I certainly wasn’t around for all the phases of the evolution of the industrial industry, but I’ve definitely read a lot about what happened throughout the years. If you’ve been to a trade-show or have spent any amount of time on social media within the manufacturing circles, you’ve certainly heard the term “Industry 4.0” tossed around quite liberally.
My goal here isn’t to give you a perspective that is the “absolute best.” My goal here is to provide you my perspective based on years of experience working for world-class manufacturers, leveraging data for decision making, and ultimately give you some food for thought weather you’re a skeptic, frustrated by the buzzwords, are fully sold on the premise, or are completely unaware of what’s it all about. Furthermore, my goal is to provide you with some tangible advice when it comes to business strategy as it relates to Industry 4.0.
Note that none of this content is written or corrected by AI - my goal is to provide you a perspective that is my own based on years of experience, not something you can find through ChatGPT.
The Early Days of Manufacturing
As I mentioned above, I’ve not had first-hand experience on manufacturing floors in the 1900s; we’re thus not going to dwell too much on the history. That being said, I believe it’s important to know why we do certain things the way we do.
Manufacturing was revolutionized through the years; it has always been about creating as many widgets (or products) as fast as possible and as cost-effectively as possible. In the early days, manufacturing was a manual process - people would create widgets or batches of product by hand. With the advancements of various power sources (steam, coal, electricity) and the invention of various engines (steam, coal, electric) it became possible to automate the most costly processes.
Electric motors can be seen as the backbone of most production processes. From mixers, pumps, and fans to servo drives, moving chains, robot arms, AMRs, and more. In the early days, this technology was expensive. You can thus see various implementations of cam drives in old facilities - a single shaft drives various process aspects, timing sensors, etc.
Assembly Line Driven Manufacturing
Most of us have heard the story of Henry Ford and Toyota Manufacturing (Lean Six Sigma). My understanding was that the early manufacturing processes were mostly batch or step-based - Ex: you’d push all the widgets through step A, then push them through step B, etc, until the final step is reached. The revolution of a production line was much more significant than most people give it credit.
Why does an assembly line matter?
Well, for those that haven’t been on a production floor, allow me to illustrate this point via a story…
When I brought equipment for a high-speed production line from Italy to the US, one of the major milestones was getting the line from “running” to “running at a specific OEE.” In other words, it wasn’t enough to run the line; it had to meet certain specifications on the equipment, product, and quality.
This process would take a few months… Different engineers (process, mechanical, and electrical) would have different areas of focus - testing programs, machinery, validating products, etc.
Imagine how much longer the exercise above would take if we needed to take one step at a time! The full production line allowed us to test different machine parameters and product specifications. - Ex: The quality team was working on the converter while the electrical team was running the product through the packer and making adjustments to the vision systems.
The moral of the story here is that an assembly line approach that was pioneered by Henry Ford is driving productivity in many facilities in the world - Engineers, Supervisors, Managers, and Executives are able to make adjustments to a process before each stage is completed and validated. This saves time, money, and reduces waste.
The Third Industrial Revolution
Since the invention of the computer, engineers have been looking to optimize the manufacturing process through the use of sensors, control systems, and related technologies. The third industrial revolution brought forth a wave of different tools that make it possible to control a process from a computer screen; dare I say a mobile phone?
What’s the reality for most facilities?
From my experience, automation isn’t as black or white as it may seem if you’ve spent a lot of time in a specific vertical, company, or facility. In other words, there’s a wide range of where manufacturing plants stand when it comes to automation - some are running equipment from the 1960s, while others have on-prem servers, cloud, etc. It’s important to understand that as you read or listen to a perspective on where industrial automation stands, what the experience of that person is.
In my opinion, there’s still a lot to be done when it comes to optimizing “pure industrial automation” - depending on the state of a facility, there’s low hanging fruit in bringing inefficient equipment, retrofitting what’s no longer producing at the needed rate (or needs too much maintenance), and adding sensors / logic that eliminates some of the issues a facility is constantly running into.
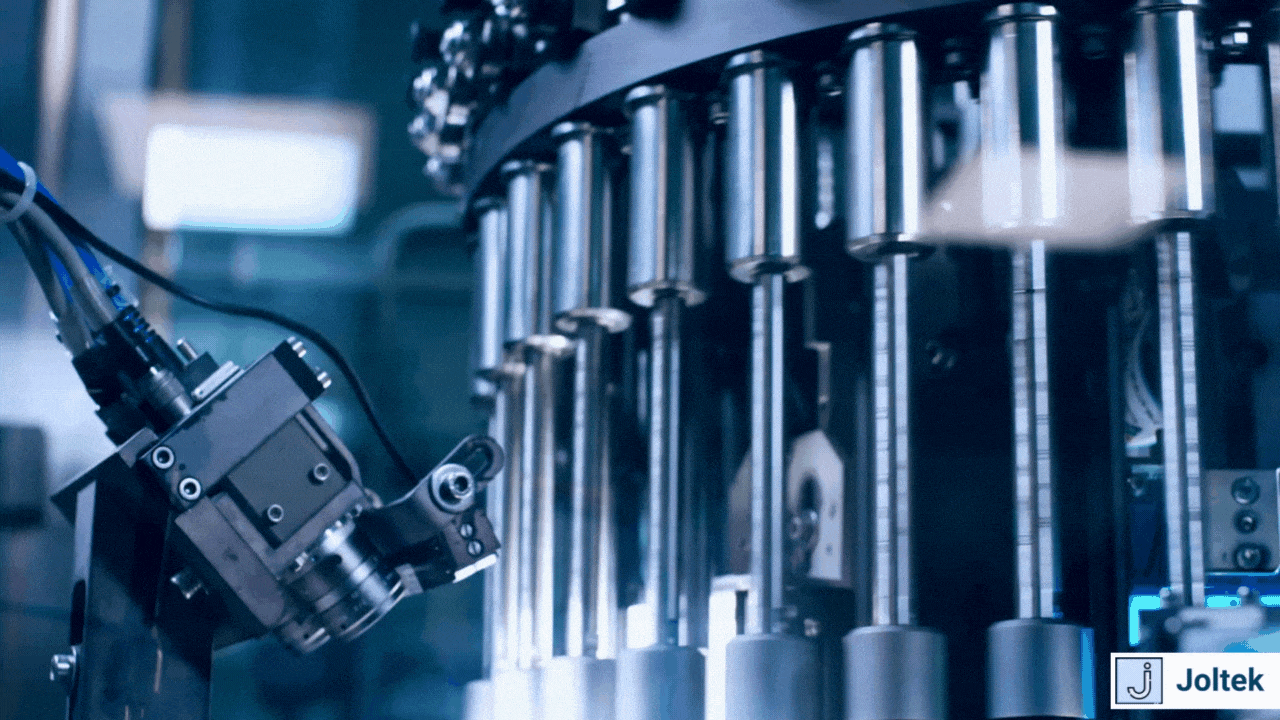
What is Industry 4.0
In recent years, companies at the forefront (important) of industrial automation have realized that they can make further gains by better understanding their process and opportunities through data.
Let’s dissect that a little…
“companies at the forefront of industrial automation”
Extracting data from a process that utilizes equipment from the previous century is nearly impossible. By “impossible,” I generally mean “not cost-effective.” In other words, the older the process and equipment, the more challenging it will be to add tooling that would effectively pull the data required. This typically translates to a postponement of any and all Industry 4.0 initiatives, which further digs the company into the hole over the years.
The above means that Industry 4.0 isn’t as relevant to those who don’t have a solid foundation in automation, a good relationship with a capable technical team (internal resource), and aren’t ready to make the necessary investments in the architecture.
“have realized”
Where has the realization come from? Well, for one, the younger generation is used to measuring everything - there’s an application for tracking your sleep, your shopping list, your tasks, your health metrics, etc. Furthermore, the technologies to “track” metrics have become much more accessible. There are better tools in the SCADA, MES, and ERP layers - it’s easier than ever to program in the data flow from the production floor to the decision-makers.
Other factors exist; the bottom line is that executives are looking to better understand their business, which would give them leverage and certainty over their operational decisions.
“make further gains by better understanding their process”
Make no mistake… We’re all paid through the shrinking margins of a production facility as it makes whatever product. In other words, if we’re able to create value through producing the product at a lower cost, we can command a higher salary / rate. We’re all trying to better understand why the facility isn’t running as well as it should, and find ways to get it to run better.
DATA
Data comes in various shapes and sizes. With enough capital, you can collect metrics on absolutely everything. To that point, collecting metrics on everything is both costly and leads to “analysis paralysis.”
So what’s a good amount of data to collect?
Once again, it depends… For certain manufacturers, knowing something as simple as OEE can lead to significant improvements. For others, these metrics won’t add any value; instead they often become a vanity in executive discussions.
Data needs to solve an existing business challenge. Here are various examples to consider. Note that they’re addressing problems of different “magnitudes.”
Capturing OEE data
OEE is a basic indicator of performance. Notice the “basic” adjective. OEE is something that provides a general understanding of a process, but it’s not going to be sufficient to understand what needs to be improved, how it can be improved, etc.
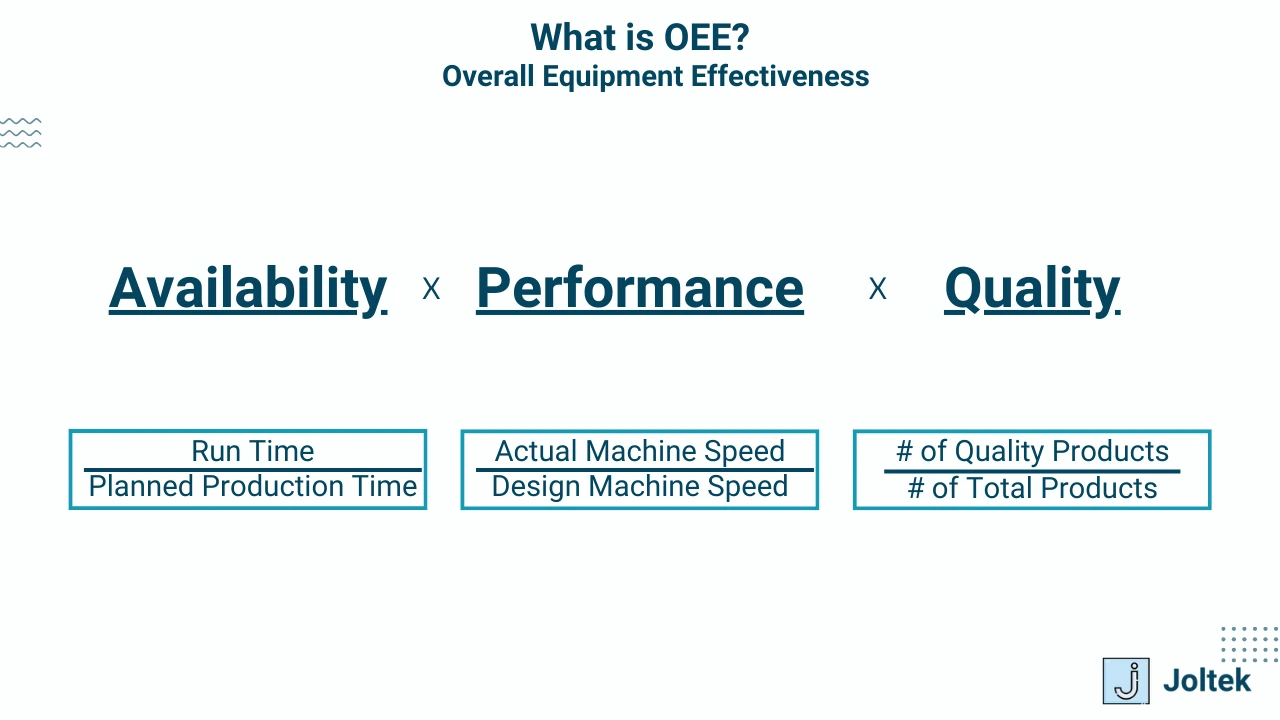
Capturing process temperatures
In food & beverage FDA regulated processes, you’re required to capture certain temperatures for compliance. In other words, you don’t have a choice to capture these metrics. However, you can apply Industry 4.0 principles to capture, analyze and figure out how to improve a process based on temperatures, setpoints, and various ingredients.
Operator Commands Data
In many facilities, operators are the masters of the process. There are multiple challenges here… For one, if that person quits, you’ve lost years of knowledge. It’s going to take months, if not years to get someone up to speed. Furthermore, you’re left wondering if there was a certain step that was missed by an operator. Capturing input data is important.
Machine Fault Tracking
A common need for data is understanding where the machine faults lie. There’s probably an entire post I could make based on my experience with various machines over the years, but it can be boiled down to this… You need to accurately capture the faults at the time of failure and you need to capture various other data points, otherwise it becomes impossible to understand what happened and to remedy the situation before it reoccurs again.
The Downsides and Dangers of Industry 4.0
I’d like to start with potential downsides before we get into the opportunities. I believe that there’s a lot of “hype” right now as to what Industry 4.0 offers and the ability of an organization to understand, navigate, and process this information is going to determine in how good of a position they’ll be in 5-10 years. Not all initiatives are made equal, some of them you should walk away from.
I’d assume that most of us have a foundation financial understanding here. To that point, the baseline for many of these projects is that they need to provide a specific ROI to be greenlit.
What does that mean…?
Well, if you can deploy $2,000,000 worth of sensors at a facility, they should “in theory” provide a benefit of at least $2,000,000 at a specified time frame. If that capital is returned in 9 months, would you be happy? What about 5 years? The point here is that there will be a lot of ambiguity in the metrics, timelines, and ROI for Industry 4.0 type of projects.
Collect ALL the data
I’ve seen organizations go down this path time and time again. They’re not certain what they’ll be doing with the data, and they’ve heard that data is the new oil, and that data is leveraged by companies like Tesla, so the new executive team decides to collect ALL the data. Millions are spent on hardware, software, servers, etc to build out the architecture.
Has the ROI been realized? No… Why? We’ll talk about that a bit later in this post.
Poor Foundational Architecture
I’ve briefly mentioned this above, but a poor network and OT / IT architecture ruins a lot of Industry 4.0 initiatives. The data needs to flow from the plant floor to decisionmakers. This flow is often “regulated” by both OT and IT which means that they need to have a solid technical and business process in place to get this data where it needs to go in the format it needs to be.
Competence, Training & Change Management
It’s not uncommon to hear the phrase “we’ve always done it this way” in a manufacturing setting - it has become the cliché of our industry. The truth is that many of these Industry 4.0 initiatives rely on the teams implementing them, the ability of their staff to have the technical mastery of the platform / tools / concepts, and the fact that they’ll adapt to the process that has been put in place. The reality is that many of these projects fail simply because there’s a misalignment between various parties - we expect fast results and aren’t accepting of a temporary setback in exchange of a “better” long term outcome.
Industry 4.0 Business Strategy
I believe that we’re all sold on the premise that data is important for decision-making. It’s easy to convince a team of executives that they need to have the hard numbers of how their facilities performed last quarter. It’s difficult to convince them that they need to have downtime reports and error tracking reports that would help their teams solve those challenges.
Why? - Because there isn’t an immediate ROI, the change management requires a significant business process, and no-one is asking them for this information besides their direct reports. It’s also often difficult to implement without external resources that can charge a hefty price for their know-how.
What’s a good approach to adopting Industry 4.0 Business Strategy?
Personally, I’m a big fan of Root Cause Analysis (RCA) - a framework which is often used by Lean Six Sigma professionals to identify the source of an issue. An RCS doesn’t need to be complex; here’s an example based on a conversation with a plant manager I had at a major food & beverage company:
Q: I see that you’ve discarded a batch last night, do you know why it happened?
A: I was told there was a quality defect with the ingredients that were mixed into the batch.
Q: Do you know how big was this batch?
A: We lost close to 40,000 lbs. of product.
Q: What was the value of those ingredients?
A: Approximately $200,000.
Q: Do we know what the issue with the ingredients was?
A: We believe that the operator didn’t mix in the right amount of sugar into the batch at the right time.
Q: Are we able to verify what happened with the batch?
A: No.
Q: Are we able to see which inputs were made at the time of the batch?
A: No.
Q: How often have you had this happen?
A: We’ve seen this issue before; it happens a few times per month.
Clearly, there’s an opportunity here to create a system that would provide visibility into the batching system.
Business Strategy
A business strategy isn’t an operational guide. Let’s use the following framework to instill a culture which matches Industry 4.0 principles:
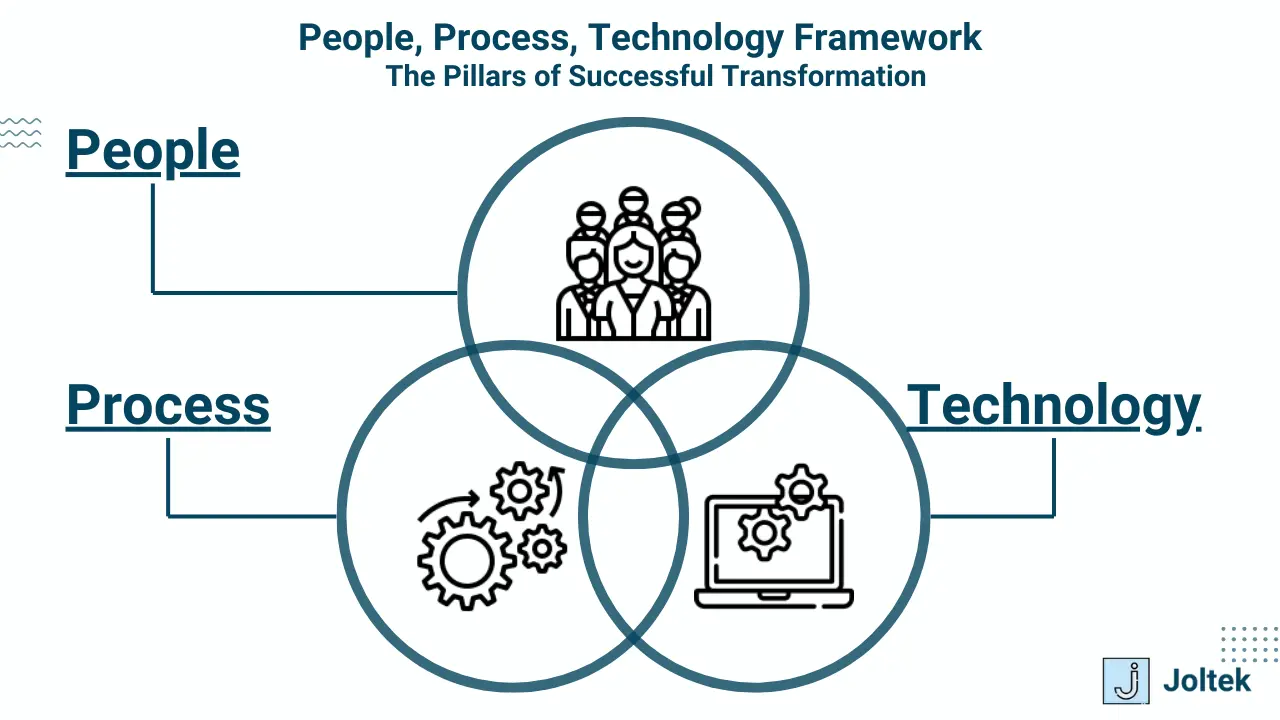
People
The core teams need to understand the importance and opportunities with data. They should be coaching their teams to understand the current tools, validate new ideas, and collect ways to improve their specific areas of ownership. Keep in mind that tools such as the 5 Whys Root Cause Analysis Template can help your people understand the process better and drive your plant into the fourth industrial revolution.
Process
The business must set specific, measurable, and actionable objectives at every level - Are the directors able to support their plant managers with the tools they need to implement change? Are the plant managers getting access to the data they need to make decisions? Is the plant management team (engineering, maintenance, operations, quality) able to use the current tools and get the data they need to do their job better? What’s the process of deploying a new tool onto the plant floor?
Technology
Despite Industry 4.0 having a technical connotation, I believe it’s often the last component of a successful business transformation. However, it’s important to have a core team of individuals that understands the current technology stack of the business, understands what’s possible and how much it would cost to implement, and lastly, be technically capable, or have a resource capable of implementation.
Industry 4.0 Technologies
I’ve had this conversation with various stakeholders multiple times. My opinion is that the bar to getting data from the plant floor continue to get lowered. However, the complexity, and thus the need for knowledge, for integration continues to increase. In other words, the right solution for your specific use case is now cheaper than ever, but the number of options and ways to implement this solution has increased which may lead to a more expensive alternative.
My opinion is that there are two “camps” in our industry - on one side, we’ve got a lot of debates going on around the definition of what “IIoT - Industrial Internet of Things” is while simultaneously we have a lot of debates around very specific protocols - Ex: MQTT vs OPC. I don’t believe that either one of those conversations are critical for most businesses - It’s not important for you to adhere to a specific definition, nor is it important for you to decide on a specific protocol (in most cases). You need to focus on technologies that add clear value to your process and people. Can you articulate the value of data derived from your batching process? - It doesn’t matter if that’s IIoT, if it communicates over Modbus, etc.
Don’t get stuck in details, nor in philosophical debates. They’re a waste of time for most organizations.
The Conclusion on Industry 4.0
I truly believe in the value of data. I get frustrated with sites that aren’t able to answer the most basic questions as to how good / bad their line performance was, let alone why that is the case. The lack of data in our industry is astonishing; there’s a lot of work to be done, and it’s going to take years.