatigue, ensuring higher output and consistent quality. Additionally, automation enhances workplace safety by minimizing workers' exposure to hazardous environments, repetitive tasks, and physically demanding labor. While the initial investment in automation can be significant, the long-term benefits often outweigh the costs, as manufacturers see reductions in waste, labor expenses, and downtime. Furthermore, automation provides the flexibility to quickly adapt to changes in production demand, making it an essential component of modern manufacturing strategies.
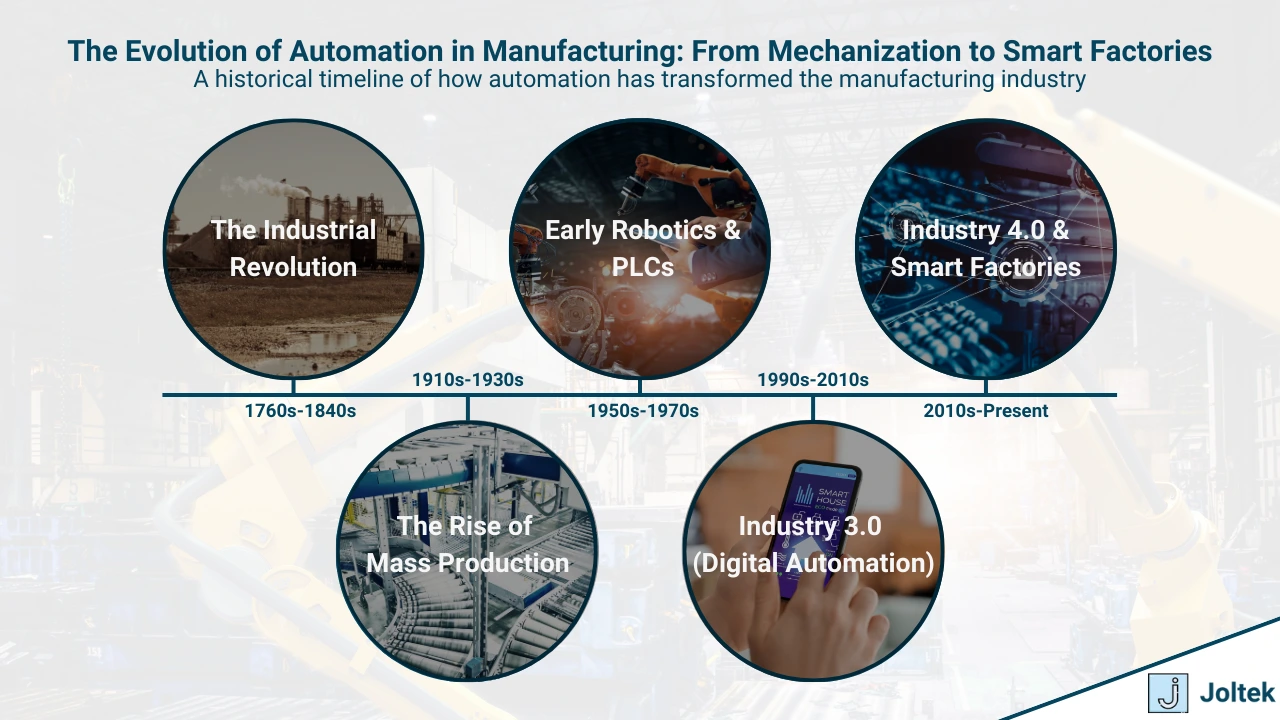
A Brief History of Automation
Automation has been an integral part of manufacturing since the Industrial Revolution, when mechanized tools and steam-powered machinery first replaced manual labor. The early 20th century saw the rise of mass production techniques, most notably Henry Ford’s assembly line, which revolutionized manufacturing efficiency. By the mid-1900s, the introduction of programmable logic controllers (PLCs) and computer numerical control (CNC) machines allowed manufacturers to automate complex processes with greater precision. In recent decades, advancements in robotics, artificial intelligence, and the Industrial Internet of Things (IIoT) have ushered in the era of smart manufacturing, where data-driven decision-making and real-time process optimization are becoming standard practices.
Key Technologies Driving Automation Today
Modern manufacturing automation is powered by a combination of robotics, artificial intelligence, and interconnected digital systems. Industrial robots and collaborative robots, or cobots, are increasingly used for tasks such as assembly, material handling, and welding. IoT-enabled sensors and AI-driven analytics provide manufacturers with real-time insights into machine performance, predictive maintenance, and quality control. Programmable logic controllers (PLCs) and supervisory control and data acquisition (SCADA) systems remain essential for automating and monitoring industrial processes. In logistics and warehouse automation, autonomous mobile robots (AMRs) and automated guided vehicles (AGVs) help streamline material transport and inventory management. As technology continues to evolve, these innovations will further enhance manufacturing efficiency, adaptability, and competitiveness in the global market.
The Evolution of Automation in Manufacturing
The Origins of Automation in Industrial Settings
Automation in manufacturing traces its roots back to the Industrial Revolution, which began in the late 18th century. Before mechanization, most manufacturing relied on skilled artisans and manual labor. The introduction of steam engines, mechanized looms, and early assembly processes transformed production by significantly increasing efficiency and output. Factories began utilizing powered machinery to reduce the reliance on human effort, leading to faster and more scalable production. Mechanization allowed industries such as textiles, ironworks, and agriculture to expand rapidly, laying the foundation for modern automated systems.
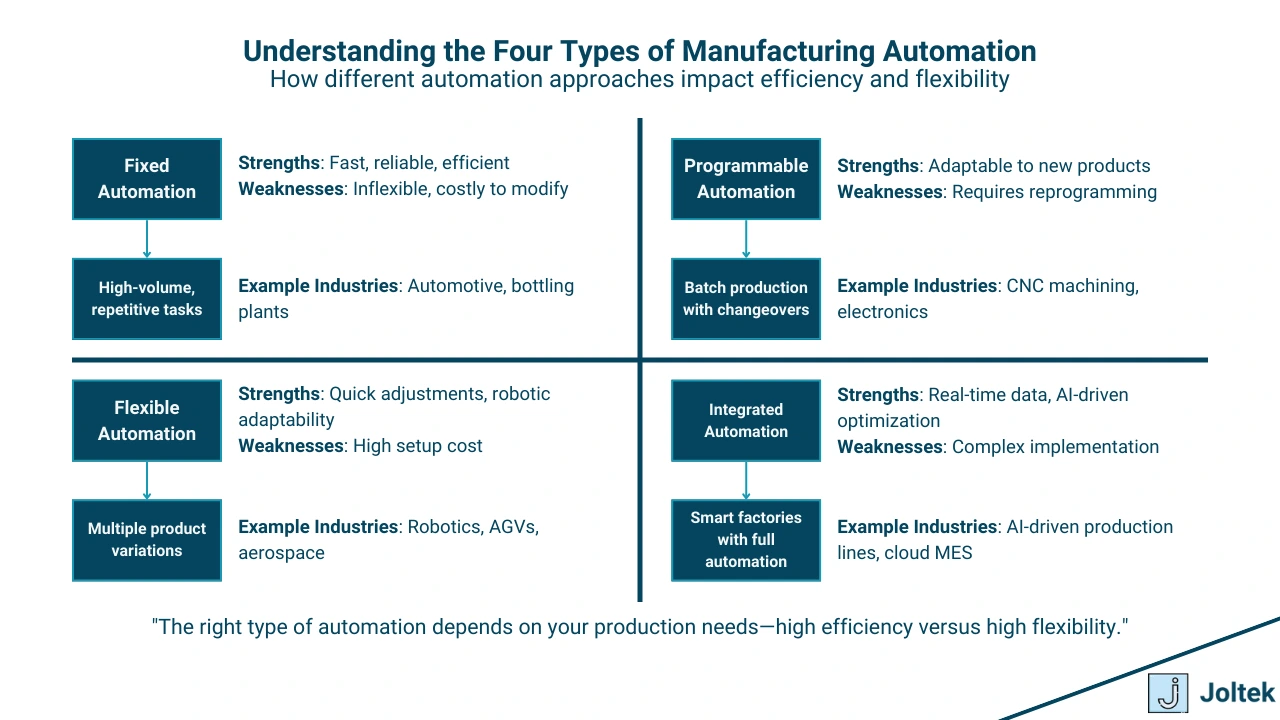
The Rise of Mass Production and Early Automation
The early 20th century marked a significant leap in manufacturing automation with the introduction of mass production techniques. Henry Ford’s assembly line, introduced in 1913, revolutionized the automotive industry by standardizing production processes and dramatically reducing manufacturing time. Instead of workers building a car from start to finish, vehicles were assembled in a sequential, repetitive process with specialized tasks at each station. This method improved efficiency, lowered costs, and set a precedent for automation by minimizing the need for skilled labor in every aspect of production. Other industries quickly adopted similar mass production methods, accelerating industrial growth worldwide.
The Introduction of Robotics and PLCs in the Mid-20th Century
The mid-20th century saw the emergence of electronic and programmable automation. In 1961, General Motors introduced the Unimate, the first industrial robot, which was used for material handling and welding on automotive production lines. This marked the beginning of robotic automation in manufacturing, where machines could perform repetitive and dangerous tasks with precision. At the same time, programmable logic controllers (PLCs) were developed to automate and control industrial processes. PLCs replaced relay-based systems with digital logic controllers, enabling greater flexibility and efficiency in manufacturing operations. These innovations reduced dependency on human intervention, allowing factories to scale production while improving quality and reliability.
The Digital Transformation Era: Industry 3.0 to Industry 4.0
By the late 20th century, manufacturing entered the Industry 3.0 phase, characterized by the adoption of computer-controlled systems and automation software. Computers and integrated circuits enabled factories to operate with greater efficiency, accuracy, and consistency. The introduction of computer numerical control (CNC) machines allowed manufacturers to automate complex machining processes, increasing productivity and reducing errors. Enterprise resource planning (ERP) systems and supervisory control and data acquisition (SCADA) systems further streamlined manufacturing operations by providing real-time data monitoring and process optimization.
The 21st century brought about Industry 4.0, often referred to as the era of smart manufacturing. This transformation integrates digital technologies such as artificial intelligence (AI), machine learning, cloud computing, and the Industrial Internet of Things (IIoT) into automated systems. Sensors and IoT devices now collect and analyze data in real-time, allowing manufacturers to implement predictive maintenance, improve quality control, and optimize production workflows. The shift toward interconnected and data-driven manufacturing has enabled factories to achieve greater efficiency, flexibility, and sustainability.
Modern Trends: AI-Driven Automation, Collaborative Robots, and Hyperautomation
Automation in manufacturing continues to evolve with advancements in AI-driven decision-making, robotics, and process automation. Collaborative robots, or cobots, are designed to work alongside human operators, enhancing productivity while maintaining safety. Unlike traditional industrial robots, cobots are flexible and easily programmable, making them ideal for a wide range of applications in industries such as electronics, pharmaceuticals, and food production.
Hyperautomation, a concept that combines AI, robotics, and advanced analytics, is also gaining traction in modern manufacturing. This approach integrates multiple automation technologies to create fully autonomous systems capable of adapting to real-time changes in demand and production requirements. Autonomous mobile robots (AMRs), self-learning AI-driven manufacturing systems, and cloud-based production planning platforms are pushing automation toward fully autonomous, self-optimizing factories.
The evolution of automation in manufacturing has been driven by the need for efficiency, cost reduction, and higher production quality. From the mechanized systems of the Industrial Revolution to AI-powered smart factories, automation continues to shape the future of manufacturing by enabling greater flexibility, precision, and scalability in industrial operations.
The Different Types of Automation in Manufacturing
Automation in manufacturing is not a one-size-fits-all approach. Different industries and production environments require varying levels of automation to achieve efficiency, flexibility, and scalability. Broadly, manufacturing automation can be categorized into four main types: fixed automation, programmable automation, flexible automation, and integrated automation. Each type serves a distinct purpose and offers unique advantages depending on production requirements.
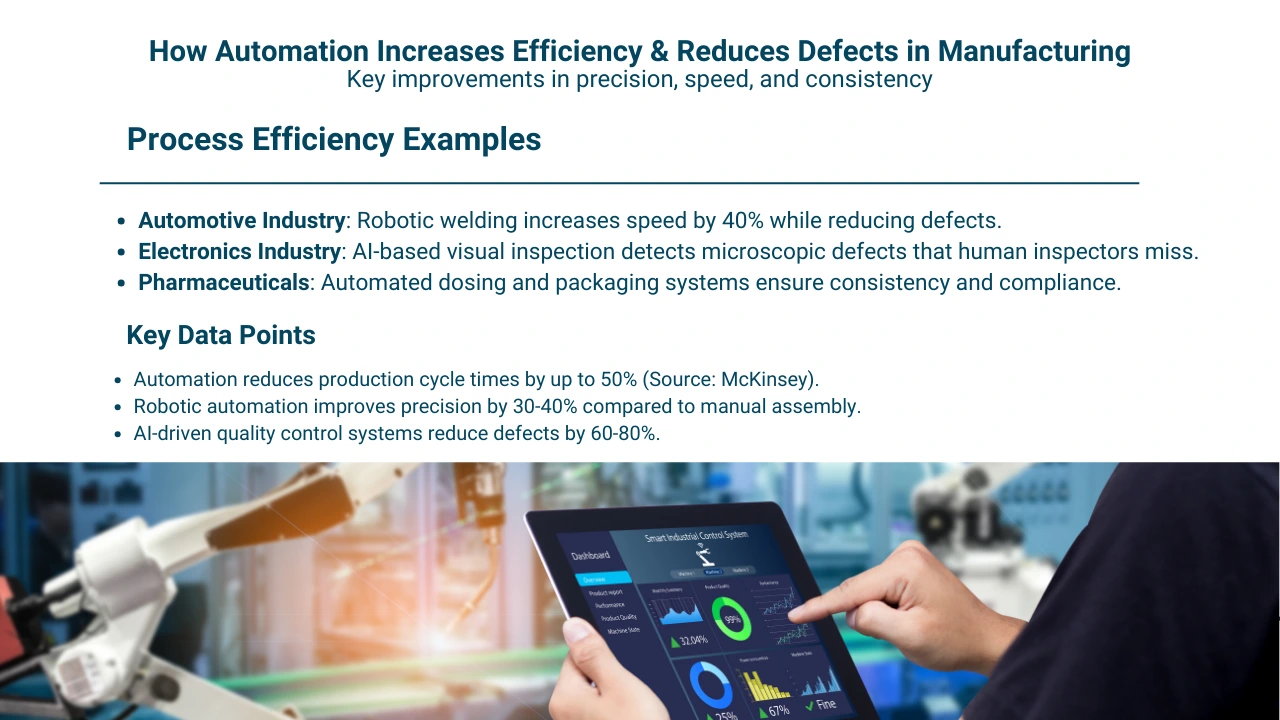
Fixed Automation (Hard Automation)
Fixed automation, also known as hard automation, is designed for high-volume, repetitive production processes where product variations are minimal. This type of automation is commonly found in industries that require large-scale, continuous manufacturing with predefined production sequences and minimal changeovers.
One of the most recognizable examples of fixed automation is automotive assembly lines, where robotic arms perform welding, painting, and assembly tasks in a highly structured environment. Similarly, bottling plants utilize fixed automation to fill, cap, and label products at high speeds with precision and consistency.
The primary advantage of fixed automation is high efficiency and consistency. Since these systems are specifically designed for dedicated tasks, they offer exceptional production speed and minimal variability. However, the downside is inflexibility—once a fixed automation system is set up, modifying it to accommodate new product designs or variations can be costly and time-consuming. Additionally, the initial investment in fixed automation equipment and infrastructure can be substantial, making it more suitable for large-scale manufacturers with stable, high-volume production needs.
Programmable Automation
Unlike fixed automation, programmable automation provides more flexibility by allowing production parameters to be modified through programming. This type of automation is commonly used in batch production environments, where different product variations need to be manufactured without requiring a complete system overhaul.
One of the best examples of programmable automation is CNC (Computer Numerical Control) machines, which can be reprogrammed to cut, drill, or shape different components based on changing design specifications. Another example is batch production systems, where a single manufacturing line can produce multiple product variants by adjusting machine settings between production runs.
The main benefit of programmable automation is its adaptability, making it well-suited for industries that experience frequent product design changes. However, reprogramming and reconfiguring the system requires time and expertise, which can result in downtime between production runs. As a result, programmable automation is ideal for mid-volume production where customization is necessary, but full flexibility is not required.
Flexible Automation
Flexible automation builds upon programmable automation by minimizing downtime and allowing for more seamless transitions between product variations. In a flexible automation system, manufacturing equipment is designed to respond dynamically to different product specifications without requiring manual intervention.
A prime example of flexible automation is the use of robotic arms in manufacturing, which can switch between multiple tasks based on programmed instructions and real-time input. Another example is automated guided vehicles (AGVs), which autonomously transport materials within a factory floor, adapting to workflow changes and production demands.
The greatest advantage of flexible automation is its ability to accommodate product diversity without significant disruptions to production. This makes it highly valuable for industries that require frequent changes in manufacturing, such as electronics, consumer goods, and aerospace. However, the cost and complexity of implementation can be higher than programmable automation, as it requires sophisticated sensors, AI-driven decision-making, and interconnected control systems to function efficiently.
Integrated Automation
Integrated automation represents the highest level of automation, where all manufacturing processes are interconnected through advanced digital systems and data-driven decision-making. This type of automation is at the core of smart factories, where machines, software, and artificial intelligence work together to create an autonomous production environment.
An example of integrated automation is a fully connected manufacturing execution system (MES), which links production machinery, quality control systems, and enterprise resource planning (ERP) software to provide real-time visibility and control over the entire production process. Integrated automation is also evident in Industry 4.0 smart factories, where IoT-enabled machines communicate with each other to optimize efficiency, minimize downtime, and reduce waste.
The major benefit of integrated automation is end-to-end workflow automation, enabling manufacturers to achieve higher levels of efficiency, predictive maintenance, and real-time process optimization. However, implementing integrated automation requires significant investment in infrastructure, software, and cybersecurity measures, making it most suitable for large-scale manufacturers looking to transition into fully automated, data-driven operations.
The Role and Applications of Automation in Manufacturing
Automation is transforming manufacturing by enhancing production efficiency, improving product quality, augmenting the workforce, streamlining logistics, and advancing sustainability efforts. From traditional assembly lines to AI-driven predictive maintenance, manufacturers across various industries are leveraging automation to remain competitive, improve operational resilience, and optimize resources. Below, we explore the most significant applications of automation in manufacturing.
Production Efficiency and Quality Improvement
One of the most compelling reasons for implementing automation in manufacturing is its ability to significantly enhance production efficiency while improving product quality. Automated systems reduce human errors and variability in processes, ensuring precision and consistency across high-volume production runs. In industries such as automotive manufacturing, robotic welding and painting systems achieve uniform quality by maintaining consistent parameters, something that is challenging to replicate manually. In the electronics sector, automated optical inspection (AOI) and pick-and-place machines ensure that delicate components are placed with pinpoint accuracy, reducing the risk of defects. Similarly, in pharmaceutical manufacturing, automation helps ensure product safety and compliance with strict regulatory standards by minimizing contamination risks and improving traceability.
Beyond reducing defects, automation also boosts production output. Machines can operate continuously without fatigue, unlike human workers who require breaks and shifts. With the integration of Manufacturing Execution Systems (MES), companies can monitor production performance in real-time, allowing for immediate adjustments to maintain optimal throughput. For manufacturers looking to leverage MES to enhance production efficiency, Joltek’s article on Understanding MES Components: Practical Deployment and Benefits for Manufacturing Efficiency provides deeper insights.
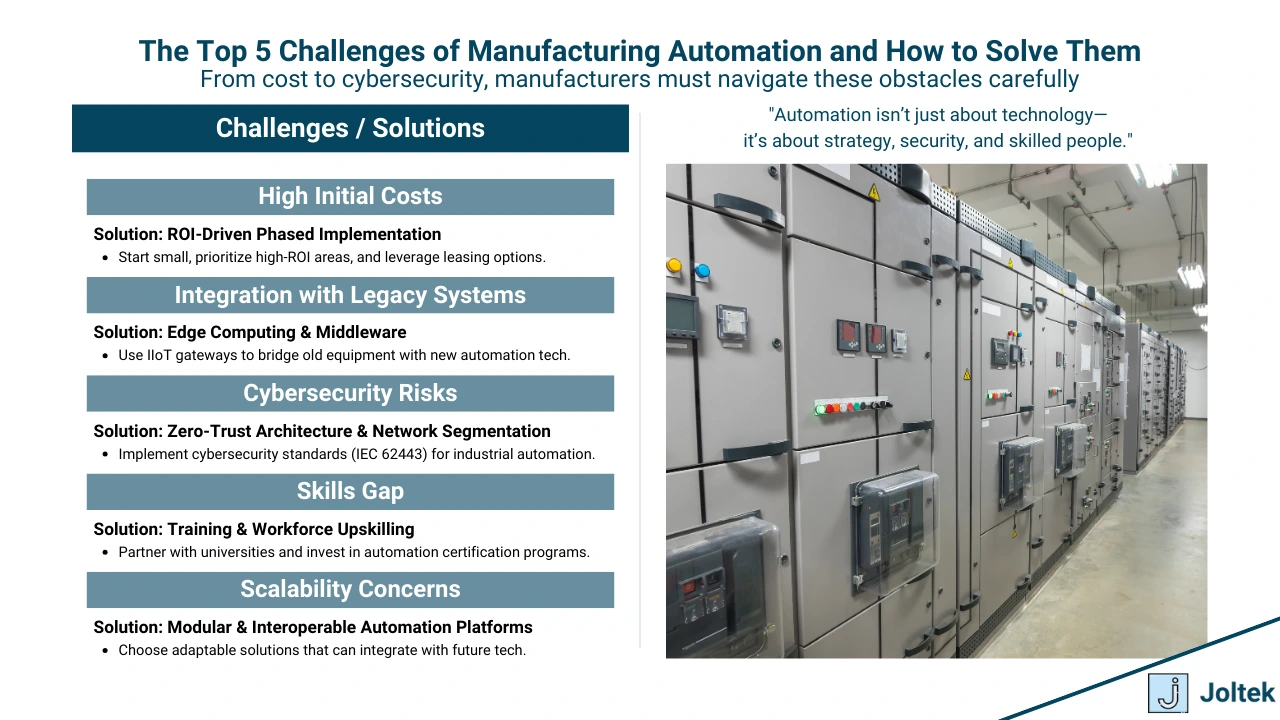
Workforce Augmentation and Safety
Automation does not necessarily replace human workers but rather augments their capabilities by eliminating repetitive, labor-intensive, and hazardous tasks. One of the most significant advancements in workforce augmentation is the introduction of collaborative robots (cobots)—robots designed to work alongside humans rather than replace them. Unlike traditional industrial robots that are confined to safety cages, cobots have built-in sensors and safety mechanisms that allow them to operate safely in shared workspaces with human workers. This is particularly beneficial in assembly lines, where cobots can handle delicate components while humans focus on quality control and final assembly tasks.
In addition to increasing efficiency, automation dramatically improves workplace safety. Many manufacturing environments involve exposure to hazardous materials, extreme temperatures, and physically strenuous activities. Automated material handling systems, such as robotic palletizers and autonomous forklifts, help reduce the risk of injuries associated with heavy lifting. AI-driven predictive maintenance further enhances safety by identifying potential equipment failures before they cause accidents. This proactive approach minimizes unexpected breakdowns, ensuring that machinery remains in safe operating conditions. By integrating automation strategically, manufacturers can create safer and more ergonomic work environments while maintaining productivity.
Supply Chain and Logistics Automation
Automation is revolutionizing supply chain and logistics management by improving speed, accuracy, and efficiency. The integration of automated material handling systems, warehouse robotics, and AI-driven inventory management solutions allows manufacturers to streamline operations from raw material procurement to final product distribution. Automated Guided Vehicles (AGVs) and Autonomous Mobile Robots (AMRs) are increasingly used in warehouses and production facilities to transport materials with minimal human intervention. These robotic systems optimize material flow, ensuring that the right components arrive at the right workstation just in time, reducing production delays and inventory costs.
In warehouse logistics, automated storage and retrieval systems (AS/RS) improve inventory management by using robotic systems to store and retrieve items efficiently. This reduces reliance on manual picking, decreasing errors and improving order fulfillment speed. AI-driven demand forecasting further enhances supply chain resilience by analyzing market trends and adjusting inventory levels accordingly. For manufacturers looking to optimize supply chain operations through automation, Joltek’s article on Understanding Supply Chains: How They Work, Why They Matter, and Where They're Headed explores these concepts in greater detail.
Workflow Automation in Manufacturing
Manufacturing operations involve complex workflows that require seamless coordination between machines, systems, and human operators. Workflow automation refers to the digitalization and integration of these processes to improve efficiency, reduce manual intervention, and enhance data visibility. Cloud-based Manufacturing Execution Systems (MES) play a crucial role in enabling real-time workflow automation by connecting production lines, monitoring machine performance, and facilitating data-driven decision-making.
Predictive maintenance is another key aspect of workflow automation. By leveraging IoT sensors and AI-driven analytics, manufacturers can track machine conditions and detect early warning signs of potential failures. This proactive approach prevents costly downtime and extends the lifespan of critical equipment. Additionally, automated quality control systems use machine vision and AI-powered defect detection to inspect products during production, ensuring that only high-quality items reach the market. These workflow automation strategies contribute to overall operational efficiency and cost savings, allowing manufacturers to maintain a competitive edge in an increasingly digitalized industry.
Sustainability and Energy Efficiency
With increasing pressure on manufacturers to reduce their environmental impact, automation plays a pivotal role in advancing sustainability and energy efficiency. Smart automation systems are designed to minimize waste, optimize energy consumption, and enhance resource utilization. AI-driven energy management systems monitor electricity usage across production lines and automatically adjust power consumption based on demand, reducing overall energy waste. Automated waste management systems sort and recycle materials more efficiently, contributing to circular economy initiatives.
Many manufacturers are now adopting carbon footprint tracking software to measure and report their environmental impact in real-time. This level of automation ensures compliance with global sustainability regulations while also improving cost efficiency by reducing unnecessary resource consumption. In industries such as food and beverage manufacturing, automation helps optimize ingredient usage, reducing spoilage and waste. Similarly, in chemical processing, automated dosing and mixing systems ensure precise ingredient proportions, minimizing excess production and hazardous byproducts.
Challenges and Considerations in Implementing Automation
While automation offers undeniable benefits in manufacturing, its implementation comes with several challenges that companies must carefully navigate. Factors such as cost, integration complexities, cybersecurity, workforce readiness, and long-term adaptability all play critical roles in determining the success of an automation strategy. Below, we explore the major challenges and considerations manufacturers face when implementing automation solutions.
High Initial Investment Costs
One of the most significant barriers to automation adoption is the high upfront investment required for equipment, software, and infrastructure upgrades. Industrial robots, automated guided vehicles (AGVs), manufacturing execution systems (MES), and AI-powered analytics platforms can be expensive to procure and integrate. Additionally, setting up automation requires changes to factory layouts, control systems, and IT infrastructure, adding to the overall cost.
To justify these investments, manufacturers must conduct a return on investment (ROI) analysis, considering factors such as increased productivity, reduced labor costs, improved quality, and minimized downtime. In many cases, financing strategies such as leasing automation equipment, government incentives, and phased implementation approaches can help mitigate financial strain. Cost-benefit analysis should also account for long-term savings on operational expenses, as automation typically leads to lower defect rates, optimized energy consumption, and reduced maintenance costs.
Integration with Legacy Systems
Many manufacturing plants still rely on legacy equipment and outdated control systems that were not originally designed to communicate with modern automation solutions. This poses a significant challenge when attempting to integrate Industrial Internet of Things (IIoT) sensors, cloud-based analytics, and AI-driven automation platforms.
A primary hurdle in this process is IT-OT convergence, where information technology (IT) systems (cloud computing, enterprise resource planning, cybersecurity) must seamlessly interact with operational technology (OT) systems (PLCs, SCADA, industrial control systems). Differences in communication protocols, data formats, and security models can lead to compatibility issues, requiring middleware solutions or custom-built industrial edge computing platforms to bridge the gap.
A structured digital transformation roadmap is essential to overcoming these challenges. Companies must assess their existing infrastructure, prioritize interoperability, and implement incremental upgrades rather than attempting a full-scale overhaul. Adopting standardized communication protocols such as MQTT, OPC UA, and REST APIs can also improve integration between modern automation technologies and legacy systems. Manufacturers can refer to Joltek’s article on IT-OT Convergence Challenges and Solutions in Manufacturing for deeper insights into addressing these issues.
Cybersecurity Risks
As manufacturing becomes increasingly digitized, the risk of cyber threats targeting industrial automation systems has grown exponentially. Connected automation solutions, including smart factories, IIoT devices, and cloud-based MES platforms, create new vulnerabilities that hackers can exploit. Ransomware attacks, data breaches, and unauthorized access to control systems pose serious risks to production continuity and intellectual property.
To mitigate cybersecurity threats, manufacturers must adopt a multi-layered security strategy, including:
- Network segmentation – Isolating IT and OT networks to prevent lateral movement of cyber threats.
- Zero-trust security models – Enforcing strict authentication for all connected devices and users.
- Real-time monitoring and threat detection – Using AI-driven cybersecurity solutions to identify anomalies.
- Regular patching and firmware updates – Ensuring that all automation hardware and software remain up to date.
Cybersecurity must be embedded into the automation deployment process from the start, rather than being treated as an afterthought. Compliance with industry standards such as NIST Cybersecurity Framework, IEC 62443, and ISO 27001 is essential to protecting automated manufacturing environments. Manufacturers looking to strengthen their industrial cybersecurity posture can explore Joltek’s article on Cybersecurity Best Practices for Industrial Automation.
Skills Gap and Workforce Readiness
The shift toward automation requires a workforce that is skilled in robotics, industrial programming, data analytics, and cyber-physical systems. However, many manufacturing companies face a skills gap, where existing employees lack the expertise needed to operate and maintain highly automated production environments.
To address this challenge, manufacturers must invest in upskilling and training initiatives, including:
- Technical training programs – Teaching workers to operate and program PLCs, robotic arms, and industrial AI systems.
- Collaboration with academic institutions – Partnering with universities and technical schools to develop automation-focused curriculums.
- On-the-job training and certification programs – Encouraging employees to pursue certifications such as Certified Automation Professional (CAP) or Six Sigma for Automation.
In addition to upskilling existing employees, manufacturers must attract a new generation of engineers, data scientists, and automation specialists to fill critical roles in an increasingly digitalized industry. Without proactive workforce development, companies may struggle to fully leverage automation's potential.
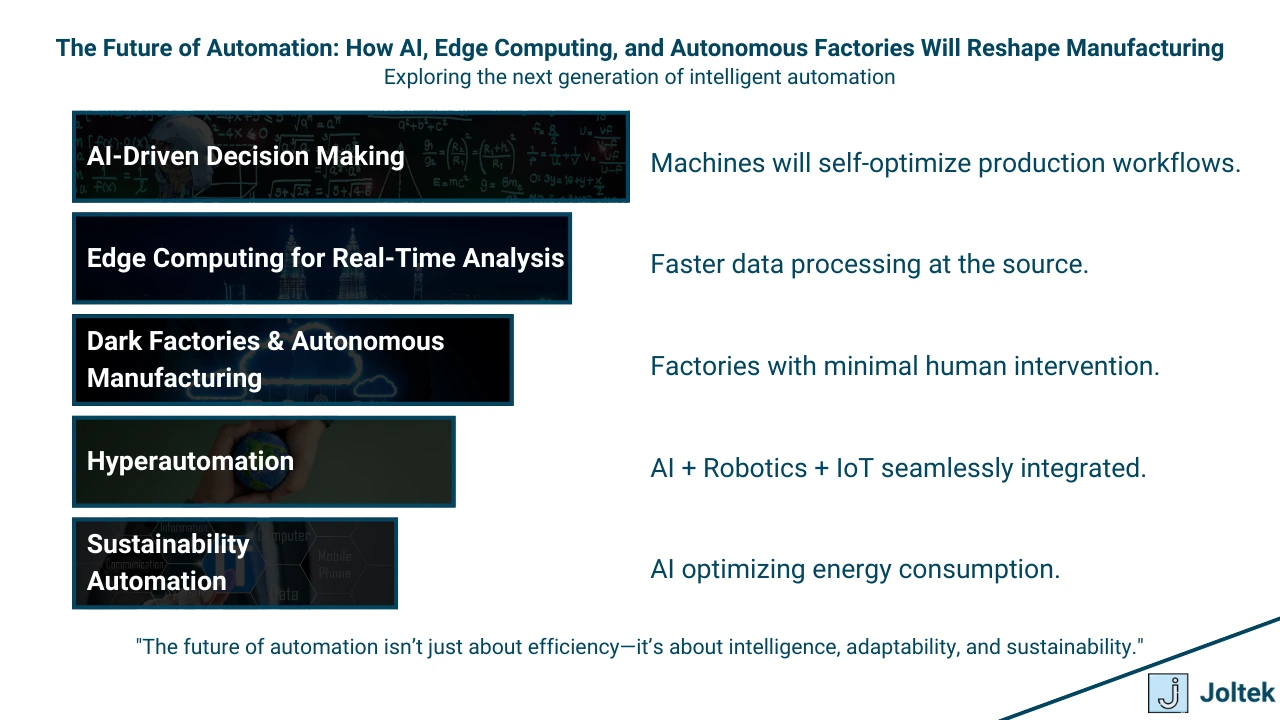
Scalability and Adaptability Concerns
While automation solutions offer immediate benefits, manufacturers must ensure that their automation strategies remain scalable and adaptable to evolving business needs. Rapid shifts in consumer demand, supply chain disruptions, and new technological advancements require automation systems that can adjust dynamically rather than being locked into rigid workflows.
Key considerations for scalable automation include:
- Modular automation systems – Implementing flexible robotic work cells, adaptive conveyor systems, and AI-driven process optimizations that can scale production up or down.
- Cloud and edge computing adoption – Utilizing cloud-based AI analytics for real-time decision-making while maintaining edge computing capabilities for localized control.
- Interoperable automation platforms – Ensuring that all new automation investments can seamlessly integrate with existing and future technologies.
Companies that adopt future-proof automation architectures will be better positioned to adapt to market changes, integrate emerging technologies, and maximize long-term return on automation investments.
Automation’s Impact on Manufacturing
Automation has fundamentally reshaped the manufacturing industry, driving improvements in efficiency, quality, safety, and cost reduction. From the early days of mechanization to today’s AI-driven smart factories, automation has enabled manufacturers to streamline operations, increase production output, and maintain high levels of precision and repeatability. Advanced robotics, manufacturing execution systems (MES), and predictive maintenance solutions have helped companies minimize downtime, reduce defects, and enhance resource utilization. Additionally, automation has extended beyond the production floor, transforming supply chain logistics, inventory management, and sustainability initiatives.
Despite its many advantages, the transition to automation comes with challenges, including high initial costs, IT-OT integration hurdles, cybersecurity threats, and workforce skill gaps. However, companies that successfully address these obstacles stand to gain long-term operational resilience, cost efficiency, and market competitiveness. As industries continue evolving, automation will remain a cornerstone of modern manufacturing strategies.
The Future of Automation: AI, Edge Computing, and Autonomous Factories
The next phase of industrial automation will be characterized by greater intelligence, adaptability, and autonomy. Key emerging technologies will shape the future of manufacturing:
- Artificial Intelligence (AI) and Machine Learning – AI-driven automation systems will go beyond pre-programmed workflows, allowing machines to learn, optimize, and make real-time decisions based on data insights. AI-powered quality control, predictive maintenance, and autonomous production planning will further enhance manufacturing efficiency.
- Edge Computing and Industrial IoT (IIoT) – The increasing adoption of edge computing will enable manufacturers to process and analyze data closer to the source, reducing latency and improving real-time automation responses. IIoT-connected devices will enhance visibility across factory operations, improving monitoring, diagnostics, and performance optimization.
- Autonomous Factories and Dark Manufacturing – The concept of "dark factories", or fully automated production facilities that require minimal human oversight, is becoming more realistic with advancements in robotics, AI, and cloud automation. While human workers will continue to play a role in supervision, maintenance, and strategic decision-making, many production processes will become fully autonomous.
Key Takeaways for Manufacturers Considering Automation
For manufacturers looking to adopt or expand automation, several key considerations should guide their approach:
- Start with a strategic plan – Companies must define clear objectives for automation, whether it’s improving production speed, reducing waste, enhancing product quality, or optimizing supply chain logistics.
- Invest in scalable automation solutions – Choosing modular, adaptable systems ensures that automation investments remain relevant as business needs evolve.
- Prioritize cybersecurity – As industrial networks become increasingly interconnected, strong cybersecurity frameworks must be in place to protect against cyber threats and system vulnerabilities.
- Focus on workforce upskilling – Automation is most effective when combined with a skilled workforce. Manufacturers should invest in technical training, robotics programming, and AI literacy to empower employees to work alongside automation.
- Evaluate ROI and long-term benefits – While automation requires significant investment, long-term cost savings, efficiency gains, and market competitiveness often justify the initial expenses. Conducting a cost-benefit analysis will help manufacturers understand the true value of automation in their operations.
Final Thoughts: Balancing Automation with Workforce Strategies
While automation is transforming manufacturing at an unprecedented pace, the human workforce remains a critical component of industrial success. The most effective automation strategies do not aim to replace workers entirely, but rather augment human capabilities by reducing repetitive tasks, enhancing safety, and enabling employees to focus on higher-value roles such as maintenance, process optimization, and innovation.
By integrating automation with workforce development initiatives, manufacturers can create a balanced approach that leverages the best of both worlds—harnessing the efficiency and precision of machines while capitalizing on the adaptability and problem-solving abilities of human workers.
Ultimately, manufacturers that embrace automation strategically, invest in workforce training, and prioritize long-term adaptability will position themselves for sustained growth, competitiveness, and resilience in an increasingly automated industrial landscape.