Introduction
The 5 Whys Root Cause Analysis (RCA) tool stems out of the lean six sigma approach and is used in factories across the globe to drive productivity in manufacturing. The 5 Whys technique is simple in process, but is a challenging culture shift for most teams that try to adopt it. Our goal is to illustrate the “why” (get it?) you’d want to use this tool, the “what” the tool actually is, and the “how” to implement the tool successfully based on our experience.
Why Use the 5 Whys Root Cause Analysis in Manufacturing
Let’s take a step back and understand why these tools are actually effective in manufacturing. The goal of every manufacturer is to transform raw materials into finished products as cost-effectively as possible. This typically means that they strive to run the equipment as efficiently as possible, invest in maintenance as required, allocate human capital effectively, and ensure that there’s as little waste (quality defects) as possible.
The above generally means that every facility is looking for opportunities they’d invest in, as long as they can get a return on their capital within a defined period of time. These investments are in form of faster equipment, technical training, tools for their team, management practices, etc.
The 5 Whys Root Cause Analysis is a methodology that drives operational excellence through helping the teams better understand their process and equipment which leads to lower MTTR (Mean Time to Repair), higher OEE (Overall Equipment Effectiveness), and a cleared prioritization of tasks when implemented correctly.
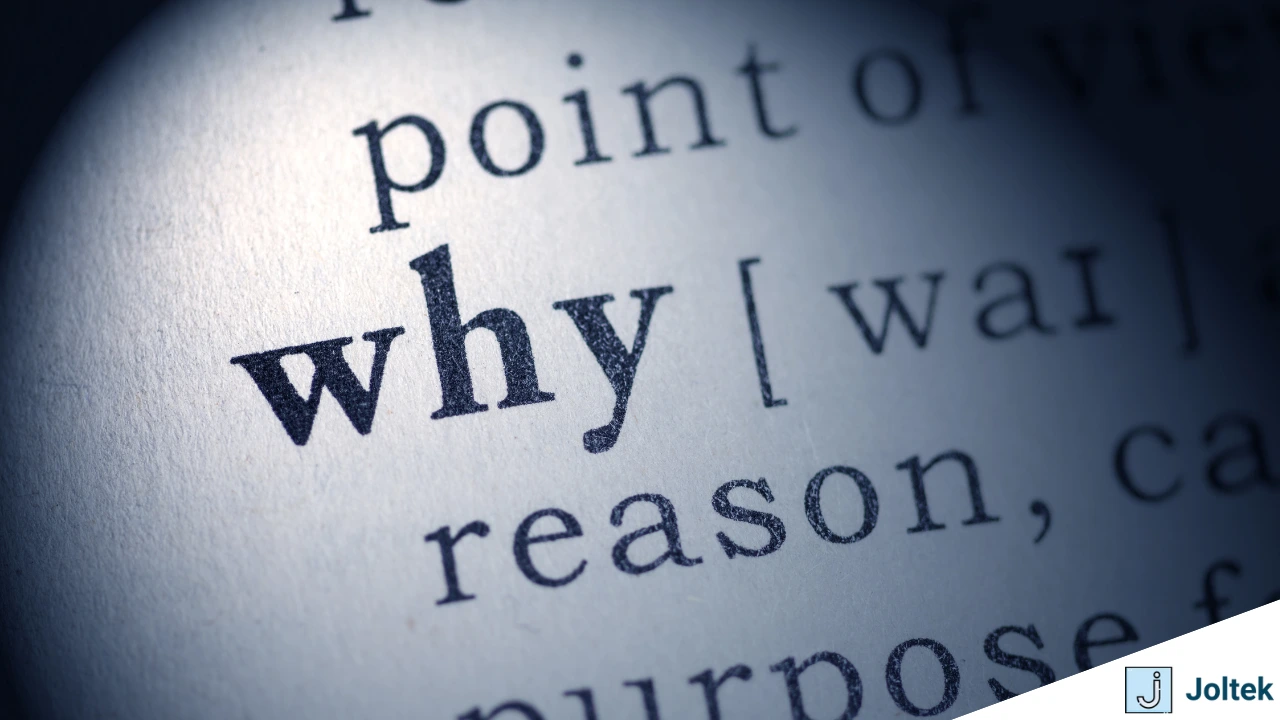
What is the 5 Whys Root Cause Analysis?
The 5 Whys is the process of repeatedly asking “Why” to get to the bottom of a specific problem.
The reality is that it’s rarely that simple…
If you’re looking at the 5 Whys as a tool for your facility, you may immediately dismiss it as “too simplistic.” However, a proper implementation of the 5 Whys is profound. Let’s look at an example that illustrates a flaw in the organizational structure:
Scenario: An operator has observed that the line was stopped due to an alarm on the case packer as indicated by the HMI / SCADA. The operator, unable to reset the machine, calls the maintenance mechanic on shift to troubleshoot the issue.
Upon arrival, the mechanic spends 20 minutes looking at the alarm and determines that there’s a malfunction of the discharge sensor which caused the case packer to stop. The mechanic, with limited electrical knowledge, calls the electrician to look at the problem.
At this point, the line has been down for 30 minutes. The electrician arrives, looks at the fault code, looks at the sensor, identifies that the vibration has loosened the sensor cable, remedies the situation, and resets the machine.
The Impact of the 5 Whys Root Cause Analysis
The example above illustrates something you’d see time and time again on production floors across many different manufacturing plants. Individuals rarely have the skillset nor a framework to investigate a problem before calling the next resource, which then inevitably needs to understand the problem from the ground up. Although one may argue that this issue may have required “electrical expertise,” it is solved by operators in world-class facilities. They solve this problem because they follow a structured problem-solving approach BEFORE reaching out to the higher resource (mechanic > electrician > engineer).
The bottom line is that in facilities that have adopted the 5 Whys, this problem would have been solved in 5 minutes. How much is 45 minutes of downtime worth to you?
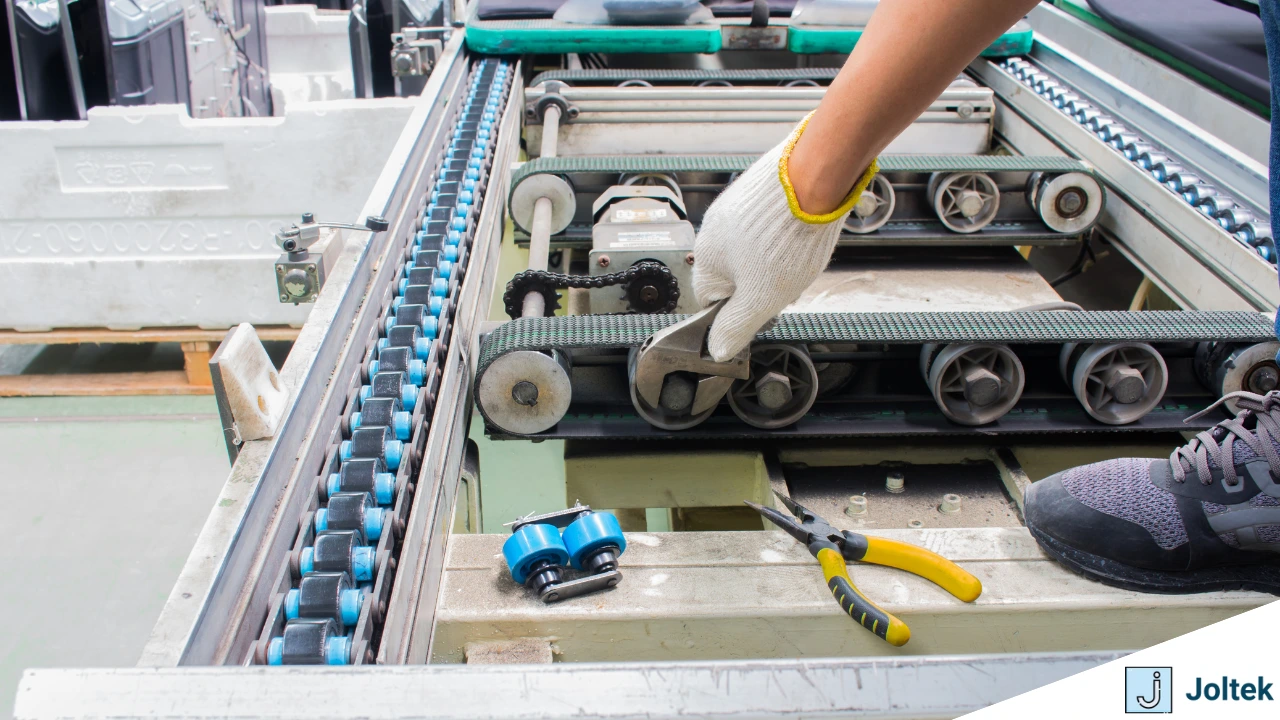
Education, Discipline, and Leadership
“No foundational change happens overnight” - Vlad Romanov.
I’ve seen multiple mistakes executives make when it comes to deploying Root Cause Analysis Tools (Not just the 5 Whys) in their facilities. Let me go through what I’ve seen and why these failed:
Short Timeline | With many change management initiatives, it’s critical to “give things time.” The first time your operators will perform a 5 Whys analysis they aren’t going to get it. The 5th time they’ll perform the analysis, they’ll make mistakes, but realize there’s a benefit to a structured approach. By their 100th report, they’ll understand that it’s not always about the “why,” that there are nuances in how to approach different problems. By their 500th report, they’ll understand the value of the 5 Whys Root Cause analysis, they’ll conduct each one with enthusiasm, they’ll understand which information is valuable for different stakeholders, and they’ll be much more skilled at resolving issues.
Poor Education / Training | Most trainers haven’t experienced a proper implementation of the 5 Whys. Having spent years on the most advanced Procter & Gamble facilities, I can tell you that many have tried to show other facilities the process and failed. They don’t include the nuances, how to follow-up, who’s in charge of each area, etc.
No Leadership Feedback | The key to 5 Whys isn’t the sheet you’ll download at the end of this article. It’s the hours spent coaching and reviewing submissions. Leaders at every level of the organization need to be involved in the 5 Whys rollout. In a practical sense, you need to have regular follow-up meetings at every layer of your team.
Poor Documentation Hygiene | The goal of the process is often to create a document on how to identify and solve a certain problem. If the person who’s looking at the same problem isn’t able to find this report / documentation, they aren’t going to benefit from the process as much as they could. Teams would spend countless hours troubleshooting various parts of the process only to move on to the next issue and leave the problem undocumented.
If you’re serious about implementing the 5 Whys, or any other Root Cause Analysis, best practice tool at your facility you should be expecting a dip in productivity before you see positive results. This is to be expected and is an adjustment period. Many teams would prefer to avoid the uncomfortable conversation with their management and quit before they realize the gains. Believe me that it is well worth the effort.
Conducting a 5 Whys Root Cause Analysis
Let’s dive into the meat of the conversation and discuss how the 5 Whys is conducted in the field.
In general, the 5 Whys approach can be used for various scenarios from simple to fairly complex. The goal of each subsequent “Why” is to narrow down the scope of the problem and provide details that aid in resolving the issue. Don’t get lost in an existential debate if you’ve gotten to a good point in 3 “Whys,” or need 8 of them.
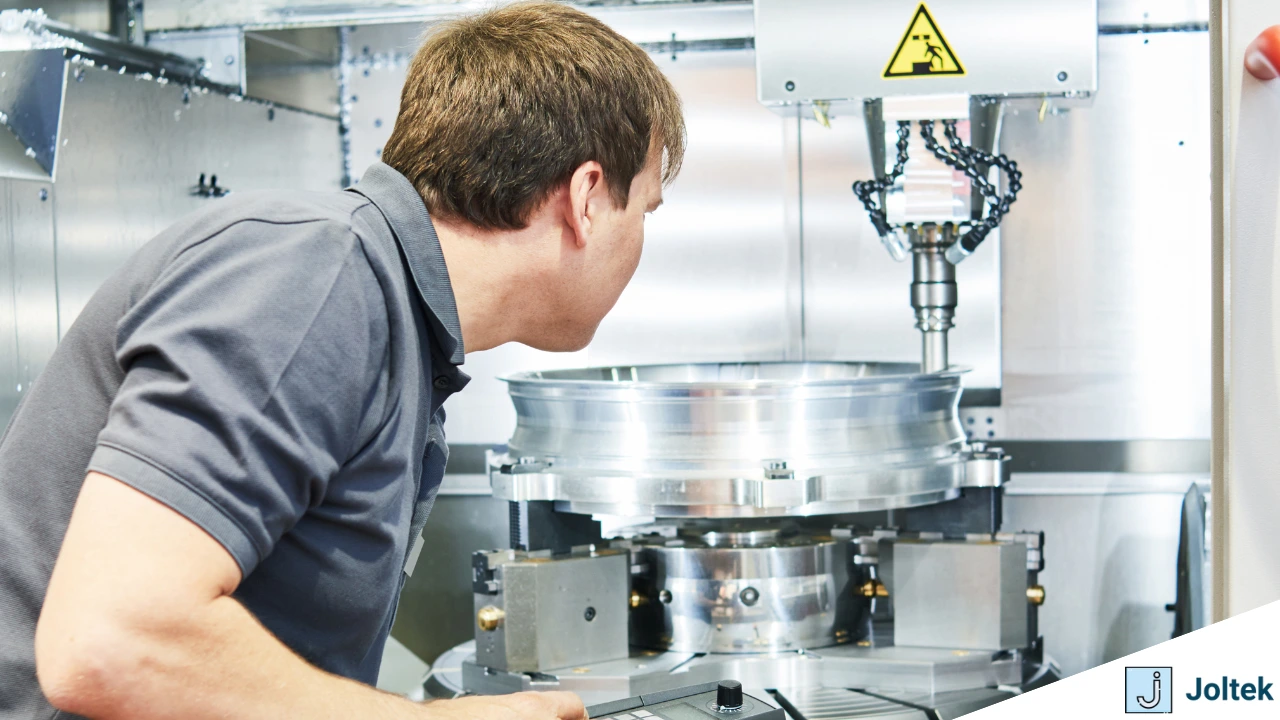
Step 1 - You’ve got a breakdown, alarm, or abnormal situation.
Document and observe the current state of affairs. Collect the information you see - part numbers, alarm codes, people involved, etc.
Step 2 - First Why
Ask yourself, or a person in charge, why this situation took place.
Ex - Why are we seeing “Alarm - The case packer is faulted”
Step 3 - Second Why
Understand the previous situation as much as possible. Take the problem to the next degree.
Ex - Why does this specific alarm stop the case packer?
Gather answers to your question - Ex: The alarm currently displayed is “Case-Packer discharge full”
Step 4 - Third Why
Investigate the various states of the system - Does the description of the alarm correspond to what you’re seeing in the field - “Why is the case-packer discharge full?”
Note that it’s possible that the case packer discharge is indeed full and the machine is simply waiting for the cases to get to the palletizer, in which case, the answer to your question is as follows:
“The case packer is currently in an alarm state “Fault XYZ” because the cases at the discharge are waiting to be transferred to the palletizer”
Note that your conclusion will lead you to another problem statement - “Why is the palletizer down?”
A second path is also possible: “The proximity sensor at the end of the case packer isn’t properly detecting the cases.”
Step 5 - Fourth Why
Why isn’t the prox detecting the cases?
A: The cable appears to be loose.
Why is it loose?
A: It was probably due to the vibration of the conveying system.
Step 6 - Final Log
At this point, you can either screw back the cable onto the sensor or call an electrician. Make sure that you provide him with this reasoning as he’ll immediately be able to fix the issue.
Step 7 - Corrective Action
Log the corrective action that was taken to resolve the issue.
Common Pitfalls of the 5 Whys Process
1. Understand that the 5 Whys is a “flexible tool” - You’re not obliged to follow the “why” pattern; sometimes you need to ask “what” or “whom.” That is perfectly fine.
2. Narrow down your scope - You’re inevitably going to fall into the trap of going “broader” as it’s usually the easy answer - Ex: Why is the case packer down? - Because it hasn’t been maintained properly. These answers are not going to help you or anyone else resolve the issue. Practice narrowing down the scope of the problem with every question.
3. Make sure to properly document the initial and final states - Knowing where and how the problem began is critical; certain information may be forgotten, so it’s important to write it down, take pictures, etc.
4. Reflect on the process as much as on the final outcome - What could you have done better? Are there key areas that you should learn about more before the next failure? Are there other groups you should involve in the process?
5 Whys Root Cause Analysis Template
Here’s a 5 Whys Root Cause Analysis Template which you can also download in PDF format below.
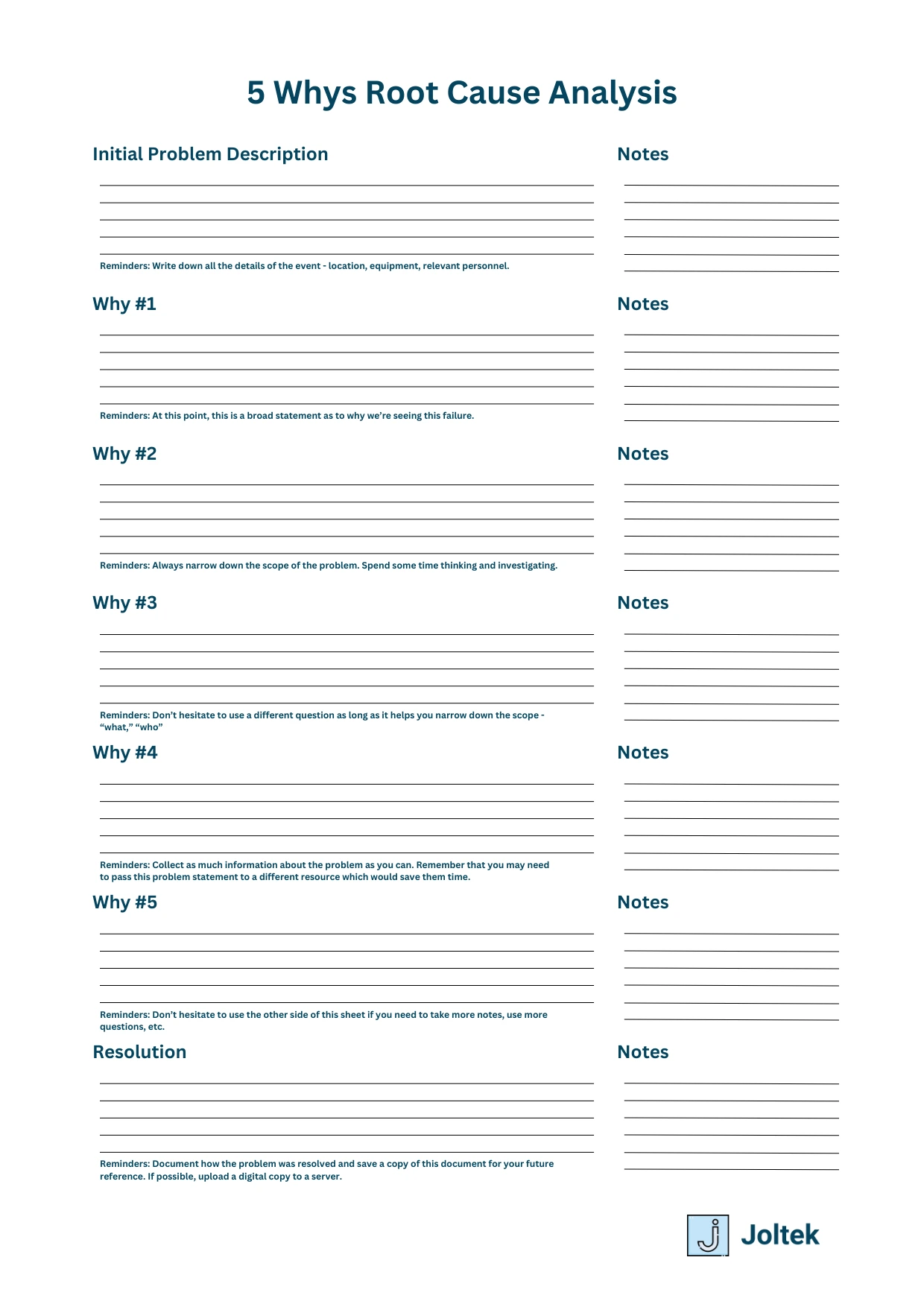
Download 5 Whys Root Cause Analysis Template - PDF
Conclusion on 5 Whys
The 5 Whys technique is more than a series of questions—it’s a mindset shift towards sustainable problem-solving. In the manufacturing industry, where efficiency and uptime are paramount, taking the time to dig into the root cause of issues can save significant time, money, and resources in the long run. While simple on the surface, the 5 Whys requires commitment, discipline, and a willingness to go beyond surface-level solutions.
When implemented with rigor and follow-through, this method fosters a culture of continuous improvement, empowering teams to proactively address the real sources of problems rather than just treating the symptoms. Whether you’re dealing with equipment issues, process inefficiencies, or quality control challenges, the 5 Whys is a powerful tool that can drive impactful and lasting improvements across your operations.
By encouraging curiosity and accountability, this approach can become an invaluable part of your organization’s problem-solving toolkit—helping to build a foundation for operational excellence, reliability, and innovation.